Hazardous Substances
Ngā Matū Mōrearea
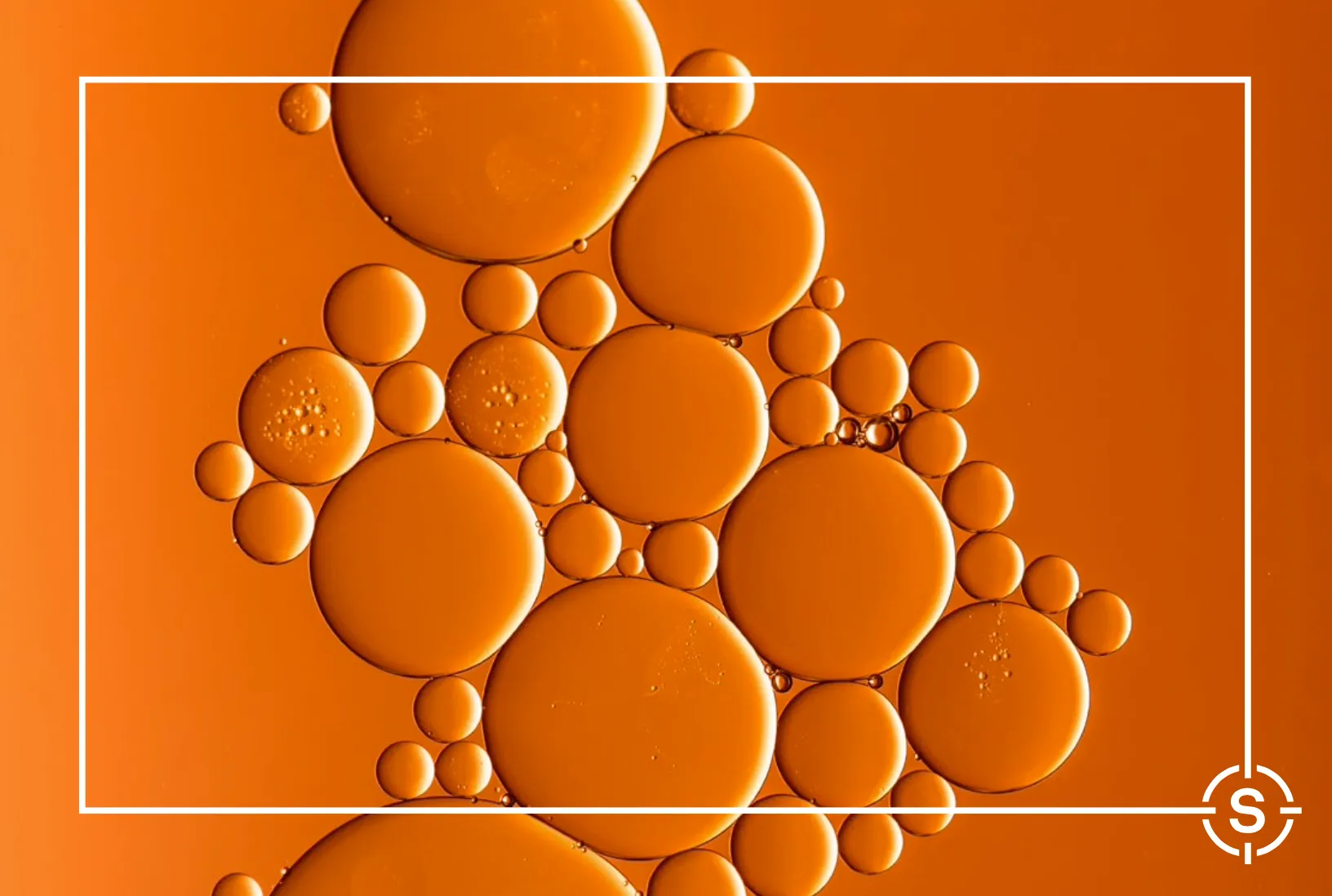
Hazardous Substances
Anyone using a hazardous substance should have a thorough understanding of the Health and Safety at Work (HazardousSubstances) Regulations 2017, which set out the rules for work-related activities involving hazardous substances.
