Tech Guidelines
Ngā Aratohu Ā-Hangarau
These Guidelines are targeted towards technical areas of Health and Safety. Please reach out to us if you see that any other guideline within the "All Guidelines" section should be included in this section.
Armoury Department: Risk Assessment for Blank Firing Firearms
These are the current guidelines for use of firearms within a production based environment, including all on and off set operations - as at 1 July 2024
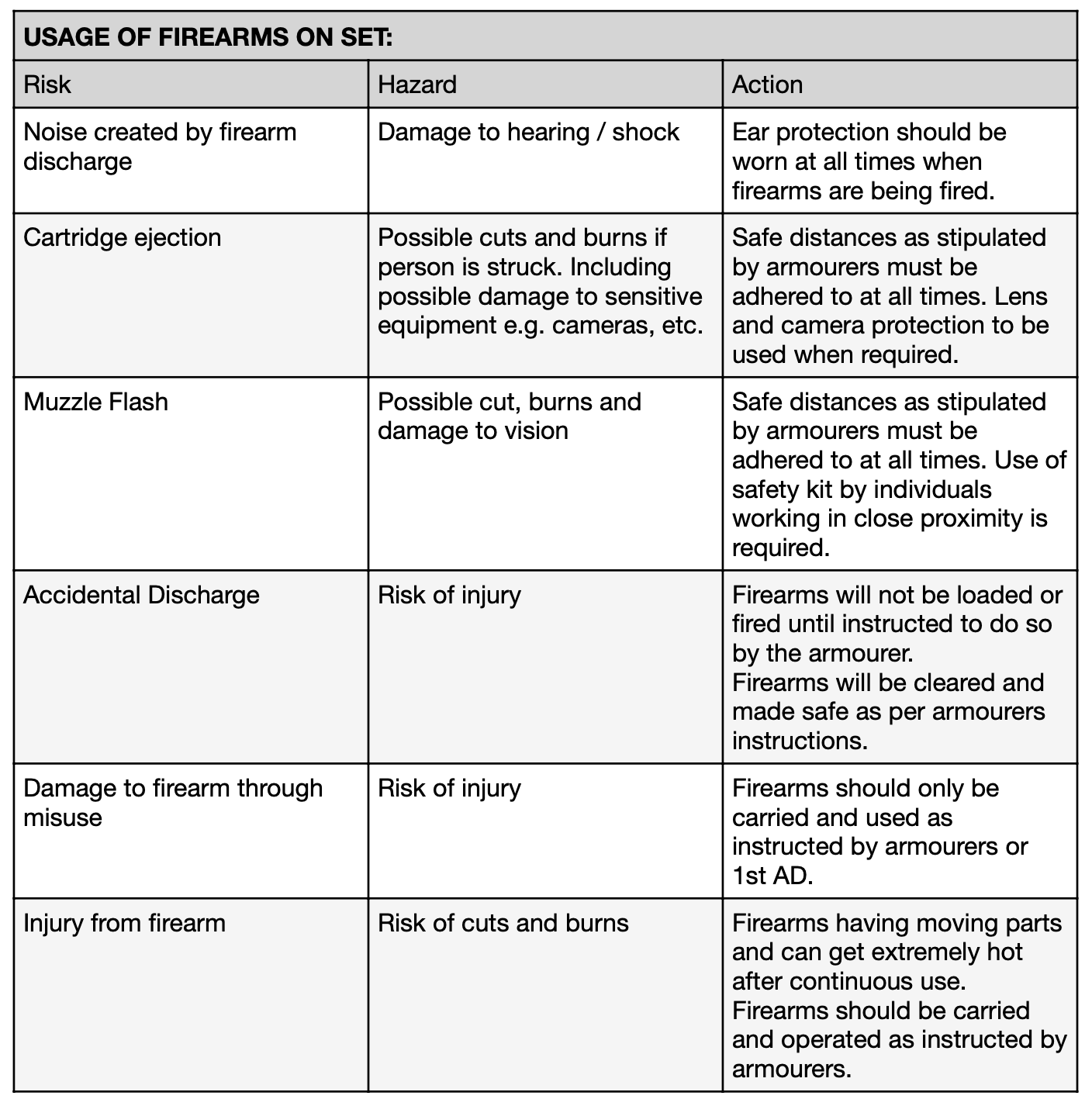
Armoury Department: General Rules for Safe Firearms Usage on Set
No person is permitted to use a firearm unless they have received adequate instruction prior to filming, in safe handling, use and firing procedures by the onset armourer.
A safety meeting for cast and crew shall be conduced prior to firearms being used on set.
BLANKS CAN KILL. TREAT ALL FIREARMS AS THOUGH THEY ARE LOADED.
“LIVE AMMUNITION” is NEVER to be used nor brought onto set, stage or stage lot at any given time.
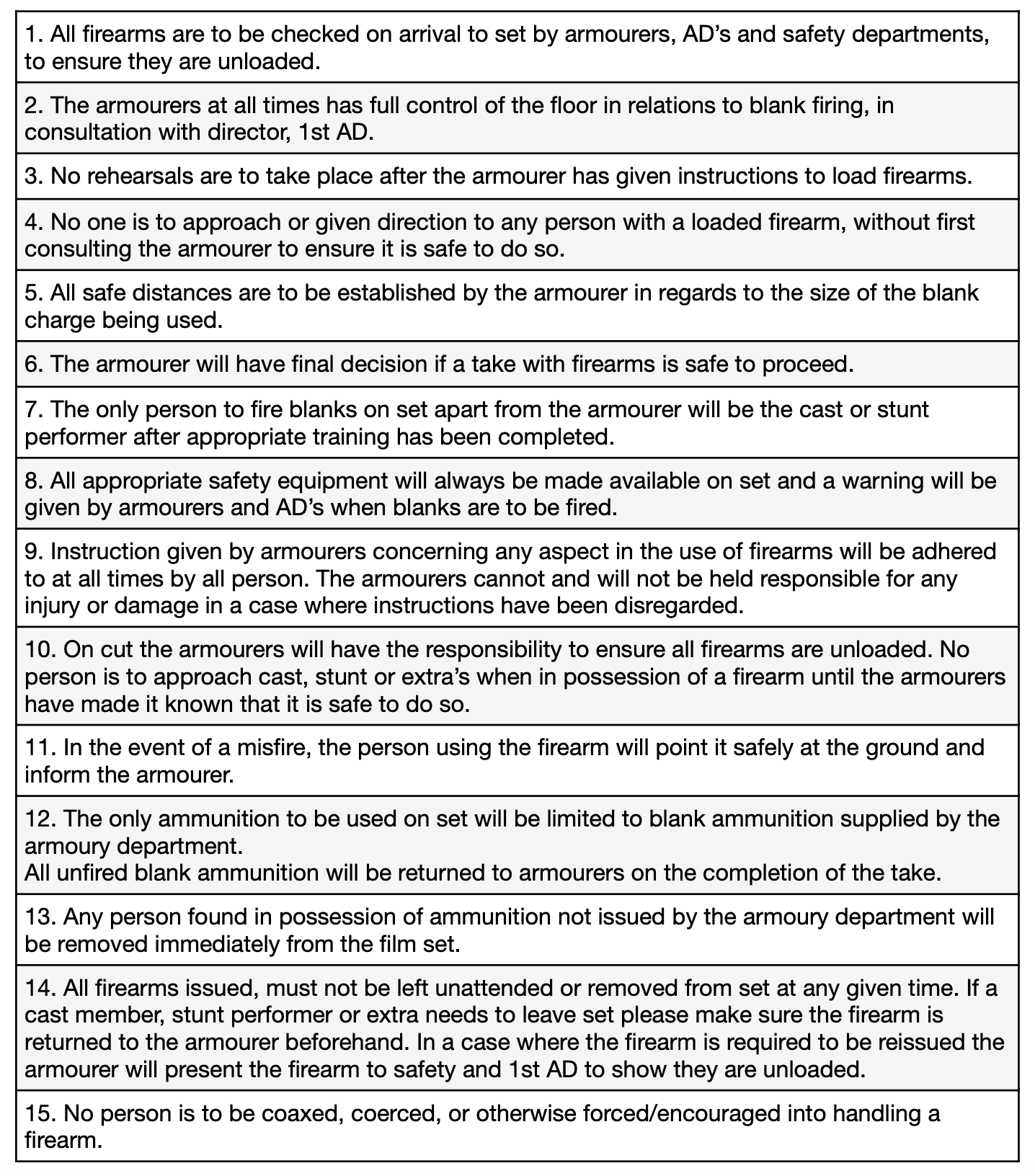
Armoury Department: Armourers Responsibility
- The Armourer is to obtain written permission from NZ Police prior to providing firearm to the production.
- NZ Police Communication Centre is to be notified daily prior to the use and completion of firearms use.
- An event number is to be obtained and recorded from the Communication Centre by the armourer.
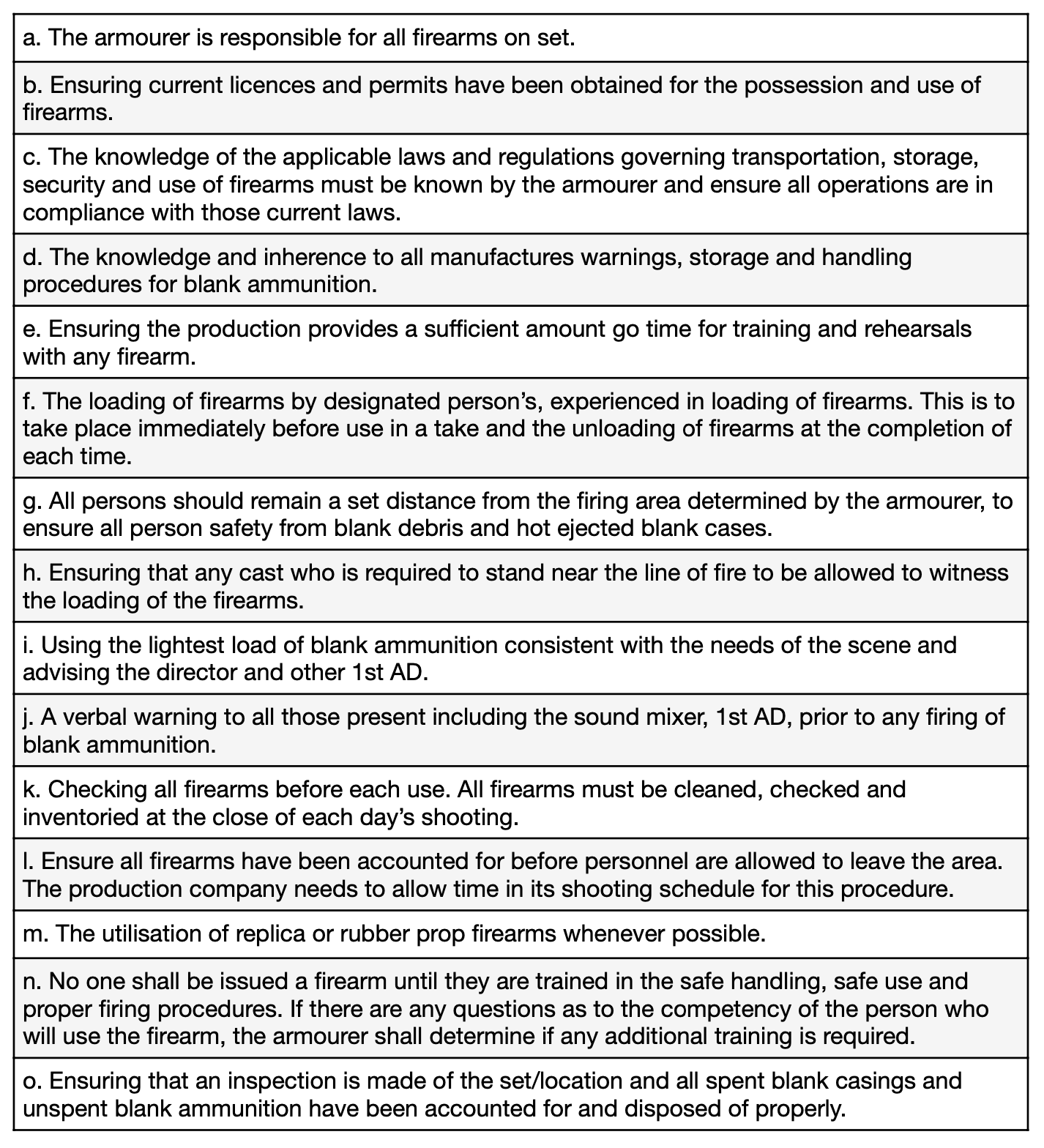
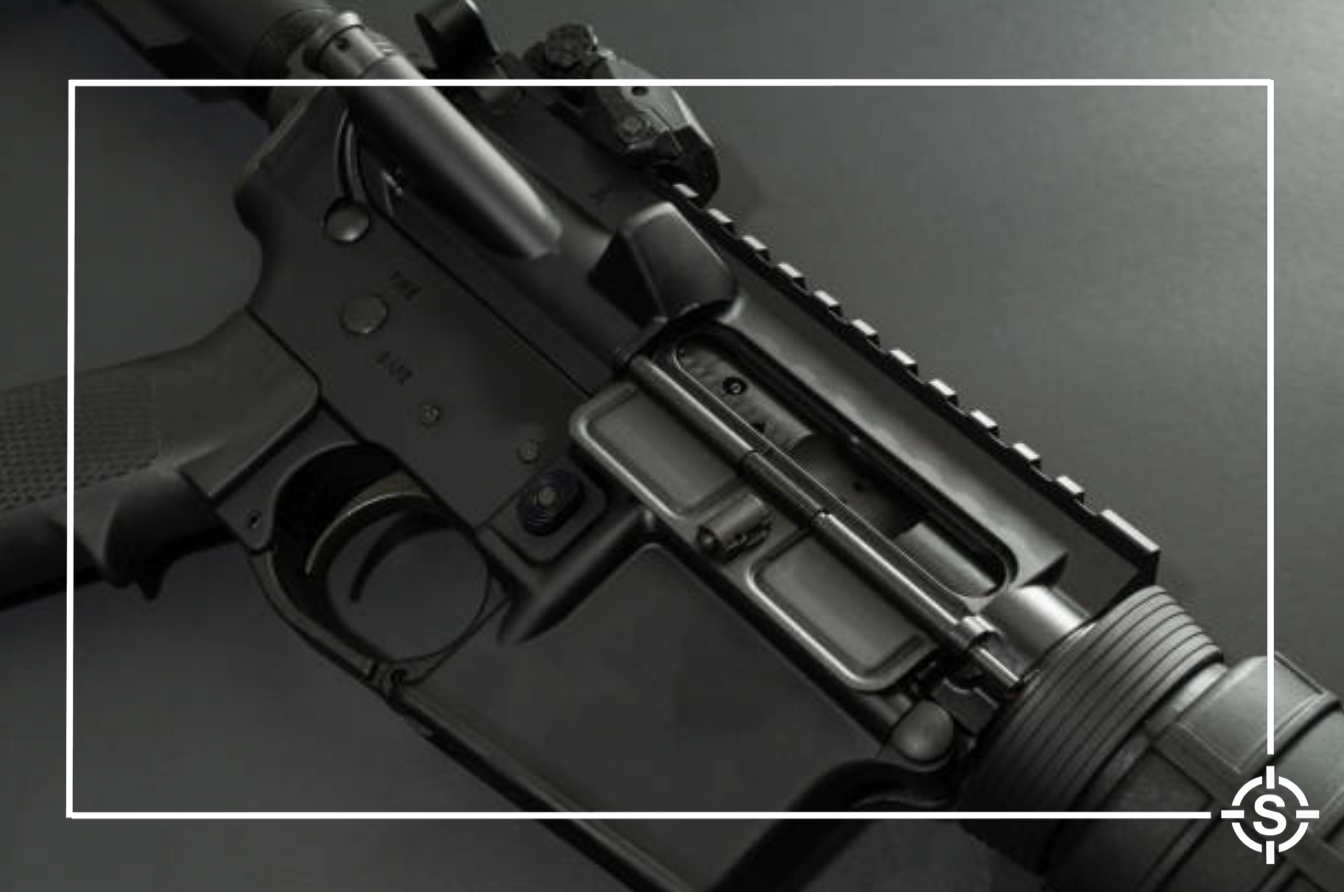
Armoury - Firearms Guidelines
Electrical
This chapter provides guidance in relation to electrical safety on a production, and is primarily based on New Zealand legislation and guidance issued by WorkSafe NZ, the BBC and IEE Wiring Matters.
Who needs to read this?
All workers who undertake electrical work should read and understand the section on ‘minimum responsibilities’.
Any person who is responsible for supplying electrical equipment to a production, both from the supply company and the production company; as well as any person who plugs anything into the electrical supply.
Roles that have specific responsibilities, or influence, over electrical work should read the section on ‘planning and guidance considerations’ – this includes producers, directors, production managers, line producers, heads of departments, assistant directors and health and safety officers.
Definitions
Competent means a person who has through a combination of training, education and experience, acquired knowledge and skills enabling that person to correctly perform a specified task.
Qualified electrician is a person who has both a current electrical registration and practicing licence.
RCD is a Residual Current Device.
What specific electrical risks are there on production sets?
- Arcing.
- Electric faults can result in a fire.
- Contact with electricity causing electrical shock and/or burns.
- Exploding bulbs/lamps.
- Generators incorrectly specified/setup for use.
- Power overload.
- Equipment falling over and causing injury.
- Electric cables and wires may create a trip hazard.
- Using electrical equipment in higher risk environments: wet, damp, humid, dusty conditions, increases the hazards significantly.
- Overhead obstructions.
- Radiation burns.
- Batteries can cause fire if the terminals come into contact with conductive materials.
-
Minimum Responsibilities for Electrical Work
Everyone on a screen production should read and understand this section.
If you have planning responsibilities for, or planning influence over, electrical work you also should read and understand the following section on planning and guidance considerations and responsibilities below.
If you undertake or are responsible for, or have influence over, electrical work you should also read and understand the section on responsibilities specific to electrical work below.
Only those persons accredited under relevant legislation shall be engaged to undertake electrical maintenance and or installation.
If electrical equipment starts to burn or smoke:
- isolate the electrical supply if possible;
- use carbon dioxide or dry powder extinguisher, if competent to do so, but do not put yourself in danger;
- avoid inhaling fumes from burning plastics; and
- call emergency services – dial 111.
All workers should:
- have a basic knowledge of electrical safety, if they are expected to handle electrical equipment;
- understand the risks associated with electrical work;
- ask the gaffer/electrician before plugging any cable into a distribution board/socket;
- immediately advise the producer, or person with delegated responsibility, and electrics crew of all potential electrical hazards;
- use personal protective equipment when required; and
- advise their supervisor or the health and safety advisor when they observe unsafe electrical work.
Workers should NEVER:
- place liquid (drinks) on any electrical appliance or fitting;
- walk on, drive over, or stand on cables – sudden or continuous weight can create a weak point in the cable and cause an electrical fault; and
- attempt to investigate or repair faulty equipment unless they are qualified.
Planning and Guidance Considerations and Responsibilities
Everyone has planning responsibilities for, or planning influence, over electrical work should read and understand this section, as well as the minimum responsibilities for everybody.
This includes funders, the production company, producers, heads of departments, and health and safety advisors.
Anyone who is responsible for or undertakes electrical work should also read and understand the next section – responsibilities specific to electrical work.
Funders
Funders should:
• be assured, through the provision of the production’s health and safety plan, that the funding provided is adequate to provide for competent people to undertake and supervise all electrical work and appropriate electrical equipment.
Production Company
In pre-production, production companies (likely to have primary responsibility over health and safety on the production) should:
- ensure that at least one member of the crew dealing with electrical matters is suitably qualified;
- consider the potential risks associated with electrical work when planning and allocating tasks;
- ensure the potential risks associated are appropriately managed, either eliminating or minimising them; and
- engage competent persons to oversee and undertake all electrical work associated with the production.
Producer / Production Manager
As Producers and Production Managers have oversight across the production, they should:
- engage competent people to undertake and / or supervise electrical work;
- consider the potential risks associated with electrical work when planning and allocating tasks;
- manage the potential risks associated with electrical work, either eliminating or minimising them;
- engage competent persons to oversee and undertake all electrical work associated with the production;
- ensure all crew are advised of any electrical hazards as necessary and immediate steps must be taken to eliminate or minimise the risk; and
- consider whether a specialist company may be required to produce a suitable electrical design
Heads of Department
Heads of department’s whose department undertakes any type of electrical work should ensure a competent person undertakes that work and read the section on responsibilities specific to electrical work.
Health and Safety Officer
The Health and Safety Officer should ensure potential risks associated with electrical work are discussed with all cast and crew during health and safety inductions and / or as required if circumstances on the set change.
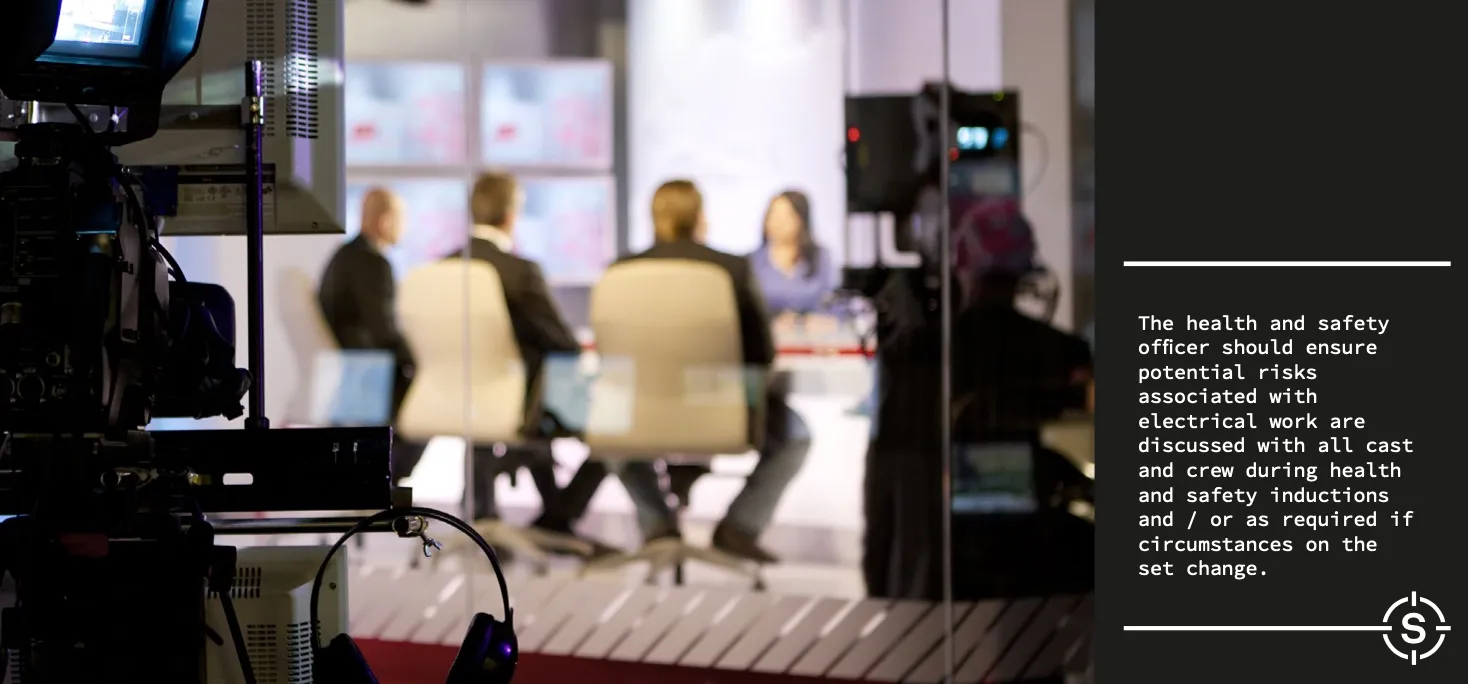
Responsibilities Specific to Electrical Work
Everyone who undertakes or is responsible for, or has influence over, electrical work should read and understand this section, as well as the previous sections.
This includes electricians, Gaffers and anyone undertaking or with responsibilities or influence over electrical work on a production.
Anyone bringing electrical items to a production should also be aware of and comply with:
- AS/NZS 3760:2010 – specifies the requirements for safe inspection and testing of electrical equipment in the workplace.
Anyone undertaking electrical work must comply with the following standards:
- AS/NZS 3010 – all electrical work must be carried out in accordance with the Electricity Act 1922 and Electrical (Safety) Regulations 2010.
- AS/NZS 4249:1994 – specifies the requirements for safe working practices in the use of electrical equipment on film, video and television sites and the in-service testing of the equipment, and must be followed,
- AS/NZS 3760:2010 – specifies the requirements for safe inspection and testing of electrical equipment in the workplace.
Any person responsible for, or with influence over, electrical work, likely to be the gaffer or head registered electrician, must ensure:
- all crew are advised of any electrical hazards as necessary and immediate steps must be taken to eliminate or minimise the risk;
- where practicable, all final circuits must be protected by a 30mA Residual Current Device (RCD);
- electrical work is carried out by a competent person, this is either a:
- ~ - registered electrician with current practising licence; or
- ~ - electrical service technician with current practising licence; or
- ~ - electrical appliance service person with current practising licence; or
- ~ - person working under supervision of the above;
- the installation of fixing wiring and electrical equipment to production sets is carried out by a competent person, as define above;
- electrical equipment is well maintained;
- electrical equipment / devices are tested for function by a competent person – testing requirements must follow those outlined in legislation and NZ standards AS/NZS 3760:2010;
- electrical equipment whether onset, in offices or workshops display a current test tag to AS/NZS3760:2010
- leads are off the ground or protected where practicable;
- electrical equipment/devices are protected from the weather, or constructed to a suitable IP rating;
- cables and distribution are of sufficient size and capacity to do the required job;
- cables are not twisted, crushed or kinked;
- cables are secured and clearly identified;
- cable routing is carefully considered and does not create a tripping hazard;
- power is turned off when installing power distribution equipment.
Minimum clearance between equipment and overhead electric power lines
Anyone supervising or operating equipment near or under power lines is responsible for ensuring the following is adhered to:
- Overhead power lines (conductors) are an often overlooked danger. Be alert for the presence of overhead conductors when operating cranes, boom swinging, carrying tall objects, being in a boat with a mast up on the water or on a trailer on land.
- When operating mechanical equipment near overhead electric power conductors the requirements of the Electricity Regulations 1993, clause 82 (3) and (5), and NZECP 34,1993 apply. There is a minimum clearance of four metres. Consult your local power supplier who may permit closer operation for lower voltages. Written permission is required to operate closer than four metres.
- When travelling on the road, the requirements of the Transport Act 1976 apply.
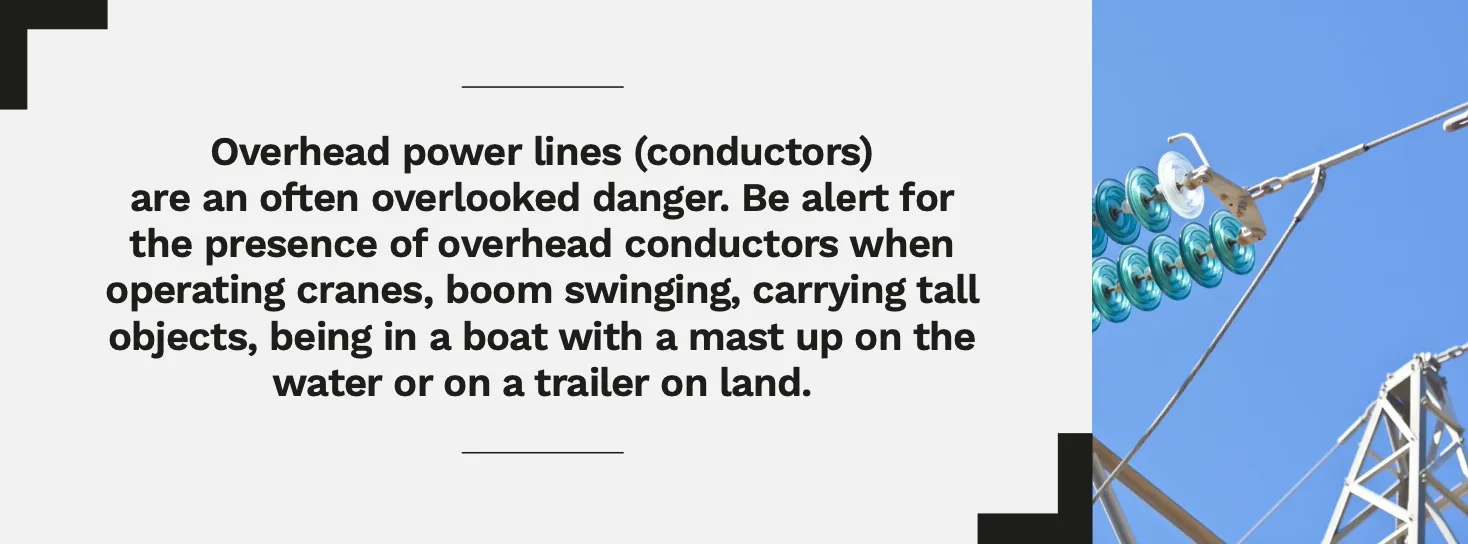
Managing the Risk
How do I control risks associated with Electrical Work?
