Guidelines for
Unit
Ngā Aratohu
These guidelines have been earmarked as being specific to the above-named department, however, we know that the work carried out during any production area can vary.
Please be aware that many other safety guidelines may also apply to you depending on the type of work you are currently undertaking.
Please also familiarise yourself with all guideline sections to ensure you are fully informed.
Who needs to read this?
The Health and Safety at Work Act 2015 requires all PCBUs to identify drug and alcohol use as a hazard, and therefore eliminate or minimise the risk.
All workers on a production (pre, during and post) should read and understand the section below on ‘Minimum Responsibilities’.
Roles that have specific responsibilities, or influence, over workers should read the section below on ‘Planning and Guidance Considerations and Responsibilities’ – this includes Producers, Directors, Production Managers, Line Producers, Heads of Department, Assistant Directors and Health and Safety Officer.
What we need to know about Alcohol and Drugs
The use of drugs and alcohol, even if consumed outside work hours, can lead to poor concentration, carelessness, fatigue, risk-taking behaviour, and errors in judgement. Misuse of drugs and alcohol not only affects work performance, but also results in higher rates of injuries, fatalities, and absenteeism.
- Alcohol includes any substance or beverage that contains ethyl alcohol including, but not limited to, beer, winepress-mix drinks and other spirits.
- Drug – a medicine or other substance which has a physiological effect when ingested or otherwise introduced into the body.
Safety sensitive tasks
Safety-sensitive tasks are ones where impaired performance, for whatever reason, could affect the safety worker or others around. While misuse of drugs or alcohol is a risk in any situation, the risk is heightened during safety-sensitive tasks.
For example, working on a film set is safety-sensitive because of the inherent risk. Other safety-sensitive roles include, but are not limited to:
- driving – at all times – not only when shuttling participants;
- construction;
- electrical work;
- rigging;
- tasks working at height;
- operating machinery and tools
- emergency response roles, which may include all staff in an operation.
-
* see - Guidance for Managing Drug and Alcohol-related Activities
Minimum Responsibilities – for Everyone!
All workers should:
- report any personal medical situations that the producer should be aware of;
- advise the Producer, their Supervisor or the Health and Safety Officer if other workers appear to be intoxicated or under the influence of drugs or alcohol which may impede their own or the safety of others;
- advise the Producer, their Supervisor or the Health and Safety Officer if other workers speak about taking drugs or alcohol in a situation that may put other sat risk;
- understand the risks associated with taking drugs(prescribed or otherwise) and alcohol;
- understand that some prescription and over-the-counter medication can lead to drowsiness;
- follow all procedures and controls put in place to keep themselves and others safe when working in noisy environments;
- understand the taking recreational drugs and alcohol outside of work can affect their ability to function safely and put others at risk, and be aware that drugs and alcohol can stay in their system for some time; and
- not turn up to work still under the influence of drugs or alcohol.

Planning and Guidance Considerations and Responsibilities
Anyone who is responsible for, or has influence over, workers should read and understand this section, as well as the minimum responsibilities for everyone.
This includes the Production Company, Producers, Directors, Line Producers, Heads of Department, Assistant Directors and Health and Safety Officers.
Drug and Alcohol Policy
The policy should:
- ensure workers understand your expectations – for example drug and alcohol-free work environment;
- be developed with good faith in mind;
- outline any proposed monitoring;
- outline how you will respond to misuse of drugs or alcohol, in the short-term (immediate safety risk) and longer-term (future expectations) – this may vary depending on whether the worker:
- shows signs of misuse of drugs or alcohol;
- has been involved in a workplace safety incident;
- is convicted of a drugs or alcohol offence – for example what is the policy if someone is convicted of drink driving.
- Drug and alcohol testing
* view Worksafe's information on Alcohol and Other Drugs in the Workplace & How to Develop Alcohol and other Drug (AOD) Policy.
Contracts / work agreements
If the production company decide that drug and/or alcohol testing is appropriate forth production, it is advised that a clause on testing is included in work agreements / contracts; this clarifies that workers consent to drug and alcohol testing.
If the production company chooses to include a clause on drug testing in its work agreements or contracts, if so this should be outlined in the policy.
Drug testing could occur:
- pre-contract;
- if there is a reasonable cause to believe someone may be under the influence; or
- post-safety incident.
Reasonable Cause
The production company or person in charge may require a worker to be tested if there is reasonable cause or reasonable grounds for suspecting they're impaired while at work. This includes factors such as the worker being:
- involved in a workplace accident or near miss – for example a lapse of concentration when driving;
- unreliable – for example being absent or late regularly, or an inability to remember instructions;
- performing poorly – for example poor judgement and decision making, reduced reaction times and efficiency, or increased error rates.
Before deciding to test, you should allow the worker to comment on the concerns. It may reduce any question of bias if more than one person makes a decision to require a post-incident test. Your safety management plan should state who will make the decision.
* Download: Hazards - Reasonable Cause Indicators Process Form
Fatigue
Sometimes, signs of drugs and alcohol misuse are signs of general fatigue. Even if you accept that in a particular case fatigue is the cause of poor performance and testing isn’t appropriate, it’s still important to stand down the worker from safety-sensitive tasks.
Post-Incident Testing
Post-incident testing is a standard procedure is becoming more common. However, it is important to remember that following an incident there may be higher priorities than testing for example first aid, trauma management, and evacuation.
If the police are involved, they may test at the scene. In other situations, the production company or person in charge must decide what is an appropriate time after the incident to test. In making this decision you should consider the length of time alcohol and drugs are present in a person’s system. See the “what to test for” table for more information.
Random Testing
Random testing should only be conducted when staff are working in safety- sensitive roles. The privacy rights of staff will outweigh an employer’s wish to be consistent across all staff and random test any staff member irrespective of staff members’ work roles.
* View information on Worksafe's view of Impairment and Testing for Drugs at Work
WHAT TO TEST FOR:

Production Company
The production company (likely to have primary responsibility over health and safety on the production) should develop a drug and alcohol policy.
The production company should:
- ensure workers affected by drug or alcohol use are managed according to the drug and alcohol policy;
- ensure workers presumed, or known, to be impaired by drug or alcohol use are treated fairly; and
- respect a worker’s right to privacy when/ if they inform the production company of use of prescribed or over-the-counter medication.
Person in charge
Anyone who is responsible for, or has influence over, workers is a person in charge and should read this entire chapter. This includes the Production Company, Producers, Directors, Line Producers, Heads of Department, Assistant Directors and Health and Safety Officers.
If it is suspected that a worker is misusing drugs or alcohol, it is recommended, as a first step, that the appropriate person in charge (this may be the Head of Department, Producer or Health and Safety Officer)and the worker talk about the problem to try to resolve the issue.
If a worker is caught misusing drugs or alcohol, the production’s response should be clearly outlined in their Drug and Alcohol Policy, and followed by the person in charge – this may include testing.


Alcohol and Drugs
Alpine Safety
When working in alpine locations, especially in high altitude or extreme conditions, productions need to ensure the environment is understood and measures are put in place to ensure safety.
It is important to have competent guides and specialist advice.