The Hazardous Substances Toolbox website also provides comprehensive information on how you can work safely with hazardous substance.
This chapter provides basic guidance and key things for you to consider in relation to working with hazardous substances on a production.
Who needs to read this?
All workers who undertake work with, or work that interacts with, hazardous substances should read and understand the section on ‘minimum responsibilities’ and ‘managing hazardous substances’.
Roles that have specific responsibilities, or influence, over work with hazardous substances should read the section on ‘planning and guidance considerations’ – this includes producers, directors, production managers, line producers, heads of departments, assistant directors and health and safety officers.
Definitions
Hazardous substance means, unless expressly provided otherwise by regulations, any substance —
- with one or more of the following intrinsic properties – explosiveness, flammability, a capacity to oxidise, corrosiveness, toxicity (including chronic toxicity), ecotoxicity, with or without bioaccumulation; or
- which on contact with air or water (other than air or water where the temperature or pressure has been artificially increased or decreased) generates a substance with any one or more of the properties specified above.
MSDS means Material Safety Data Sheets; these provide concise safety and health information about the hazards and safety precautions of the substance and should be available for all products.
Specific Risks
- Explosiveness
- Flammability
- Health effects
- Infection
- Toxicity - both short and long-term effects
*NOTE: Substances may be inhaled, ingested or absorbed into the body. The effect is dependent upon the substance involved and the degree of exposure.
What we need to know about Hazardous Substances
Many hazardous substances are in daily use on a production set. While all hazardous substances can be safely used if proper work methods are adopted, safer, alternative substances and/or work methods should be used instead of using highly hazardous substances where practicable.
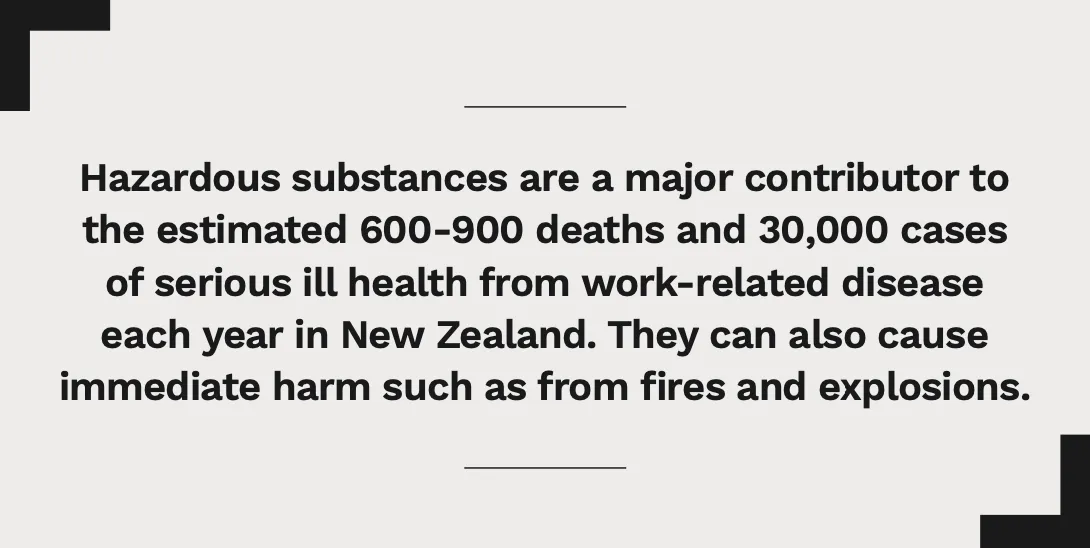
What is a Hazardous Substance?
A hazardous substance is any product or chemical that has explosive, flammable, oxidising, toxic, corrosive or ecotoxic properties.