First, you must consider whether you can eliminate the risk, if this is not reasonably practicable then you must minimise that risk – this is called the hierarchy of controls.
Appendix 2: health and safety risk assessments process will further help you understand how to use the hierarchy of controls.
The Risk of Electrical Shock and Fire
Risks associated with temporary installations are those of electric shock and fire.
These arise from:
• the temporary nature of the installation;
• lack of permanent structures;
• severe mechanical stresses; and
• access to the public.
Attention should be paid to:
• suitability of the equipment for the environment;
• earthing and bonding requirements;
• connection to the supply; and
• use of accessories of the appropriate Degree of Protection (IP code) to suit the external influences.
* see TEMPORARY POWER DISTRIBUTION SYSTEMS AND ELECTRICAL SUPPLIES FOR ENTERTAINMENT RELATED PURPOSES
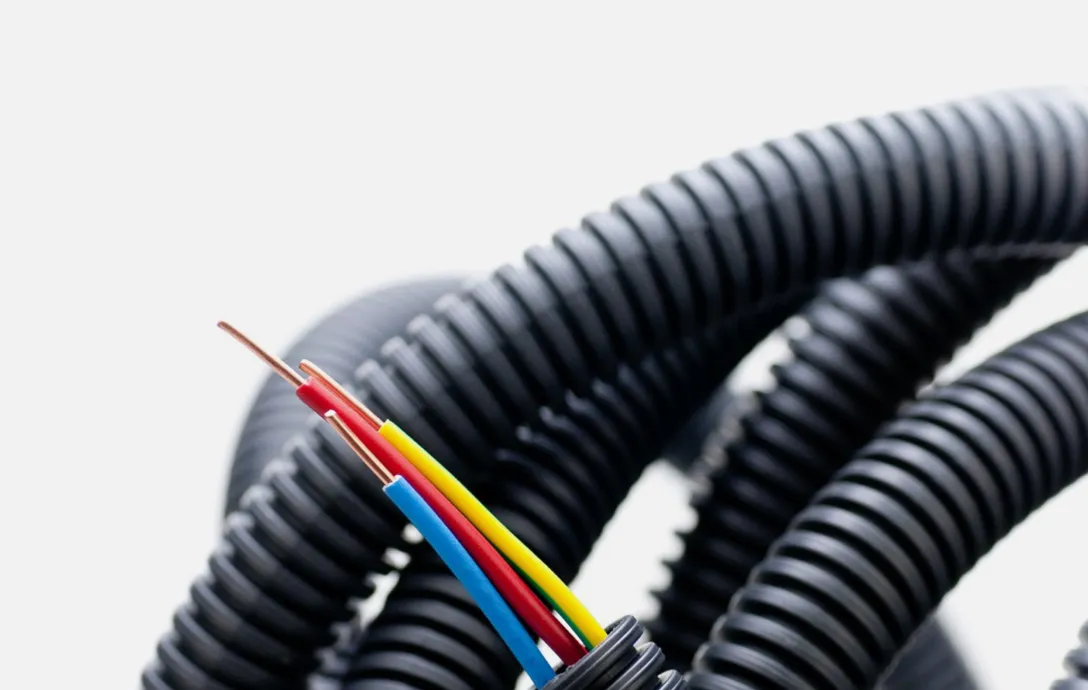
Gaffer and/or Head Electrician
By law, electricians have greater authority and responsibility than non-electricians in matters around electricity. If the head gaffer is not an electrician, the head electrician within the department, where the work is occurring, is responsible for all electrical items on the job.
Gaffers and/or the head electrician should:
- manage and represent the electrical crew under their supervision;
- ensure the electrical competency of all electrical crew under their supervision;
- undertake a risk assessment for all electrical work undertaken by you and your team;
- check all electrical equipment is sound before use and, where applicable, testing certificates are current.
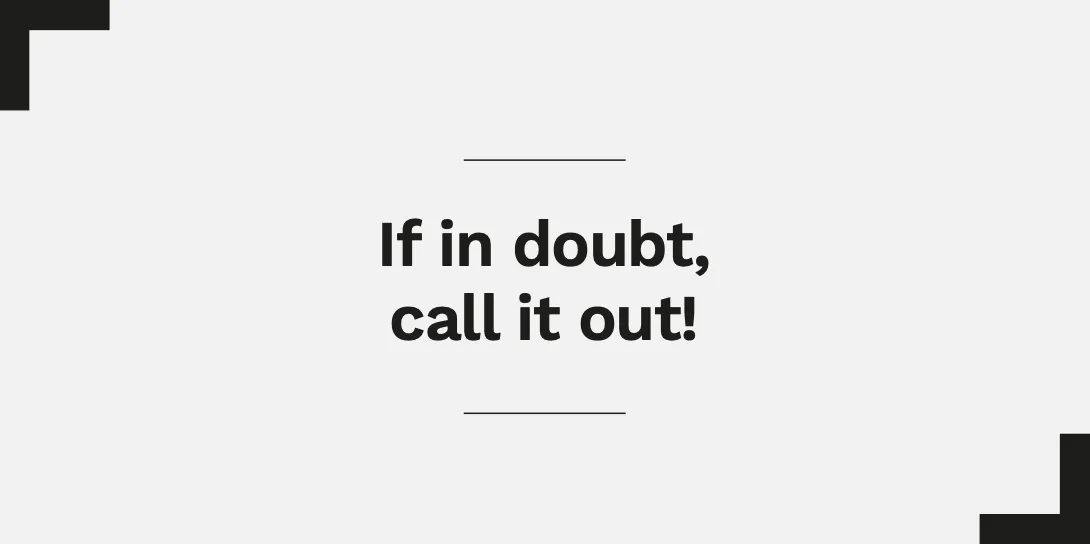
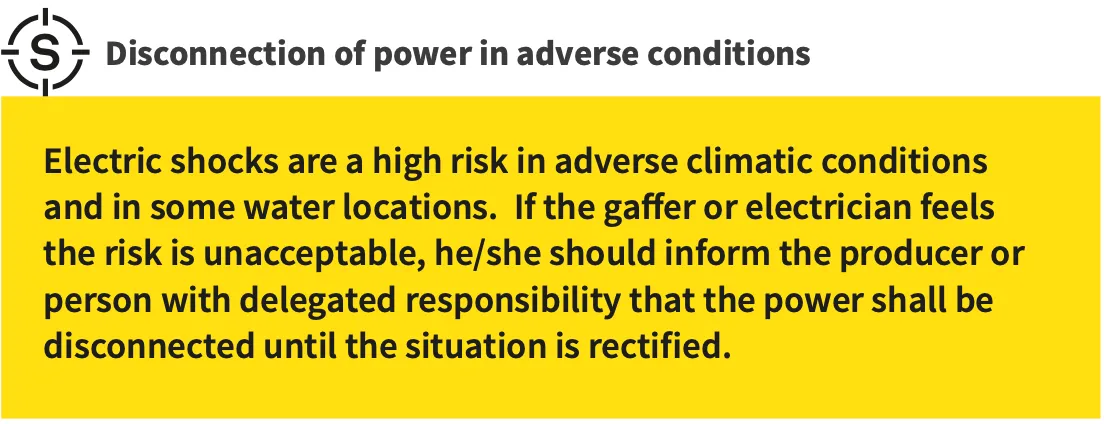
Training
As part of all PCBU's primary duty of care to provide and maintain a safe and healthy work environment, they must ensure workers have had the necessary training to allow them to undertake their work safely.
Anyone who has direct oversight of electrical work should ensure the crew undertaking the task/s are adequately trained and competent in their work.
Things to think about include, does the worker require:
- a qualification to undertake the task;
- supervision by a competent person, if they are new or don’t have the required level of training?
- basic training teaching them how to undertake the task safely; or
- basic training teaching them how to ensure the risk control is effective, including use of personal protective equipment?
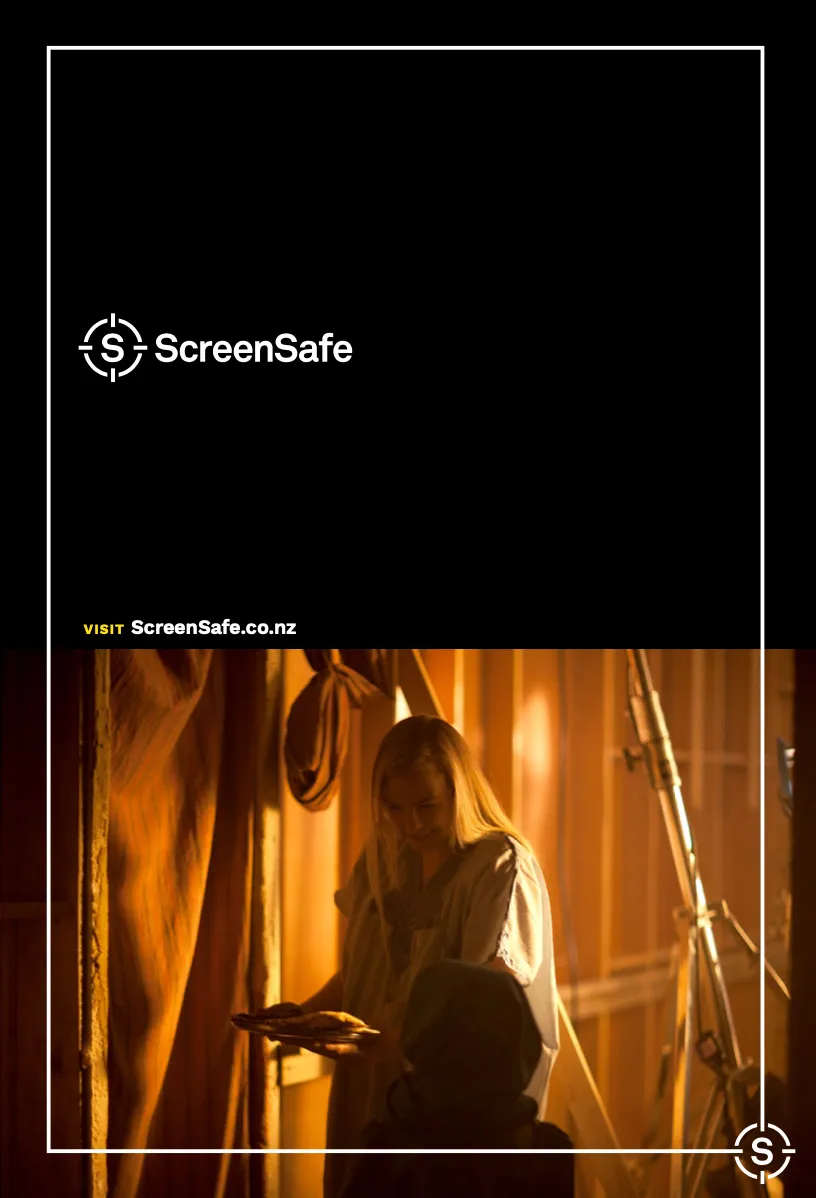
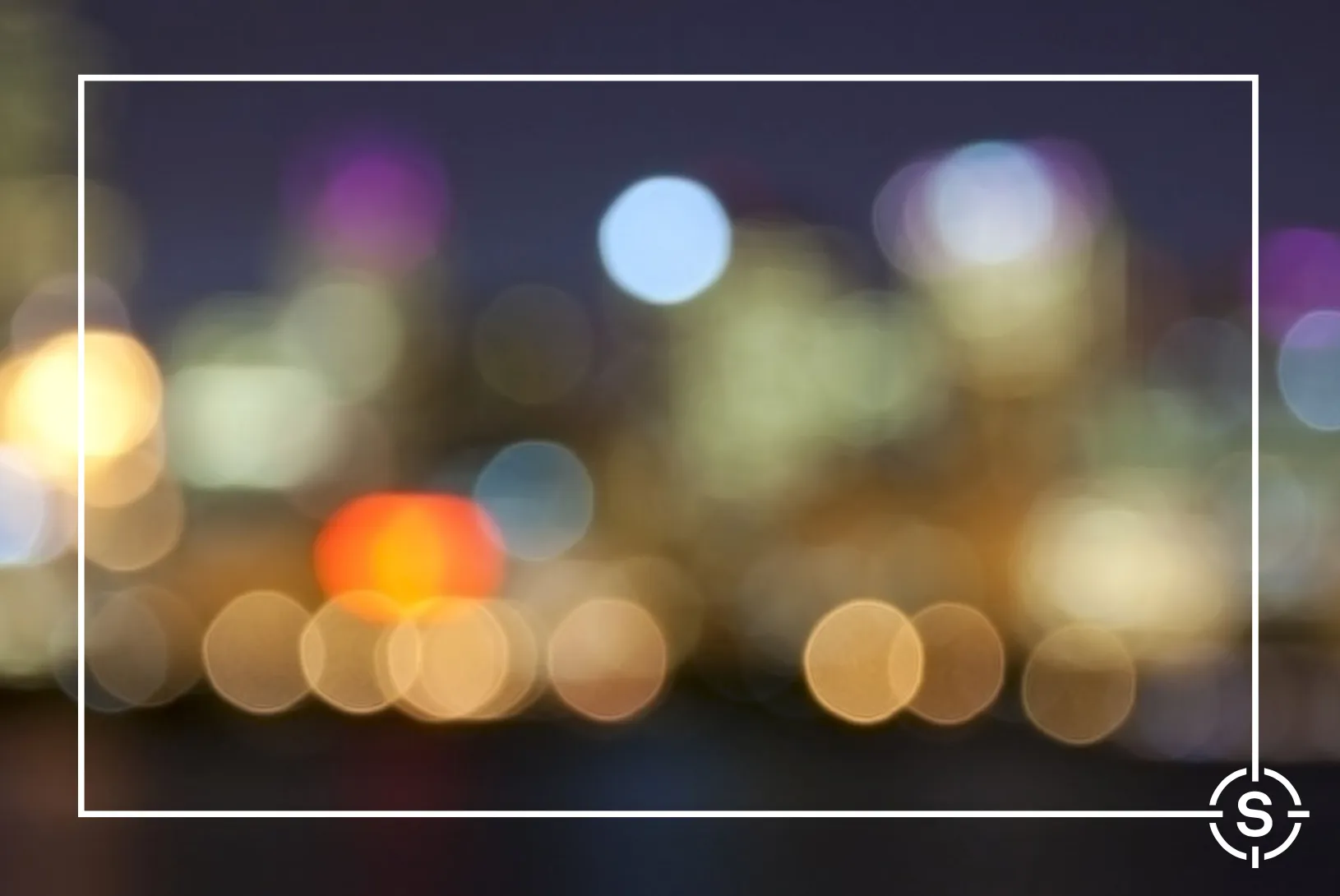
Electrical
Hazardous Substances
Anyone using a hazardous substance should have a thorough understanding of the Health and Safety at Work (HazardousSubstances) Regulations 2017, which set out the rules for work-related activities involving hazardous substances.
The Hazardous Substances Toolbox website also provides comprehensive information on how you can work safely with hazardous substance.
This chapter provides basic guidance and key things for you to consider in relation to working with hazardous substances on a production.
Who needs to read this?
All workers who undertake work with, or work that interacts with, hazardous substances should read and understand the section on ‘minimum responsibilities’ and ‘managing hazardous substances’.
Roles that have specific responsibilities, or influence, over work with hazardous substances should read the section on ‘planning and guidance considerations’ – this includes producers, directors, production managers, line producers, heads of departments, assistant directors and health and safety officers.
Definitions
Hazardous substance means, unless expressly provided otherwise by regulations, any substance —
- with one or more of the following intrinsic properties – explosiveness, flammability, a capacity to oxidise, corrosiveness, toxicity (including chronic toxicity), ecotoxicity, with or without bioaccumulation; or
- which on contact with air or water (other than air or water where the temperature or pressure has been artificially increased or decreased) generates a substance with any one or more of the properties specified above.
MSDS means Material Safety Data Sheets; these provide concise safety and health information about the hazards and safety precautions of the substance and should be available for all products.
Specific Risks
- Explosiveness
- Flammability
- Health effects
- Infection
- Toxicity - both short and long-term effects
*NOTE: Substances may be inhaled, ingested or absorbed into the body. The effect is dependent upon the substance involved and the degree of exposure.
What we need to know about Hazardous Substances
Many hazardous substances are in daily use on a production set. While all hazardous substances can be safely used if proper work methods are adopted, safer, alternative substances and/or work methods should be used instead of using highly hazardous substances where practicable.
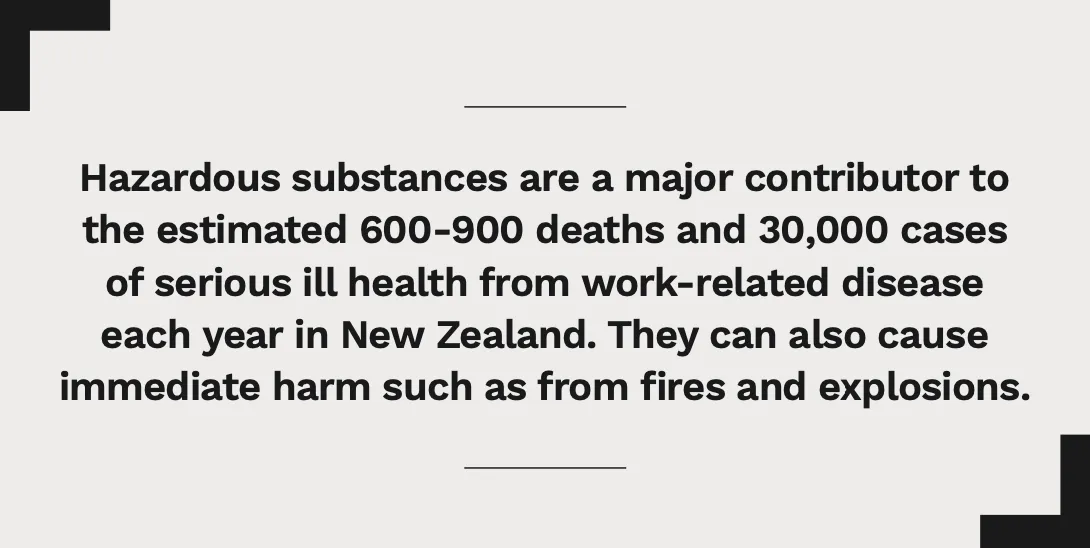
What is a Hazardous Substance?
A hazardous substance is any product or chemical that has explosive, flammable, oxidising, toxic, corrosive or ecotoxic properties.
Explosive: explodes or causes explosion.
Flammable: ignites easily and burns rapidly.
Oxidising: could be gaseous, solid or liquid and can cause or intensify fire and explosion.
Toxic: can harm people if it enters the body through contact, being inhaled or ingested. The effects can range from mild to life-threatening, and can be immediate or long-term.
Corrosive: can cause severe skin burns and eye damage. Ecotoxic: is toxic to the environment.
All hazardous substances should have an MSDS, provided by the supplier of the substance – these provide concise safety and health information about the hazards and safety precautions of the substance.
*See: WorkSafe / What the Hazardous Substances Regulations mean for you
What could go wrong?
Emergencies you need to consider and plan for include:
- a worker being poisoned by ingesting or inhaling a toxic substance;
- a worker being burnt by a corrosive substance;
- a fire caused by flammable or oxidising substances; or
- hazardous substances leaking or spilling from their containers, injuring people and contaminating land and waterways.
*See: WorkSafe / Emergency plans
Certified Handler requirements
Some work with highly hazardous substances must be carried out by a certified handler.
Certified Handlers need to:
- meet certain competency requirements, and
- receive workplace-specific information, training and instruction by or on behalf of the business, and
- obtain a certified handler compliance certificate from a compliance certifier.
You need a certified handler for:
• substances that require a controlled substance licence (CSL), such as most explosives, fumigants and vertebrate toxic agents (VTAs); and
• acutely toxic (6.1A and 6.1B) substances.
*See: WorkSafe / Certified handler requirements
Minimum Responsibilities
Everyone on a screen production who does, or could, work with hazardous substances, should read and understand this section.
All workers must:
- follow all health and safety information, training and instruction they have received;
- must be aware of what personal protective equipment they are expected to provide themselves and what will be provided by the production;
- follow instructions provided by the person in charge of any activity that involves the use of, or is conducted near, hazardous substances; and
- know escape routes when working around or near hazardous substances; if they are unsure of the escape route check with the 1st assistant director to learn the escape route before entering the work area.
Managing Hazardous Substances
Anyone who operates or is responsible for, or has influence over, hazardous substances must read and understand this section, as well as the sections on minimum responsibilities and planning and guidance considerations and responsibilities.
Create an Inventory
First and foremost, it’s important to know what hazardous substances are being stored or used on a production.
- Make an inventory of all the hazardous substances manufactured, used, handled or stored at your workplace including hazardous waste.
- Keep your inventory up-to-date and accurate.
- Make sure your inventory is readily accessible to emergency services workers.
The Hazardous Substances Calculator will help you create an inventory and work out what key requirements you need to meet, based on the hazardous substances you use, handle, manufacture and store at your workplace.
*See: WorkSafe / Inventory
Assess and Manage the Risk
All hazardous substances have a level of risk.
If there is no alternative and it is necessary to use hazardous materials on the production, those responsible for the use of the hazardous substance need to identify all risks associated with the hazard and decide on how to manage the risk by minimising it.
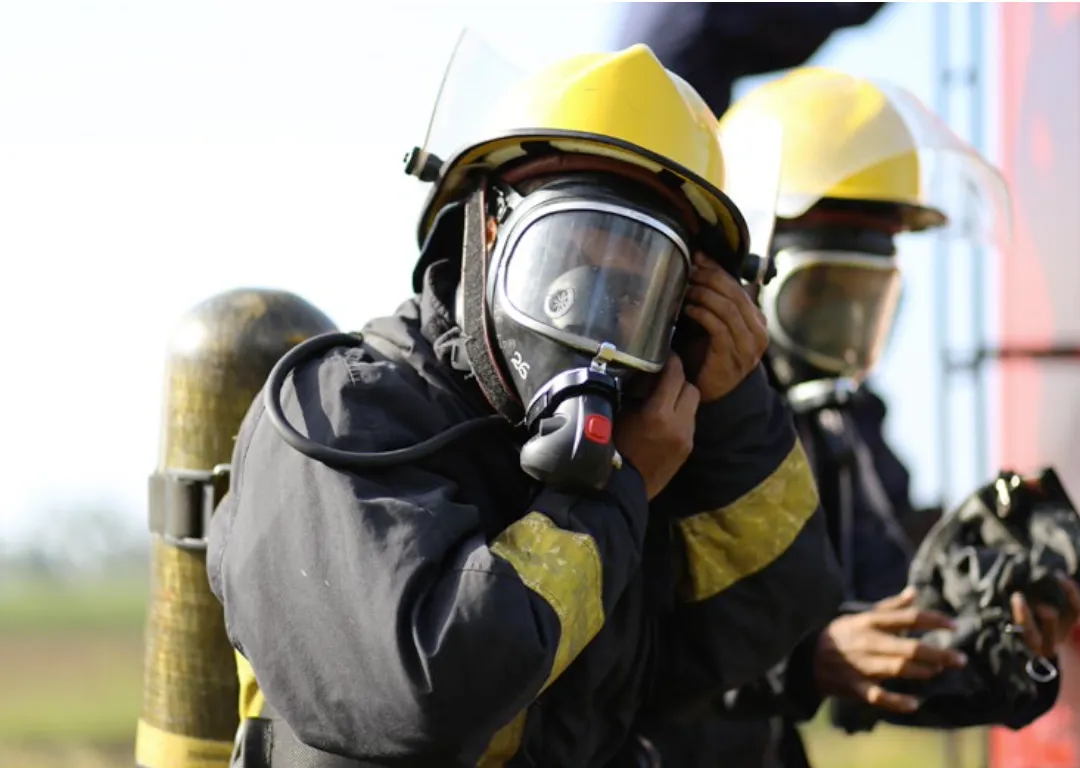
Minimising Risk
If you cannot eliminate the risk, there is a hierarchy of minimisation options.
*See: WorkSafe / What the Hazardous Substances Regulations mean for you
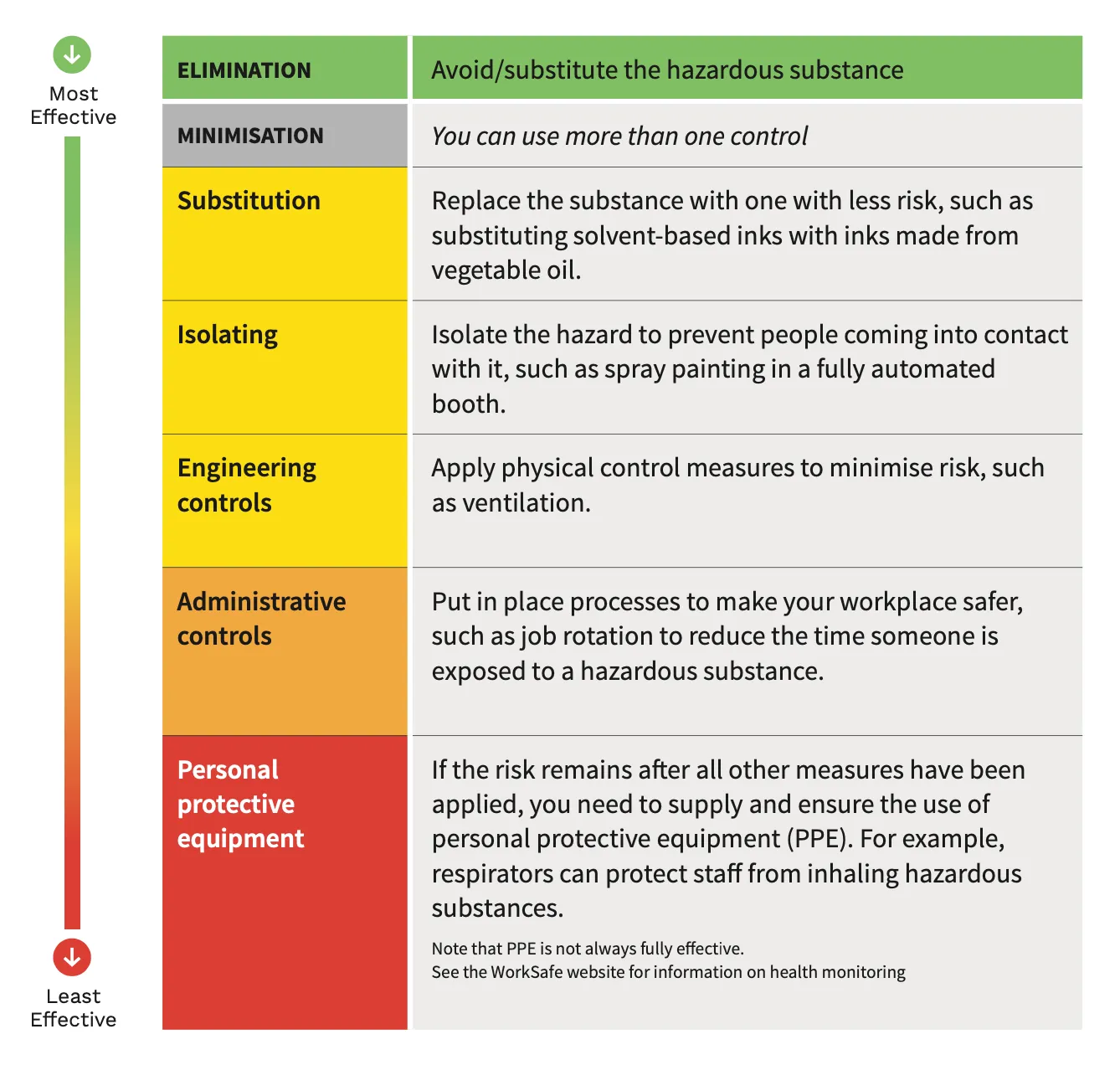
Keeping People Safe
If hazardous substances are used on a production, there are multiple ways you can keep workers and visitors safe.