ScreenSafe suggests all productions are familiar with the Mountain Safety Association and AdventureSmart.
Ensuring Safety
Productions should ensure:
- specialist advice is sought for all activities;
- competent guides are used, especially in extreme conditions;
- seek local knowledge;
- crew and cast have and use personal protective equipment, including solid shoes, rain jacket, warm clothing (avoid cotton and denim), hat and gloves;
- all equipment is maintained, tested and present;
- crew and cast understand the risk of hypothermia, how to identify it and what to do;
- crew and cast have enough food (to last an extra night in case of an emergency) and water (at least 2L per person);
- two-way communication is available;
- alternative exit routes are planned in case conditions change;
- emergency shelters are available;
- an appropriate first aid kit is available;
- weather forecasts are checked – MetService mountain weather forecast;
- surroundings are checked for recent avalanche activity, changes in terrain and snowpack;
- fatigue is taken into consideration and managed;
- crew and cast are provided appropriate breaks to rest and take on food / water;
- an emergency plan is in place;
- crew and cast prepare for, and understand, the risk of avalanches;
- crew and cast understand the risks
- ~ consider putting key crew members through safety courses; and
- ensure crew and cast are fit enough for the tasks required of them, such as having to hike for an extended period of time.

Alpine safety
ScreenSafe is committed to ensuring the safety and wellbeing of all children and young people in the New Zealand screen sector.
ScreenSafe has zero tolerance for child abuse. All allegations and child safety concerns are treated seriously and consistently with our guidelines, policies and procedures.
ScreenSafe is committed to providing guidance on child safe environments where children and young people are safe and feel safe, and their voices are heard. Particular attention is paid to the cultural safety of Māori children and children from culturally and/or linguistically diverse backgrounds, as well as the safety of children with a disability and those who identify as gay, lesbian, bisexual, transgender and/or intersex. Our complaints process is child-focused and responsive to the concerns of children and young people.
Every person involved in the New Zealand screen sector has a responsibility to understand the important and specific role they play both individually and collectively to ensure that the wellbeing and safety of all children and young people in the screen sector is at the forefront of all they do and every decision they make.

What are these guidelines and who is covered by them?
These guidelines set minimum recommended standards for the screen sector to create and maintain child safe environments, free from abuse, exploitation and hazards.
These guidelines:
- affirm our commitment to the safety and well-being of children and young people in the screen sector;
- inform all production companies, producers, managers, directors, cast and crew of their obligations to act ethically towards children and young people, and their roles and responsibilities in ensuring the safety and well-being of children and young people; and
- give guidance on the processes and procedures that aim to ensure children and young people’s safety and well-being across all areas of screen sector work.
These guidelines are for all people who conduct work in the screen sector in a paid or unpaid capacity including, but not limited to: production companies, producers, managers, directors, cast, crew, students on placement, volunteers, interns, trainees, contractors, consultants and visitors on set.
When referring to protection from abuse and neglect, a child is defined as anyone under 18 years of age. For the purposes of workplace health & safety legislation and regulations, a child is defined as anyone under 16 years of age.
These guidelines support the requirements of Appendix 1 of the SPADA & New Zealand Actors’ Equity Individual Performance Agreement 2014.
These guidelines are informed by the following legislation and standards:
- The Children’s Act 2014
- Children’s (Requirements for Safety Checks of Children’s Workers) Regulations 2015
- The Health and Safety at Work Act 2015
- The Education Act 1989
What is Child Abuse?
A common understanding about the nature and impact of child abuse informs our response to child safety. Production companies, producers, managers, directors, cast and crew must be aware of the types and indicators of child abuse, and the impact of child abuse and neglect on the healthy development of children and young people.
The abuse of children and young people is highly complex in nature with multiple forms of abuse often co-existing. Abuse can be:
- physical abuse
- emotional abuse
- neglect
- sexual abuse
- sexual exploitation
- sexually harmful behaviours in children
- exposure to family violence
- grooming.
A summary of each abuse type can be found below in Appendix A.
There are many indicators of child abuse and neglect. The presence of a single indicator, or even several indicators, does not mean that abuse or neglect
has occurred. However, the occurrence of an indicator or multiple indicators should alert people to the possibility of child abuse and neglect. Equally, abuse and neglect may occur without the presence of obvious indicators (e.g. in cases of emotional abuse), so those working with children and young people should remain open and aware in assessing risk to a child or young person.
Observable indicators of abuse may include:
- physical abuse – bruises, burns, sprains or fractures;
- sexual abuse and exploitation – displaying sexualised behaviour, sexually transmitted infections, or unexplained gifts or money;
- emotional abuse – developmental delays, withdrawn, or anxious; and
- neglect – malnutrition, poor hygiene, and stealing food.
A detailed list of abuse and neglect indicators is provided below in Appendix B.
Bullying and harassment are also forms of abuse. They will not be tolerated in our screen community and will be treated seriously.
Who has responsibilities under these guidelines?
Child safety is everyone’s responsibility.
Production Companies should ensure that:
- criminal record checking is conducted on all chaperones and house parents, and any personnel who may have contact with a child including costume, makeup and sound personnel, casting and stunt coordinators, health and safety officers, intimacy coordinators, and any other staff employed to ensure the safety and wellbeing of children on set, e.g. psychologists;
- appropriate planning, budget and resources are provided to support their minimum requirements under the law and recommendations contained in these Child Safety Guidelines; and
- conditions as set out in Appendix 1 of the SPADA & New Zealand Actors’ Equity Individual Performance Agreement 2014 are met.
Producers / Line Producers / Production Managers should consider appropriate support and ensure budget and/or personnel are available to provide the minimum requirements for the number of children involved in the production; this includes:
- hiring competent people with an appropriate or necessary level of training, experience and/or qualifications;
- ensuring police and safety checks are carried out where required for chaperones or tutors, with respect to the requirements of the production;
- ensuring the appropriate number of people are hired in relation to the size of the project and children engaged on the production.
Best practice ratios are as follows:
- 0–2 years-one adult to three children
- 2–3 years-one adult to four children
- 4–8 years-one adult to six children
- 9–12 years-one adult to eight children
- 13–18 years-one adult to 10 children
- ensure intimacy coordinators are hired for productions where required; and
- ensuring sufficient resources, including budget, are allocated to enable appropriate and safe practices and satisfy the minimum requirements under law.
As producers, line producers and production managers have oversight across the production, they should:
- meet with the child and parent or guardian to confirm vital information such as emergency contact information, costume measurements, allergies, educational needs such as tutors, dietary requirements and any other considerations relating to the subject matter of the film or requirements of the role; and
- ensure appropriate planning, budget and resources are provided to support their minimum requirements under the law and recommendations contained in these Child Safety Guidelines.
Producers should ensure a production schedule is developed that provides adequate time for work to be undertaken safely.
Directors / Heads of Department are equally responsible for ensuring the welfare and safety of children working on a production. This may include but is not limited to:
- appropriate behaviour and language used around children and young people;
- working within the legal restrictions on working hours;
- providing appropriate rest breaks; and
- liaising with chaperones or guardians on set.
Directors on a production are in a position to influence all of the above, as well as the conduct of the other heads of departments and crew, and should expect to be responsible for doing so.
- Assistant Directors should remind the cast and crew about the expectations and standards of behaviour when children are working on set during inductions.
- Cast and Crew are expected to comply with the recommendations in these Child Safety Guidelines.