Explosive: explodes or causes explosion.
Flammable: ignites easily and burns rapidly.
Oxidising: could be gaseous, solid or liquid and can cause or intensify fire and explosion.
Toxic: can harm people if it enters the body through contact, being inhaled or ingested. The effects can range from mild to life-threatening, and can be immediate or long-term.
Corrosive: can cause severe skin burns and eye damage. Ecotoxic: is toxic to the environment.
All hazardous substances should have an MSDS, provided by the supplier of the substance – these provide concise safety and health information about the hazards and safety precautions of the substance.
*See: WorkSafe / What the Hazardous Substances Regulations mean for you
What could go wrong?
Emergencies you need to consider and plan for include:
- a worker being poisoned by ingesting or inhaling a toxic substance;
- a worker being burnt by a corrosive substance;
- a fire caused by flammable or oxidising substances; or
- hazardous substances leaking or spilling from their containers, injuring people and contaminating land and waterways.
*See: WorkSafe / Emergency plans
Certified Handler requirements
Some work with highly hazardous substances must be carried out by a certified handler.
Certified Handlers need to:
- meet certain competency requirements, and
- receive workplace-specific information, training and instruction by or on behalf of the business, and
- obtain a certified handler compliance certificate from a compliance certifier.
You need a certified handler for:
• substances that require a controlled substance licence (CSL), such as most explosives, fumigants and vertebrate toxic agents (VTAs); and
• acutely toxic (6.1A and 6.1B) substances.
*See: WorkSafe / Certified handler requirements
Minimum Responsibilities
Everyone on a screen production who does, or could, work with hazardous substances, should read and understand this section.
All workers must:
- follow all health and safety information, training and instruction they have received;
- must be aware of what personal protective equipment they are expected to provide themselves and what will be provided by the production;
- follow instructions provided by the person in charge of any activity that involves the use of, or is conducted near, hazardous substances; and
- know escape routes when working around or near hazardous substances; if they are unsure of the escape route check with the 1st assistant director to learn the escape route before entering the work area.
Managing Hazardous Substances
Anyone who operates or is responsible for, or has influence over, hazardous substances must read and understand this section, as well as the sections on minimum responsibilities and planning and guidance considerations and responsibilities.
Create an Inventory
First and foremost, it’s important to know what hazardous substances are being stored or used on a production.
- Make an inventory of all the hazardous substances manufactured, used, handled or stored at your workplace including hazardous waste.
- Keep your inventory up-to-date and accurate.
- Make sure your inventory is readily accessible to emergency services workers.
The Hazardous Substances Calculator will help you create an inventory and work out what key requirements you need to meet, based on the hazardous substances you use, handle, manufacture and store at your workplace.
*See: WorkSafe / Inventory
Assess and Manage the Risk
All hazardous substances have a level of risk.
If there is no alternative and it is necessary to use hazardous materials on the production, those responsible for the use of the hazardous substance need to identify all risks associated with the hazard and decide on how to manage the risk by minimising it.