Inform and Train Workers
Ensure everyone who works with or around hazardous substances has the experience and knowledge to do so safely.
Inform workers of hazardous substances on the production, and the control measures in place during the daily health and safety briefing and place this information on the call sheet.
Label Containers
You need to ensure containers of hazardous substances are always clearly and correctly labelled, this includes:
- substances that have come from a supplier and are therefore already labelled;
- substances that you decant or transfer into a smaller container at your workplace;
- stationary tanks, process containers and transportable containers; and
- hazardous waste.
*See: WorkSafe / Labelling
Install Signs
Place clearly visible signs at entranceways, and on buildings, or in outdoor areas, where substances are used or stored. They should inform people of what hazardous substances are present, the general type of hazard and what to do in an emergency.
*See: WorkSafe / Signs
Store Hazardous Substances Safely
Where and how you store hazardous substances will depend on the type of substance and the amount you have.
The Health and Safety at Work (Hazardous Substances) Regulations 2017 set out the requirements for storing different types, classes and quantities of hazardous substances in different situations.
The MSDS includes handling and storage information about the substance.
*See: WorkSafe / Storage
Plan for an Emergency
If using hazardous substances an emergency plan should be developed, it must:
- address all ‘reasonably foreseeable’ emergencies;
- state any special training needed to deal with an emergency involving each substance;
- include the inventory of hazardous substances present at the workplace;
- include a site plan showing all the hazardous substances locations in the workplace; and
- advise how you will:
- ~ call emergency services
- ~ warn people at the workplace and nearby about the emergency
- ~ advise people how they can protect themselves
- ~ help or treat any one injured in the emergency
- ~ manage the emergency to restrict its effects to the initial area, reduce its severity and if possible, eliminate it.
Fire and Emergency New Zealand (FENZ) can review your plan.
*See: WorkSafe / Emergency plans
Disposal and Recycling
Unused chemicals, and empty chemical containers, are a risk to people, the environment and animals.
You can arrange for unused chemicals to be disposed, or empty containers recycled, through AgRecovery. Information about disposing of products can also on be found on the MSDS.
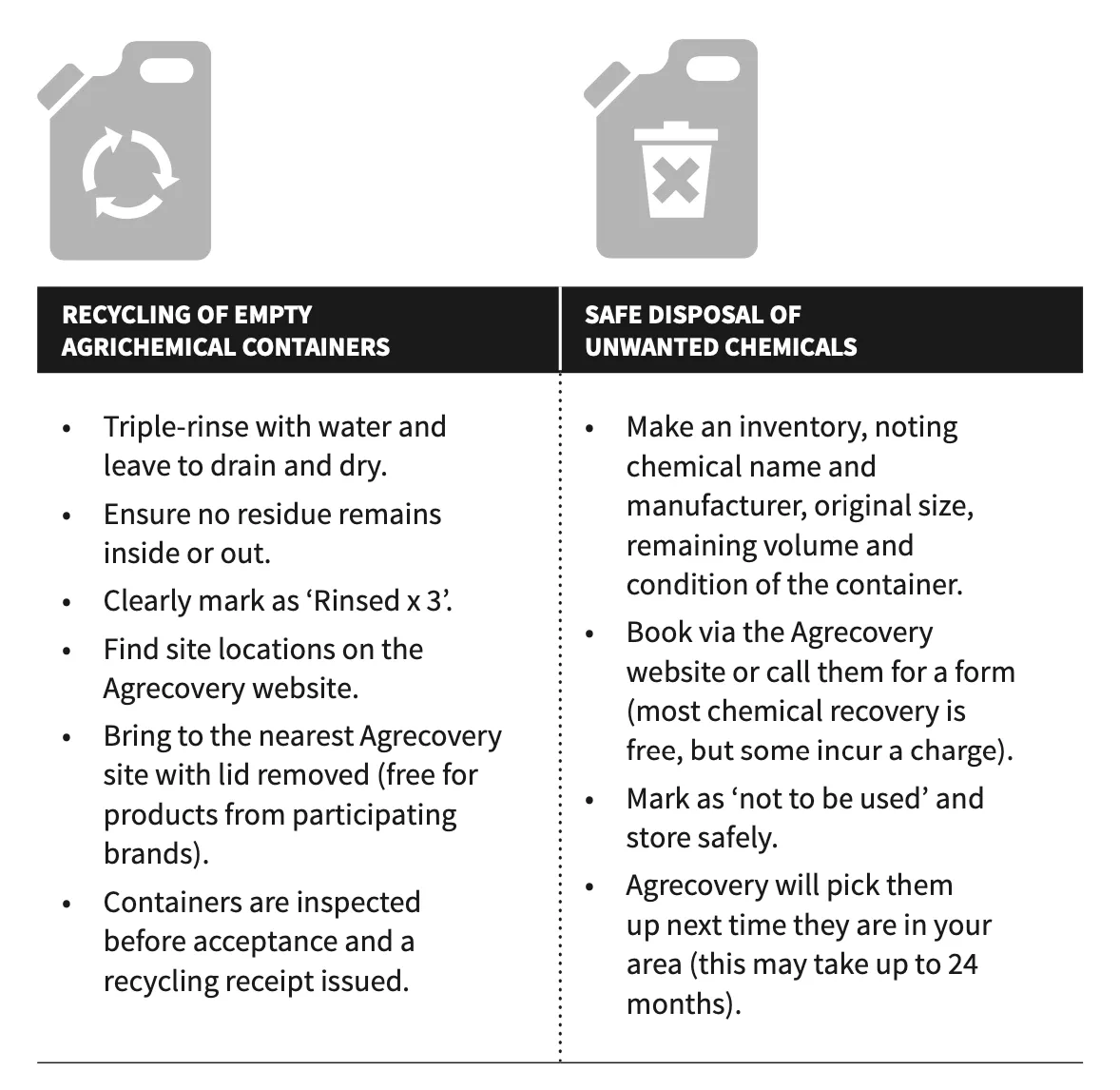
Transport
A certified handler must always be present when explosives are being transported.
Transport of hazardous substances are covered by the relevant transport agency.
Road and rail – the New Zealand Transport Agency
Key points to note:
- Generally, if you're transporting dangerous or hazardous goods, you need a dangerous goods (D) endorsement on your driver licence.
- For transport, dangerous goods are identified with a UN number, a proper shipping name and a diamond-shaped class warning label. Some products also have special marks to warn of hazards that are not indicated by other labels or marks.
- The Land Transport Rule: Dangerous Good 2005 (Rule 45001/1) details how you can transport dangerous goods safely and securely, depending on the nature and quantity of the dangerous goods.
Sea – Maritime New Zealand
Key points to note:
- Controls must be in place to safely manage the hazardous substances.
- An inventory of the hazardous substances you use, handle or store on board must be maintained.
- Anyone who uses or handle hazardous substances must have training to do so.
- The advice on the MSDS must be followed.
- All hazardous substances must be correctly labelled.
- Signs must be displayed to let workers, visitor and emergency service personnel know there are hazardous substances onboard.
Air – Civil Aviation Authority of New Zealand
Key points to note:
- Articles and substances must be properly classified according to a set of standard criteria.
- The packaging used for dangerous goods must meet certain criteria set by the technical instructions.
- The hazards posed by these articles and substances must be identified by markings, package labels and accompanying documentation.
- An airline must have the opportunity to inspect and verify the acceptability of each dangerous goods package as declared by the shipper.
Planning and Guidance Considerations and Responsibilities
Everyone has planning responsibilities for or planning influence over activities that interact with hazardous substances should read and understand this section, as well as the above sections.
This includes funders, the Production Company, Producers, Heads of Department, and Health and Safety Advisors.
Funders
Funders should:
- be assured, through the provision of the production’s health and safety plan, that the funding provided is adequate to provide for competent people to undertake and supervise work with hazardous substances; and
- ensure that all senior contractors have sufficient insurance cover, appropriate to the risk and scale of the work to be undertaken.
Production Company
In pre-production, production companies (likely to have primary responsibility over health and safety on the production) should:
- ensure people who use hazardous substances are competent in their use;
- consider the potential risks associated with hazardous substances when planning and allocating tasks; and
- ensure the potential risks associated are appropriately managed, either eliminating or minimising them.
Producers and Production Managers
As Producers and Production Managers have oversight across the production, they should:
- communicate to all personnel the presence and/or use of hazardous substances;
- provide appropriate information on safety matters should be included;
- ensure workers are provided appropriate personal protective equipment;
- ensure workers are wear appropriate personal protective equipment;
- ensure that emergency and first aid procedures are in place;
- ensure sufficient firefighting equipment is provided and that it is immediately available on set if required; and
- ensure there is a clear access way for emergency and firefighting equipment and vehicles on set.
Heads of Department
As Heads of Department have specific oversight of areas of work that may use hazardous substances for specific task, they should:
- ensure workers using hazardous substances carry the necessary skills, certifications and / or experience;
- ensure hazard identification and risk assessments are undertaken for all activities using hazardous substances, and controls implemented;
- ensure that emergency and first aid procedures are followed;
- ensure personal protective equipment specific for hazardous substance work is provided to, and used by, workers when required;
- communicate to all personnel the presence and/or use of hazardous substances;
- provide appropriate information on safety matters should be included;
- ensure workers are provided appropriate personal protective equipment; and
- ensure workers wear appropriate personal protective equipment.
Health and Safety Officer
The Health and Safety Officer should ensure potential risks associated with hazardous substances are discussed with all cast and crew during health and safety inductions and / or as required if circumstances on the set change.
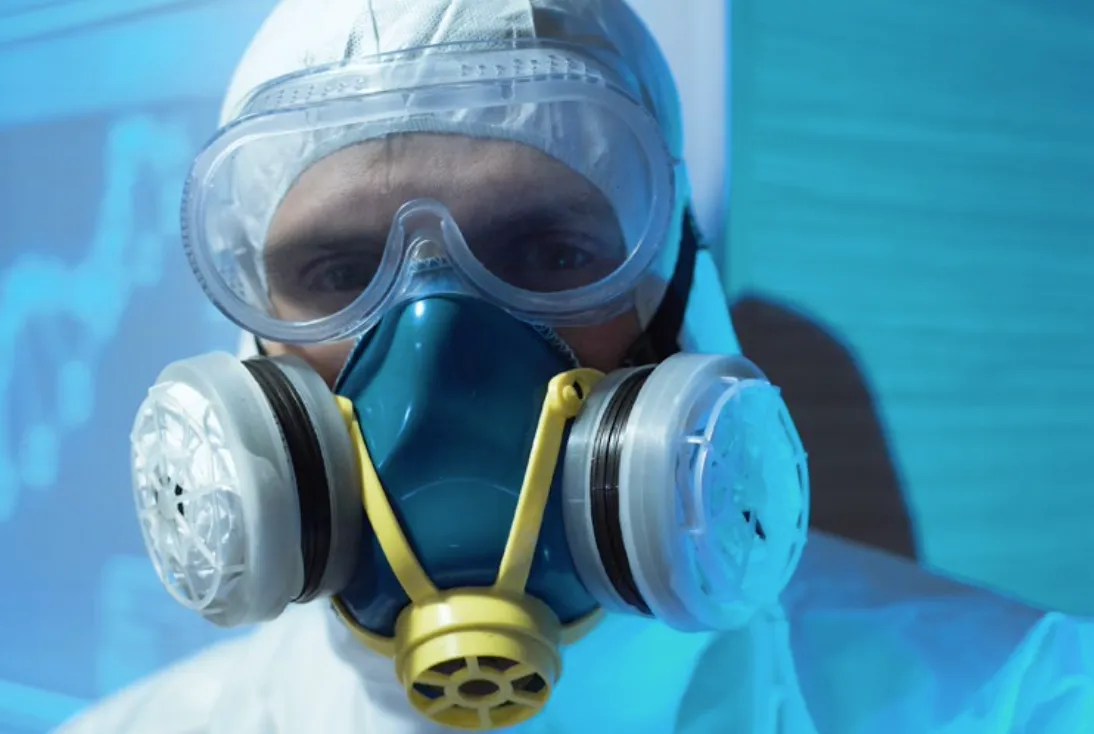
Training and Knowledge
Hazardous substances must only be used by people with knowledge about the substance, its health effects and emergency procedures.
Substances requiring a controlled substance licence (CSL), such as most explosives, fumigants and VTAs, and acutely toxic (class 6.1A and 6.1B) substances, such as certain pesticides and VTAs, need to be handled by a certified handler.
However, in some cases, people who are not certified handlers can handle substances with certified handler requirements, which are outlined in WorkSafe’s quick guide – certified handler requirements.
To check if you need a certified handler in your workplace, enter your substances into the Hazardous Substances Calculator or search the Environmental Protection Authority’s Approved Hazardous Substances with Controls database.
Anyone handling or working with hazardous substances needs to:
- be trained or supervised in safe handling procedures;
- be provided with information and MSDS about the product;
- understand the physico-chemical and health hazards associated with the hazardous substances;
- understand the procedures for the safe use, handling, manufacture, storage and disposal of the hazardous substances;
- ensure their safety, and the safety of others, when using the hazardous substances;
- understand obligations under the Health and Safety at Work (Hazardous Substances) Regulations 2017; and
- know the actions to be taken in an emergency involving the hazardous substances.
Being a certified handler can help fulfil these requirements.
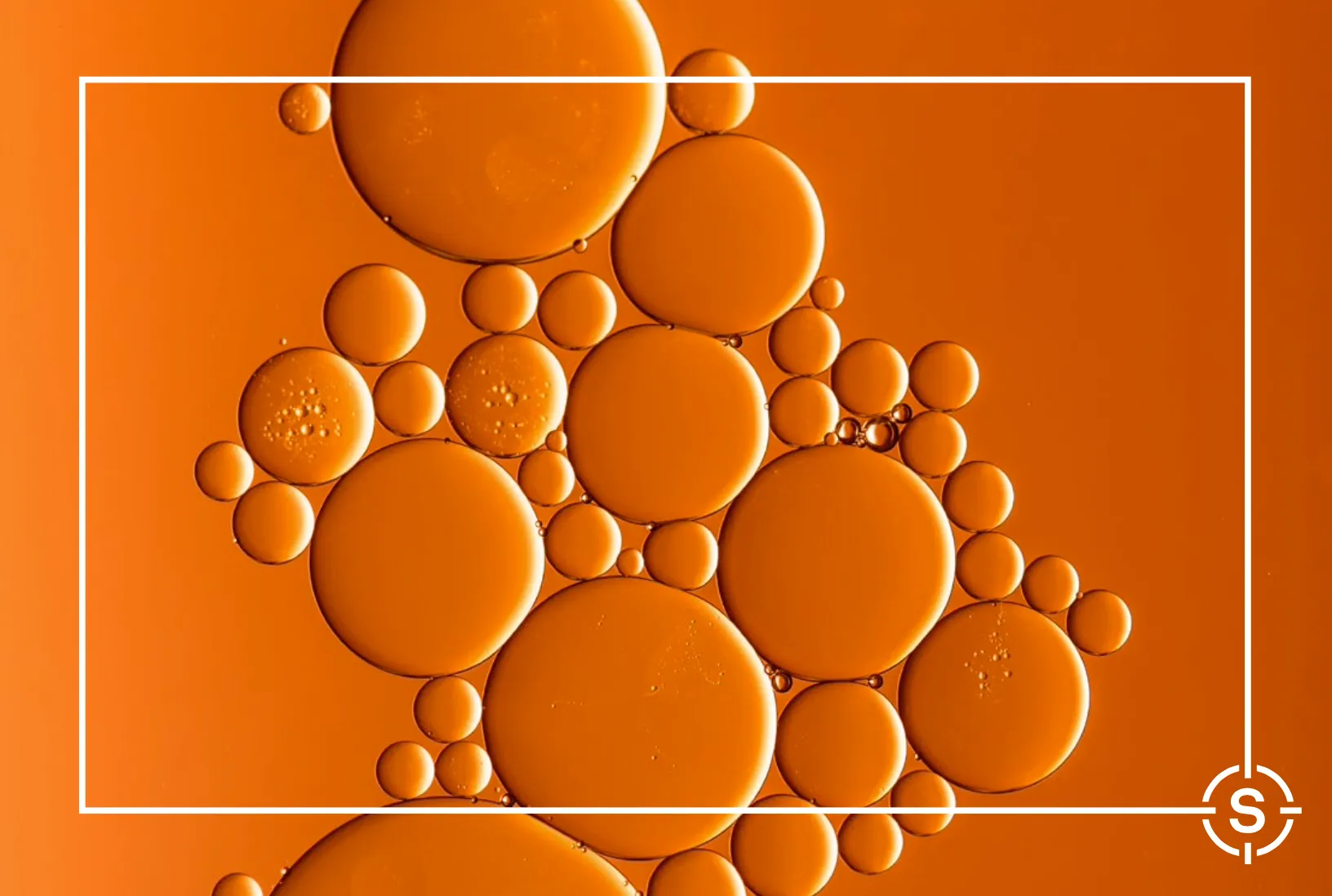
Hazardous Substances
Who needs to read this?
All workers who undertake work with, or work that interacts with, motor vehicles or drive to work should read and understand the section on ‘minimum responsibilities’.
Roles that have specific responsibilities, or influence, over work with motor vehicles should read the section on ‘planning and guidance considerations’ – this includes producers, directors, production managers, line producers, heads of departments, assistant directors and health and safety officers.
Anyone who operates or is responsible for, or has influence over, a motor vehicle must read and understand all sections of this chapter. This includes drivers of Heavy Motor Vehicles/ Goods Service Vehicles of more than two axles or greater than 3500 kilos manufacturer's gross laden weight, and to drivers of any vehicle carrying more than 10 passengers.
Definitions
Action vehicle means any moving vehicle being used as part of a film sequence.
All-terrain vehicle (ATV) means any vehicle that is principally designed for off-road use. They have three or more wheels, an engine capacity exceeding 50ml and a gross weight of less than 1000kg.
Motor vehicle means any powered vehicle or trailer used on or off the road. Tracking vehicle means a vehicle that is used for the mounting of cameras and
other equipment for photography of, or in, a stationary or moving vehicle.
Specific risks
- Being struck by a vehicle
- Crashes between vehicles and with structures and equipment
- Falls from vehicles
- Fatigue
- Fire
- Exhaust fumes
Minimum Responsibilities
Everyone on a screen production who does, or could, work with motor vehicles, or drives to work, should read and understand this section.
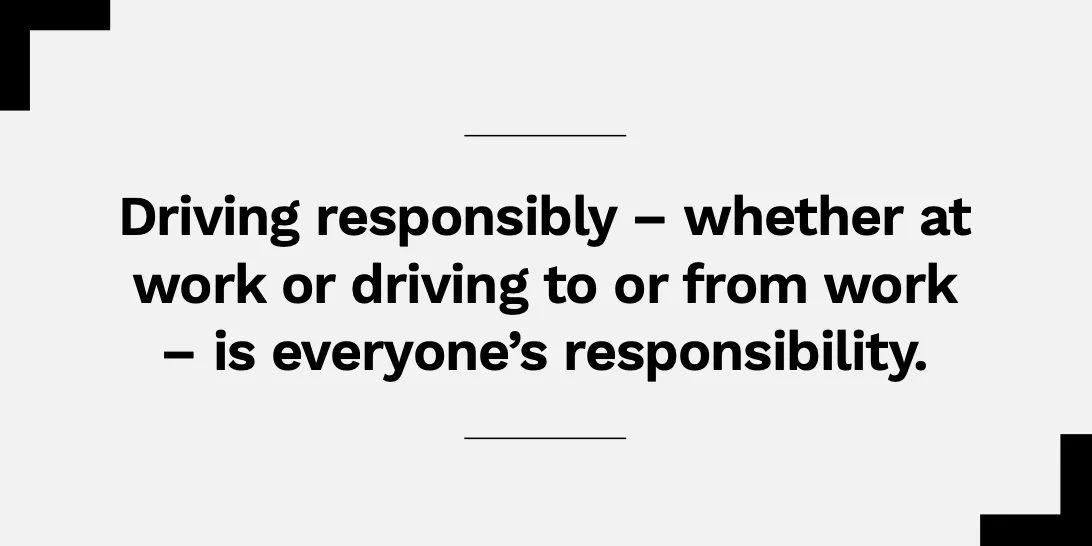
All workers must:
- hold the appropriate license/s for the vehicle/s they drive;
- understand and follow New Zealand laws and regulations relating to motor vehicles and driving;
- understand how fatigue can impact their ability to drive safely and should read the fatigue chapter;
- wear seatbelts, where fitted;
- abide by the alcohol and drugs chapter (link to alcohol and drug chapter); and
- inform the production manager if they lose their license.
Foreign drivers should follow this chapter and can find out more useful information from the NZ Transport Agency.
Planning and Guidance Considerations and Responsibilities
Everyone who has planning responsibilities for or planning influence over activities that interact with motor vehicles should read and understand this section, as well as the minimum responsibilities for everybody.
This includes funders, the Production Company, Producers, persons in charge, and Health and Safety Officers.
Person in charge
The person in charge / those with direct planning responsibilities for or influence over a driver (such as the worker’s superior or the person who hired them) must ensure the driver:
- holds the appropriate license/s for the vehicle/s they drive; and
- abides by the guidelines outlined in the section ‘Responsibilities specific to operating motor vehicles’ below;
- is given, and does not exceed, limitations for driving;
- is given adequate time off; and
- reads and understands the chapter on fatigue.
Funder
Funders should:
- be assured, through the provision of the production’s health and safety plan, that the funding provided is adequate to provide for competent people to undertake and supervise work with motor vehicles.
Production Company / Producer / Production Manager
- Production companies (likely to have primary responsibility over health and safety on the production) must:
- consider the potential risks associated with the use of motor vehicles when planning and allocating tasks;
- ensure the potential risks associated are appropriately managed, either eliminating or minimising them; and
- consider fatigue and workloads involving driving when creating schedules;
- engage competent persons to oversee and undertake work with motor vehicles.
- ensure location and studio driving restrictions are followed – for example a lower speed limit on a studio lot.
Health and Safety Officer
The Health and Safety Officer should ensure potential risks associated with motor vehicles are discussed with all cast and crew during health and safety inductions and / or as required if circumstances on the set change.
Responsibilities specific to operating Motor Vehicles
Anyone who operates or is responsible for, or has influence over, a motor vehicle must read and understand this section, as well as the previous sections, including, but not limited to, drivers of passenger vehicles, Heavy Motor Vehicles and Goods Service Vehicles.
Drivers – all
All drivers must:
- hold the appropriate license/s for the vehicle/s they drive; and
- understand and follow New Zealand laws and regulations relating to motor vehicles and driving – in particular restrictions specific to their type of driver’s license, for example:
- ~learners license;
- ~small passenger service vehicle license;
- ~heavy vehicle license; or
- ~motorcycle license.
All drivers should:
- undertake a safety check of the vehicle and any attachment before each job;
- check the vehicle has a current Warrant of Fitness or Certificate of Fitness or Permit to Operate;
- check heavy vehicles’ road user charges (RUC) are up-to-date;
- read and understand the section below on tracking vehicles, action vehicles, and/or all-terrain vehicles if relevant to their role as a driver;
- not exceed legal, or recommended, driving limitations; and
- have adequate time off duty.
Person in charge
The person in charge of those operating motor vehicles – such as a direct supervisor or the person who hired the worker – on or around the production should ensure:
- drivers have adequate time off duty; and
- where possible, that drivers do not exceed driving limitations.
Driving Limitations
It is recommended that all drivers on a production follow the same rules provided by the New Zealand government to drivers of heavy motor vehicles / good service vehicles and small passenger service vehicles.
This means, in any 24-hour period drivers:
- should not drive for more than 11 hours;
- should not drive for more than 5.5 hours continuously, and the minimum break is half an hour;
- should not be at work or be on duty for more than 14 hours
- ~~this includes all working and driving time combined, whether paid or unpaid; "on duty" is defined as any time required to carry out the requirements of the job and includes any other paid employment in which a person is engaged;
- should be off-duty for at least nine hours continuously; ie: from the time a person finishes work at the end of the working day to the time a person starts back at work.
NOTE: There are substantial fines and disqualification penalties for abuse of these rules and they may be imposed on both the driver and the employer.
Tracking Vehicles
Drivers of tracking vehicles should understand and ensure recommendations in this section are followed.
Vehicle-to-Vehicle Shoots
When performing vehicle-to-vehicle shoots, the vehicles should be driven by a driver competent in close moving vehicle driving.
Restricted Access to the Vehicle and Safe Loading
The vehicle should be restricted to essential personnel only and the loading shall be within the safe loading limits of the vehicle.
There should no more people in the vehicle than there are seats with seatbelts.
Public Roads
When filming on or adjacent to public roads a Traffic Management Plan (TMP) must be applied for and approved by the roading authority responsible for
that section of road. TMP's can only be obtained through a registered traffic management company. It is recommended that a traffic management company familiar with filming and events is contracted to provide these services.
When filming on or adjacent to a public road where the driving public may be distracted, the Police should be notified. Adequate warning should be given to other traffic of a tracking vehicle operating. The Traffic Management Company notifies Police if necessary, not the film company.
If on an open road, the overall dimensions of the vehicle should not exceed the dimensions set out by the NZ Transport Agency.
Traffic Controller
When filming on or adjacent to public roads, a designated traffic controller must be engaged, likely by the locations manager, to be responsible for carrying out temporary public traffic control duties as required.
The traffic controller:
- must use appropriate safety equipment and clothing; and
- has the responsibility to stop a shoot if the crew are operating outside of the approved condition of the TMP
Mounting Equipment on the Vehicle
Any equipment attached to a vehicle that is to be driven on a public road must be included in the TMP (see above) and approved of in advance by the issuing authority.
Equipment mounted on the vehicle must be firmly attached to the vehicle.
If using lamps or other equipment running off 230 volt power supply (mains, generator or invertor), lamps must comply to relevant New Zealand regulations and the chapter on electrical safety should be read and followed.
Any rigging on a vehicle must be undertaken by a competent person.
Equipment rigged inside or outside of a vehicle should be secured so as to not harm occupants in an accident.
NOTE: that rigging to outside and/or inside of vehicle may make vehicle safety devices inoperable or more dangerous in case of an incident.
Towing Weight Limitations
The manufacturers limitations on the maximum weight being towed by a vehicle should be complied with.
Safety in Adverse Conditions
Extra consideration should be given to the safety of personnel working on such vehicles in adverse conditions.
Communication between Traffic Controller and Driver
The 1st assistant director or person with delegated responsibility should ensure that adequate communication with the driver and traffic controller is established before any driving takes place.
Warning of Movement of Vehicles
Warning of the movement of vehicles should be given to all crew and cast members in the immediate vicinity of the vehicles.
Dry Run and Authority to Abort
A "dry run" or "walk through" of any action should be conducted prior to rehearsal or filming with all personnel involved present. An understanding of any intended action, possible deviations and authority to abort, should be made clear to all concerned.
Action Vehicles
The appropriate person in charge, for example the stunt or vehicle coordinator, must ensure action vehicles:
- are only be used under the control of a competent person; and
- whether independently mobile or not, are appropriate for the task for which it is to be used.
All-Terrain Vehicles
All-terrain vehicles (ATVs) include quad bikes, smaller ‘side-by-sides’ and amphibious vehicles.
On Road
When using ATVs on roads, drivers, and the person in charge, must ensure:
- the ATV is registered and licensed;
- the ATV has a current warrant of fitness (except if used as a farm vehicle);
- the driver holds a current New Zealand driver licence;
- the manufacturer’s recommendations for passengers and loading are followed
- ~~ there should only ever be one person on a quad bike; and
- the driver, and any passengers, wears an approved safety helmet.
Off Road
An ATV that is never used on a road does not need to be registered or licensed.
When using ATVs off roads, drivers, and the person in charge, must ensure:
- the manufacturer’s recommendations for passengers and loading are followed
- ~~there should only ever be one person on a quad bike; and
- the driver, and any passengers, wear an approved safety helmet.
For more information about ATV requirements visit the NZ Transport Agency website.