Before you start
Managing the risks
Children are uniquely vulnerable and there are specific activities that pose a greater risk to children that need to be managed.
ScreenSafe recommends that specific child safety risks are included in production risk assessments. These risks include, but are not limited to:
- toilet and change facilities;
- transportation;
- breakout spaces (eg green room, catering facilities);
- water shoots;
- physical contact;
- supervision of staff; and
- overnight stays with house parents.
These specific child safety risks should be understood by staff involved in the production and effective mitigation processes put in place to reduce the likelihood of the risk occurring.
In addition, if a child works directly or indirectly with the equipment or in situations such as those listed below, it is recommended a specific risk assessment be carried out to protect or minimise the risk of potential harm to child performers:
- stage combat, firearms and weaponry;
- electrical devices or scenery that are mobile or automated;
- high levels of noise exposure;
- working at heights; or
- exposure to contagious illnesses, such as those carried by mosquitoes.
Refer to Risk Assessment of the NZ Screen Sector Health & Safety Guidelines for more information on identifying hazards and assessing risk. (word this differently)
Hiring the right people
Making sure you have the right people in your production, and that you do not hire the wrong people, is a key child safeguarding mechanism.
ScreenSafe recommends that the responsibilities required by production staff to safeguard children and young people are detailed in all Duty Statements, job advertisements and employment contracts for the production. For roles such as child performers’ coordinator, chaperones and house parents, child safety questions should be included in the interviews and in reference checks prior to employment offers being made.
ScreenSafe recommends that productions designate a child performers’ coordinator, responsible for coordinating matters related to the welfare, safety and comfort of child performers.
Criminal history checks
Criminal history checks are a key mechanism in ensuring that no-one with a criminal history that could pose a threat to the safety of children on set is allowed to work on your production. There are two main types of criminal history check that production companies can utilise.
Police Vetting
The Children’s Act 2014 sets a legal minimum standard for safety-checks for state services and those individuals and organisations funded by them.
Anyone employed or engaged in work that involves regular or overnight contact with children must undergo a criminal history check known as police vetting.
If the production is funded, wholly or partly and whether directly or indirectly, by a state service, it must comply with the Children’s Act 2014.
Police vetting is requested by the employing agency, not the individual, and results are returned to the employer. Production companies who run funded productions will need to register for NZ Police Vetting.
More information about the Police vetting process and who qualifies to register can be found at https://www.police.govt.nz/advice-services/businesses-and-organisations/vetting.
Criminal Record Check
Criminal record checks are provided by the Department of Justice and can be requested by an individual or by a third party (with the individual’s written consent on the form). The results are returned to the individual or to the third party.
More information about the Criminal record check can be found here at https://www.justice.govt.nz/criminal-records/
Best practice
ScreenSafe recommends that all productions working with children, or filming at schools or events that involve a significant number of children, irrespective of whether it is a funded production covered by the Children’s Act 2014, undertake the appropriate criminal history checking (police vetting or requesting a Department of Justice criminal record check) of all production crew, and employ a child performer’s coordinator to monitor the production’s interaction with the children. This should be in addition to any chaperone and/ or house parent contracted to care for a child/children.
In cases where a production requires crew at short notice or for short production run-times, it is recommended that crew are encouraged to provide evidence of a criminal record check from the Department of Justice undertaken within the previous six months. Over time, this will set the expectation that criminal histories will be checked for convictions of concern, and also provide a pool of people who have recently had their criminal history checked.
In addition, it is recommended that production companies keep a record of crew who have undergone police vetting for productions in the last six months as a risk management strategy when timeframes are tight.

Induction
All staff on set should be briefed on child safety and behavioural expectations as part of their induction, including signing a Child Safety Code of Conduct. ScreenSafe’s recommended Child Safety Code of Conduct covers:
- professional boundaries;
- transporting children;
- chaperones and house parent arrangements;
- makeup and costume;
- images of children; and
- use of social media/technology.
Training
Ensuring that producers, directors, chaperones and house parents, cast and crew know what child abuse looks like, know how to recognise when a child is being abused, and know who to talk to if they have any concerns is a key child safety strategy.
ScreenSafe recommends that key personnel on any production that involves children participate in annual professional development around child safety. ScreenSafe recommends Safeguarding Children New Zealand’s training programs which can be found here: https://safeguardingchildren.org.nz/ training/
ScreenSafe recommends that experts are engaged to brief all personnel on child safety at the commencement of a production. Safeguarding Children New Zealand can provide customised briefing sessions for productions.
They can be contacted on 027 772 4469 or office@safeguardingchildren.org.nz
Chaperones and house parents
Chaperones and house parents are the primary supervisors and carers of child performers on behalf of their parents or guardians. As such, the engagement of chaperones and house parents must comply with clause 10 and clauses 19 through 29 of Appendix 1 of the SPADA & New Zealand Actors’ Equity Individual Performance Agreement 2014. This includes ensuring that chaperones and house parents are suitably qualified and experienced and have undergone police vetting.
Chaperones and house parents should also receive specific child safety training, and induction with respect to the Child Safety Code of Conduct and expected behaviours while in their role, including approaches to child discipline.
Engaging a child performer
Pre-meeting with the child’s parent or guardian
Before employing or contracting for the services of a child, a producer or line producer must meet with the child’s parent or guardian. This meeting may also include the child’s agent and / or legal representative, if deemed necessary by the child’s parent or guardian, and could be held in person, by telephone, or by electronic conferencing. The child is also entitled to be present.
The information to be disclosed by the producer at the meeting includes:
- the ScreenSafe Child Safety Code of Conduct which guides the behaviour of all adults involved in the production;
- any health or safety hazards, as well as the precautions that will be taken to prevent injury, including the appointment of relevant professionals, e.g. stunt coordinators;
- any special skills the child will be expected to perform;
- any special effects to which the child may be exposed;
- what off-set facilities will be provided for the child and how they will be cared for on the production, such as a green room area and meals; and
- confirming that a quiet space will be made available for doing schoolwork if this is a longer production.
Following this meeting, the producer must disclose any subsequent proposed changes to the matters discussed and may not implement any of the proposed changes without the written agreement of the child’s parent or guardian.
At the meeting or during contracting stages, a parent or guardian of the child should provide the producer with current contact and emergency telephone numbers, the name and number of the family doctor and pertinent medical information that would be useful in an emergency. In the case of an international child performer, a local medical contact must be provided.
Special considerations for infants
If the child is an infant (under two-years old), they must be cared for by a parent or parent’s approved alternative. Producers must comply with clauses 12 through 18 of Appendix 1 of the SPADA & New Zealand Actors’ Equity Individual Performance Agreement 2014 with respect to infants.
The following guidelines must also apply:
- infants must be attended too at all times and appropriate facilities for naps, feeding, changing, playing, in consultation with the caregiver, should be provided; and
- no person with an illness or infection is to come into contact with the infant.
Scheduling
When scheduling a production (including travel time), the producer needs to consider the age and maturity of the child, and under no circumstances will travel time exceed the restrictions as stated below.
Maximum hours of work per day and associated conditions are set out in clauses 2 through 6 of Appendix 1 of the SPADA & New Zealand Actors’ Equity Individual Performance Agreement 2014.
Children under the age of 16-years-old should not work between the hours of 10pm and 6am. However, if required, work may be undertaken during these hours in consultation with, and if agreed to, by the child’s parent or guardian.
On-set induction
The producer must provide information and instruction to a child and the parent, guardian, or chaperone of the child on the following matters with respect to each location where he or she works:
- who is the key contact for the child if they have any concerns (e.g. child performers’ coordinator);
- restricted areas;
- safe waiting areas;
- a quiet space for the child to do schoolwork if they are on a long production;
- restroom locations, make-up areas, and anywhere else relevant to the child’s work;
- emergency procedures, including health and safety precautions specific to the location; and
- the procedure for reporting concerns or complaints.
Induction for the child must be appropriate to their developmental stage.
Healthy food / dietary requirements
The producer must:
- provide healthy snacks and meals as close to the child’s regular snack and mealtimes as possible – these should be agreed during the initial meeting/ contracting stages; and
- ensure that the food provided meets the child’s needs in respect of any food allergies or special dietary requirements.
It is recommended that productions post menus detailing the snacks and meals provided, to inform children (and their parents, guardians and chaperones) of the food available, including information about any allergies or special dietary requirements that may apply.
A parent or guardian should provide the producer with information on any food sensitivities, allergies or dietary requirements.
Changing and toilet facilities
Male and female children should have separate dressing rooms and toilet facilities, separate from those provided to adult performers.
It is recommended that gender neutral toilets be made available wherever possible as an alternative changing space.
At no time should a child be left alone in a closed room with only one person (with the exception of the parent, guardian or authorised chaperone).
Travel safety
Everyone on a screen production who does, or could, work with motor vehicles, or drives to work, should read and understand the chapter on motor vehicles in the NZ Screen Sector Health & Safety Guidelines.
The producer must ensure:
- drivers hold the appropriate license/s for the vehicle/s they drive;
- suitable child seats / restraints are provided when requiring children to travel by vehicle; and
- children or young person must not be transported in a private vehicle without the child’s chaperone or parentally approved alternative. In circumstances where this is not possible, the child performers coordinator or producer must be informed of the purpose of the travel, how long the travel is expected to take and what the expected time of arrival is. Arrival must also be confirmed with the child performers coordinator or producer.