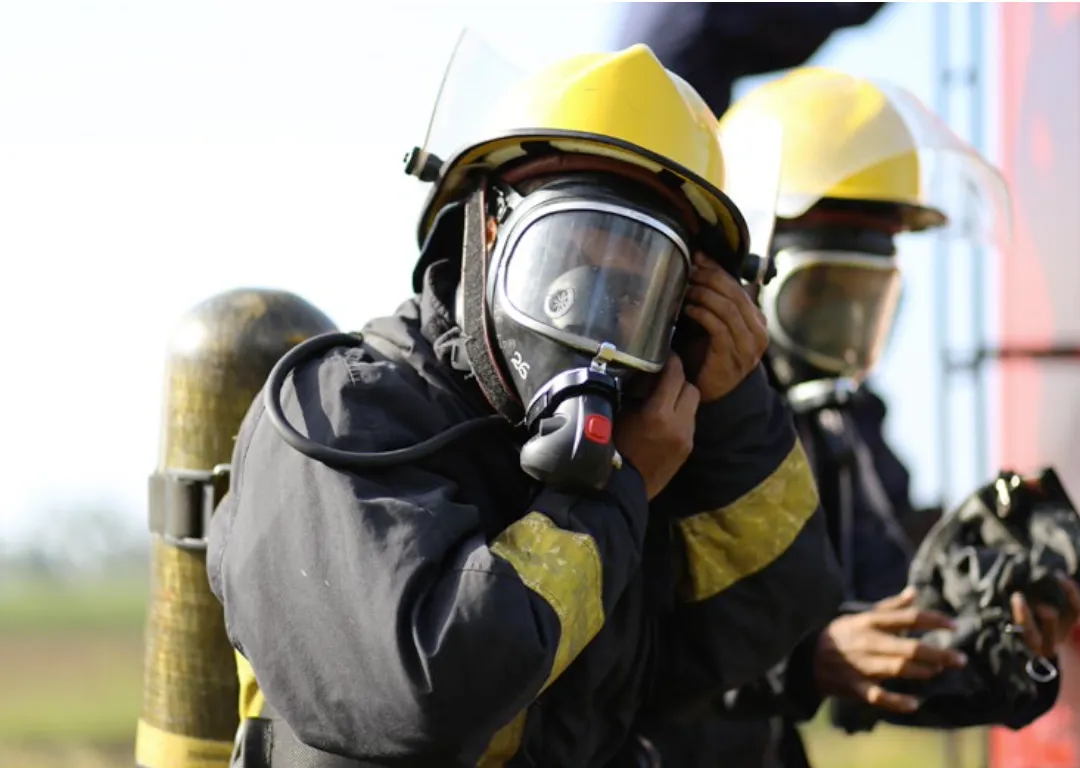
Minimising Risk
If you cannot eliminate the risk, there is a hierarchy of minimisation options.
*See: WorkSafe / What the Hazardous Substances Regulations mean for you
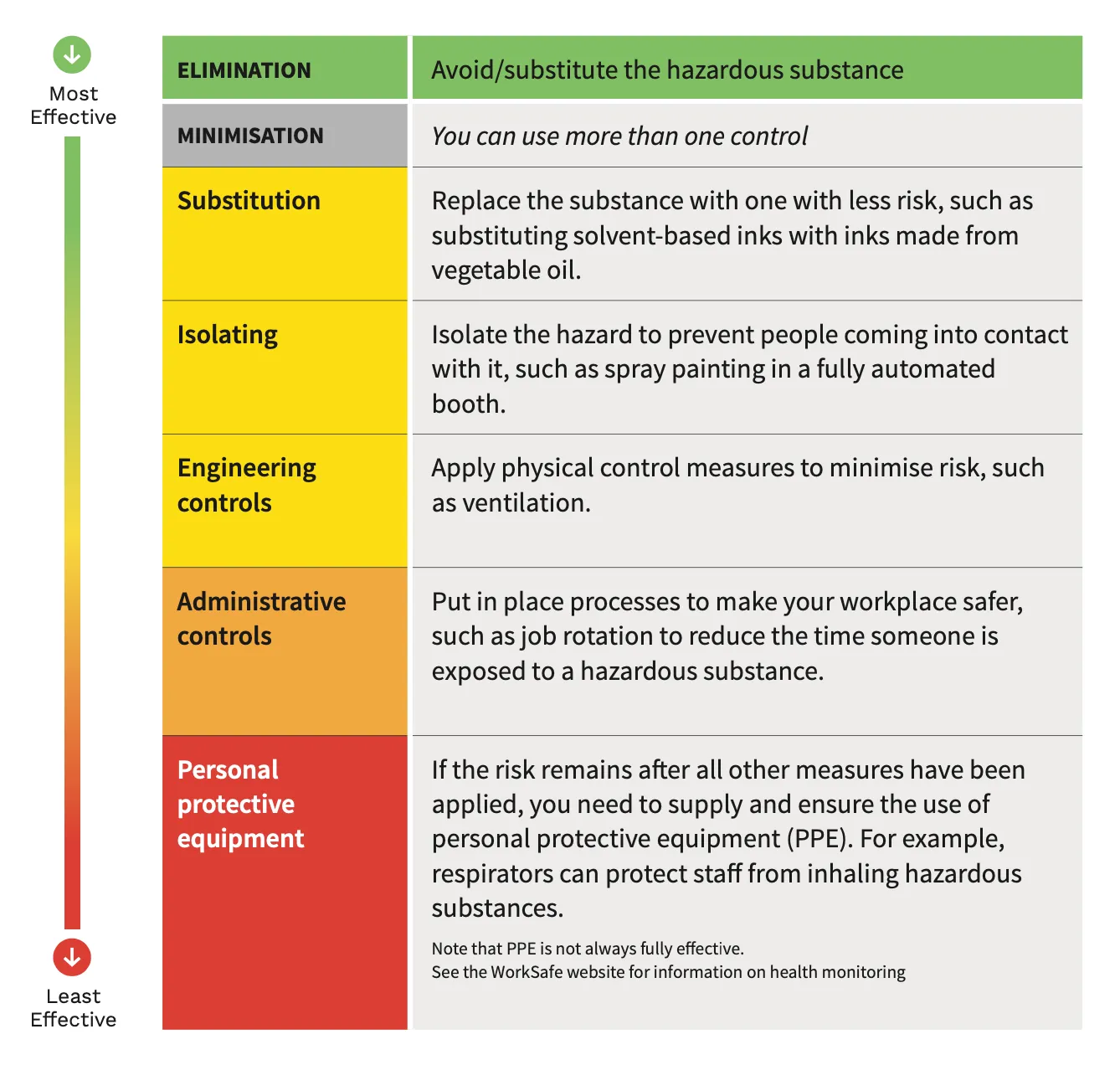
Keeping People Safe
If hazardous substances are used on a production, there are multiple ways you can keep workers and visitors safe.
Inform and Train Workers
Ensure everyone who works with or around hazardous substances has the experience and knowledge to do so safely.
Inform workers of hazardous substances on the production, and the control measures in place during the daily health and safety briefing and place this information on the call sheet.
Label Containers
You need to ensure containers of hazardous substances are always clearly and correctly labelled, this includes:
- substances that have come from a supplier and are therefore already labelled;
- substances that you decant or transfer into a smaller container at your workplace;
- stationary tanks, process containers and transportable containers; and
- hazardous waste.
*See: WorkSafe / Labelling
Install Signs
Place clearly visible signs at entranceways, and on buildings, or in outdoor areas, where substances are used or stored. They should inform people of what hazardous substances are present, the general type of hazard and what to do in an emergency.
*See: WorkSafe / Signs
Store Hazardous Substances Safely
Where and how you store hazardous substances will depend on the type of substance and the amount you have.
The Health and Safety at Work (Hazardous Substances) Regulations 2017 set out the requirements for storing different types, classes and quantities of hazardous substances in different situations.
The MSDS includes handling and storage information about the substance.
*See: WorkSafe / Storage
Plan for an Emergency
If using hazardous substances an emergency plan should be developed, it must:
- address all ‘reasonably foreseeable’ emergencies;
- state any special training needed to deal with an emergency involving each substance;
- include the inventory of hazardous substances present at the workplace;
- include a site plan showing all the hazardous substances locations in the workplace; and
- advise how you will:
- ~ call emergency services
- ~ warn people at the workplace and nearby about the emergency
- ~ advise people how they can protect themselves
- ~ help or treat any one injured in the emergency
- ~ manage the emergency to restrict its effects to the initial area, reduce its severity and if possible, eliminate it.
Fire and Emergency New Zealand (FENZ) can review your plan.
