Risk Assessment
Aromatawai Tūraru
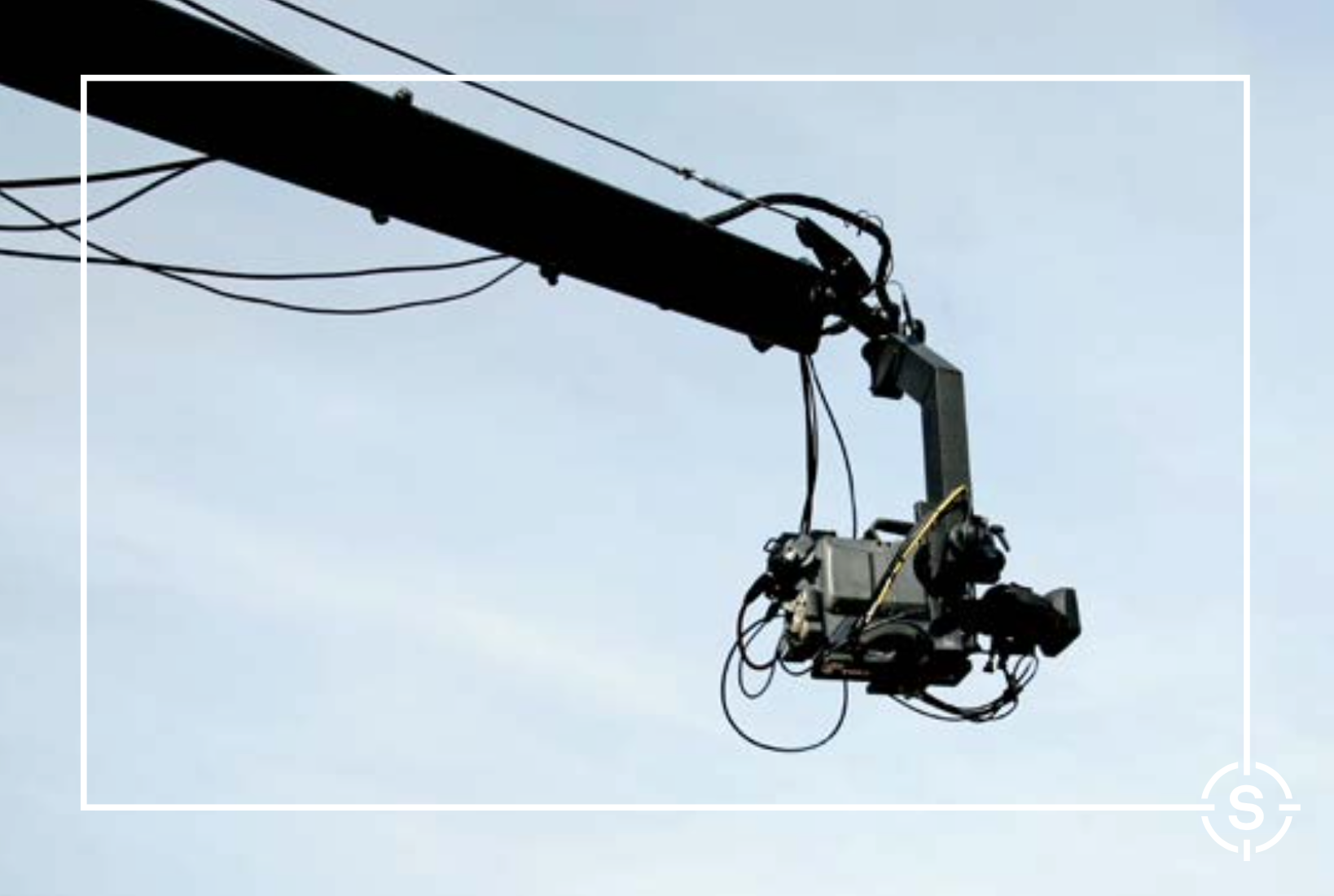
Introduction
PCBU’s, including those who are responsible for a task or activity, must manage potential risk by identifying, understanding and deciding how to control it. This is commonly known as a risk assessment.
The value of a health and safety officer is that they are competent to undertake this process for the production.
It is useful for all PCBUs and workers to understand how this process works, so they can identify and notify hazards and risks, and think about how to manage them.
* YOU CAN FIND A TEMPLATE HERE TO HELP YOU WITH YOUR HEALTH AND SAFETY RISK ASSESSMENT.
Identifying, Assessing and Managing Risk
Most safety events could have been prevented with better planning.
Risks to health and safety are caused by people being exposed to hazards. Your job is to identity hazards and assess risks and do all you can to ensure no one is harmed.