Recommended Reading
- Quads bikes and ATVs, NZTA
- Safe filming and recording in, from and around vehicles, HSE
- Vehicles: recording in, from and around, BBC
- Guidelines to filming on the move, Metropolitan Police
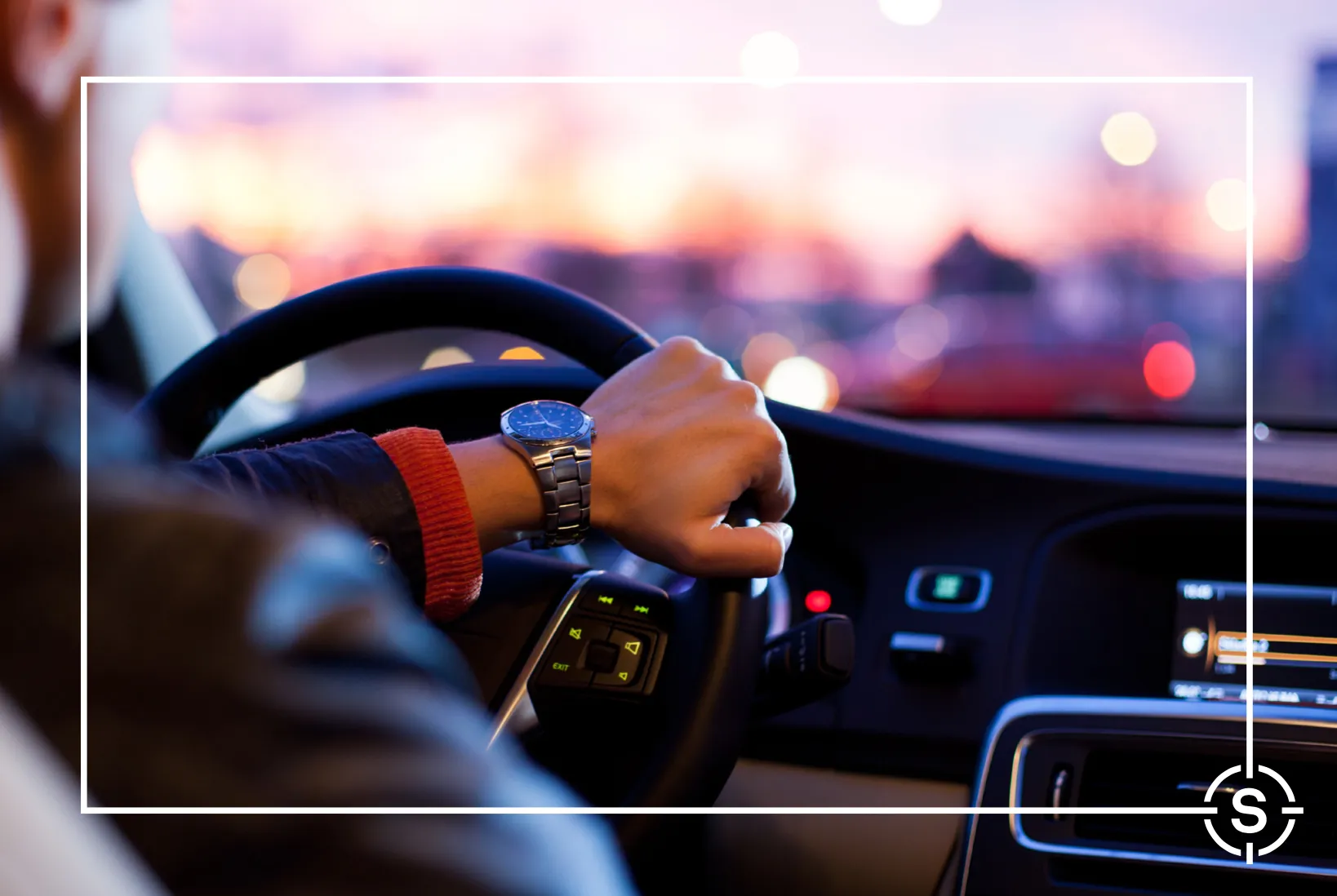
Motor vehicles – Restrictions
Noise Management
This chapter provides guidance in relation to noise, and is primarily based on New Zealand legislation and guidance issued by WorkSafe NZ.
Who needs to read this?
All workers who undertake tasks where they are, or could be, exposed to excessive noise should read and understand the section on ‘minimum responsibilities’.
Roles that have specific responsibilities, or influence, over workers who are, or could be, exposed to excessive noise should read the section on ‘planning and guidance considerations and responsibilities’ – this includes producers, directors, production managers, line producers, heads of departments, assistant directors and health and safety officers.
Definitions
Audiometry6 means the measurement of the hearing threshold level of a person by means of a bilateral pure tone air conduction threshold test.
Excessive noise, for the purpose of this document, is noise that is at or above the following levels—
~(1) eight-hour equivalent continuous A-weighted sound pressure level, LAeq,8h of 85 dB(A); and
~(2) a peak sound pressure level, L-peak, of 140 dB —whether or not the individual is wearing a personal hearing protector; or
~(3) if the threshold is lower, the levels defined in the Health and Safety at Work 2016 Regulations. Note: these Regulations are due to be updated and the noise threshold may be lowered.
Hearing protector means a device or pair of devices that have been tested to an appropriate national or international standard and classified (or graded) by a suitably equipped and independently audited laboratory with full trace ability to National Standards. Such a device is worn by a person or inserted in the ears of a person to protect that person from exposure to noise.
Impulse noise means noise consisting of a single pressure peak, or a sequence of such peaks, or a single burst with multiple pressure peaks, or a sequence of such bursts.
Noise means any sound which is present in the place of work whether it is wanted or not wanted, and includes sound energy of any frequency, whether or not capable of being perceived by the unaided human ear.
Noise induced hearing loss is hearing loss that occurs due to excessive noise exposure; it can be identified by deterioration in hearing, a loss excessive for age, or a noise pattern discovered during audiometric testing.
What we need to know about noise
Excessive noise, both short but extremely loud noise (impulse noise) and prolonged continuous noise, can cause noise induced hearing loss.
Exposure to excessive noise can also trigger workplace stress, causing anxiety or psychological harm, as well as headaches, fatigue and decreased concentration, increasing the risk of accidents. Excessive noise and noisy processes are also often associated with vibrations, which can impact a worker's health.
Excessive noise exposure can also prevent people from hearing alarms or warning signals, limiting awareness and potentially leading to avoidable accidents.
How can I tell what excessive noise is?
Daily exposure to noise above 85 decibels (dBA) will damage hearing; however, 85dBA might not mean a lot to most people.
Excessive noise, or a noise hazard, probably exists if:
- you have difficulty understanding what's being said one metre away;
- you have ringing in your ears (tinnitus) after exposure to the noise;
- or your hearing seems muffled after leaving a noisy area.
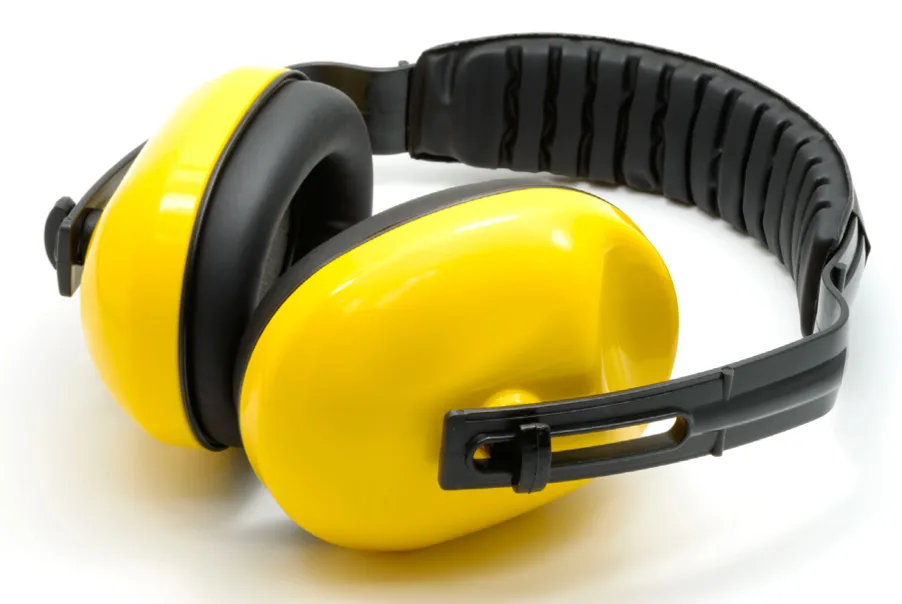
Example of noise levels are outlined below:
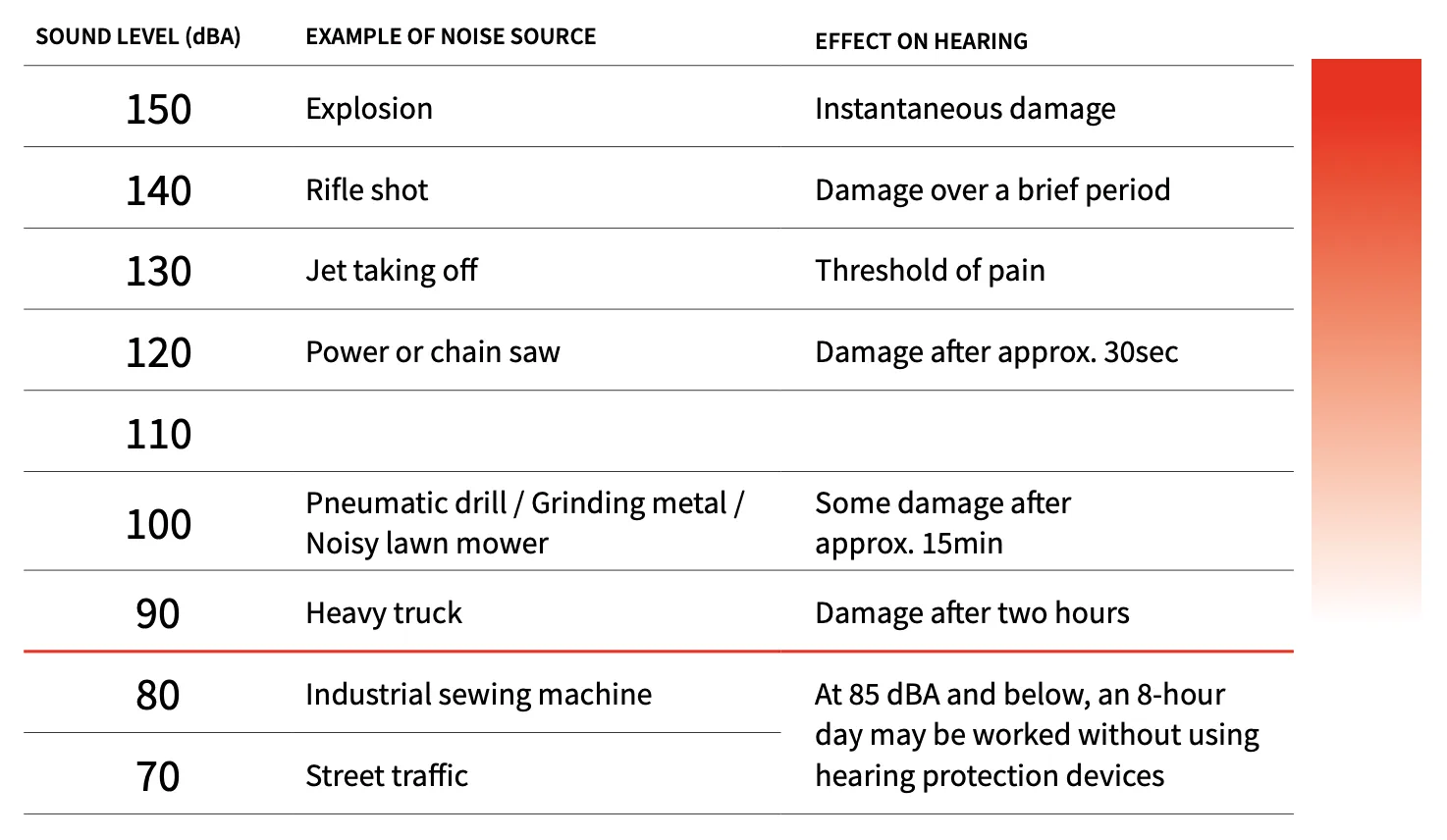
Minimum responsibilities – everyone!
Everyone who undertakes tasks where they are, or could be, exposed to excessive noise should read and understand this section, as well as the section above on ‘what we need to know about noise’.
Anyone who is responsible for, or has influence over, workers who are, or could be, exposed to excessive noise should also read and understand the following section on ‘planning and guidance considerations and responsibilities’.
All workers should:
- understand the risks associated with working in noisy environments;
- follow all procedures and controls put in place to keep themselves and others safe when working in noisy environments;
- use personal hearing protective devices when required, and ensure they are worn correctly;
- read the section later in this document on personal hearing protective devices;
- understand the noisy activities outside of work that can negatively impact on their hearing, such as listening to loud music or undertaking noisy tasks like mowing the lawn or using power tools at home; and
- advise their supervisor or the health and safety officer if they are concerned about the level of noise they, or others, are exposed to.
* See the Hearing Protection Guidebook from Worksafe
Planning and guidance considerations and responsibilities
Anyone who is responsible for, or has influence over, workers who are, or could be, exposed to excessive noise should also read and understand this section, as well as the minimum responsibilities for everyone.
This includes the production company, producers, directors, line producers, heads of departments, assistant directors and health and safety officers, who must consult, cooperate and coordinate with other PBCUs whose work may create, or be impacted by, excessive noise.
Everyone who is responsible for, or has influence over, an activity or task which creates, or is impacted by, excessive noise should:
- consider the risks associated with noise when planning and allocating tasks; and
- manage the risks associated with excessive noise, either eliminating or minimising them.
Identifying excessive noise
Everyone who is responsible for an activity or task in relation to the production should consider the risks associated with excessive noise.
Preliminary Noise Assessment
A preliminary noise assessment is often called a walkthrough survey. It is a screening tool, which will help identify probable or possible excessive noise and should highlight which tasks, processes or areas in the workplace require a detailed noise assessment.
Anyone can undertake a preliminary noise assessment – see appendix A below for an example of a checklist.
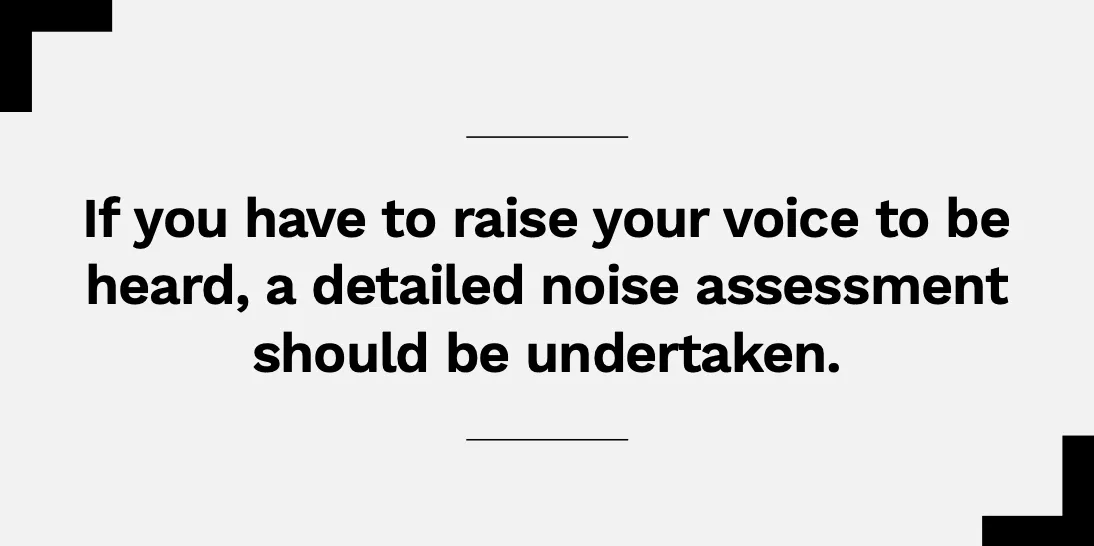
Detailed Noise Assessment
A detailed noise assessment will determine if the workplace contains noise that exceeds the exposure limits, and is required when:
- complex noise sources are present;
- if there is doubt over the noise levels – raised by the PCBU or workers; or
- if a preliminary noise assessment raises doubt over the noise levels.
A detailed noise assessment will:
- quantify the amount of noise workers are exposed to;
- help identify the noise source;
- assist in developing control solutions; and
- determine if hearing protection devices are required.
A detailed noise assessment must be undertaken by a competent person.
Further information can be found in Management of noise in the workplace - Approved Code of Practice (ACOP).
Hearing conservation programme
As soon as a PCBU is aware that workers are being exposed to noise that exceeds exposure limits, they must put in place a hearing conservation programme, which includes determining if hearing protection devices and hearing protection areas are required.
For more information about what needs to be considered as part of a hearing conservation programme refer to the Noise in the workplace – Approved Code of Practice (ACOP).
Hearing Protection Areas
Hearing protection areas are workspaces that have, or may have, excessive noise, where hearing protection devices must be worn, even if a worker or visitor is only in the area for a short amount of time.
These areas must be identified, with the areas and machinery concerned clearly labelled. The PCBU may wish to put up signs.
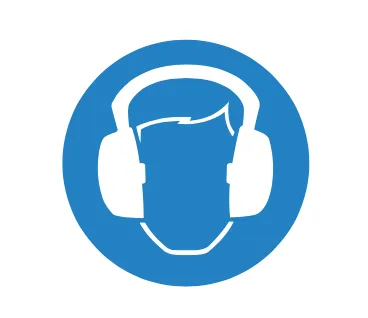
If signs are not practicable, the PBCU must work with workers to come up with other ways of informing both workers and visitors on set that they must wear hearing protection devices. This could include:
- warning notices;
- instructions on call sheets or during inductions; or
- specific supervision in areas with excessive noise.
The requirements for hearing protector areas are detailed in clause 10 Hearing protector areas of AS/NZ 1269.3
or you can read about them in part 6.4 (pg 23-24) of Approved Code of Practice (ACOP).
Managing the risk
Elimination is the most effective control method; you do this by completely removing or avoiding the possibility that someone will be exposed to excessive noise – 85dBA a day or a peak sound pressure level, Lpeak, of 140 dB.
If complete elimination is not reasonably practicable, you must consider ways to minimise the risk so workers are not exposed to excessive noise.
There are two primary ways to minimise, or control, excessive noise – at the source or by isolating either the source or the worker.
You can control the source of the noise by:
- purchasing equipment with the lowest noise rating;
- ensuring that, where reasonably practicable, machinery is installed with vibration isolators to reduce noise; or
- ensuring that equipment is properly maintained and operated.
Controlling noise at the source is best achieved at the planning stage; you can do this by:
- increasing the distance between the noise source and the exposed person;
- placing barriers between the noise source and the exposed person; or
- decreasing the time the at-risk person is exposed to the noise.
If you cannot reduce noise exposure to less than 85dBA a day, the final option is to minimise the risk using suitable hearing protection.
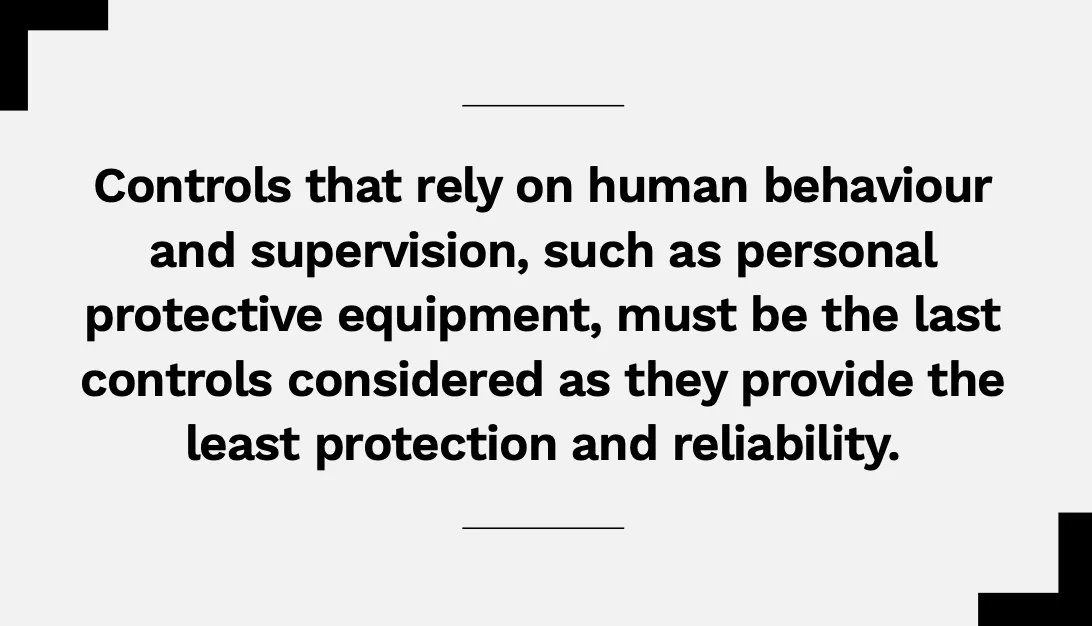
Hearing protection devices
If you cannot reduce the noise to a safe level for workers, you must ensure workers have suitable hearing protection devices (HPDs); the worker is responsible for using them appropriately.
Areas where HPDs must be worn must be designated hearing protection areas and, where practicable, signposted indicating that HPDs must be used.
The main types of HPDs are ear muffs and earplugs; either type can provide effective protection provided it makes an airtight seal in (plugs) or around (muffs) your ear.
The head of department, or equivalent supervisor:
- must ensure all HPDs are manufactured to a recognised Standard and must be the correct grade for the noise level encountered;
- should let the worker choose what HPD to use, providing it gives adequate protection;
- should ensure HPDs are clean and in a good state of repair.
It is important that hearing protectors fit correctly.
For more information about choosing and maintaining HPDs refer to the Noise in the workplace - Approved Code of Practice (ACOP).
See also - Hearing Protection (Worksafe booklet)
Training and Education
All workers should be trained in the selection, fitting, use, care and maintenance of HPDs.
Health and safety inductions should include an explanation about the risk that removing HPDs can have to an individual’s hearing.
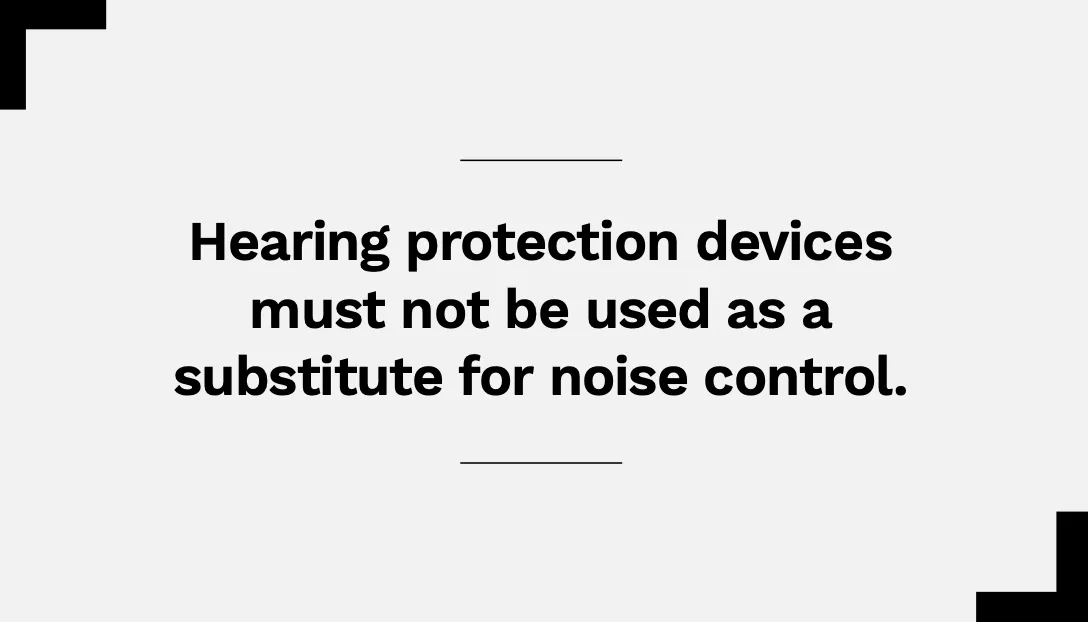
Monitoring the risk
During the production, workers’ exposure to noise should be monitored to ensure they are not being exposed to excessive noise.
If noise does exceed exposure limits, the PCBU must put in place a hearing conservation programme and may consider carrying out audiometric testing.
For more information refer to the Noise in the workplace - Approved Code of Practice (ACOP).
Funders
Funders should:
- be assured, through the provision of the production’s health and safety plan, that the funding provided is adequate to provide HPDs.
Production Company
In pre-production, production companies (likely to have primary responsibility over health and safety on the production) should:
- ensure workers’ exposure to noise to monitored; and
- ensure a hearing conservation programme is put in place.
Producer / Line Producer / Production Manager
As Producers and Production Managers have oversight across the production, they should:
- consider the potential for exposure to excessive noise when planning and allocating tasks;
- ensure the potential for exposure to excessive noise is either eliminated or minimised;
- ensure workers’ exposure to noise to monitored;
- ensure a hearing conservation programme is put in place;
- ensure information about hearing protection areas and the requirement for HPDs is included on daily call sheets.
Director
Directors should:
- consider the potential for exposure to excessive noise when planning and allocating tasks; and
- ensure the potential for exposure to excessive noise is either eliminated or minimised.
Heads of Department
Heads of Departments should:
- consider the potential for exposure to excessive noise when planning and allocating tasks;
- ensure the potential for exposure to excessive noise is either eliminated or minimised;
- ensure information about hearing protection areas and the requirement for HPDs is discussed at team meetings;
- let the worker choose what HPD to use, providing it gives adequate protection; and
- ensure HPDs are clean and in a good state of repair.
They must also ensure all HPDs are manufactured to a recognised Standard and are the correct grade for the noise level encountered. See the Approved Code of Practice.
Assistant Director/s
The Assistant Director/s should:
- ensure risks associated with excessive noise are discussed with all cast and crew during health and safety inductions and / or as required if circumstances on the set change; and
- report incidents of noise-related injury – notifiable event.
Health and Safety Officer
The Health and Safety Officer should:
- ensure risks associated with excessive noise are discussed with all cast and crew during health and safety inductions and / or as required if circumstances on the set change;
- explain the risk that removing HPDs can have to an individual’s hearing; and
- report incidents of noise related injury – notifiable event.