*See: WorkSafe / Emergency plans
Disposal and Recycling
Unused chemicals, and empty chemical containers, are a risk to people, the environment and animals.
You can arrange for unused chemicals to be disposed, or empty containers recycled, through AgRecovery. Information about disposing of products can also on be found on the MSDS.
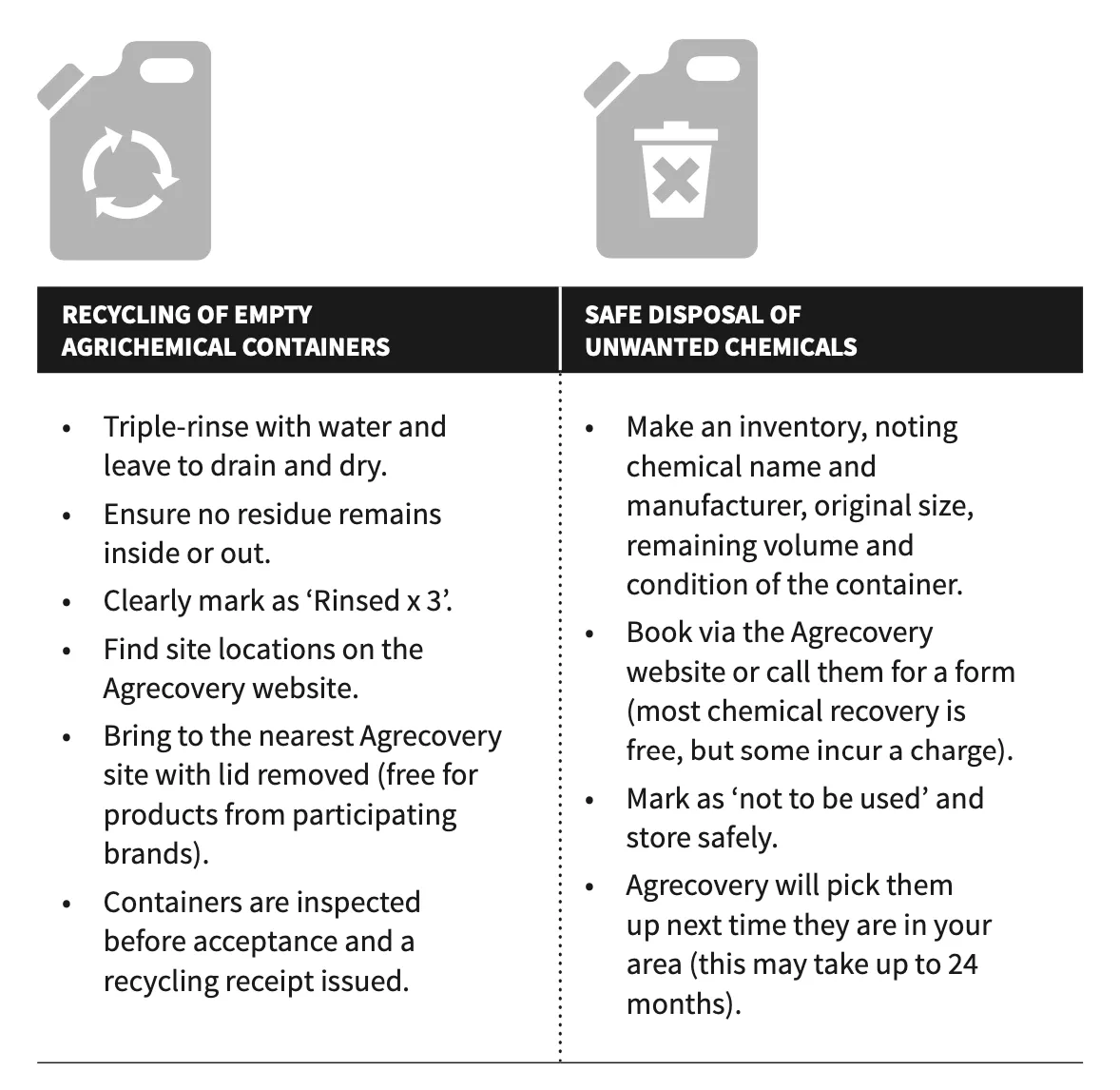
Transport
A certified handler must always be present when explosives are being transported.