Risks must be eliminated so far as is reasonably practicable. If the risk cannot be eliminated, then you must minimise that risk so far as is reasonably practicable.

When do I need to undertake a risk assessment?
You should carry out a risk assessment for all workplaces, before work commences.
What do I need to do?
A safe workplace requires a structured method to finding and fixing hazards and risks. This takes four main steps.
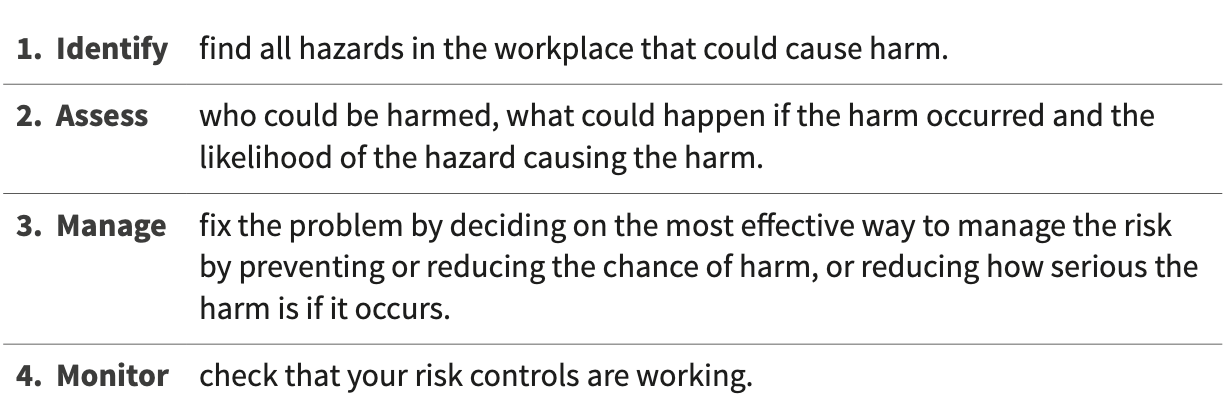
This process doesn’t need to create a huge amount of paperwork; you should officially record your significant risks but don’t need to record everyday risks.
* Keep it simple. Focus on managing risk and stopping people from being hurt.
1. Identify
How do I Identify Hazards?
The best place to start is often just by walking around the production set or location and looking for anything that could harm your workers and others.
You may also want to speak with people who have experience working on similar production sets or locations, and those with expert knowledge of the specific location.
Another way of identifying risk is to look at what has happened in the past, including incident reports.
* Remember, harm can be acute – occur immediately, or chronic – occur over time.
Examples of Workplace Hazards:
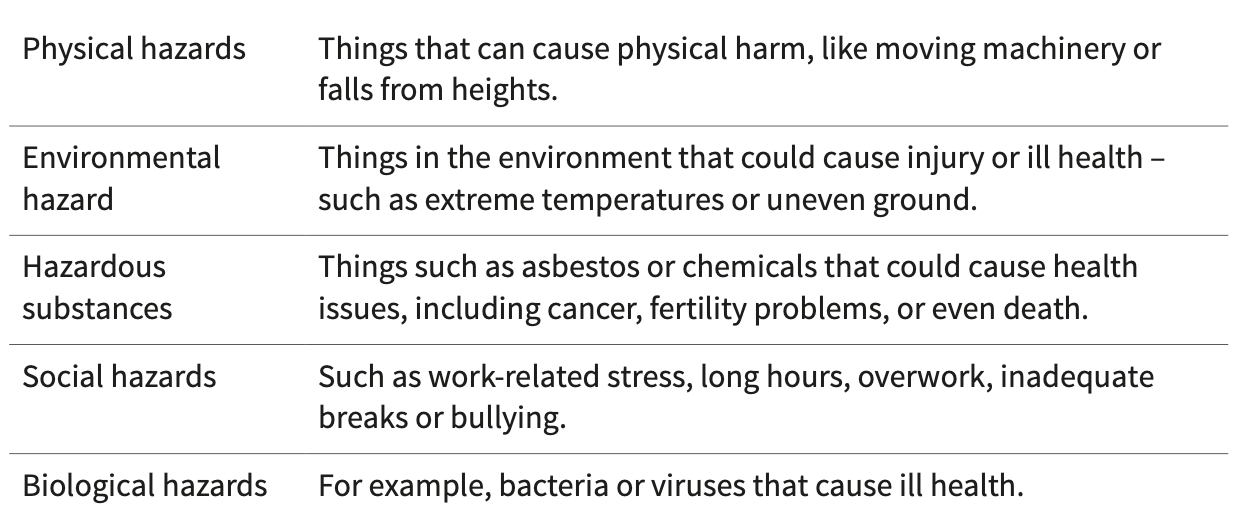
2. Assess
How do I Assess the Risks?