References
- Health and Safety in Employment Regulations 1995
- Occupational Health and Safety Service, Department of Labour (now WorkSafe New Zealand); A Message to Employers on Preventing Hearing Loss
- Occupational Health and Safety Service, Department of Labour (now WorkSafe New Zealand); Management of noise in the workplace – Approved Code of Practice (ACOP)
- Occupational Health and Safety Service, Department of Labour (now WorkSafe New Zealand); Management of Noise at Work - Control Guide (1996)
- ACC - Occupational Noise Levels
Appendix 1: preliminary noise assessment checklist
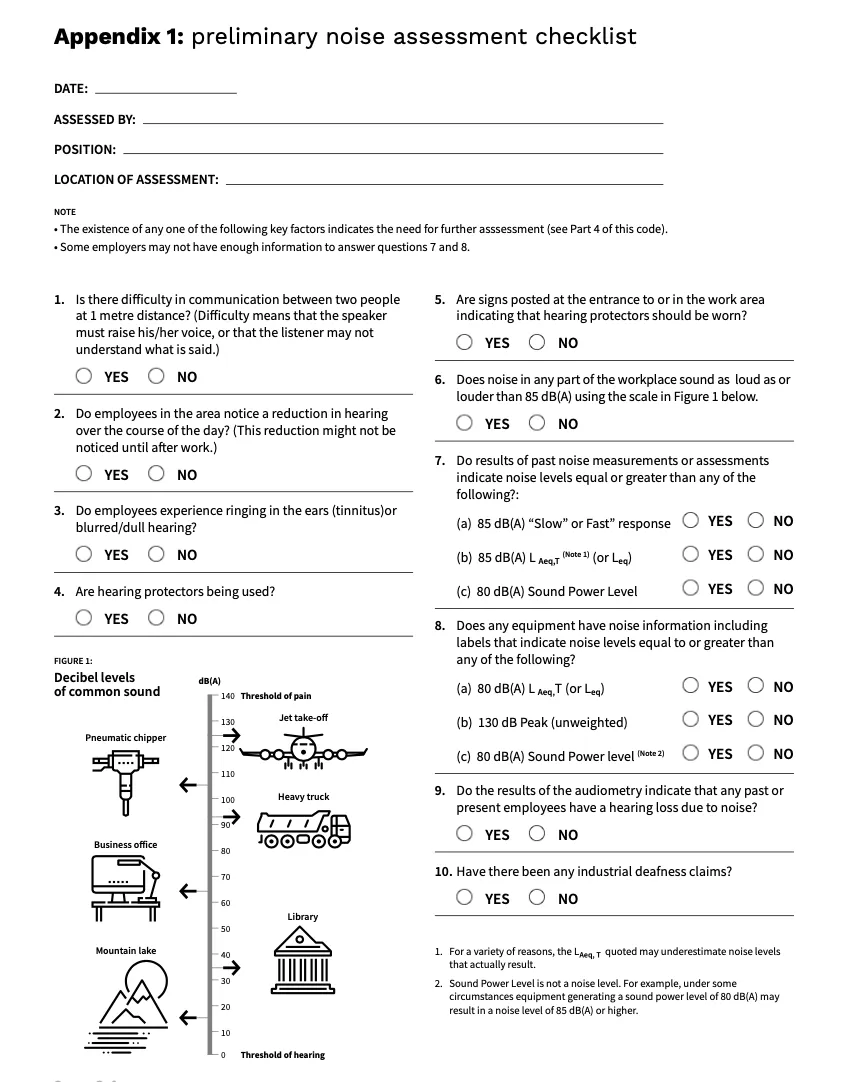
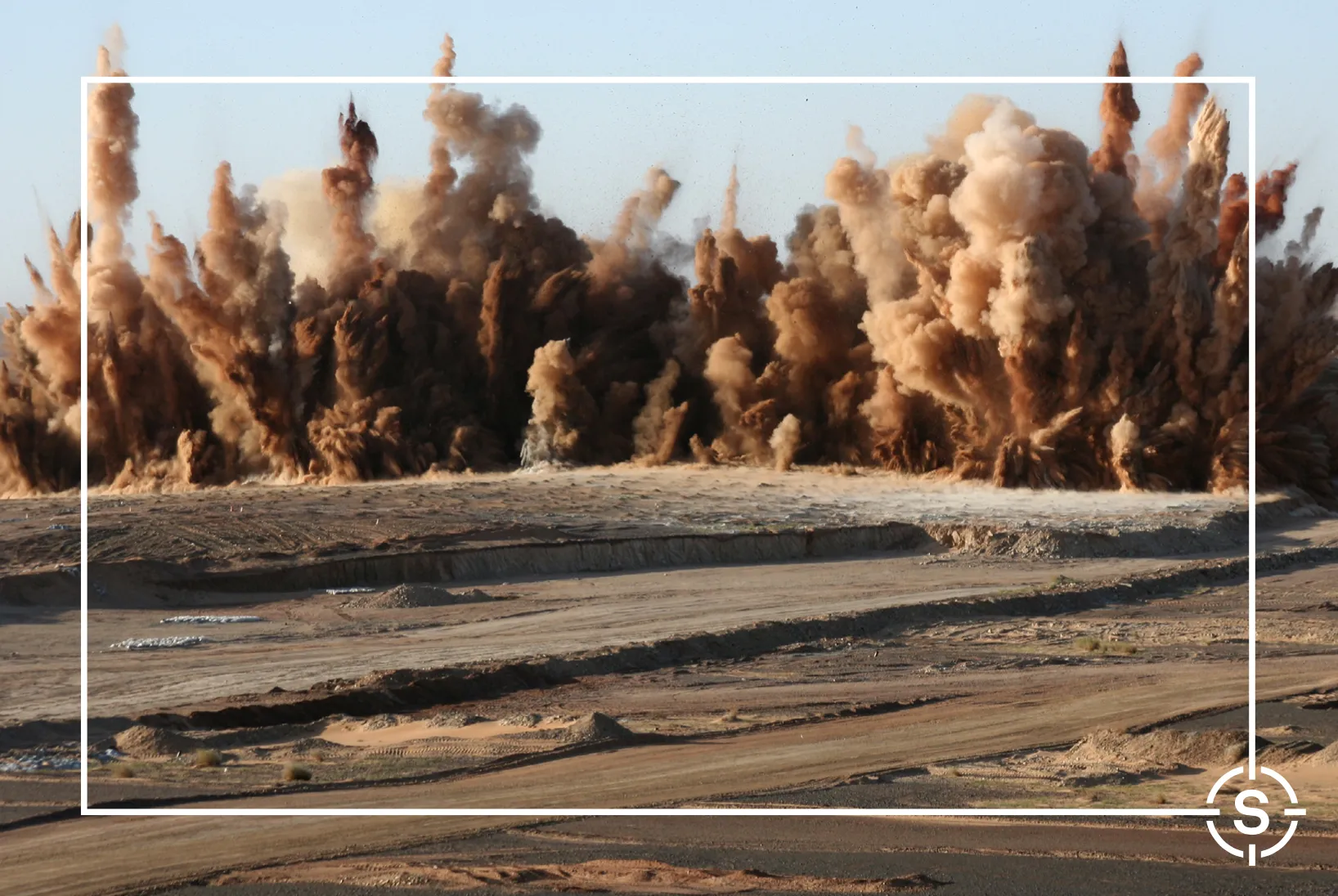
Noise Management
Rigging
This chapter relates to the chapter on working at heights and provides guidance on using rigging on a production set. It is primarily based on New Zealand legislation and guidance issued by WorkSafe NZ.
Who needs to read this?
All workers who use rigging equipment should read and understand the section of minimum responsibilities.
Roles that have specific responsibilities over setting up and managing rigging equipment should read and understand the planning and considerations section – this includes Producers, Directors, Production Managers, Heads of Departments, Assistant Directors and Health and Safety Officers.
What does rigging include?
Rigging on a production set includes:
- the use of mobile powered cranes and elevating equipment, excluding camera cranes;
- camera rigs including car rigs;
- lighting rigs including soft boxes for night shooting;
- construction rigs for sets; and
- scaffolding, which is covered in a separate section.
Definitions
Mobile powered cranes and elevating equipment includes but is not limited to cherry pickers, scissor lifters and mobile cranes; it excludes camera cranes, which are covered with in a separate section: Camera - cranes.
What risks do I need to look out for?
- Crane tipping over
- Electric cables and wires
- Incorrect assembly
- Overhead obstructions
- Struck by crane
- Structural collapse of crane
- Wind
Minimum Responsibilities for Rigging
Everyone who undertakes tasks using rigging, including mobile-powered cranes and elevating platforms, should read and understand the section.
Workers should:
- only operate the equipment if they are competent;
- only operate the equipment in accordance with the operating instructions and appropriate codes of practice;
- ensure the safe working load of equipment is not exceeded;
- wear a safety harness where directed;
- use seats provided where practical;
- fill out log books supplied with machinery; and
- understand the fundamentals of safe rigging.
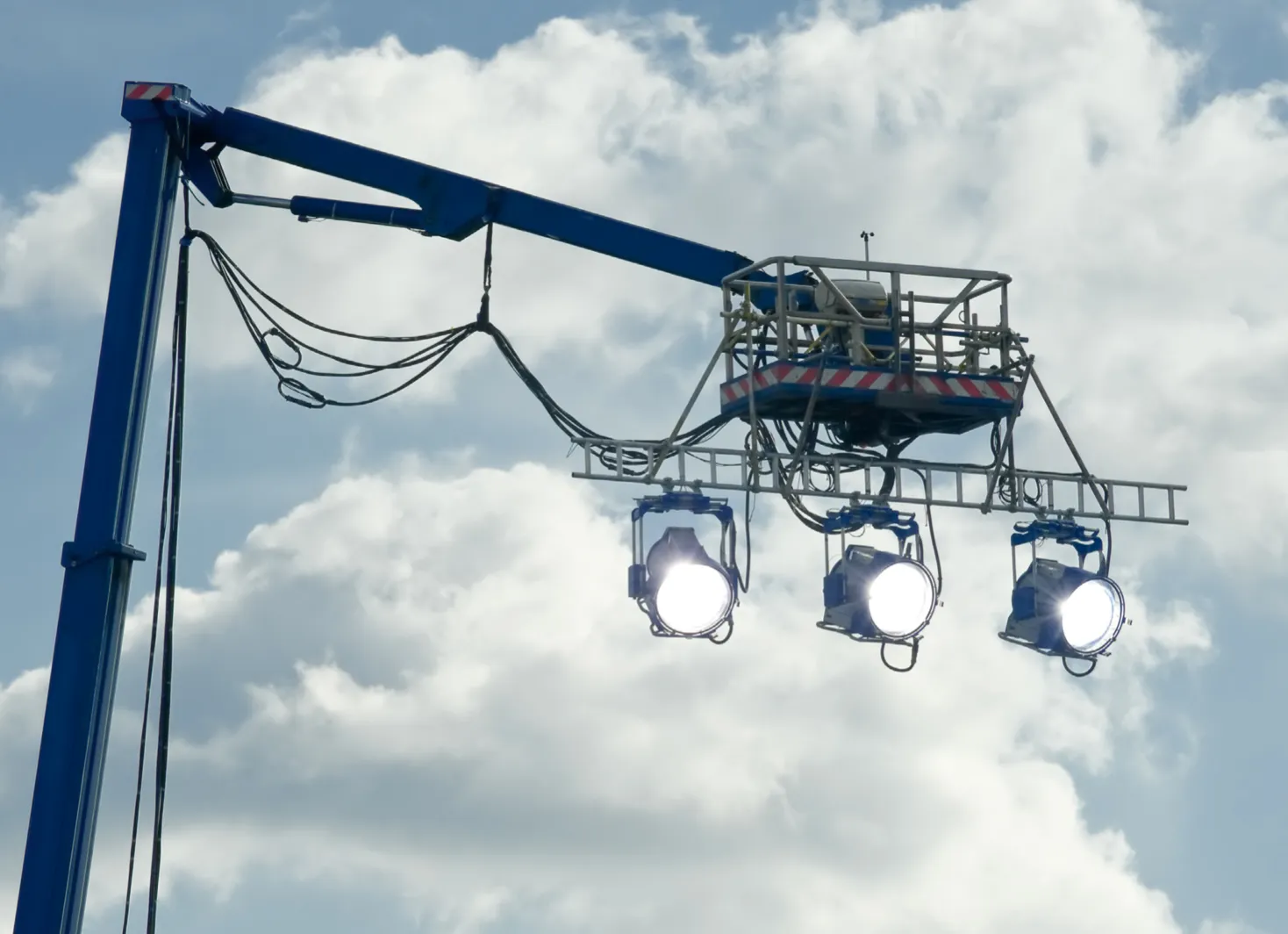
Fundamentals of Rigging Safety
No rigging should be undertaken unless it can be done in a way that protects people from danger.
For a rig to be safe it must have the following five elements:
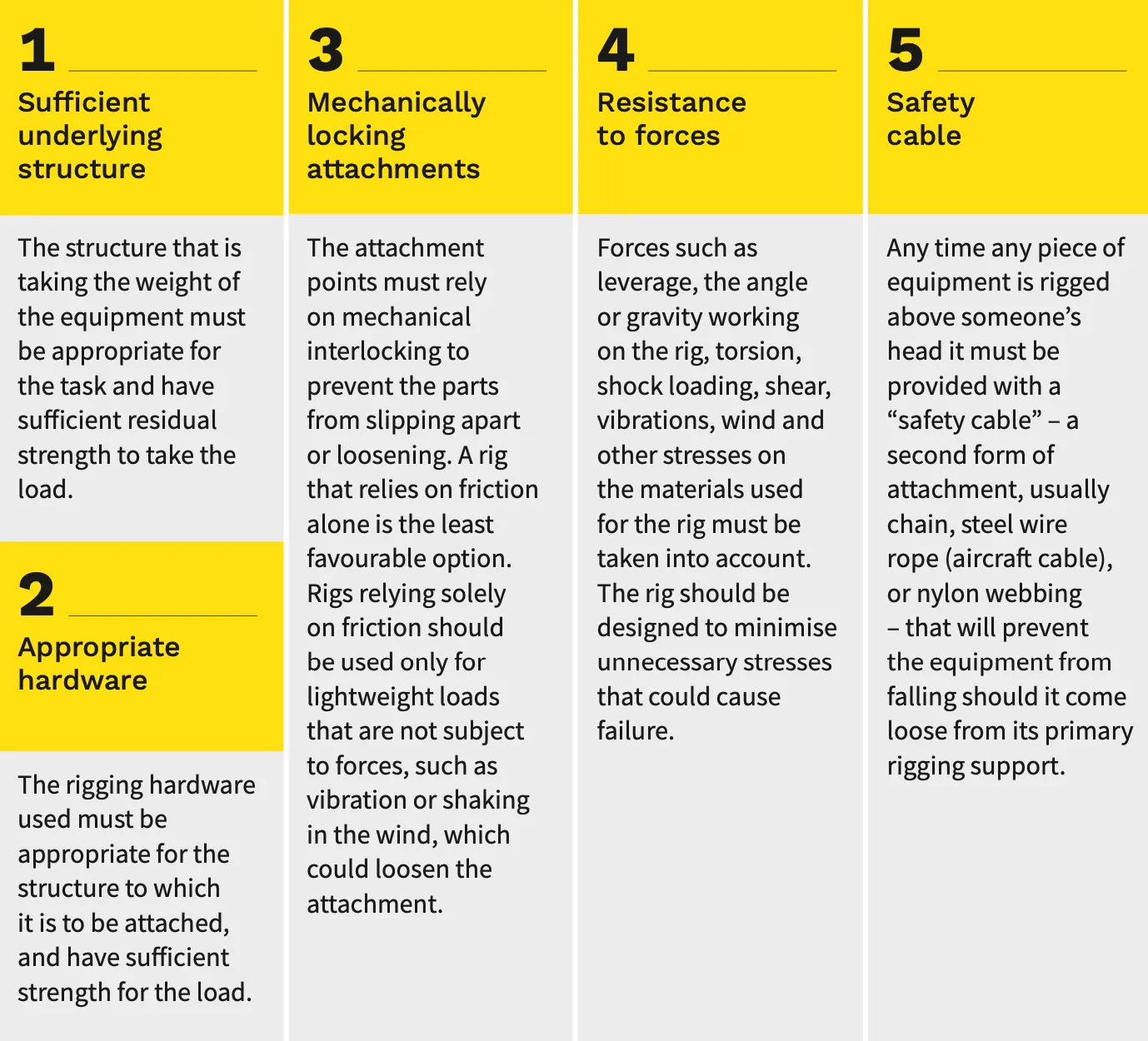
*ref: FilmSkills, Production Safety, Series: FilmSkills: Behind the Screen,
Publisher: CreateSpace Independent Publishing Platform; 1 edition (August 12, 2015), ISBN-10: 1514627957/ ISBN-13: 978- 1514627952
Planning and Guidance Considerations
Everyone who is responsible for, or has influence over, an activity or task in relation to setting up and managing rigging should read and understand this section, as well as the minimum responsibilities section, in particular the fundamentals of safe rigging.
Producer / Production Manager
The Producer / Production Manager, as the person ultimately in charge of the task, should:
- consult with heads of department as to the adequacy of any specific equipment to be used for a particular task taking into account the conditions; and
- specify, in consultation with head of departments, who oversees rigging work on the production set.
Person in charge
The person in charge of rigging will depend on the size of the production, and the responsibilities may be split between multiple people.
The Producer or Production Manager should specify, in consultation with head of departments, who is in charge of rigging on the production set.
Mechanical Access Plant
The person in charge should consider:
- the surface – some mechanical access plant are designed for flat surfaces, while others are designed for operating on uneven ground;
- an appropriate communications system for those operating the mechanical access plant; and
- any potential overhead obstructions.
Mobile Elevating Work Platform
Mobile elevating work platforms (MWEPs) include cherry pickers, scissor lifts, hoists and travel towers.
Anyone, including the PCBU or a supervisor, who asks someone to use a MEWP, must make sure that the operator is adequately trained by a competent person and can demonstrate their competency before using any equipment.
The person in charge should ensure the MEWP:
- safe working load of equipment is not exceeded – calculating all factors that may affect the load including lighting equipment, and the number and weight of workers;
- is clearly marked with the rated lifting capacity;
- has been inspected and tested within the previous six months;
- has a current six-monthly inspection certificate displayed;
- does not create further risks – for example the boom will not swing out into the path of other vehicles;
- is not be overloaded or used as a crane; and
- operating and maintenance manual is available for use.
The person in charge should also:
- ensure risks associated with power lines are considered and appropriately controlled;
- ensure the area covered by the swing of the arms is a limited access area;
- instruct workers to use a safety harness or belt and restraint where practical;
- ensure operators of boom-style MEWPs wear a safety harness with a lanyard incorporating a short energy absorber attached to a certified anchor point.
Further information about the safe use of MEWPs is provided in the AS 2550.10 Cranes, hoists and winches – Safe use – Mobile elevating work platforms.
Knuckle Boom
A knuckle boom has a second articulated joint pathway along the arm to allow for extra flexibility and reach for the work platform.
Minimum Clearance from Overhead Electric Power Lines
There are minimum clearances from overhead conductors depending on their voltages.
The Producer/Production Manager or Head of Department or delegated representative should consult with the local power supplier in each case.
Otherwise, maintain a minimum of four metre clearance between the crane including any person or equipment on it, the swing of the arms, and the overhead conductors.
New Zealand Electrical Code of Practice for Electrical Safe Distances
Training and qualifications
The PCBU, likely to be the production company, must ensure that it if there are specific regulations or training requirements / qualifications that these are adhered to.
If there is not a specific regulation or training requirement, the PCBU must ensure workers are either sufficiently competent to do their work or are adequately supervised by an experienced person, as well as adequately trained in the safe use of equipment in the workplace.
Scaffolding
Any anyone responsible for managing, setting up or using scaffolding should read the ScreenSafe chapter on scaffolding and WorkSafe guidelines on scaffolding, including the specific section on training.
Elevated Working Platforms
The person in charge must ensure the operator:
- gets training on the type of MEWP they will be using; and
- is supervised during the training period until the person is considered competent to operate the MEWP.
For the purposes of operating a MEWP, a competent person is a person who has achieved and demonstrated competency in the safe use of a particular type of MEWP; this may include completing nationally recognised MEWPs NZQA unit standard or an equivalent or higher qualification.
Forklifts
The operator must follow the Approved Code of Practice for Training Operators and Instructors of Powered Industrial Lift Trucks (Forklifts).
Harness Work
For workers who are to complete basic work while under total restraint, a recommended means of achieving competence is NZQA Unit Standard 23229 – Use a safety harness for personal fall prevention when working at height, or an equivalent or higher qualification.
A recommended means of obtaining competence for workers who are involved in planning, installing, operating fall arrest systems and supervising staff is NZQA Unit Standard 15757 – Use, install and disestablish proprietary fall arrest systems when working at height or an equivalent or higher level of qualification. NZQA Unit Standard 23229 is a prerequisite for achieving NZQA Unit Standard 15757.
Further reading
Safe Rigging Practices for the Entertainment Industry in New Zealand; Entertainment Technology New Zealand Incorporated; June 2015
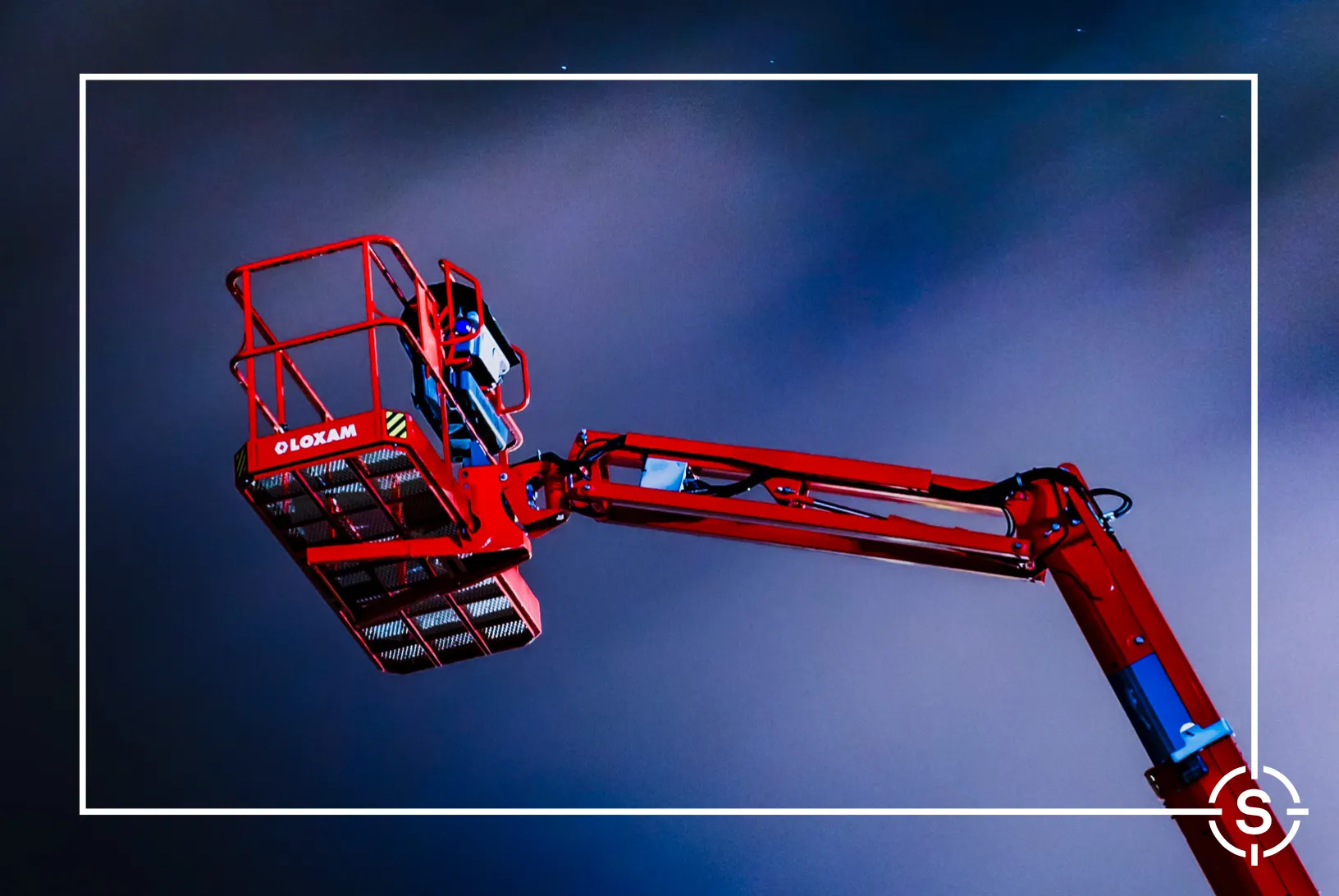
Rigging
Special Effects
This chapter provides guidance in relation to working with special effects on a production.
The information provided within this chapter has been developed in consultation with special effects subject matter experts from within the New Zealand and international screen industry and draws from the Health and Safety at Work (Hazardous Substances) Regulations 2017.
Who needs to read this?
All workers who undertake work with, or work that interacts with, special effects should read and understand the section on ‘minimum responsibilities’ and ‘responsibilities specific to special effects’.
Roles that have specific responsibilities, or influence, over work with special effects should read the section on ‘planning and guidance considerations’ and ‘responsibilities specific to special effects’ – this includes producers, directors, production managers, line producers, heads of departments, assistant directors and health and safety officers.
Definitions
Atmospheric special effects are the use of artificial smoke and mists produced from chemicals or oil for theatrical purposes; this includes simulating steam, rain, wind, snow, water and wave effects.
Exclusions zones are areas defined by the person in charge / PCBU that may receive debris or malfunctioning pyrotechnics and help to ensure people’s safety.
Explosives may be high explosive, such as bullet hits, detonators, detonating cord, gelignite or TNT, or low explosive of the burning (deflagrating) or propulsive, such as flash or gun powder.
Hazardous substance means, unless expressly provided otherwise by regulations, any substance —
- with one or more of the following intrinsic properties – explosiveness, flammability, a capacity to oxidise, corrosiveness, toxicity (including chronic toxicity), ecotoxicity,
- with or without bioaccumulation; or which on contact with air or water (other than air or water where the temperature or pressure has been artificially increased or decreased) generates a substance with any one or more of the properties specified above.
Mechanical special effects are ways of creating special effects using, but not limited to, air mortar explosions, breakaways, falling objects, action props, flying sequences, counter weight systems, hydraulic, pneumatic and kinetic effects including the use of computer and hydraulic controlled Gimbals.
Open flames refers to the planned use of fire and combustible fuels for filming purposes.
Pyrotechnics are devices, compounds and mixtures that burn fiercely and produce light, heat, smoke or sparks in varying colours and quantities without an explosive effect.
Pyrotechnic special effects are ways of creating special effects using, but not limited to, explosives, pyrotechnics, fireworks, bullet hits and pyrotechnic smoke devices.
Note: that safety flares, parachute rocket flares and pyrotechnic smoke pots all fall into the category of pyrotechnics when used as special effects.
Special effects means the use of a physical mechanical and chemical process to produce on camera effects elements.
Special effects supervisor (SPFX supervisor) means the person responsible for the planning, preparation and use of special effects.
Special effects technician (SPFX technician) means a person responsible for the preparation and use of special effects under the supervision of a special effects supervisor.
Specific risks
- Chemicals and fumes
- Concussion from explosive blast overpressure
- Blunt force trauma from flying objects
- Lacerations from flying projectile debris
- Heat radiation from pyrotechnics, steam or fire
- Flash burns
- Loud noises
- Light flashes
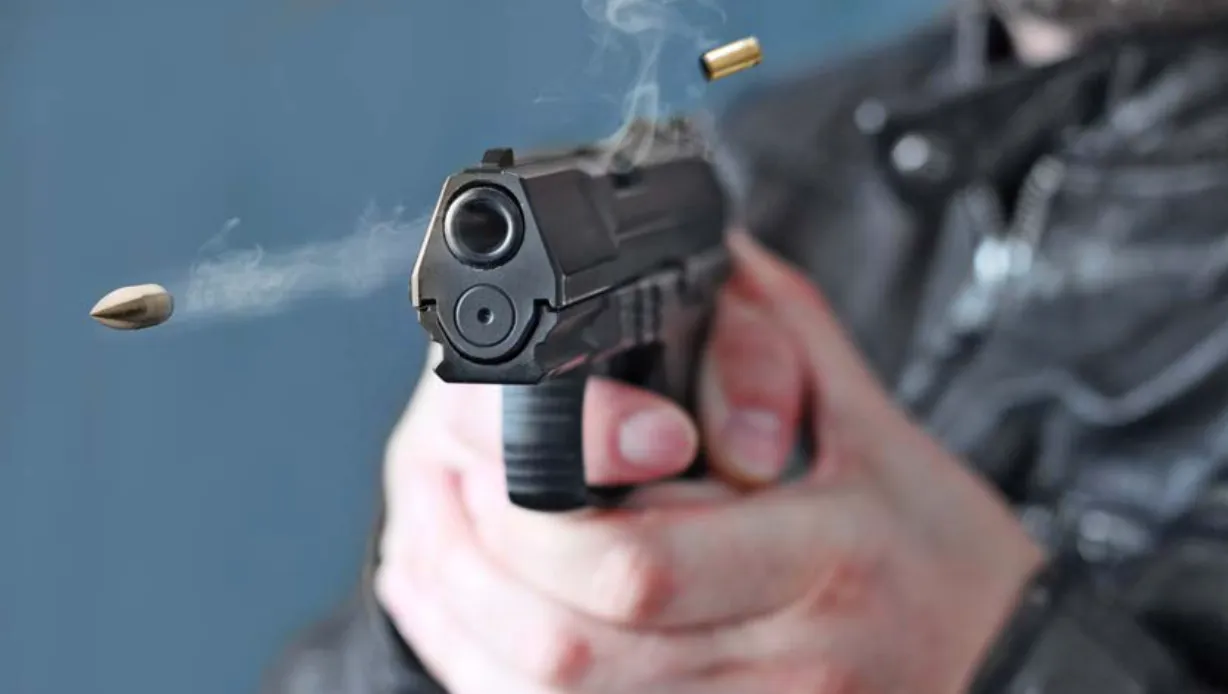
Minimum responsibilities
Everyone on a screen production who does, or could, work with special effects, should read and understand this section.