Transport of hazardous substances are covered by the relevant transport agency.
Road and rail – the New Zealand Transport Agency
Key points to note:
- Generally, if you're transporting dangerous or hazardous goods, you need a dangerous goods (D) endorsement on your driver licence.
- For transport, dangerous goods are identified with a UN number, a proper shipping name and a diamond-shaped class warning label. Some products also have special marks to warn of hazards that are not indicated by other labels or marks.
- The Land Transport Rule: Dangerous Good 2005 (Rule 45001/1) details how you can transport dangerous goods safely and securely, depending on the nature and quantity of the dangerous goods.
Sea – Maritime New Zealand
Key points to note:
- Controls must be in place to safely manage the hazardous substances.
- An inventory of the hazardous substances you use, handle or store on board must be maintained.
- Anyone who uses or handle hazardous substances must have training to do so.
- The advice on the MSDS must be followed.
- All hazardous substances must be correctly labelled.
- Signs must be displayed to let workers, visitor and emergency service personnel know there are hazardous substances onboard.
Air – Civil Aviation Authority of New Zealand
Key points to note:
- Articles and substances must be properly classified according to a set of standard criteria.
- The packaging used for dangerous goods must meet certain criteria set by the technical instructions.
- The hazards posed by these articles and substances must be identified by markings, package labels and accompanying documentation.
- An airline must have the opportunity to inspect and verify the acceptability of each dangerous goods package as declared by the shipper.
Planning and Guidance Considerations and Responsibilities
Everyone has planning responsibilities for or planning influence over activities that interact with hazardous substances should read and understand this section, as well as the above sections.
This includes funders, the Production Company, Producers, Heads of Department, and Health and Safety Advisors.
Funders
Funders should:
- be assured, through the provision of the production’s health and safety plan, that the funding provided is adequate to provide for competent people to undertake and supervise work with hazardous substances; and
- ensure that all senior contractors have sufficient insurance cover, appropriate to the risk and scale of the work to be undertaken.
Production Company
In pre-production, production companies (likely to have primary responsibility over health and safety on the production) should:
- ensure people who use hazardous substances are competent in their use;
- consider the potential risks associated with hazardous substances when planning and allocating tasks; and
- ensure the potential risks associated are appropriately managed, either eliminating or minimising them.
Producers and Production Managers
As Producers and Production Managers have oversight across the production, they should:
- communicate to all personnel the presence and/or use of hazardous substances;
- provide appropriate information on safety matters should be included;
- ensure workers are provided appropriate personal protective equipment;
- ensure workers are wear appropriate personal protective equipment;
- ensure that emergency and first aid procedures are in place;
- ensure sufficient firefighting equipment is provided and that it is immediately available on set if required; and
- ensure there is a clear access way for emergency and firefighting equipment and vehicles on set.
Heads of Department
As Heads of Department have specific oversight of areas of work that may use hazardous substances for specific task, they should:
- ensure workers using hazardous substances carry the necessary skills, certifications and / or experience;
- ensure hazard identification and risk assessments are undertaken for all activities using hazardous substances, and controls implemented;
- ensure that emergency and first aid procedures are followed;
- ensure personal protective equipment specific for hazardous substance work is provided to, and used by, workers when required;
- communicate to all personnel the presence and/or use of hazardous substances;
- provide appropriate information on safety matters should be included;
- ensure workers are provided appropriate personal protective equipment; and
- ensure workers wear appropriate personal protective equipment.
Health and Safety Officer
The Health and Safety Officer should ensure potential risks associated with hazardous substances are discussed with all cast and crew during health and safety inductions and / or as required if circumstances on the set change.