Once you have identified potential hazards you must assess the potential for harm. Think about:
- how serious could harm be if it occurred; and
- what is the likelihood of someone being harmed by the hazard?
* Focus on the real risks – those that are most likely to cause harm.
As with the identifying process, you may want to engage with those who have experience working on similar production sets or locations, and subject matter experts, as they may be able to help with your assessment.
A risk matrix can help you identify the potential for harm.
Risk Rating Table
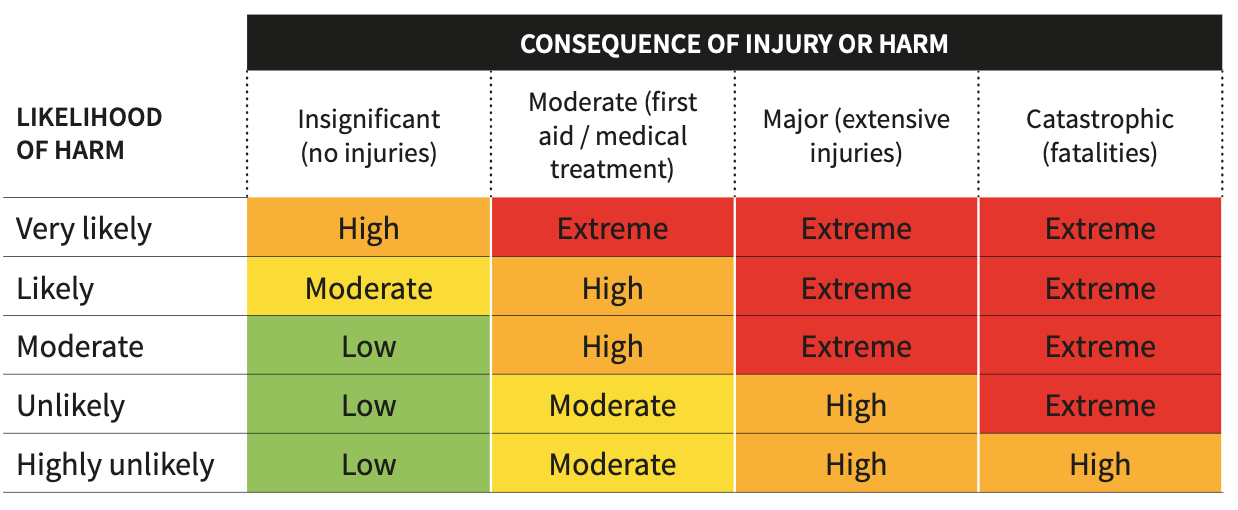
Once you have rated the level of risk/s, all risks should be prioritised and appropriate action taken – this process is subjective, however you could prioritise as below:
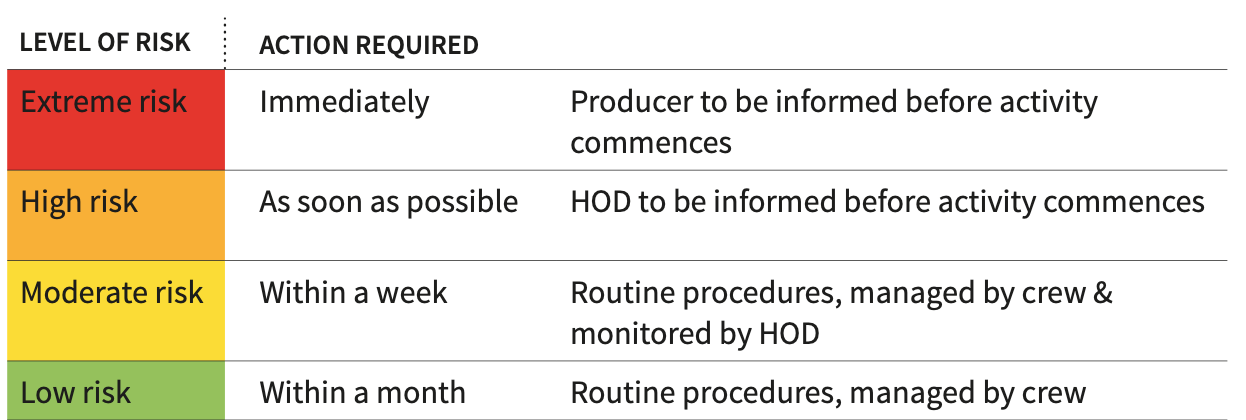
If you have multiple ‘extreme’ or ‘high’ risks, you may want to reconsider your plans for the production and whether set locations or tasks need to be changed.