All workers:
- are required to follow all health and safety information, training and instruction they have received;
- must be aware of what personal protective equipment they are expected to provide themselves and what will be provided by the production;
- follow instructions provided by the person in charge of any activity that involves the use of, or is conducted near, special effects; and
- know escape routes, when working around or near special effects, and if they are unsure of the escape route check with the 1st assistant director to learn the escape route before entering the work area.
* All SPFX Supervisors and Technicians must also read the section on Responsibilities Specific to Special Effects.
Planning and Guidance Considerations and Responsibilities
Anyone who has specific responsibilities, or influence, over work with special effects should read and understand this section as well as the minimum responsibilities for everybody. This includes funders, Producers, Directors, Production Managers, Line Producers, Heads of Departments, Assistant Directors, SPFX Supervisors and Technicians, and Health and Safety Officers.
Further information about responsibilities related to special effects can be found in the following section.
While the production company is likely to be the primary PCBU (person in control of a business undertaking), all PCBUs (such as contractors) are responsible
for the overall safety of the workplace and those who are influenced by their work, including workers, visitors and other persons on, or in the vicinity, of that workplace.
Funders
Funders should:
- be assured, through the provision of the production’s health and safety plan, that the funding provided is adequate to provide for competent people, to undertake and supervise all work related to special effects, and the appropriate equipment required; and
- ensure that all senior contractors have sufficient insurance cover, appropriate to the risk and scale of the work to be undertaken.
Production Company
In pre-production, the production company must clearly identify who has control of special effects, and ensure those people are competent.
During production, production companies must consult, cooperate and coordinate with other PBCUs on set and subject matter experts, where necessary.
Producer and Production Manager
The Producer, Production Manager or person with delegated responsibility should:
- ensure all cast and crew are aware that explosives and pyrotechnics, open flame/ fire sequences or smoke producing equipment will be used
- ensure workers are aware of risks associated with special effects;
- ensure workers are provided appropriate personal protective equipment;
- consider how changing deadlines and making changes to briefs at the last minute can lead to fatigue and stress for workers;
- consider how changing work briefs, resulting in workers starting the project from scratch, can lead to stress for workers;
- consult and collaborate with the special effect supervisor to understand how long tasks will take and how deadlines may impact workload and final product;
- ensure hazard identification and risk assessments are undertaken for all applicable special effects;
- ensure all potential risks on location are eliminated or, if elimination is not reasonably practicable, minimised;
- ensure that emergency and first aid procedures are in place;
- ensure sufficient firefighting equipment is provided and that it is immediately available on set if required;
- ensure there is a clear access way for emergency and firefighting equipment and vehicles on set;
- ensure that all those who undertake specific effects hold the relevant permits/ licences;
- ensure that the SPFX Supervisor is allowed adequate on-set pre-production time unhindered by other filming or other crew or cast members;
- ensure that adequate testing of all special effects is carried out during pre- production and where possible that such testing is carried out in the presence of all relevant heads of department and those cast members involved; and
- ensure that the SPFX Supervisor always has in their possession all necessary permits and licences covering products and equipment used to carry out their contract of employment, together with literature on all relevant chemical compositions and safety guidelines regarding the use of pyrotechnics and flammable materials.
Assistant Director/s
The 1st Assistant Director will ensure that the SPFX Supervisor is allowed adequate on-set pre-production time unhindered by other filming or other crew or cast members.
In the absence of a Health and Safety Officer, the Assistant Director/s should:
- ensure hazard identification and risk assessments are undertaken for all special effects activities, and controls implemented;
- ensure that emergency and first aid procedures are followed;
- ensure personal protective equipment specific for special effects work is provided to, and used by, workers when required;
- ensure workers know escape routes, when working around or near special effects, before entering the work area.
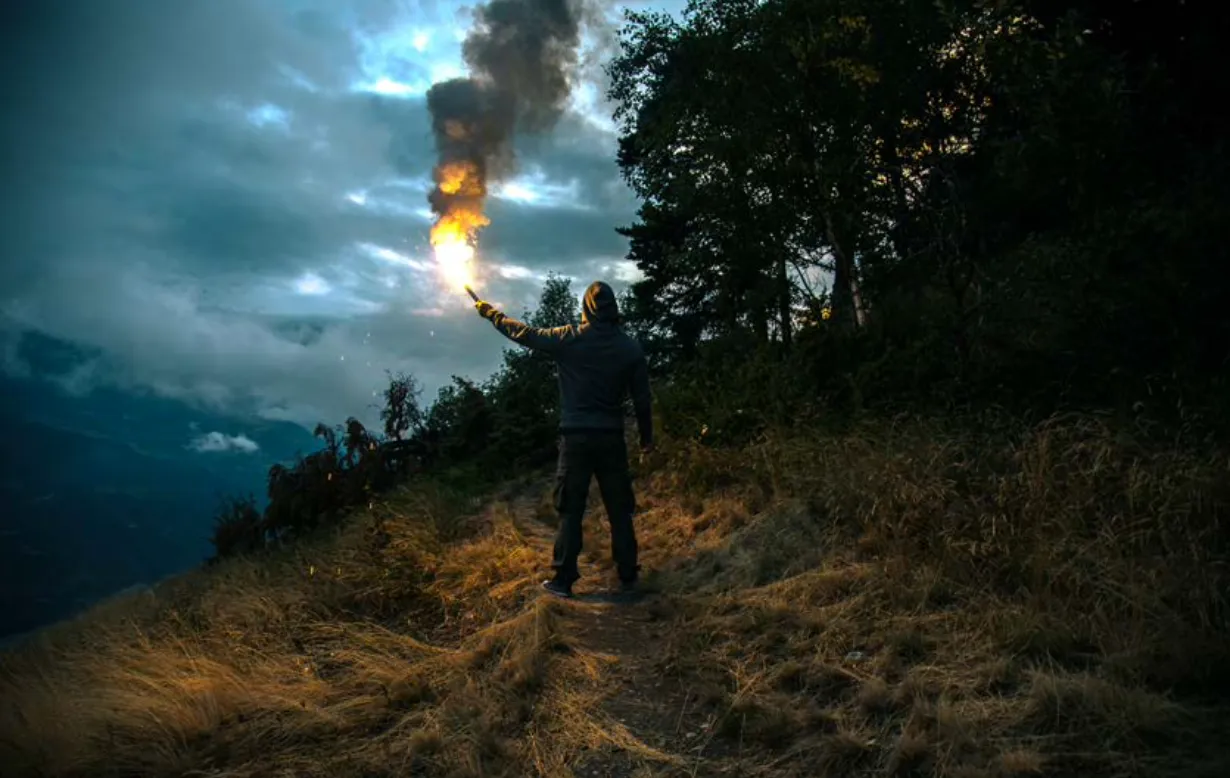
Special Effects Supervisor
The SPFX Supervisor should:
- ensure all SPFX Technicians have the necessary skills, certifications and experience to ensure safe and compliant outcomes for the production;
- carry out adequate testing of all special effects during pre-production and, where possible, ensure that such testing is carried out in the presence of all relevant heads of department and those cast members involved;
- set exclusions zones based on testing data to contain risk to cast and crew;
- always have in their possession all necessary permits and licences covering products and equipment used to carry out their contract of employment, together with literature on all relevant chemical compositions and safety guidelines regarding the use of pyrotechnics and flammable materials;
- ensure notification is made to the appropriate authorities, as outlined in the Health and Safety at Work (Hazardous Substances) Regulations, of the planned use of explosives and pyrotechnics or open flames;
- prepare an emergency response plan, which includes acceptable avenues of escape;
- ensure they, and all SPFX Technicians, have a suitable approved handler certification for any pyrotechnic work undertaken;
- organise a walk-through and safety brief before any hazardous sequence;
- consider how changing deadlines and making set changes at the last minute can lead to fatigue and stress for workers; and
- if there are problems relating to special effects on set, find practical solutions that don’t affect health and safety and, if necessary, raise concerns with the production to ensure safety.
Health and Safety Officer
The Health and Safety Officer should:
- work with the SPFX Supervisor to identify all potential risks;
- liaise with the appropriate competent persons to identity and implement appropriate controls for all risks;
- ensure workers are provided, or advised of, the appropriate personal protective equipment required on the location; and
- ensure workers know escape routes, when working around or near special effects, before entering the work area.
Responsibilities specific to Special Effects
General safety procedures
Competent Person
Only a competent person, such as a SPFX Supervisor or SPFX Technician, may carry out mechanical or pyrotechnic special effects.
A suitable approved handler certification is required for any pyrotechnic work.
Fatigue
Changing deadlines and set changes at the last minute can lead to fatigue [add link] and stress for workers; such impacts must be taken into consideration and minimised.
Notification of Planned Use
Notification to the appropriate authorities, such as WorkSafe and / or closest Police or Fire and Emergency communication centres, of the planned use of explosives and pyrotechnics or open flames must be made as required in the relevant Regulations or local bylaws.
Notification to Personnel
All personnel must be notified that explosives and pyrotechnics, open flame/fire sequences or smoke producing equipment will be used and briefed on safety precautions.
Emergency Response Plan
An emergency response plan must be prepared, including acceptable avenues of escape.
Permits and Licenses
The relevant permits/licenses must be held by those using and supervising special effects.
Safety Briefing and Walkthrough
Before any potentially hazardous sequence is performed, an on-site meeting should be called for all personnel who are involved in, or working near, the sequence. The meeting should include an "on-site walk-through" or "dry run" with the SPFX supervisor and all personnel directly involved in the event.
The SPFX Supervisor should clearly identify:
- the intended action
- possible deviations;
- communication signals and chain of command;
- authority to abort event;
- acceptable avenues of escape;
- location of necessary safety equipment and personnel.
Substantial Changes to the Planned Special Effect
If at any time substantial changes become necessary, another meeting should be called to confirm everyone's understanding of, and agreement to, the change(s).
Live Rehearsal
A live rehearsal should be held whenever practicable.
Emergency Vehicle Access
There must be a clear access for emergency and firefighting equipment and vehicles.
Effect of Special Effects on Studios/buildings
When planning the use of special effects in a studio/building, expert advice, such as that from an engineer or test certifier, should be sought as to how such effects might affect or be affected by the studio/building itself.
Firefighting Equipment
Appropriate and sufficient firefighting equipment must be provided and available immediately available on set.
Smoking
A ban on smoking and naked flames must be enforced in the entire area in which the special effects is being created, including workshops and storage areas.
Explosives and Pyrotechnics
Anyone using explosives or pyrotechnics should also read and understand the chapter on hazardous substances.
Restrictions on Use
The use of explosives and pyrotechnics are set out under the Health and Safety at Work (Hazardous Substances) Regulations 2017.
WorkSafe New Zealand enforces the statutory regulations on the use of, transportation, importation, storage and of explosives and pyrotechnics.
Any use of explosives or pyrotechnics for filming must be under the control of someone who has a “certified handler” certification for the classes of pyrotechnics being used in addition to a “controlled substances licence” listing the classes of pyrotechnics for explosives being used.
SPFX supervisors conducting pyrotechnic sequences that fall into the category of a fireworks display, must ensure they obtain an "OPD (Outdoor pyrotechnic display compliance certificate)".
The Discharge Area and Exclusion Zones
The Health and Safety at Work (Hazardous Substances) Regulations 2017 set out the requirements for discharge area and exclusion zones.
The discharge area is where the pyrotechnic effect is initiated. The exclusion zone6 is the area where the hazardous effects of the
discharge are contained.
The SPFX supervisor or certified handler in charge of the detonation or deflagration should determine the exclusion zone to ensure no person is exposed to adverse:
- heat radiation;
- blast overpressure; or
- fragmentation.
Exclusion zones are best determined through testing.
Testing must be scheduled away from the day’s shooting and prior to filming the effect and is required to determine safe distances and minimum quantities of explosive necessary to produce the effect.
Where objects are projected into the air, the testing method must be with the objects themselves or their equivalent to ensure the effect and the outcome is correctly simulated. Any subsequent changes made to the effect after initial testing will require a re-run of the testing procedure.
Restricted Access to the Exclusion Zone
The certified handler in charge must have complete control over who enters the exclusion zone; only crew and cast members necessary for filming should be in the exclusion zone.
After each pyrotechnic event, no one should enter the pyrotechnic area other than the pyrotechnic special effects operator in charge, or their designated representative(s), until it is declared safe. This includes for testing, rehearsals and filming.
Detonation of Pyrotechnics or Explosives
A sequence of firing cues and a strict routine of rehearsals should be established and understood by all involved.
Pyrotechnic special effects should not be fired unless the area involved with the firing is in the continuously unobstructed full view of the pyrotechnic special effects operator in charge, or their designated representative, at the time of firing, unless equal means of observation are used.
Appropriate fire watch, as determined by the certified handler in charge, should be maintained after each pyrotechnic event.
Reducing Risk of Unintended Initiation or Detonation
Radio transmissions of any kind, including mobile phones, should be turned off in the explosives area, unless exempted by the SPFX supervisor. This restriction applies from the start of the preparation of pyrotechnics until after the explosives area has been cleared by the SPFX supervisor.
In the event of audible thunder or visual sighting of lightning, all pyrotechnic or explosive work must be suspended and made safe.
There must be no smoking or any type of fire, spark or other source of ignition near any explosives.
To protect against accidental firing, all electrically fired pyrotechnic devices should be shunted prior to firing.
Power sources for firing pyrotechnic special effects devices should be restricted to isolated ungrounded batteries or individually designated ungrounded generators (below 5 kilowatts to comply with non-grounding requirements) used exclusively for firing purposes only.
Bullet Hits and Rigging Body Bullet Hits
Only use custom-made bullet hits designed for use in the close vicinity of crew and cast members.
Only the SPFX sSupervisor or SPFX Technicians should rig body hits.
All body bullet hits should be tested prior to use with the same fabric or costume.
The rigging of any type of pyrotechnic device to a performer needs to be done by a SPFX Technician and have been sufficiently tested.
Open flames
Restriction use of LPG
LPG is a Class 2.1.1A hazardous substance, and its use is governed by the Health and Safety at Work (Hazardous Substances) Regulations 2017.
If there is more than 100kg of LGP on set, it must be under the direct control of a certified handler or secured correctly.
A non-approved handler may handle the product provided a certified handler is present at the location and available to assist or has provided guidance to the use and handling.
Once the quantity of LPG in a location is over 100kg this activates the requirement to establish a Hazardous Substance Location and a Hazardous Atmosphere Zone.
Flammables and Combustibles
Flammable and combustible materials need to be kept a safe distance from open flames and in approved labelled containers.
When used on set to act as a fire accelerant, continual ventilation needs to be initiated until ignition or clean-up and storage is completed.
When LPG is used to provide a yellow flame, carbon monoxide is produced, so adequate ventilation needs to be maintained.
Each LPG tank "shut-off” location should have an operator who always has a clear view of any LPG fires.
All gas lines in connection with the use of open flames need to be rated and appropriate for use with gas/LPG.
All stationary open flame fixtures and devices need to be firmly secured.
The fuel source for special effects fire rigs need to be sufficiently isolated/bunkered/ distanced from the remainder of the crew to avoid any risk to personnel in the event of a flashback. The use of flash back arresters is advised.
On an interior set where smoke and open flame are used together, precautions must be taken to ensure the smoke does not reach a level of density where it could ignite from the open flame.
Fire Area
The producer or person with delegated responsibility and the SPFX supervisor should determine the fire area. Only essential personnel should enter the fire area.
Fire and Provision of Respirators and Personal Protective Equipment
When creating a fire, the operator should exercise all reasonable precautions to prevent heat and smoke inhalation and should make respirators available on request ¬– respirators should be appropriate for the type of smoke.
Cast and crew near open flame should wear appropriate protective clothing. Depending on the hazards involved, this clothing should include appropriate closed-toe footwear, long pants and a long-sleeved shirt made of 100 percent cotton or material which provides equal or greater protection.
Cast and crew need to be notified by the designated responsible person when there is potential for exposure to open flame. Appropriate personal protective equipment must be for the hazard(s) involved and considerations must be made for head, hands, eyes, ears and respiratory protection.
Atmospheric effects
Artificial Smoke and Mists
Bronchial sufferers
Cast and crew should be warned of the risk caused by artificial smoke and mists, and effects, to sufferers of bronchial disorders. Bronchial sufferers need to be provided with appropriate respiratory equipment if required to be in the vicinity the effect.
Type of chemical
The type of chemical selected should cause the least respiratory irritation and be safe to use.
Dense artificial smoke can be highly flammable. Special care should be taken to prevent ignition from any source. An MSDS for each substance used should be immediately at hand.
Exposure to artificial smoke and mists
Exposure to artificial smoke and mists should be kept to a minimum. When smoke or fog effects are created on an interior set, the stage needs to be periodically ventilated or exhausted, vertically and laterally. All personnel and animals should be given a break away from the stage at appropriate intervals.
Ventilation
When using smoke on an interior set on location, the creator(s) needs to provide a means to exhaust or ventilate the set.
When smoke and/or mist is created on an interior set, the stage needs to be periodically ventilated or exhausted, vertically or laterally. All people and animals should be given a break away from the stage at appropriate intervals.
Provision of protective respiratory equipment
The producer or person with delegated responsibility needs to provide specialised respiratory equipment when personnel are exposed to long or intense periods of artificial smoke or mist.
Evacuation of crew and cast rooms
When artificial smoke and/or mist is used on any interior set, all non-essential personnel should be removed from all areas close enough to be affected by the smoke or mist.
Water Effects
All water used in rain sequences where the water falls on cast and/or crew should not pose a health risk.
Only appropriately licensed and authorised personnel can draw water from hydrants and stand pipes.
All personnel operating nozzles must be adequately trained in their use.
Fire hoses must be routed to minimise danger (of electrocution or whiplash from the fire hose) if a coupling failure occurs.
Hoses must be maintained in sound working order to avoid rupture.
Ramps must be used to cover hoses whenever there is pedestrian or vehicular traffic.
Rain stands and sprinklers must be adequately sandbagged and secured to prevent them from toppling over.
Electrical Safety in Conjunction With Rain and Water Effects
AS/NZS 4249: Electrical safety practices—Film, video and television sites and all relevant regulations must be complied with during rain and wet-down effects.
All electrical cables must be insulated and must be kept off the ground wherever possible to avoid electrical current being carried through the water.
All single phase and three phase outlets, leads and three-pin connections must be kept dry. Where possible, submersible cables should be used.
Snow Effects
When snow effects are being carried out, materials used must have an MSDS and be used in accordance with relevant technical information.
Mechanical Effects
Breakaways
When constructing breakaways, a competent person, SPFX supervisor or SPFX technician should be consulted.
Hydraulic and Pneumatic Ram and Gimbal Systems
Hydraulic or pneumatic jerk rams, deadweight drops, shaker motors and any mechanical rigs need to be used according to manufacturer recommendations, and risk assessed and documented on a rig-by-rig basis, including:
- establishing an exclusion zone around the rig that ensures no cast or crew are struck or injured by the moving parts or any projectiles coming from it;
- ensuring only SPFX technicians trained in the safe use of the equipment are in control of its operations; and
- ensuring the rig and safety procedure have been extensively tested before use around cast and crew.
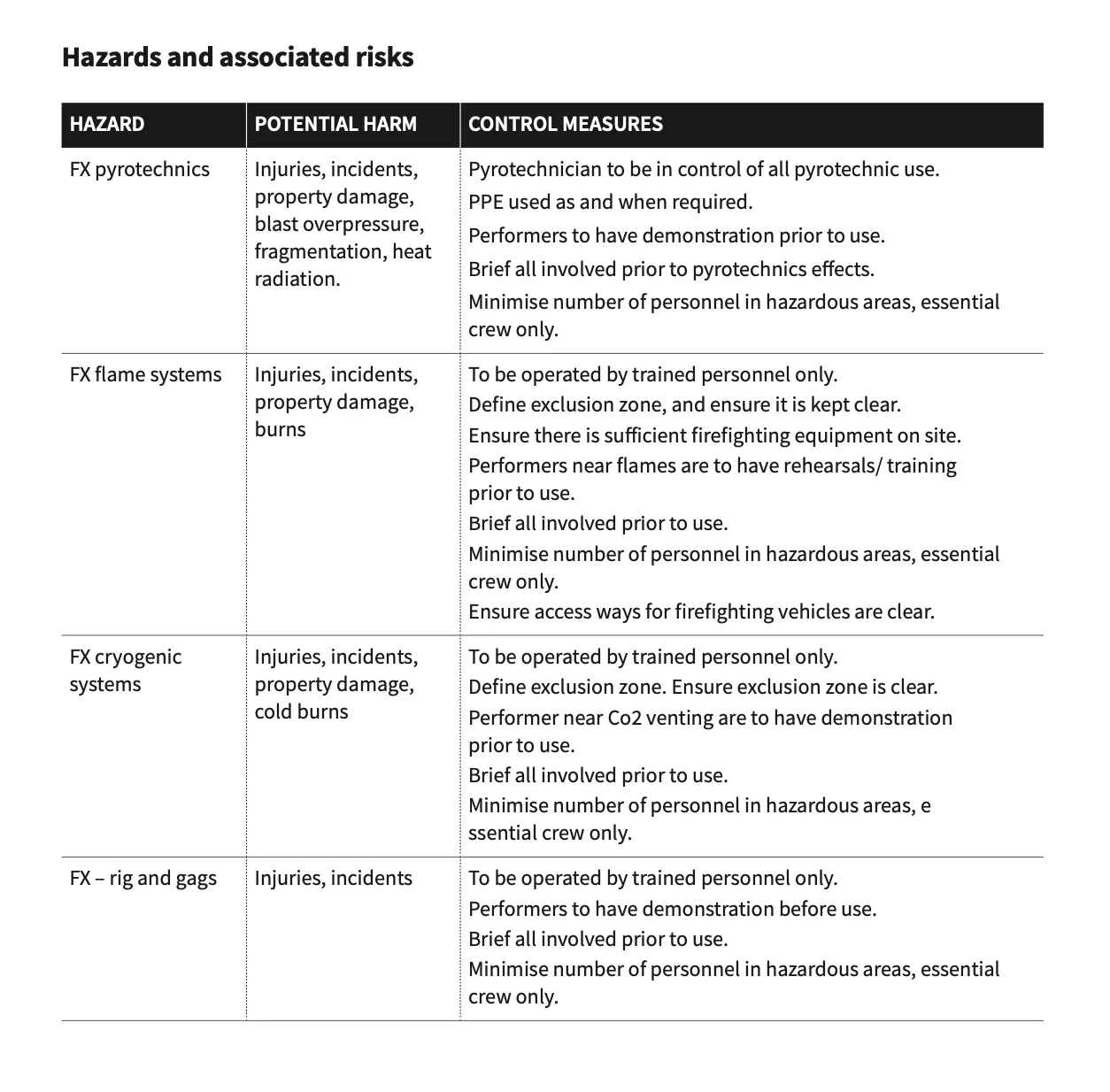
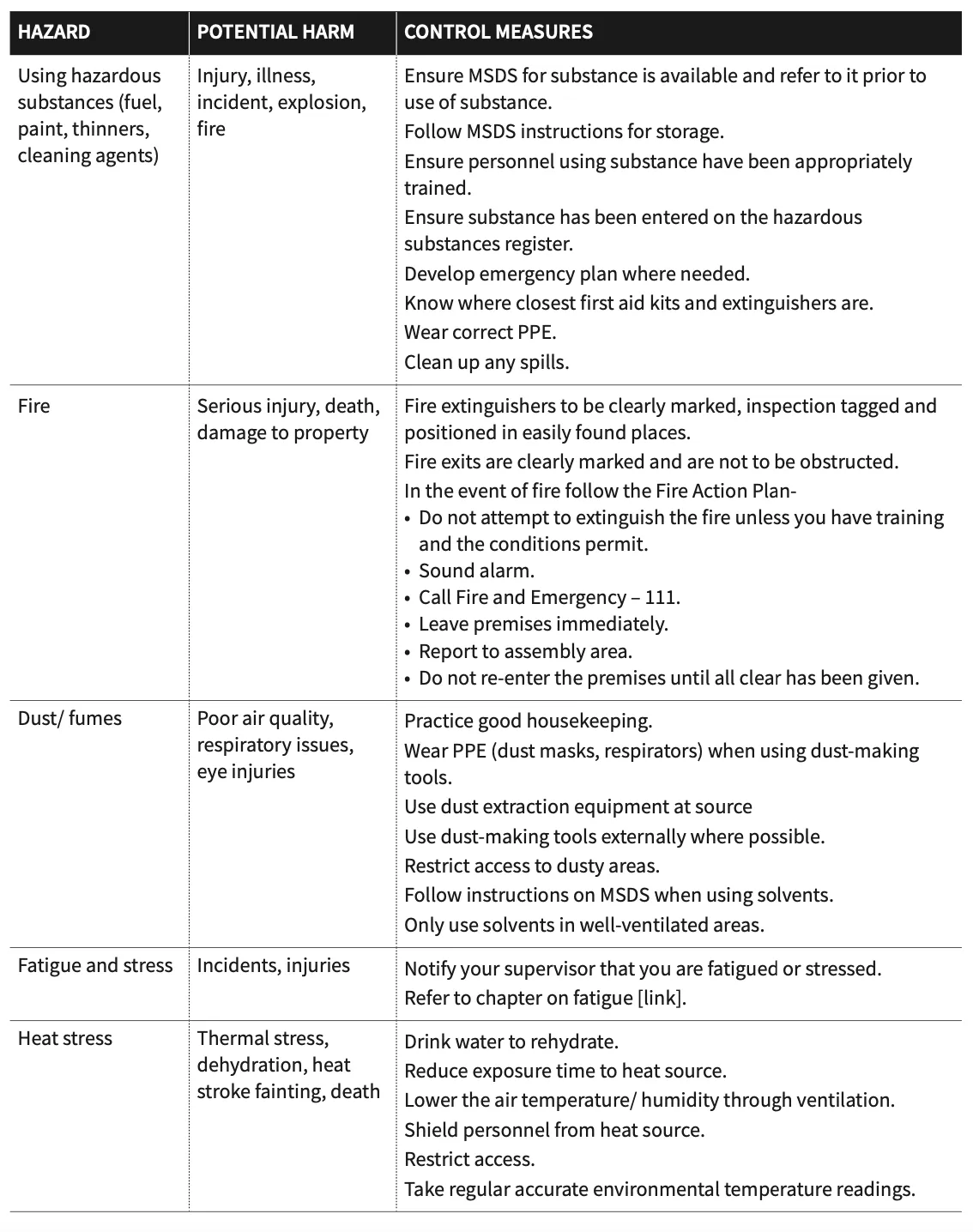
Training
Anyone handling or working with hazardous substances must have the appropriate training and knowledge as outlined in the hazardous substance chapter.
SPFX Supervisors and Technicians taking a lead role in pyrotechnics should be a certified handler and have a controlled substance license for any class 1 substances being used.