Looking after a child’s wellbeing
The safety and wellbeing of a child is paramount at all times. At no time should the producer or PCBU involved in the production expose a child under the age of 16-years-old to any situation that could be deemed detrimental to the child’s mental, physical or moral wellbeing.
Filming should be scheduled, and filmed shots constructed, in such a way so that the child is not exposed to scenes that are harmful or likely to cause distress, taking into account the nature of the material, the child’s age and the requirements of the performance.
The producer must disclose information about proposed scenes that include nudity or coarse language, or any scenes that could cause psychological or emotional distress. The parent should also be informed about changes to scenes that include exposure to nudity or coarse language, or to scenes that may cause psychological or emotional distress. The producer and parent or guardian should agree to any such changes before the child is required to rehearse or perform the changed scene.
If the producer is responsible for travel for the child to and from the production base, the child should be accompanied by the chaperone, or an approved alternative.
Traumatic Content
For any scenes of a sensitive nature being performed, a closed set is always recommended. On productions dealing with sensitive subject matter and scenes of a traumatic nature, especially if they involve a child with experience relevant to the subject matter, ScreenSafe recommends that a psychologist or therapist and an intimacy coordinator who are properly qualified be hired by the producer to guide and assist the child with this.
In the case of lesbian, gay, bisexual, or transgender children or young people playing roles that could be traumatic for them to perform, it is recommended that special care and attention be given to ensure their safety and wellbeing before, during and after their time performing on set. If relevant, this may include providing appropriate briefing, training and awareness for other cast and crew involved with a production where gender identity and / or sexuality is relevant. For example, educating cast and crew on the appropriate use of the correct pronouns and how to provide a safe and supportive environment in which the young performers can safely be vulnerable and offer their best work.
Similar further consideration should also be given to child workers where the subject matter may contain triggers in relation to disabilities, eating disorders and mental illnesses.
Being child safe on-set
Workplace health and safety
Under workplace health and safety regulations, a child is defined as anyone under 16-years of age during any of the pre-production or principal photography dates. If the child turns 16 during pre production or principal photography, they will be treated as a child until and including their birthday. From the day after their birthday, they will be treated as an adult engaged on the production.
A child has the same responsibilities as an adult in keeping themselves and others physically safe. There are a range of regulations that provide further guidance as to the types of work that children can be engaged in, and some of the practical things those working in the screen sector need to think about when working with children.
Most notably, regulations require that children:
- do not work in any area where construction work is being carried out, or in any area where work is being carried out that is likely to cause harm to the child’s health and safety;
- do not lift weights or perform any task that is likely to be injurious to their health; and
- do not operate machinery, including tractors and other self-propelled plant.
Special activities / stunts
No child should undertake a special activity unless they are qualified or have the appropriate training to perform the activity safely. Any special activity should include walk-through time to confirm the child performer is comfortable carrying out the activity.
If the special activity heightens the risk of harm, a risk assessment must be carried out and measures developed to protect the child, taking into account age and skill level.
The above guidance does not include stunt work. All activities deemed to be a stunt should be performed by a suitably qualified stunt double or performer unless previously discussed and agreed to by all parties directly responsible for the child performer’s health and wellbeing. Any such activity should be appropriately planned, arranged and rehearsed under the strict guidance of the stunt coordinator prior to the day of filming.
Props, costumes, make-up and hair products
A child’s age and size should be considered at all stages of design, purchase, construction and use of hand props, wigs, and costumes. Costumes should be designed to adequately fit and avoid tripping hazards, or hazardous accessories such as belts. Hand props for children under the age of three, or those likely to put small objects into their mouths, should adhere to the Toy Safety Standards provided by the NZ Commerce Commission:
https://www.consumerprotection.govt.nz/tradingstandards/product-safety/ keepingkids-safe/toy-safety/
Information on a child’s skin sensitivities should be collected before the child is provided with or exposed to costumes, accessories, make-up, wigs, or hair products. Products should be chosen with regard to the age and skin sensitivity of the child.
It is recommended the person responsible for providing a child performer with costumes, accessories, make-up, wigs, or hair products check for negative skin reactions, as appropriate.
Costume and make-up artists should refer to the ScreenSafe Child Safety Code of Conduct for guidance on acceptable and unacceptable behaviour with children in their context.
Special effects
Exposing children to special atmospheric effects should be avoided. If effects, such as smoke or fog, are used, exposure should be minimised by limiting the amount of time of their exposure. A discussion with the child’s caregiver should also occur before any special effects are used. Any child performers with asthma or other airway disorders should not be exposed to smoke or fog at any time.
Working with animals
Extra care should be taken to protect children when animals are used on a production. A risk assessment should be carried out and a plan made around the protection of children, which must include police vetting of any animal trainers engaged on the production.
A child must be acquainted with hazards associated with the animals and instructed on the procedures required to work safely. It is also recommended the parent, guardian or chaperone be acquainted with any of the hazards and procedures for working safely around the animals the child will be working with on a production.
Outdoor work
Children should be protected from heat and humidity. Precautions include providing cool areas for rest periods, water and costumes that take into consideration the weather conditions.
Avoid exposure to sunlight for long periods by using shaded areas for rest periods, sun hats and sunscreen formulated for children with a sun protection factor (SPF) of 30 or higher.
Children should also be protected from the cold. Precautions include providing warm areas for rest periods, costumes and outerwear such as jackets and blankets made available for use when possible.
Water safety
Children should be adequately instructed in safety precautions to be taken when working on, in or by water. It is recommended that the parent, guardian or chaperone be acquainted with the hazards and procedures for working safely around water.