You should also think about any control measures already in place to manage risks and if they are enough to stop harm from occurring.
Who might be Harmed and How?
When evaluating risks to health and safety you must identify who could be exposed to the hazard and how harm may occur.
Workers who come in contact with the hazard every day are the most obvious groups to be at risk.
Your risk assessment should identify the ways in which workers could be harmed, as well as the number of people in the different groups who could come in contact with the hazard and how often this may occur.
3. Manage
How do I Manage the Risk?
Risks specified in regulation
Firstly, you need to check if the identified risk is one that has to be dealt with in a certain way under a specific health and safety regulation. For example, handling asbestos or preventing falls from height. If it is, you need to follow the regulated requirements.
Other risks
If the risk does not have to managed under a regulation, you need to ask two questions:
- Can I eliminate the risk, so far as is reasonably practicable?
- If I can’t eliminate the risk, how can I minimise the risk, so far as is reasonably practicable, so that harm is unlikely?
This process is called using the hierarchy of control, which is a way of ranking levels of protection – from the highest level of protection and reliability to the lowest.
Hierarchy of Controls
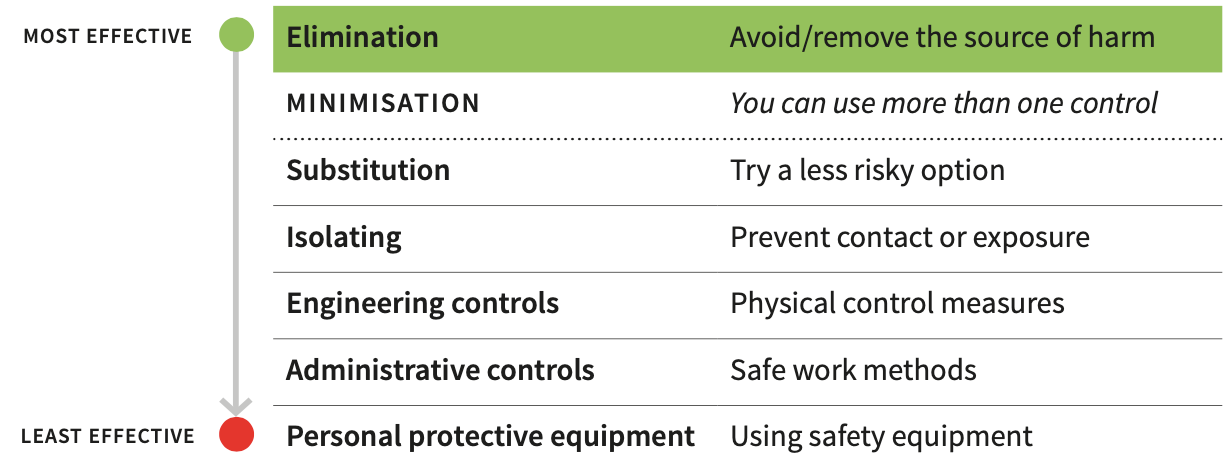
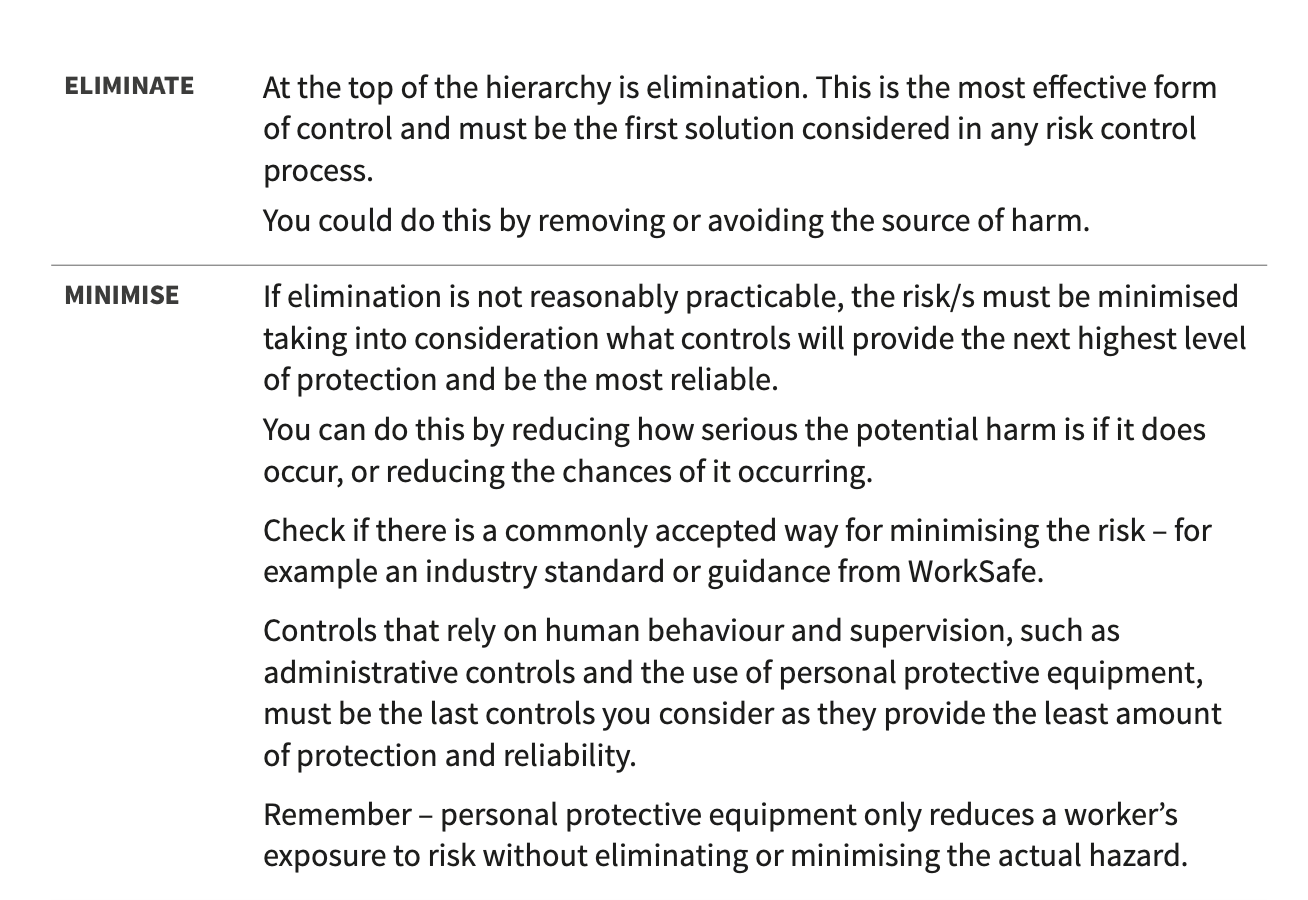
Dealing with Risks in a Reasonably Practicable Way
‘Reasonably practicable’ means what is, or was, reasonably practicable to manage the risk. You do this by weighing up relevant matters, including:
- how likely it is that the hazard or risk will occur;
- the degree of harm that might result from that hazard or risk;
- what you know, or ought to know, about the risk; and
- how to eliminate or minimise the risk.
Only after thinking about the extent of the risk and the available ways of eliminating or minimising it, should cost to mitigate the risk be considered and whether such cost is grossly disproportionate to that risk.