A handler certification should be held for Class 2 and 3 where quantities of those exceed the thresholds listed in Table 2 of Schedule 9 Health and Safety at Work (Hazardous Substances) Regulations 2017
References
Health and Safety at Work (Hazardous Substances) Regulations 2017
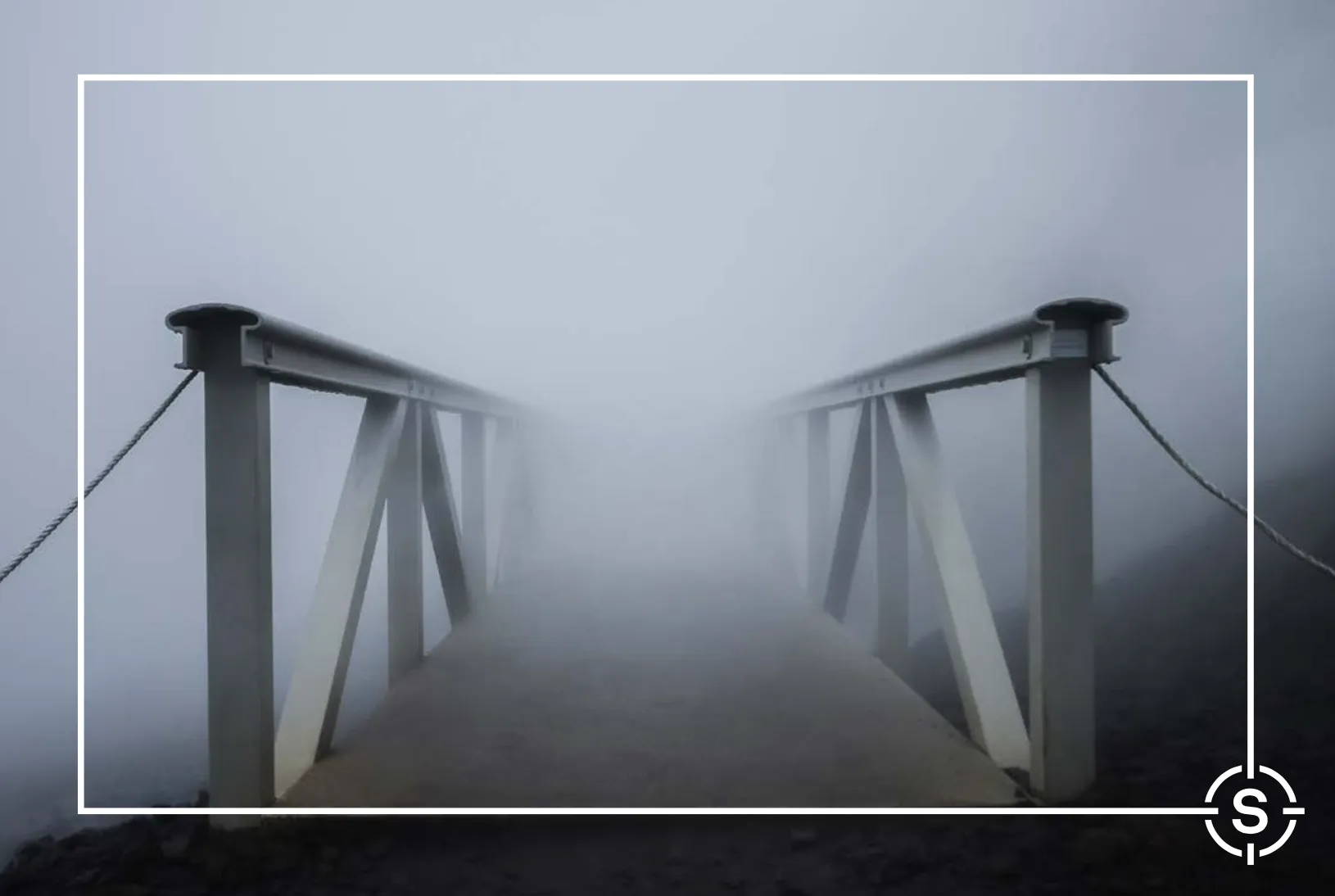
Special Effects (SPFX)
Water safety
New Zealand has one of the highest fatal drowning rates in the OCED and New Zealand waters are unpredictable; if filming on, in or around water the production must take into consideration water safety for people and animals.
ScreenSafe suggests all productions are familiar with Water Safety New Zealand and AdventureSmart. Water can include the ocean, rivers, streams, lakes and pools.
Ensuring safety
Productions should ensure:
- competent guides are used where appropriate, especially in extreme conditions;
- qualified life-saving personnel are present for the duration of the production activity;
- equipment (such as safety boats, lifejackets and scuba diving equipment) is maintained and tested;
- all divers working on production have the relevant certificate of competence for the work they are undertaking and current medical clearance;
- WorkSafe’s guidelines are followed for all diving related to a production;
- actors required to dive have appropriate training, this could be a resort/discovery course (at a minimum) or a full Open Water course or higher:
- ~ if they only have done a resort / discovery course, they must have a safety diver, who holds a certificate of competence; if they
hold a higher level of training, the number of safety divers is determined as part of the risk assessment approved by the diver supervisor; - people understand the risk of hypothermia, how to identify it and what to do;
- two-way communication is available;
- anyone expected to swim is competent to do so;
- life jackets are used where practicable;
- water is checked for hazards, including depth, currents and rips, tides, waves, objects and dangerous marine life;
- weather forecasts are checked, especially when working around, in or on rivers as water levels can rise rapidly;
- people or animals are not fatigued when required to work in, on or around water;
- if people or animals are required to enter the water, quality tests should be undertaken to ensure the water is free of contaminants;
- if people or animals are required to enter the water, water temperature and length of exposure should be considered;
- have an emergency plan in place;
- only competent people, who understand maritime rules, drive vessels;
- if working at a beach, crew know how to identify a rip and what to do if stuck in one;
- if crossing rivers, this is done so safely and sensibly;
- if animals are used, trainers should be adequately instructed in water safety precautions; it is recommended that trainers be acquainted with the hazards and procedures for working safely around water and that any animals working on, in or at the water’s edge are comfortable doing so prior to the production.
Navigation and safety rules
Be aware navigation and safety rules can vary from region to region in New Zealand, in the form of regional bylaws; ScreenSafe recommends that productions take the time to get acquainted with the rules relevant to that region.
References
https://www.watersafetynz.org
https://www.adventuresmart.nz
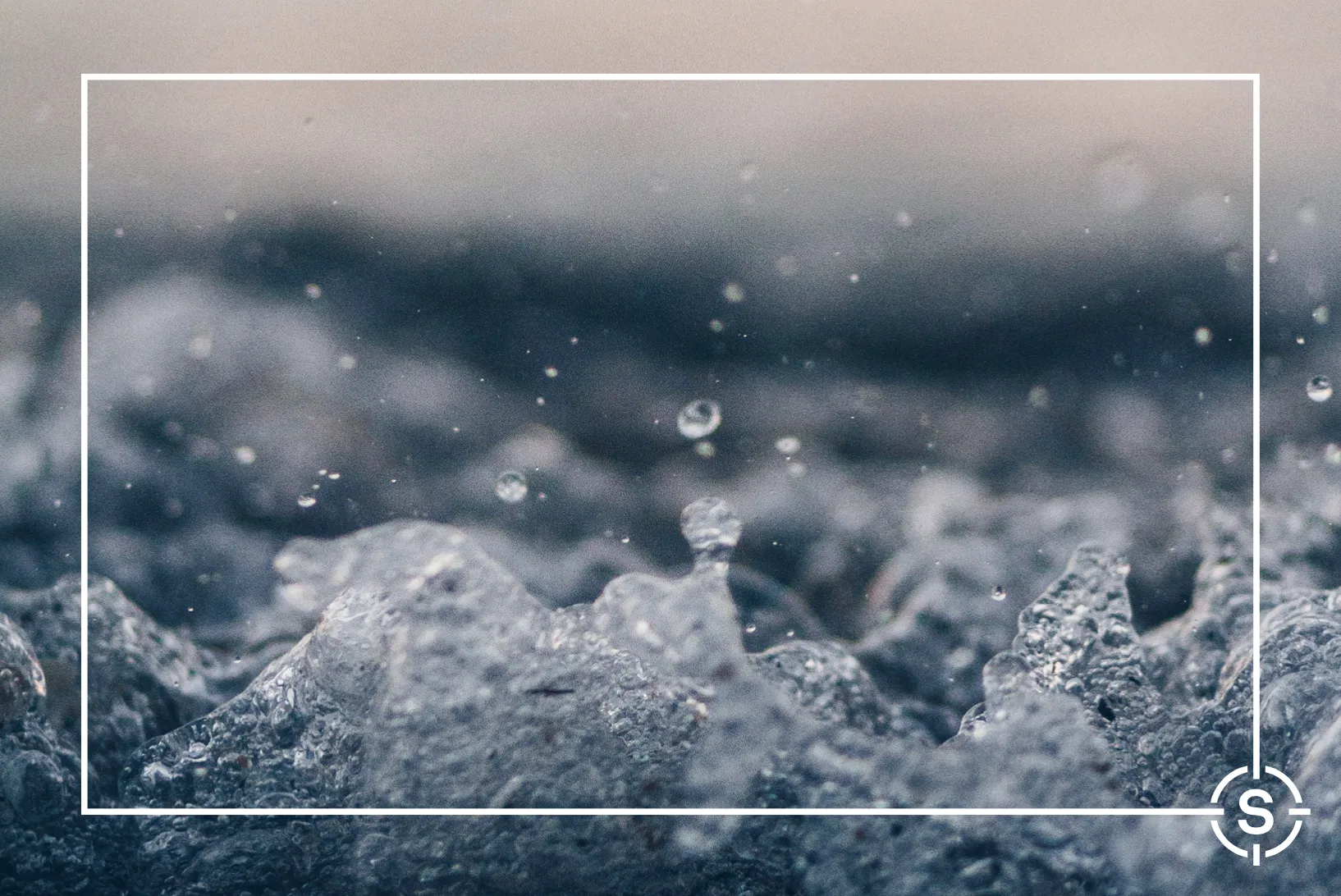
Water Safety
Who needs to read this?
All workers who undertake tasks at height should read and understand the section on ‘minimum responsibilities of working at height’.
Roles that have specific responsibilities, or influence, over setting up and managing work at height should read the section on ‘planning and guidance considerations and responsibilities’ – this includes Producers, Directors, Line Producers, Production Managers, Art Directors, Construction Managers, Heads of Department, Assistant Directors and Health and Safety oOfficers.
What is Working at Height?
Work at height means working in a place where a person could be injured if they fell from one level to another.
When considering working at height you must also consider and manage the risk/s associated with falling objects, if it is reasonably likely that the object would fall on and injure a person.
There is no threshold for working at height; if someone or something could fall from one level to another and injure an individual then that is working at height.
Work at height does not include slips, trips and falls at the same level.
What specific working at height risks are there on production sets?
- Camera platforms (mobile and static)
- Rigging, including cranes (mobile powered elevating equipment)
- Scaffolding
- Ladders
- Elevated working platforms
- Rostra
- Studio lighting grids, gantries and catwalks
These risks are further outlined in individual chapters.
see also:
WorkSafeNZ (Ministry of Business, Innovation & Employment) Best practice guidelines for working at height in New Zealand. April 2012
Regulations 24 and 25 of the Health and Safety at Work (General Risk and Workplace Management) Regulations 2016
Minimum Responsibilities for Working at Height
Everyone who works at height on a screen production should read and understand this section, including Grips, Lighting crew, Camera crew, Special effects and Art Department crew.
If you are responsible for, or have influence over, an activity or task where there is work at height, you should read and understand the following section on ‘Planning and Guidance Considerations and Responsibilities’.
All workers should:
- understand the risks associated with working at height, and the possibility of both people and objects falling and injuring someone;
- follow all procedures and controls put in place to keep themselves and others safe when working at height;
- use personal protective equipment when required; and
- advise their supervisor or the health and safety officer if they observe unsafe working at height practices.
Planning and Guidance Considerations & Responsibilities
Too many falls from height occur because of a failure to plan or organise work properly.
Everyone who is responsible for, or has influence over, an activity or task where there is work at height should read and understand this section, as well as the minimum responsibilities for everybody.
This includes the Production Company, Producers, Art Directors, Construction Managers, Line Producers, Heads of Department, Assistant Directors and Health and Safety Officers.
Identifying the Risk of Working at Height
Everyone who is responsible for an activity or task in relation to the production should consider the potential risks associated with working at height; this is where someone or something could fall from one level to another causing harm to an individual.
Ways of identifying such risks include:
- physical inspections – walk around the production set, you could use a checklist to help you;
- looking at work practices and required tasks;
- consulting with cast and crew; and
- reviewing previous safety event information.
see also:
WorkSafeNZ. Working at Height Toolkit.
Fact sheet 1. Planning a safe approach to working at height. June 2015.
How do we Assess the Risk of Working at Height?
Just like any health and safety risk you must assess it – thinking about:
- the likelihood of the potential harm; and
- the consequence – how bad the harm would be.
* See the Risk Assessment Section: This health and safety risk assessment process will help you undertake a risk assessment.
What are other risks that can Impact on working at Heights?
The potential risks associated with working at height can be compounded by other hazards. The following list is not exhaustive and a full risk assessment, by a competent person, should always be undertaken prior to work at height.
- Overhead power supplies – electrical shock.
- Corroded or fragile upper level surfaces.
- Poorly constructed, secured and or positioned scaffolding.
- Weather elements – e.g. wind or rain.
- Slippery or unstable surfaces.
- Working alone.
Managing the risk of working at height
How do I control the Risks of Falls from Height?
First, you must consider whether you can eliminate the risk, if this is not reasonably practicable then you must minimise that risk – this is called the hierarchy of controls.
* See Risk Assessment Section: This health and safety risk assessment process will further help you understand how to use the hierarchy of controls.
see also:
WorkSafeNZ. Working at Height Toolkit. Fact sheet 1. Planning a safe approach to working at height. June 2015.
WorkSafeNZ (Ministry of Business, Innovation & Employment) Best practice guidelines for working at height in New Zealand. April 2012
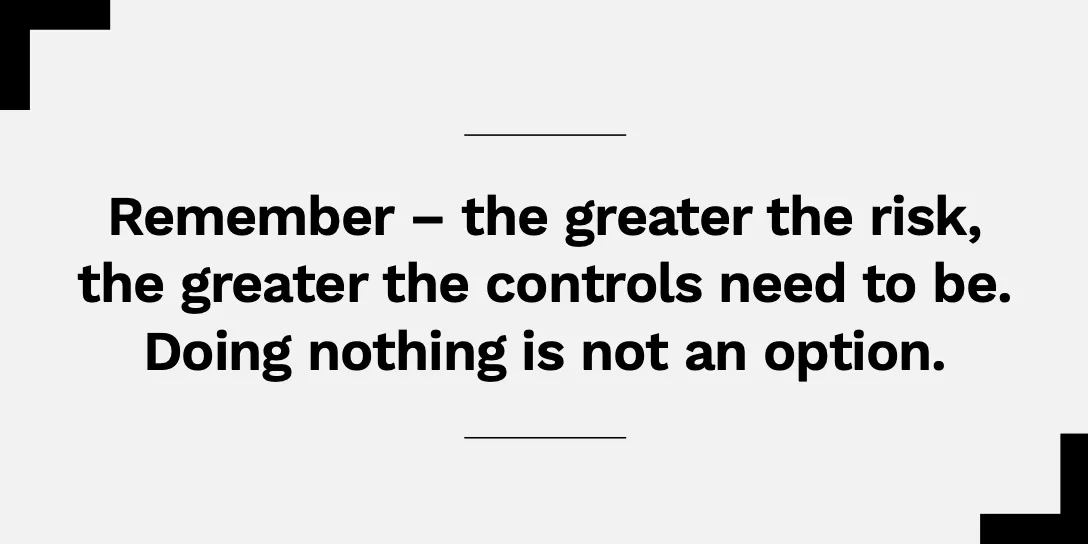
Elimination is the most effective control method.
You could eliminate the risk of working at height by:
- removing the requirement for the task, if practicable under the circumstances;
- using long handled tools from ground level;
- building structures at ground level and lifting them into position when finished; or
- ensuring equipment that may require maintenance is placed close to the ground
Elimination can be best achieved at the design and construction planning stage.
If complete elimination of the risk is not reasonably practicable, you must consider ways to minimise the risk starting by looking at how you could prevent a fall from occurring.
You could minimise the risk by preventing the fall through the use of:
- edge protection;
- a guard railed work platform (such as scaffolding or elevated work platforms);
- barriers to restrict access; or
- a total restraint system to prevent people getting close to the height hazard.
If you cannot prevent a fall then you must look at ways to minimise the harm that could occur from a fall.
Minimising the distance and impact of a fall must only be considered after you’ve exhausted all elimination controls and minimisation controls that would have prevented the fall in the first place. You can minimise the distance and impact of a fall using:
- a fall arrest (harness) or work positioning system; or
- safety nets or soft-landing systems.
What's the difference between Group Controls and Personal Controls?
As well as the hierarchy of controls, you need to think about controls that will protect multiple people. These are group controls, and the best methods to use as they that don’t require active judgement by individuals to keep themselves safe – for example scaffolding or a safety net.
Personal controls only protect the individual using the control and rely on the user using them correctly to ensure their safety.
See also
WorkSafeNZ (Ministry of Business, Innovation & Employment) Best practice guidelines for working at height in New Zealand. April 2012
How do I select the right Equipment?
When deciding what control to use, as well as considering the hierarchy of controls and group versus personal controls, you should also think about other factors that may affect the success of your controls. See the table below as a guide.
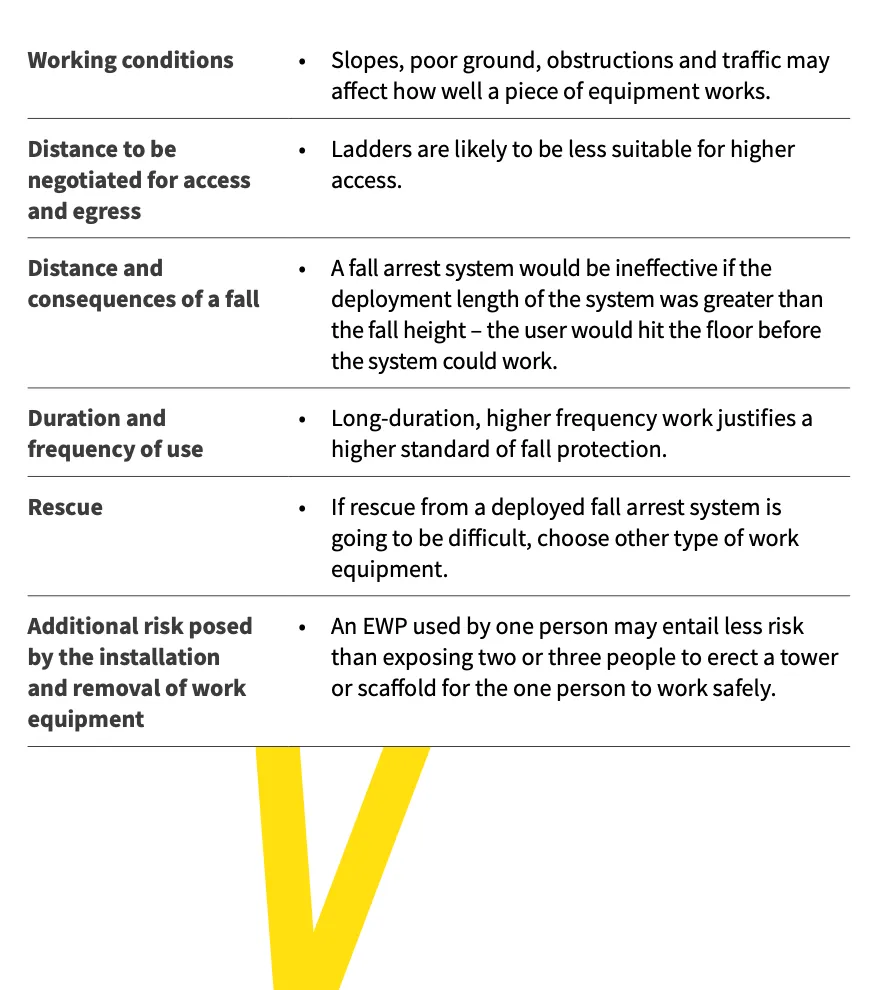
What type of controls can you use?
There are many different types of controls that you could use for eliminating or minimising the risks associated with working at height.
The primary controls used within the screen industry are detailed further risk-specific chapters.
Depending on the set circumstances, you may also wish to consider the below controls, you can find out more information about these control methods in WorkSafe guidance.
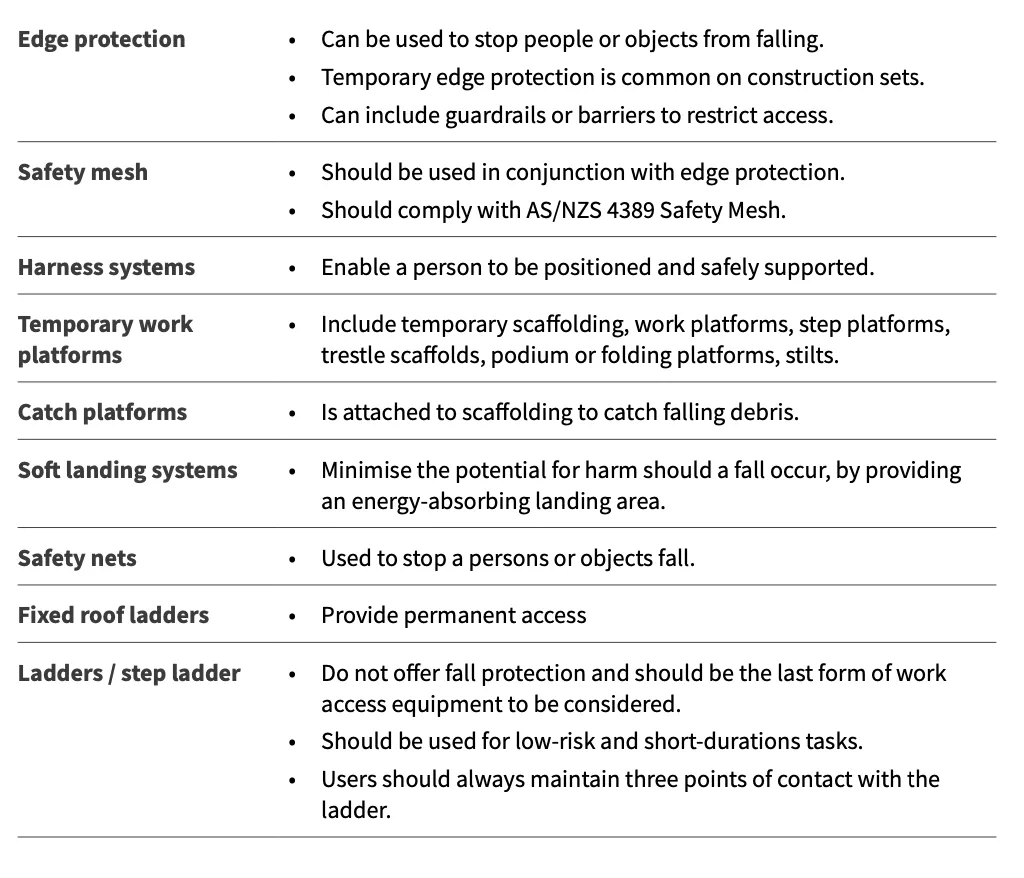
Rescue plan
All working at height activities, where it has been identified that a fall would require a rescue mission or any potential harm, would require an immediate medical response should have a rescue plan.
Factors to be considered while developing a rescue plan include:
- the location of the work area in terms of the accessibility to appropriate medical facilities;
- ensuring there is an adequately trained person on ground level able to initiate the rescue plan in the event of a fall;
- communications;
- the type of rescue equipment required and its proximity to the work area; and
- first aid capabilities.
Adequate information and training on the rescue plan should be provided to those working at height, and any potential rescuers.
The rescue plan should be formally tested, before work commences, to ensure effectiveness.
Under no circumstances is a person to be used in suspended casualty emergency drills. The drills should be simulated using a mannequin or other suitable method.
Click HERE to download the RESCUE PLAN TEMPLATE
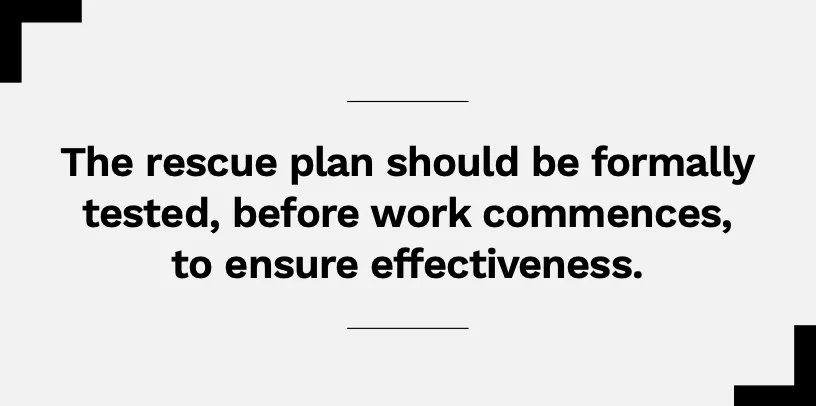
Responsibilities
Funders
Funders should:
- be assured, through the provision of the production’s health and safety plan, that the funding provided is adequate to provide controls for working at height tasks.
Production Company
In pre-production, production companies (likely to have primary responsibility over health and safety on the production) should:
- consider the potential risks associated with working at height when planning and allocating tasks;
- ensure the potential risks associated with working at height are appropriately managed, either eliminating or minimising them; and
- engage competent persons to oversee and undertake all working at height tasks associated with the production.
Producer / Production Manager / Art Director / Construction Manager / Heads of Department
As these roles have oversight across these elements of production, they should (during pre-production and the production):
- ensure to engage competent people to implement working at height tasks;
- consider the potential risks associated with working at height when planning and allocating tasks;
- manage the potential risks associated with working at height, either eliminating or minimising them; and
- engage competent persons to oversee and undertake all working at height tasks associated with the production.
Assistant Director/s
The Assistant Director/s should ensure the potential risks associated with working at height are discussed with all cast and crew during health and safety inductions and / or as required if circumstances on the set change.
Health and Safety Officer
The Health and Safety Officer should ensure potential risks associated with working at height are discussed with all cast and crew during health and safety inductions and / or as required if circumstances on the set change.
Training
Insufficient training for the task being carried out is one of the primary contributing factors to injuries caused by working at height.
As part of all PCBUs primary duty of care to provide and maintain a safe and health work environment, they must ensure workers have had the necessary training to allow them to undertake their work safely.
Anyone who has direct oversight of a worker undertaking a working at height task should ensure they are adequately trained and competent in their work. This will often be the Head of Department.
Things to think about include, does the worker have:
- basic training to competently undertake the task safely; and
- basic training / experience teaching them how to ensure the risk control is effective, including use of personal protective equipment?
Or do they require:
- a specific certificate or qualification to operate the equipment or undertake the task; or
- supervision by a competent person, if they are new or don’t have the required level of training?
WorkSafe’s guidance outlines the levels of compliance and competency required for specific working at height tasks and control.