All children involved in filming around deeper water should be strong swimmers or wear the appropriate water safety devices. Qualified, police-vetted life-saving personnel and equipment (such as safety boats) should be present for the duration of the production activity. Costume weight should be considered when choosing personal flotation devices as well as water temperature and length of exposure. Washing facilities should be available for use after completion of filming.
How do I handle concerns about child safety?
The screen sector has zero tolerance for child abuse. All allegations and child safety concerns must be treated very seriously and in a manner consistent with our guidelines, policies and procedures. We have a moral and ethical obligation to contact authorities when we are concerned about a child or young person’s safety.
The producer should encourage child performers and all adults in contact with children on a production to identify any safety or wellbeing concerns, and to bring them to the attention of the child’s supervisor or the child performers’ coordinator. Adults should also be sensitive to the distress or discomfort expressed by infant or child performers, which could be an indication of a safety or wellbeing issue.
ScreenSafe has developed the Managing Disclosures Guide to provide advice on how to deal with disclosures of abuse. It is recommended that child performers’ coordinators, chaperones and house parents receive training or briefings on managing disclosures.
Record Keeping
Producers should:
- create and keep full and accurate records relevant to child safety;
- create records for all incidents, response and decisions affecting child safety;
- maintain and appropriately store the records relevant to child safety – records related to child sexual abuse that has occurred or is alleged to have occurred, will be maintained and stored for a minimum of 45 years;
- only dispose of records relevant to child safety in accordance with legal requirements; and
- fully recognise the individuals’ rights to access, amend or annotate records about themselves.
Review
These Child Safety Guidelines, and related procedures, will be reviewed every second year and following significant incidents if they occur. ScreenSafe will ensure that families, children and young people have the opportunity to contribute to the review process.
Related Policies and Procedures
- ScreenSafe Child Safety Code of Conduct Template
- ScreenSafe Child Safety Reporting Concerns Procedure
- ScreenSafe Managing Disclosures Guide
- NZ Screen Sector Health & Safety Guidelines
- ScreenSafe Sexual Harassment Prevention Policy
________________________________________________________________________
Appendix A
Forms of Abuse
Emotional abuse – This may involve a child being repeatedly rejected, verbally abused or put down. It may involve children being frightened by threats or subjected to continual coldness. Emotional abuse can diminish a child’s sense of identity, dignity and self-worth, resulting in damage to the child’s social, intellectual or emotional development. It does not leave physical injuries and its ongoing nature usually means there is no crisis which would precipitate easy identification. For
this reason, emotional abuse is the most hidden and underestimated form of child maltreatment despite the impact being chronic and debilitating. Stakeholders therefore need to be particularly aware of the behavioural indicators of emotional abuse and astute in any assessment of risk.
Physical abuse – Occurs when a person intentionally or recklessly uses physical force against or in the presence of a child without their consent, which causes or could cause harm to that child. It can also occur when someone intentionally or recklessly causes a child to believe that physical force is about to be used against them without their consent. Physical abuse can take the form of punching, beating, shaking or otherwise harming a child and also includes behaviours, such as words or gestures that leads a child to believe they are about to experience physical abuse.
Neglect – Involves the failure on the part of the caregiver to meet a child’s basic needs, such as providing adequate nutrition, clothing, supervision, and hygiene and medical attention to the extent that the child’s health and development are, or are likely to be, placed at risk. Neglect also includes a failure to meet a child’s social and emotional needs, for example a child may receive no emotional warmth, nurture and affection with the caregiver unattuned or disinterested in the child’s needs.
Sexual abuse – Occurs when a person uses power, force or authority to involve a child in any form of sexual activity. Sexual offences include: touching or fondling; obscene or suggestive phone calls/texts; exhibitionism and voyeurism; showing children or involving them in the production of child exploitation material; and penetration. Sexual misconduct is another type of sexual abuse and includes a variety of sexualised behaviours toward children. Examples of sexual misconduct include inappropriate comments of a sexual nature, and behaviour that crosses a professional boundary such as establishing (or seeking to establish) an overly familiar relationship with a child.
Sexual exploitation – Is a specific form of sexual abuse where children and young people, by virtue of their age and development, are unable to give informed consent to sexual activity. Sexual exploitation of children takes different forms. It can include children being involved in sexually exploitive relationships, exposing a child to pornography, receiving money, goods, drugs or favours in exchange for sex, or being exploited in sex work. In all cases, those exploiting the children have power over them due to the child’s age, gender, physical strength, economic or other resources such as access to drugs or gifts.
Sexually harmful behaviour in children - Sexually harmful behaviour involves a child (17 years of age or younger) engaging in sexual activity that is either unwanted or where, due to the nature of the situation, the other party is not capable of giving consent (e.g. children who are younger or who have cognitive impairment). In children under 10 years of age, such behaviour is usually referred to as sexually problematic behaviour.
Grooming – Refers to actions deliberately undertaken by an adult, adolescent or child to befriend and influence a child (and in some circumstances members of the child’s family) with the intention of achieving the criminal objective of sexual activity with children. Grooming is generally subtle and ambiguous. Adults therefore need to be vigilant in reporting any breach of policy, code of conduct or generalised concern to enable patterns of behaviour to be identified early and potential abuse prevented.
Grooming behaviours can include the following:
• sharing secrets with a child;
• engaging inappropriately with a child on social media;
• non-sexual touching such as tickling, hugging or rough play;
• allowing the child to break the rules;
• spending time with the child away from protective adults; and
• favouritism toward a child through giving gifts or money.
Exposure to family violence – The nature of children's exposure to family violence ranges from witnessing (including seeing and overhearing violence and witnessing its effects) to being directly involved. Children were previously seen as "silent witnesses" to domestic and family violence; however, a now substantial body of research indicates children may be involved in domestic and family violence in a range of ways, including being forced to watch or participate in assaults or intervening to stop the violence occurring.
________________________________________________________________________
Appendix B
Indicators of Abuse