Do I have to eliminate ALL Risks?
The law doesn’t expect you to remove all risks, but it does expect you to stop people from getting hurt by putting controls in place to significantly reduce all identified risks, as far as reasonably practicable.
What you must do is make sure you know about the main risks and the things you need to do to manage them responsibly.
What if I miss a Risk?
Your risk assessment only needs to include what you could reasonably have been expected to know when the assessment was undertaken. It is not expected to anticipate ‘unforeseeable’ risks.
What if I share the workplace with other PCBUs?
If you share your workplace with another PCBUs, you will both need to:
- tell each other about the specific risks that may affect the other; and
- cooperate and coordinate with each other to control the health and safety risks.
Do I need to keep records of the Risk Assessment process?
While keeping written records of your risk assessment process is your decision, it is good practice to do so, as they will help you review your risks and controls if something on the production set changes.
Who needs to know about the Risks and Control Measures put in place?
You need to ensure all PCBUs and workers know:
- about the potential risks;
- what are the control measures;
- why it’s important to use controls; and
- how to apply the implemented controls.
It is up to you how you communicate this with PCBUs and workers. You may hold health and safety briefings or include information on daily call sheets.
4. Monitor
What does monitoring involve?
Production sets are unusual as they are usually set up for a finite amount of time, unlike permanent workplaces. However, you still need to ensure your control measures remain effective over the life of the production.
You should regularly:
- check that control measures are correctly installed / set up and being used by workers;
- check that control measures are still effective; and
- monitor worker exposure to risks, to check the control measures are minimising risk.
Download The Health & Safety Risk Assessment Worksheet HERE