References
Click HERE to download the QUICK GUIDE checklist for Working at Height
Click HERE to view WorkSafe's overview on Working at Height
Read: A GUIDE FOR SAFE WORKING PRACTICES IN THE NEW ZEALAND THEATRE & ENTERTAINMENT INDUSTRY
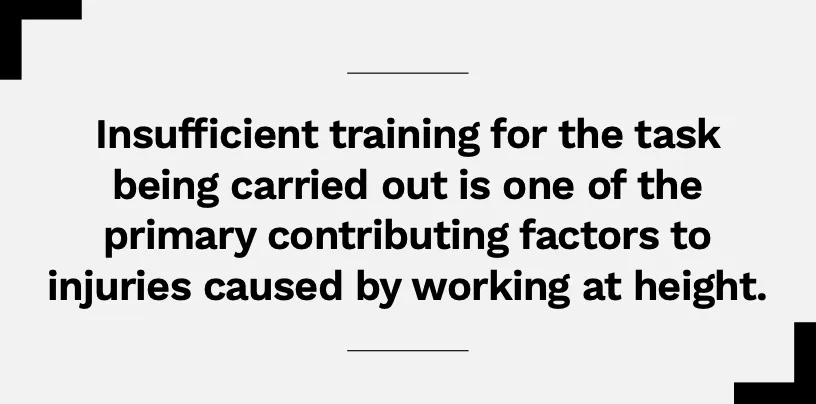
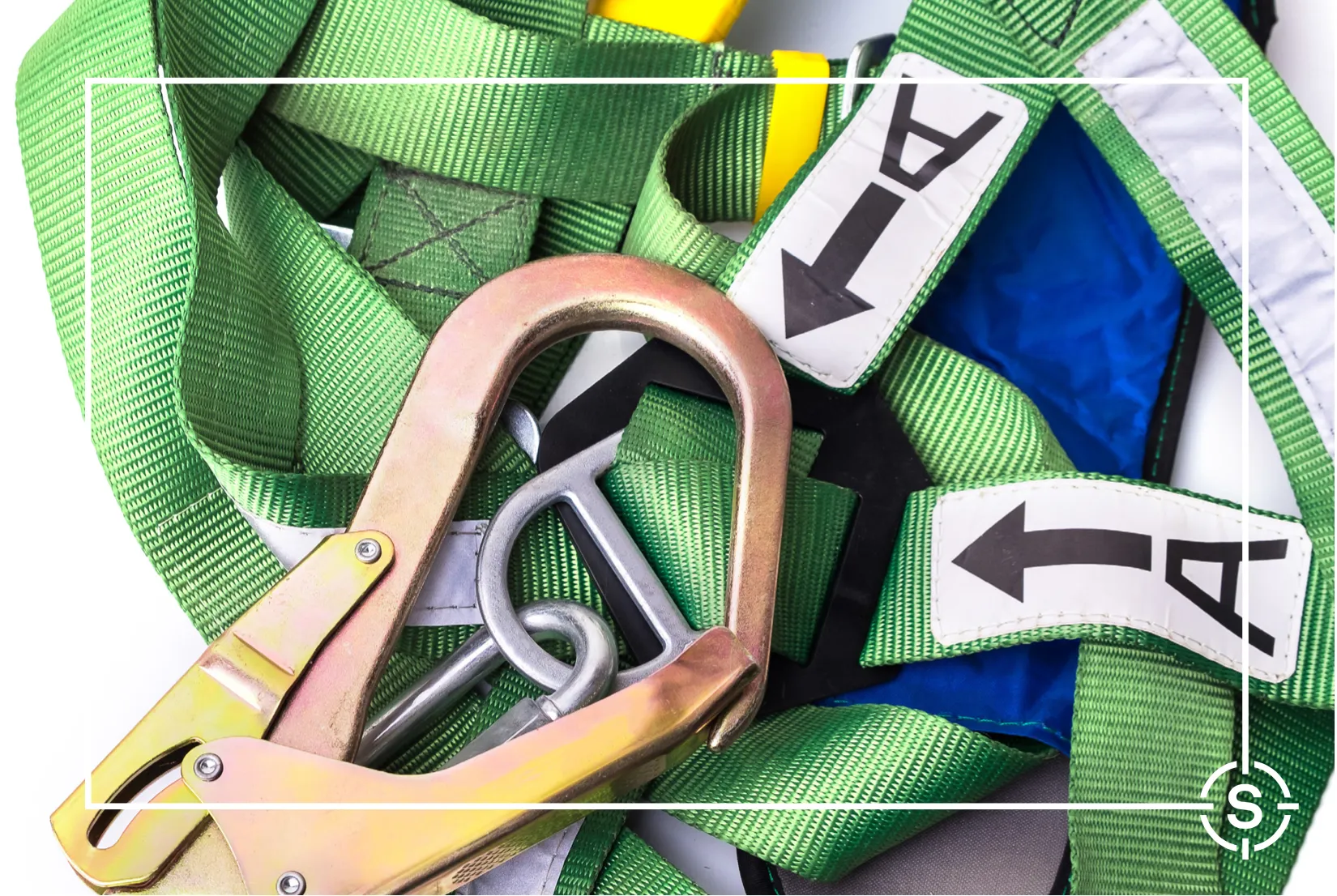
Working at Height
Scaffolding
This chapter relates to the chapter on working at heights and provides guidance on using scaffolding on a production set. It is primarily based on New Zealand legislation and guidance issued by WorkSafe NZ.
Who needs to read this?
All workers who undertake tasks using scaffolding should read and understand the section on minimum responsibilities.
Roles that have specific responsibilities, or influence, over setting up or managing work conducted using scaffolding should read the section on ‘planning and guidance considerations’ – this includes producers, directors, production managers, art directors, construction managers, heads of departments, assistant directors and health and safety advisers.
Definitions
Scaffolding is any advanced scaffolding, basic scaffolding or suspended scaffolding or any framework or structure, of a temporary nature, used or intended to be used for:
- the support or protection of persons carrying out construction work or work connected with construction work, for the purpose of that work; or
- the support of materials used in connection with any such work, and includes:
- ~any scaffolding constructed as such and not dismantled, whether or not it is being used as scaffolding; or
- ~any coupling device, fastening, fitting, or plank used in connection with the construction, erection or used of scaffolding.
Scaffolding process is the planning for and/or the design, erection, inspection, alteration, use or dismantling of any scaffolding and/or related components.
This includes all structures constructed using scaffolding components, such as falsework, temporary grandstands, lighting towers and stair access towers.
What risks do I need to look out for?
- Falls
- Collapse of the structure
- Equipment falling from the structure
- Wind
Minimum responsibilities
Everyone who undertakes tasks using scaffolding should read and understand this section.
Workers should:
- ensure equipment being ferried up and down is properly secured and belayed;
- secure equipment being used on the scaffolding;
- leave mobile scaffolding if it is being moved; and
- only erect, alter and dismantle scaffolding if they have been adequately trained and have suitable experience with the type of scaffolding being used – see the section on training below for more information.
Planning and guidance considerations
Everyone who has responsibilities, or influence, over setting up or managing work conducted using scaffolding should read and understand this section, as well as the minimum responsibilities for everybody.
This includes the production company, producers, directors, line producers, art directors, construction managers, heads of departments, assistant directors and health and safety advisers
Person in charge
The person in charge / those with responsibilities, or influence, over setting up or managing work conducted using scaffolding should ensure all scaffolding:
- is used for the purpose for which it was built;
- complies with the Scaffolding, Access & Rigging New Zealand (SARNZ) Best Practice Guidelines for Scaffolding in New Zealand or equivalent guidelines or a higher standard;
- is erected, altered and dismantled by persons who have been trained and have suitable experience with the type of scaffolding being used;
- from which a person or object could fall more than five metres, as well as all suspended scaffolds, is:
- ~ erected, altered and dismantled by or under the direct supervision of a person with an appropriate certificate of competency;
- ~ this work must be notified to the Ministry of Business, Innovation and Employment as particularly hazardous work;
- has a minimum clearance of four metres from overhead live electric power lines.
They must also:
- ensure that if a scaffold is altered, modified, tampered with and/or appears to be unsafe, the scaffold is not used until it has been checked and certified as safe by a competent person as outlined in the SARNZ Best Practice Guidelines for Scaffolding in New Zealand;
- know the safe working load of the scaffolding and adhere to it;
- always consider the effect of the weather on the use of scaffolding in particular wind.
All scaffolding should have:
- safety rails to prevent falls, with a mid-rail if higher than three metres; and
- ladders fixed in place – only ladders should be used for climbing.
Training
The PCBU, likely to be the production company, must ensure workers are either sufficiently experienced to do their work or are adequately supervised by an experienced person, as well as adequately trained in the safe use of equipment in the workplace.
Anyone erecting scaffolding should:
- be competent (or in the case of trainees, supervised by a competent person) for the type of scaffolding work they are undertaking; and
- have received appropriate training relevant to the type and form of scaffolding they are working on.
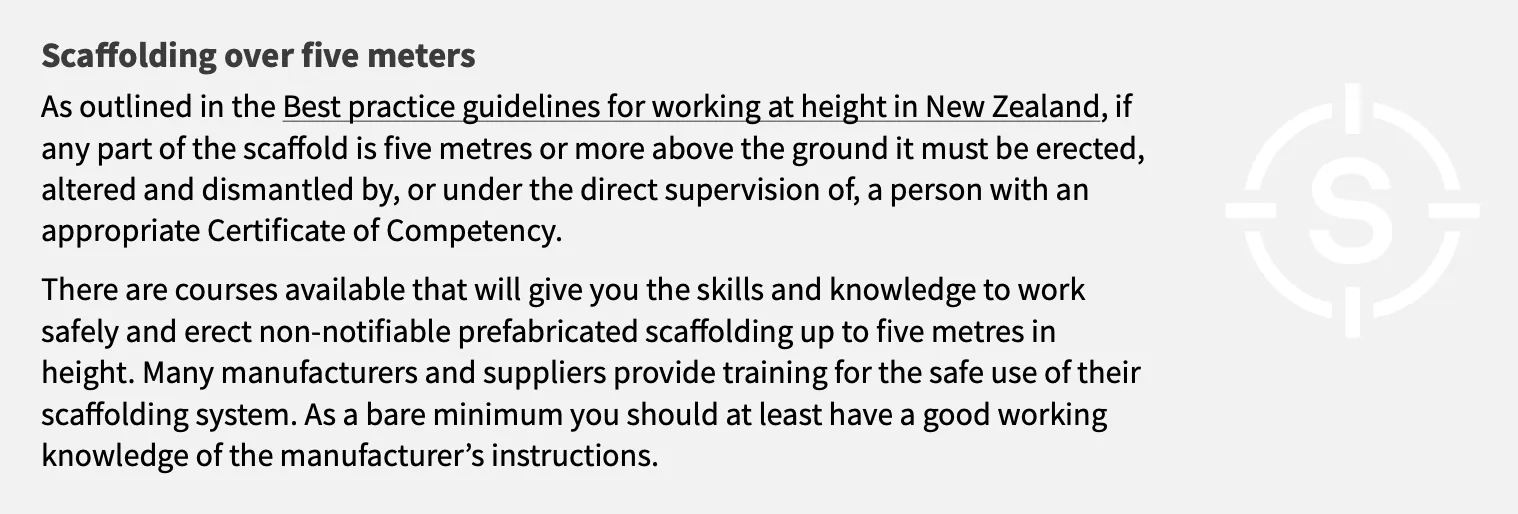
Mobile scaffolding
Where work is performed using mobile scaffolds, the scaffold should be erected by a competent person and used in accordance to the manufacturer’s specifications.
Certificates of competency
Certificates of competence are issued by Scaffolding, Access & Rigging New Zealand Inc (SARNZ)5 under delegated authority from WorkSafe NZ.
To be issued with a certificate of competence individuals need to provide evidence of:
- training to national certificate level or an equivalent international qualification; and
- recent relevant industry experience; or
- holding a current certificate of competence requiring renewal and meeting the requirements of regulations 31 and 35 of the HSE Regulations 1995.
Ongoing certification requires continued involvement in the industry and proof of continued competence.
National certificates
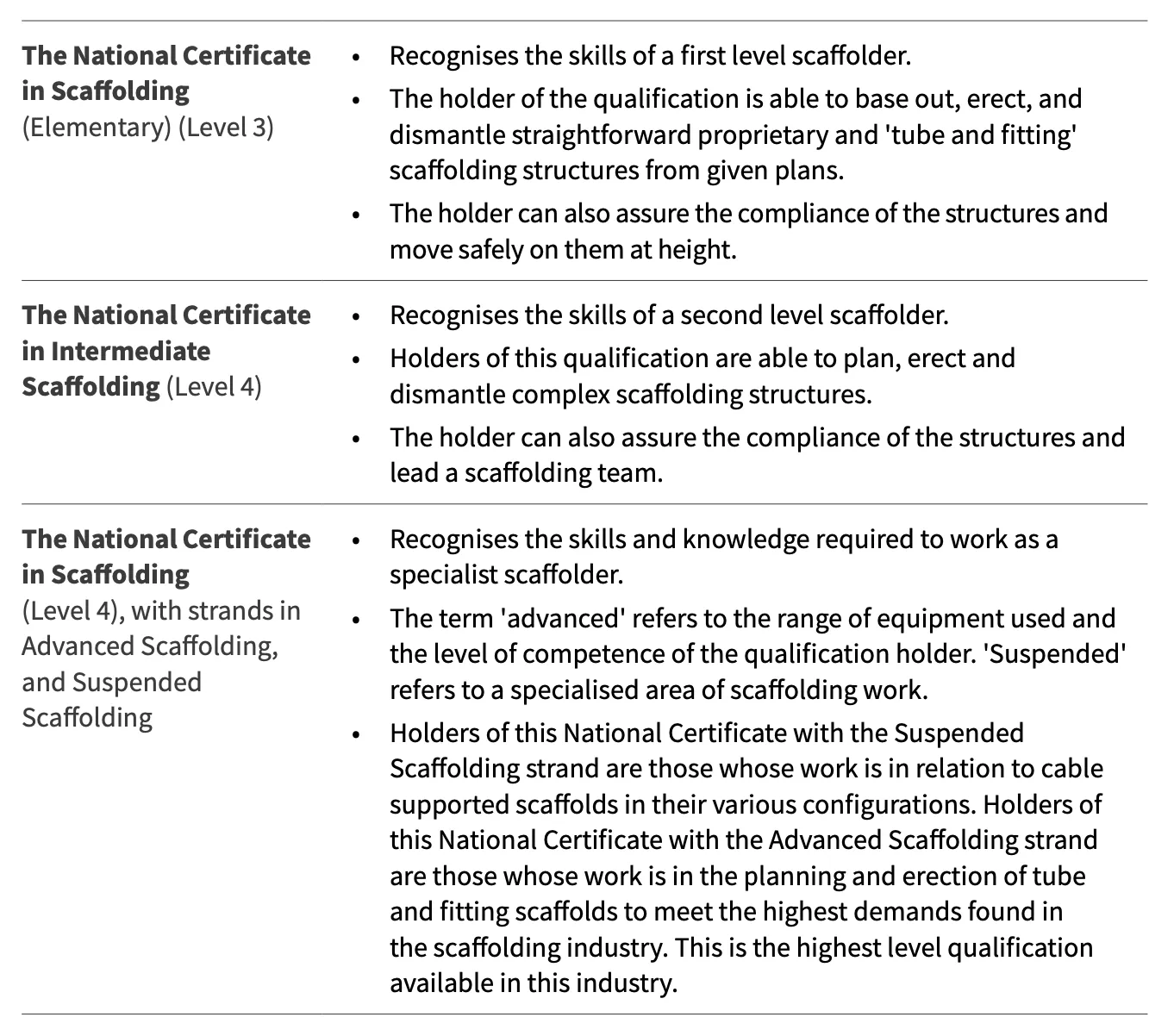
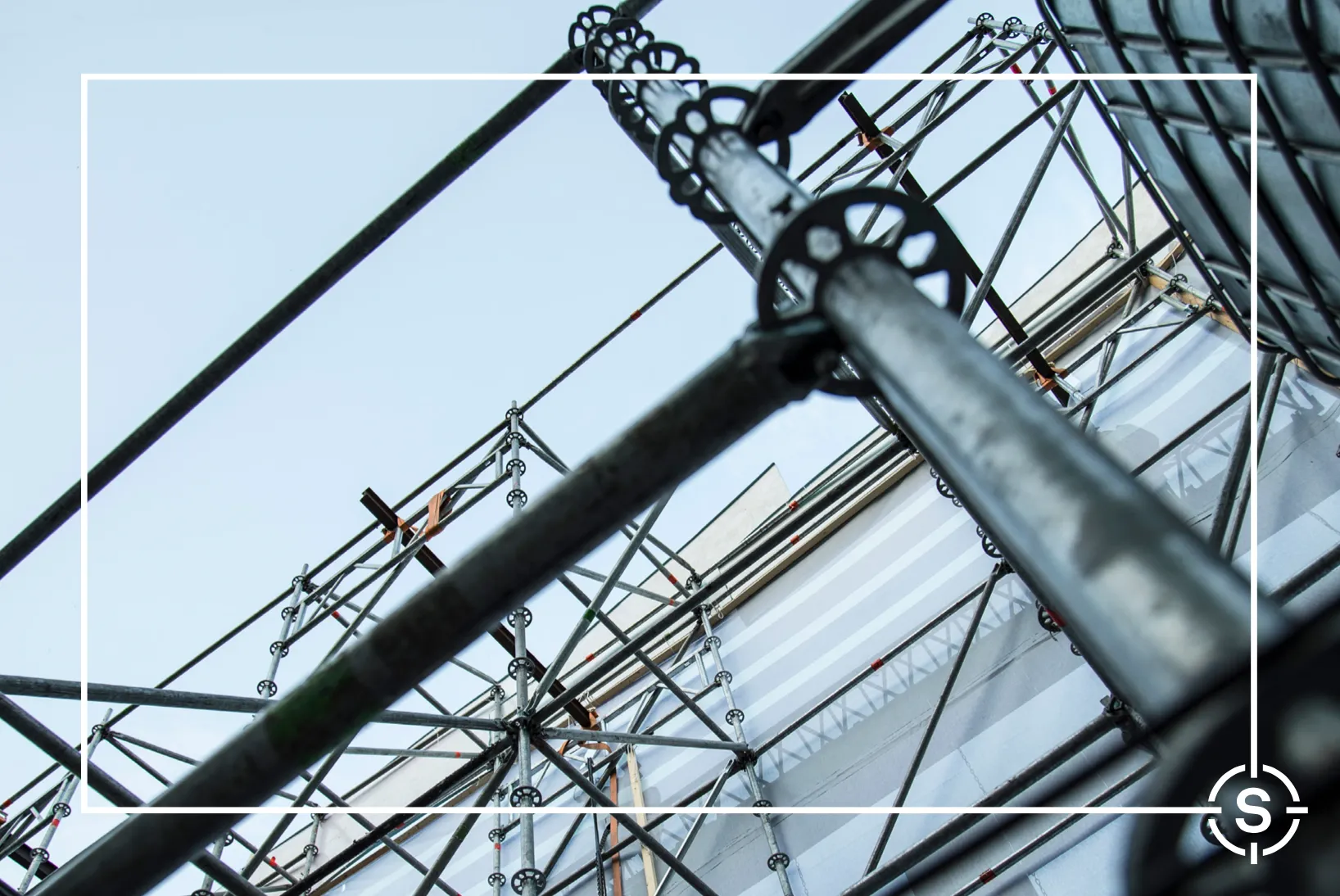
Working at Height - Scaffolding
Cranes – camera
This chapter relates to the chapter on working at heights and provides guidance on using camera cranes on a production set.
This guide is primarily based on New Zealand legislation and guidance issued by WorkSafe NZ and the Ontario Ministry of Labour.
Who needs to read this?
All workers who undertake tasks using camera cranes should read and understand the section of minimum responsibilities.
Roles that have specific responsibilities over setting up and managing camera cranes should also read and understand the planning and considerations section
– this includes producers, directors, production managers, heads of departments, assistant directors, grips, and health and safety officers.
Definitions
Camera cranes means manually powered counterbalanced cranes and motorised telescoping cranes used to position cameras.
What risks do I need to look out for?
- Crane tipping over
- Electric cables and wires
- Imbalance when camera equipment is taken off and on
- Imbalance when people step on or off counterbalance cranes
- Overhead obstructions
- Persons being struck by crane or being crushed against crane
- Structural collapse of crane
Minimum responsibilities of working on camera cranes
Everyone who undertakes tasks using camera cranes should read and understand the section.
Workers should:
- only operate the equipment if they are trained and competent in the operation of the crane they are using;
- only operate the equipment in accordance with the operating instructions and appropriate codes of practice;
- ensure the safe working load of equipment is not exceeded;
- wear a safety harness where directed; and
- use seats provided where practical.
Planning and guidance considerations for camera cranes
Everyone who is responsible for, or has influence over, an activity or task in relation to setting up and managing camera cranes should read and understand this section, as well as the minimum responsibilities section.
Minimum Clearance From Overhead Electric Power Lines
There are minimum clearances from overhead conductors depending on their voltages.
Unless otherwise specified, maintain a minimum of four-metre clearance between the crane including any person or equipment on it, the swing of the arms, and the overhead conductors.
Producer / Production Manager
The Producer / Production Manager, as the person ultimately in charge of the task, should:
- consult with the director of photography and key grip as to the adequacy of any specific equipment to be used for a particular sequence or shot given the conditions; and
- ensure there is a designated person in charge of the camera crane.
The Producer / Production Manager should consider appropriate support and ensure budget and/or personnel are available to provide the minimum requirements for the production; this includes:
- hiring competent people with an appropriate or necessary level of training, experience and/or qualifications with respect to the requirements of the production;
- the number of people hired in relation to the size of the project; and
- ensuring sufficient resources, including budget, are allocated to enable appropriate and safe practices and satisfy the minimum requirements under law.
Person in charge
The key grip or their nominated representative should:
- ensure there is an appropriate communications system for those operating the crane;
- ensure operators are trained and competent
- ensure at least two people are designated as crew for the camera crane;
- consider the surface, as some cranes are designed for flat surfaces, while others are designed for operating on uneven ground – extra care must be taken for camera cranes operating on uneven surfaces;
- consider any potential overhead obstructions, and ensure that adequate clearance is maintained at all times from overhead obstructions;
- consult, if required, with the local power supplier regarding the minimum clearance from overhead electric power lines;
- ensure the crane is attended at all times while being prepared for use or while in use;
- ensure manned balanced camera cranes are adequately crewed for safe operation;
- ensure the area covered by the swing of the camera crane arms is a limited access area;
- ensure that cranes intended to be mounted by crew members are fitted with seats and restraints – workers riding the crane should use the seats and restraints where practical; and
- ensure that manual operated cranes are stress tested.
Assistant Director
The Assistant Director should ensure:
- the use of a camera crane is noted in the safety section of the call sheet; for example
~~ "a camera crane will be used while filming scene [XXXXX]. Please keep its working radius clear of people and equipment and respond to the requests of the grip in charge".
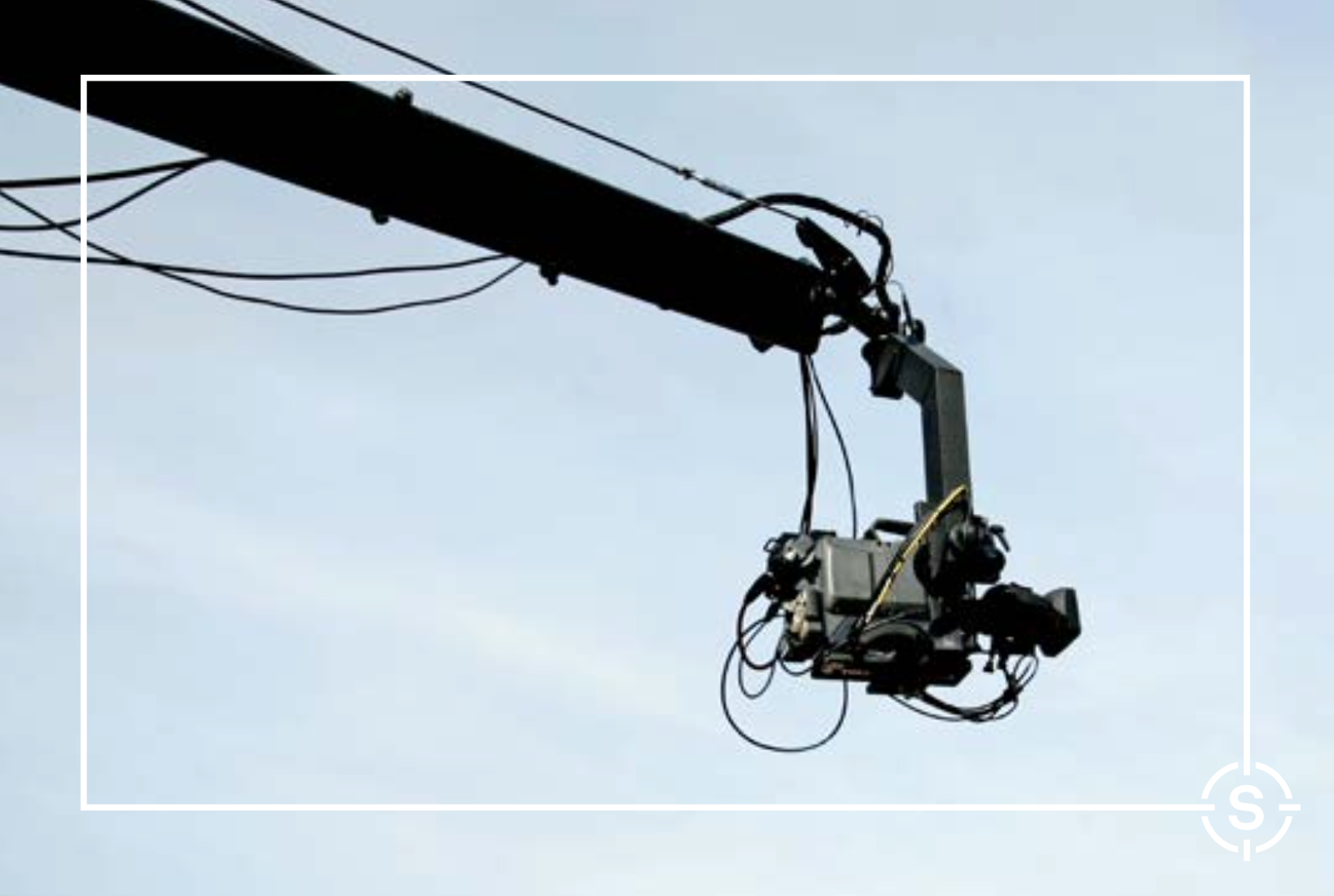
Working at Heights - Cranes – camera
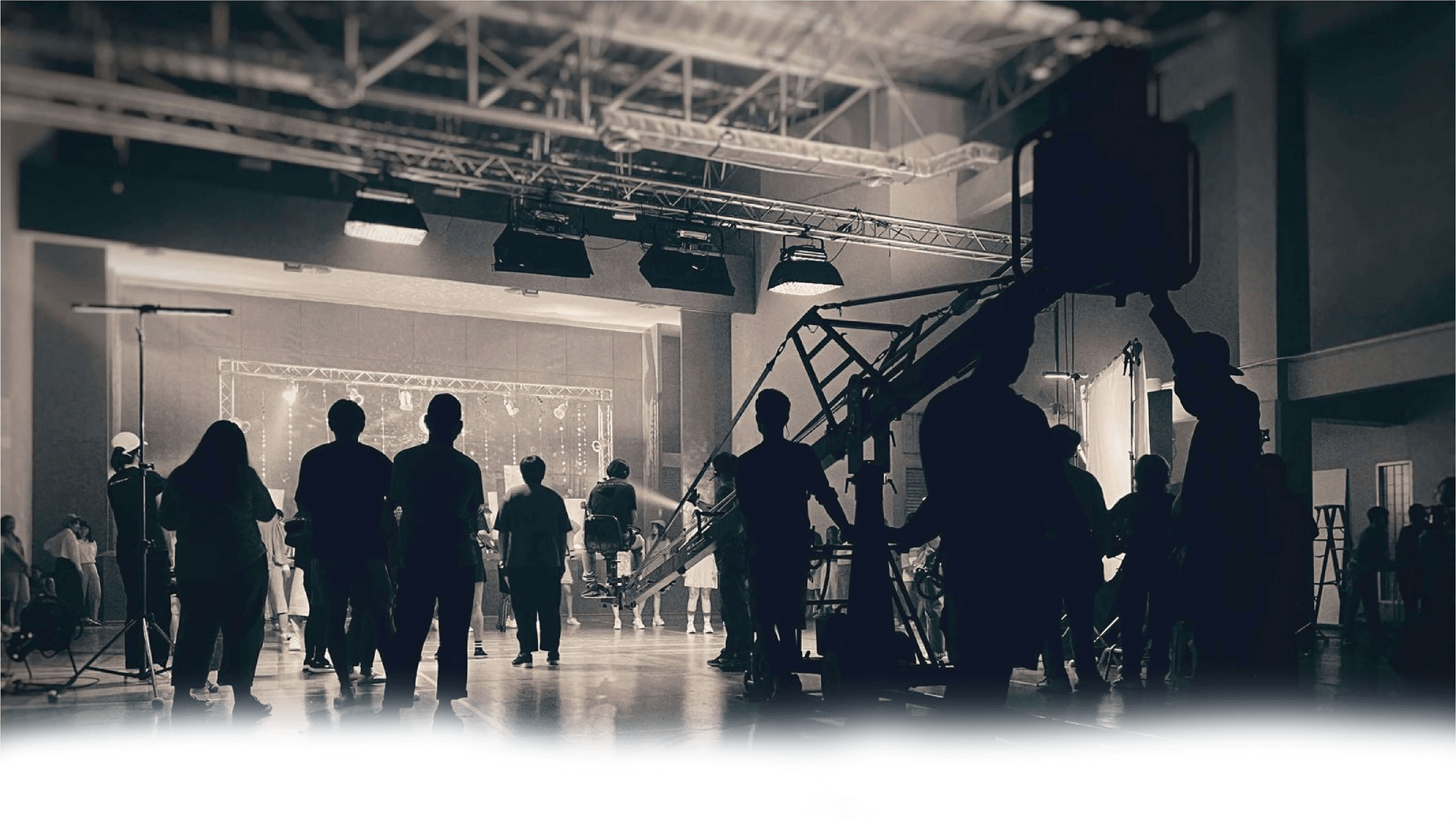