Child Safety Guidelines
Fatigue
Productions can be a demanding undertaking, not only in the duration of the production but also in the hours expected of cast and crew on a daily basis. We need to look after our people and consider the potential for fatigue throughout a production and how we can manage it.
While how to manage fatigue is not specifically legislated, under the Health and Safety at Work Act 2015 we are all responsible for workplace health and safety, and that includes fatigue.
This chapter is primarily based on guidance issued by:
- WorkSafe NZ;
- the Canadian Centre of Occupational Health and Safety;
- the New Zealand Film & Video Technicians Guild and The Screen Production & Development Associations; and
- WorkSmart, United Kingdom.
The chapter also draws from The Blue Book: The Code of Practice for the Engagement of Crew in the New Zealand Screen Production Industry.
Who needs to read this?
All workers involved in a production have health and safety duties regarding fatigue and should read and understand the section on ‘minimum responsibilities for everybody’. Roles that have direct influence over other workers should also read the ‘planning and guidance considerations’ section; this includes production company representatives, producers, directors, production managers, heads of departments, assistant directors, health and safety officers and location managers.
Definitions
Definitions specifically related to fatigue.
Day off is an unpaid scheduled period, usually at the end of the working week intended for rest. Specified timings for short and long term engagements are outlined in the Blue Book.
Fatigue is the state of feeling very tired, weary or sleepy resulting from insufficient sleep, prolonged mental or physical work, or extended periods of stress or anxiety.
Jet lag is the rapid movement (faster than one time zone per day) across more than three time zones.
Rest an uninterrupted period during which work should not be undertaken – in a production it is ideally a 10-hour stand-down.
Scheduled day means the set period of time in which a worker is scheduled to carry out their duties.
What we need to know about Fatigue
What is Fatigue?
Fatigue is a state of physical and/or mental exhaustion that may impair an individual’s strength, speed, reaction time, coordination, decision making capability or balance, diminishing their ability to perform work safely and effectively. Fatigue reduces alertness, which can lead to errors and an increase in workplace incidents and injuries.4
Research has shown that people who have gone without sleep for an extended period of time are just as impaired as people who are over the legal alcohol limit.
Fatigue can be described as either:
- acute – resulting from short-term sleep loss or short periods of heavy physical or mental work, and usually can be reversed by sleep and/or relaxation; or
- chronic – the constant, severe state of tiredness that is not relived by rest, with symptoms similar to the flu and can last longer than six months.
Types of Fatigue
Circadian rhythm disruption occurs when a worker’s normal, 24-hour, rhythmic biological cycle is disrupted from its current setting due to either:
- shift lag – one or more nights of work; and
- jet lag – rapid movement (faster than one time zone per day) across more than three time zones.
Cumulative fatigue or sleep deprivation is when a worker’s mental capability is weakened due to disturbed or shortened major sleep periods. Several major uninterrupted sleep periods will be needed to reduce or eliminate the sleep debt.
Emotional fatigue can result from excessive job and/or personal demands and stress.
Mental fatigue can be caused by continual mental effort and attention on a particular task, as well as high levels of stress or emotion. Mental fatigue can be related to cumulative fatigue or sleep deprivation.
Physical fatigue is when an individual’s physical capability is weakened due to over-exertion – both prolonged physical activity and brief but relatively extreme physical activity can tax a worker’s physical endurance or strength beyond their normal limits. Physical fatigue can either be due to dynamic work, where muscles are continually moving, or static work, where muscles are held tense.
Find out more about common types of fatigue in Appendix 1 below.
What causes Fatigue?
Just as there are different types of fatigue, there are many different reasons why fatigue may occur; it is important we are all aware of what can cause fatigue so we can help prevent it from occurring.
While the most common cause of fatigue is disturbance to sleep, with fatigue being higher among shift-workers, there any many reasons why fatigue may occur and we should consider all possible factors.
The below tables outline some factors that can contribute to fatigue within the screen sector.