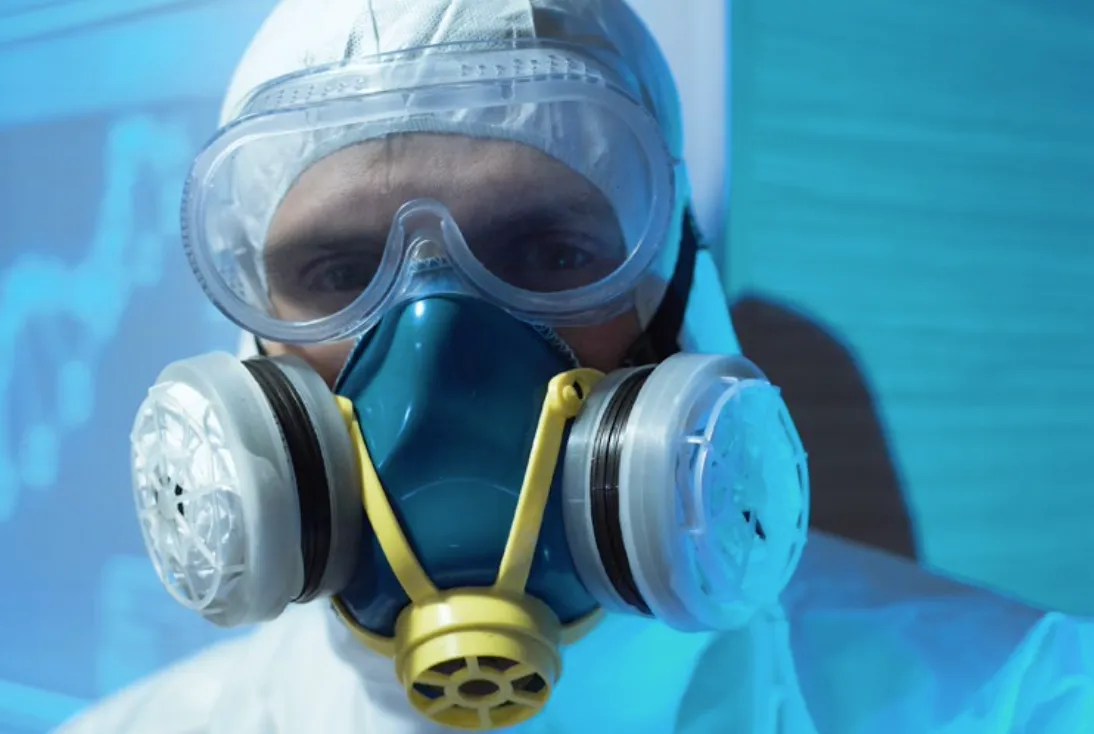
Training and Knowledge
Hazardous substances must only be used by people with knowledge about the substance, its health effects and emergency procedures.
Substances requiring a controlled substance licence (CSL), such as most explosives, fumigants and VTAs, and acutely toxic (class 6.1A and 6.1B) substances, such as certain pesticides and VTAs, need to be handled by a certified handler.
However, in some cases, people who are not certified handlers can handle substances with certified handler requirements, which are outlined in WorkSafe’s quick guide – certified handler requirements.
To check if you need a certified handler in your workplace, enter your substances into the Hazardous Substances Calculator or search the Environmental Protection Authority’s Approved Hazardous Substances with Controls database.
Anyone handling or working with hazardous substances needs to:
- be trained or supervised in safe handling procedures;
- be provided with information and MSDS about the product;
- understand the physico-chemical and health hazards associated with the hazardous substances;
- understand the procedures for the safe use, handling, manufacture, storage and disposal of the hazardous substances;
- ensure their safety, and the safety of others, when using the hazardous substances;
- understand obligations under the Health and Safety at Work (Hazardous Substances) Regulations 2017; and
- know the actions to be taken in an emergency involving the hazardous substances.
Being a certified handler can help fulfil these requirements.