How do we identify Fatigue?
Some symptoms of fatigue can only be identified by the individual:

Other signs can also be identified by others:

These lists of symptoms are not exhaustive, and you should consult a professional if you have concerns about fatigue on the production set.
A checklist for identifying fatigue, and causes, can be found in Appendix 2 below.
Minimum Responsibilities for Everybody
Everyone involved in a screen production should read and understand this section.
Everyone involved in a production should:
- understand what causes fatigue;
- understand the signs and symptoms of fatigue, for both themselves and others; and
- ensure they advise the Health and Safety Officer, their direct supervisor, the Assistant Directors, and/or the Production Manager/office if they become aware of fatigue or the potential for fatigue.
Everyone is responsible for ensuring their exposure to fatigue is minimised to prevent risks to health and safety, and should:
- have a nutritious diet;
- get adequate sleep, this could include, but is not limited to:
- knowing about sleep, sleep disorders and sleep hygiene
- exercising regularly, but not just before going to bed
- using bed primarily for sleeping
- avoiding caffeine, tobacco and alcohol, especially close to when you plan on sleeping
- making the bedroom as quiet and dark as possible
- negotiating with others if sleep must occur during the day
- understand what tasks to do and what not to do if sleep is compromised
- get adequate meal and rest breaks during work shifts;
- have adequate rest between shifts; and
- use recovery time wisely.
Stimulants
The use of stimulants, such as nicotine, caffeine, and some other drugs, can help maintain alertness in the short-term; however, they can cause individuals to “crash” as the effects wear off, and lead to poor quality sleep.
If cast and crew are constantly relying on stimulants to keep them alert, we need to consider what is causing the fatigue and what can be done to prevent, or reduce, it.
* Coffee is not a solution to fatigue, it merely masks it.
Sleeping tablets can reduce fatigue, if used appropriately and for limited periods of time. However, each different type has advantages and disadvantages and generally they just mask the problem if the causes of sleep problems remain unchanged.
Planning and Guidance Considerations and Responsibilities
Everyone who is responsible for, or has influence over, an activity or task in relation to a production should read and understand this section, as well as the minimum responsibilities for everybody.
This includes funders, production company representatives, directors, producers, production managers, line producers, heads of department, assistant director/s and health and safety officers. All of whom should follow the guidance provided in the below sections on ‘identifying the risk of fatigue’ and ‘managing the risk of fatigue’, as well as the section for their specific role.
Assessing the Risk of Fatigue
Everyone who is responsible for an activity or task in relation to a production should understand what causes fatigue and know how to identify fatigue. We are all responsible for taking reasonable care of our own health and safety and ensuring that our actions, or inactions, do not harm others – including understanding fatigue.
It’s important that we don’t solely rely on someone already showing signs of fatigue to identify the risk of fatigue occurring.
We should all consider fatigue when:
- a new job is started;
- there is a change or increase in work demand;
- designing work schedules and allocating tasks;
- assigning physically or mentally demanding tasks; or
- moving across time zones.
The risk of fatigue can also be assessed by:
- consulting with cast and crew;
- looking at work practices and schedules;
- reviewing previous safety event information; and
- using specific assessment tools, if required – see Appendix 3 below for an example.
The risk of fatigue should always be considered across all roles on a production. In particular, fatigue needs to be constantly monitored in higher-risk areas of work, such as driving, operating heavy machinery or equipment, working at heights, working in extreme environments, working with hazardous substances or electrical work, or stunt work.
Fatigue on the Production Set
There are specific circumstances on a production that can contribute to fatigue. We should all know and understand what these are:
- repeated, long and extended hours;
- difficult technical setups;
- poor production planning; and
- bad weather delaying productions.
While we cannot predict the future, some of these causes of fatigue can either be avoided or managed through proactive and smart planning.
A key component of risk management is about identifying the potential for fatigue. If we are aware of a risk that could cause fatigue, and we do nothing to try to manage that risk then something goes wrong – we haven’t done our job to ensure the health and safety of all workers and others affected by our work.
* If something goes wrong because someone was fatigued, and you could have managed the circumstance that led to that fatigue, how would you feel?
Managing the Risk of Fatigue
While it is understood that production sets are not your typical 9-to-5 workplace, fatigue must still be managed. Everyone responsible for setting or organising an activity or task in relation to the production should always consider how they could prevent fatigue from occurring.
* Remember, as PCBU’s and individual workers we are all responsible for making every effort, so far as is reasonably practicable, to ensure the safety of ourselves and others.
Below are some key factors that should be considered to help prevent fatigue from occurring.
Work Schedules
* The search for the perfect work schedule is a wild goose chase; but by acknowledging the need for balance and flexibility we can help prevent fatigue.
- The Blue Book: The Code of Practice for the Engagement of Crew in the New Zealand Screen Production Industry should always be consulted when setting work schedules.
- Schedule tasks suitably throughout a work period.
- ~ It is important to understand that for most people their ability to be alert or to focus is at its lowest between 3am and 5am, and 3pm and 5pm. During these natural low-function times, adopt a conservative approach to safety and avoid critical jobs, where practicable.
- If night work is deemed essential to the production, fatigue must then be considered as an increased potential risk.
- Consider how people will get to and from work
- .~ Workers who don’t work traditional 9am-5pm days, such as screen industry crew, have more accidents commuting to and from work than those who do work 9am to 5pm, which are likely to be caused by fatigue.
- Try to schedule work so workers can get at least two consecutive nights’ sleep (with a normal day in between) each week, as this will help reduce the risk of fatigue.
- Ensure, so far as is reasonably practicable, that working hours are not too long. If longer working days are required, consider staggered start and finish times, and/or longer rest breaks and periods off work.
- Ensure the schedules allow enough recovery time for a good nights’ sleep.
- Monitor and place limits around overtime worked. Avoid incentives to work excessive hours – remember, every extra hour worked is an hour’s less recovery time.
Sleep
- Design schedules to allow for good sleep opportunity and recovery time between work days.
- Design schedules that minimise disruptions to natural sleeping rhythms.
- If night work is required, try to limit a workers’ number of scheduled nights in a row.
* Remember people are ‘programmed’ to be awake during the day and asleep at night
Environmental Conditions
- Avoid working during periods of extreme temperature, or minimise exposure through job rotation.
- Outdoor work, rough surfaces, sloping surfaces, wind and sunlight / heat can all cause fatigue.
- Provide adequate facilities for rest breaks, such as shade and access to potable water.
Physical and Mental Work Demands
- Limit periods of excessive mental or physical demands (ie through job rotation where practicable).
- Ensure fit for purpose plant, machinery and equipment is used at the workplace.
- Make sure workloads are manageable. Take into account work flow changes due to factors such as production delay, machinery breakdowns, unplanned absences or resignations. Avoid impractical deadlines.
Emotional Well-being
- Where possible, be aware of personal circumstances that affect your workers and provide support. Allow time off where circumstances require. As appropriate, ensure co-workers are aware of any important issues affecting their colleagues.
- Create a positive work environment where good relationships exist and workers are encouraged and supported. Provide good supervision.
Facilities
- Ensure there is good lighting and ventilation.
- Provide rest facilities where possible.
- Provide healthy meals – nutritional requirements vary from daytime to night-time and should be considered.
Workplace Fatigue Policy
Consider developing a fatigue policy to sit alongside your health and safety policy. The policy should include information about:
- maximum workday length and average weekly hours;
- work-related travel;
- procedures for reporting fatigue risks; and
- procedures for managing fatigued workers.
Make sure anyone can report fatigue-related issues, and ensure you investigate incidents where fatigue may be involved.
Responsibilities
Funders
Funders should:
- be assured, through the provision of the production’s health and safety plan, that the funding provided is adequate for the proposed length of the production process, so as not to lead to fatigue; and
- incorporate health and safety clause/s in the funding agreement, which might include expected standard hours of engagement.
Production Company
In pre-production, production companies (likely to have primary responsibility over health and safety on the production) should:
- consider whether the proposed length of the production shoot, the locations or other factors, and daily hours could lead to fatigue; and
- clearly articulate the requirement for fatigue to be managed through the production life-cycle.
The production company should consider developing a fatigue policy to demonstrate commitment to fatigued management.
If it is not reasonably practicable to manage the risk of fatigue and reduce hours of work during the production, the production company should consider providing:
- nearby accommodation; and/or
- transport.
Producer / Production Manager
As Producers and Production Managers have oversight across the production, they should:
- consider the potential for fatigue when planning and allocating tasks;
- ensure the potential for fatigue is either eliminated or minimised;
- provide adequate rest between or during shifts; and
- ensure the potential for fatigue and any controls in place are included on daily call sheets.
If it's not reasonably practicable to manage the risk of fatigue and reduce hours of work, the Producer should consider providing:
- nearby accommodation; and / or
- transport.
Line Producer
Line Producers also have oversight of the production process and should create a production schedule that provides adequate time for the work to be undertaken.
Director / Heads of Department
Directors and Heads of Department should:
- consider the potential for fatigue when planning and allocating tasks; and
- ensure the potential for fatigue is either eliminated or minimised.
Assistant Director/s
The Assistant Director/s should:
- ensure the potential for fatigue is discussed with all cast and crew during health and safety inductions and / or as required if circumstances on the set change;
- create a production schedule that provides adequate time for the work to be undertaken;
- understand how to identify and control fatigue;
- ensure appropriate people are informed if crew members are fatigued, for example heads of department; and
- report incidents of fatigue where necessary, for example if fatigue leads to a notifiable event.
Health and Safety Officer
The Health and Safety Officer should:
- work with the Producer, Production Manager and Heads of Department to help them identify the potential for fatigue;
- ensure the potential for fatigue is discussed with all cast and crew during health and safety inductions and/or as required if circumstances on the set change; and
- understand how to identify and control fatigue; and
- report incidents of fatigue where necessary, for example if fatigue leads to a notifiable event.
Appendix 1
Comparison of types of fatigue common to the screen industry
The two tables below describe several characteristics of types of fatigue common to the screen industry.


Appendix 2
Identifying Fatigue and Causes Checklist
This checklist provides guidance to assist in identifying fatigue but is not an exhaustive list of risk factors. If the answer is yes to any of the questions, fatigue risks should be further assessed and control measures implemented, as required.
Click HERE to view and download the Fatigue Checklist.
Appendix 3
Tools to determine Levels of Fatigue
Prior Sleep and Wake Rules (PSWR) are based on the sleep requirements of the average adult, and can be used to calculate the likelihood of fatigue.
The PSWR are likely to underestimate the fatigue likelihood score (FLS) in older adults, teenagers and those workers who suffer from disrupted sleep. Therefore, it should be used with caution.
The following table uses PSWR to help determine a fatigue likelihood score.

Based on the FLS, a worker or supervisor can then refer to a fatigue likelihood profile. This is not prescriptive but can be used to determine what an acceptable FLS is based on operational tempo or tasks being planned.
The following table is an example of fatigue likelihood profile:

Other Tools and References:
Fatigue Prevention in the NZ Workplace - Guidebook
The Fatigue Scoreboard - (xlsx worksheet to help determine risk)
Canadian Centre of Occupational Health and Safety. 2016. Fatigue.

Fatigue
Guidelines for Covid-19 - May 2024
Removal of COVID-19 public health requirements:
The New Zealand Government removed the remaining COVID-19 public health requirements. This approach reflects the downward trend in case numbers, hospitalisations, and the populations high level of immunity.
Removal of the Public Health requirements means that mandatory isolation for positive cases and mask wearing is no longer required.
Recommendations:
The recommendation from the Te Whatu Ora, Health NZ is to isolate for 5 days from the day you tested positive or symptoms first started, whichever is first.
The HSWA still requires a PCBU and workers to provide a healthy & safe workplace where we look out for each other and not put others at risk, including exposure to illness.
ScreenSafe NZ encourages crew to stay home if they are unwell and test if you have COVID-19 related symptoms.
Testing
You should undertake a COVID-19 test if you have cold, flu or COVID-19 symptoms as soon as you start feeling unwell.
There are two main types of testing for COVID-19 in Aotearoa New Zealand: Rapid Antigen Tests (RATs) and PCR (nasopharyngeal, nasal & throat and saliva) tests.
RATs are available free for personal use and whanau from various public site like pharmacies, healthcare providers, libraries and community hubs. A detailed list for free RATs is located here.
Whether positive or negative, RAT results should be reported through this site.
Even though the COVID-19 public health requirements have been removed, a PCBU/business may choose to undertake surveillance testing using PCR or RATs to enhance production continuity. This will enable early detection and prevent further spread throughout a production. The costs associated with surveillance testing is the responsibility of the PCBU/business.
More information on testing can be found here
PCR Testing Providers
Central Safety Ltd – salivatesting@centralsafety.co.nz
APHG - https://covid19salivatesting.co.nz/

Guidelines for Covid-19 - May 2024
Hazardous Substances
Anyone using a hazardous substance should have a thorough understanding of the Health and Safety at Work (HazardousSubstances) Regulations 2017, which set out the rules for work-related activities involving hazardous substances.
The Hazardous Substances Toolbox website also provides comprehensive information on how you can work safely with hazardous substance.
This chapter provides basic guidance and key things for you to consider in relation to working with hazardous substances on a production.
Who needs to read this?
All workers who undertake work with, or work that interacts with, hazardous substances should read and understand the section on ‘minimum responsibilities’ and ‘managing hazardous substances’.
Roles that have specific responsibilities, or influence, over work with hazardous substances should read the section on ‘planning and guidance considerations’ – this includes producers, directors, production managers, line producers, heads of departments, assistant directors and health and safety officers.
Definitions
Hazardous substance means, unless expressly provided otherwise by regulations, any substance —
- with one or more of the following intrinsic properties – explosiveness, flammability, a capacity to oxidise, corrosiveness, toxicity (including chronic toxicity), ecotoxicity, with or without bioaccumulation; or
- which on contact with air or water (other than air or water where the temperature or pressure has been artificially increased or decreased) generates a substance with any one or more of the properties specified above.
MSDS means Material Safety Data Sheets; these provide concise safety and health information about the hazards and safety precautions of the substance and should be available for all products.
Specific Risks
- Explosiveness
- Flammability
- Health effects
- Infection
- Toxicity - both short and long-term effects
*NOTE: Substances may be inhaled, ingested or absorbed into the body. The effect is dependent upon the substance involved and the degree of exposure.
What we need to know about Hazardous Substances
Many hazardous substances are in daily use on a production set. While all hazardous substances can be safely used if proper work methods are adopted, safer, alternative substances and/or work methods should be used instead of using highly hazardous substances where practicable.
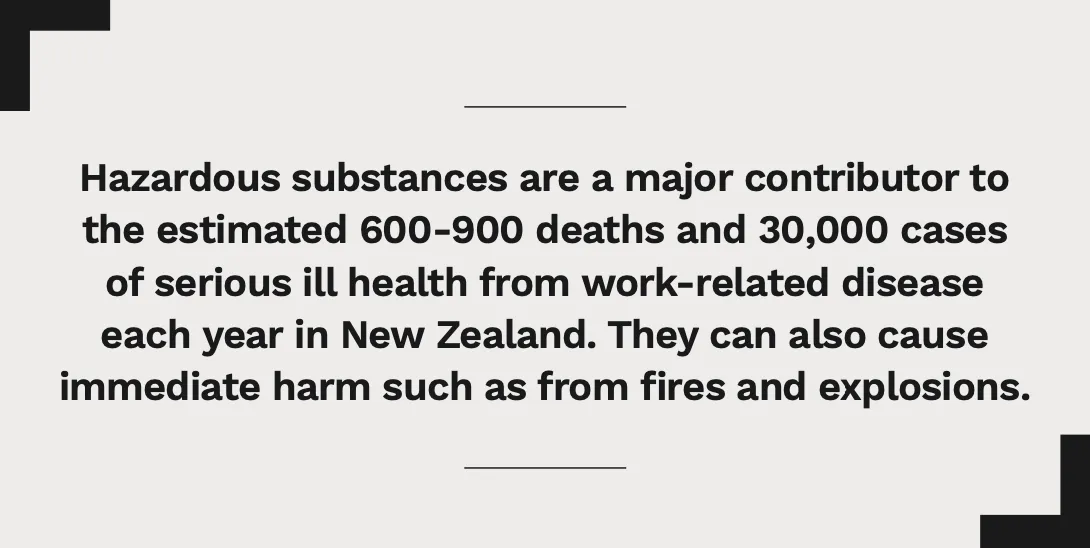
What is a Hazardous Substance?
A hazardous substance is any product or chemical that has explosive, flammable, oxidising, toxic, corrosive or ecotoxic properties.
Explosive: explodes or causes explosion.
Flammable: ignites easily and burns rapidly.
Oxidising: could be gaseous, solid or liquid and can cause or intensify fire and explosion.
Toxic: can harm people if it enters the body through contact, being inhaled or ingested. The effects can range from mild to life-threatening, and can be immediate or long-term.
Corrosive: can cause severe skin burns and eye damage. Ecotoxic: is toxic to the environment.
All hazardous substances should have an MSDS, provided by the supplier of the substance – these provide concise safety and health information about the hazards and safety precautions of the substance.
*See: WorkSafe / What the Hazardous Substances Regulations mean for you
What could go wrong?
Emergencies you need to consider and plan for include:
- a worker being poisoned by ingesting or inhaling a toxic substance;
- a worker being burnt by a corrosive substance;
- a fire caused by flammable or oxidising substances; or
- hazardous substances leaking or spilling from their containers, injuring people and contaminating land and waterways.
*See: WorkSafe / Emergency plans
Certified Handler requirements
Some work with highly hazardous substances must be carried out by a certified handler.
Certified Handlers need to:
- meet certain competency requirements, and
- receive workplace-specific information, training and instruction by or on behalf of the business, and
- obtain a certified handler compliance certificate from a compliance certifier.
You need a certified handler for:
• substances that require a controlled substance licence (CSL), such as most explosives, fumigants and vertebrate toxic agents (VTAs); and
• acutely toxic (6.1A and 6.1B) substances.
*See: WorkSafe / Certified handler requirements
Minimum Responsibilities
Everyone on a screen production who does, or could, work with hazardous substances, should read and understand this section.
All workers must:
- follow all health and safety information, training and instruction they have received;
- must be aware of what personal protective equipment they are expected to provide themselves and what will be provided by the production;
- follow instructions provided by the person in charge of any activity that involves the use of, or is conducted near, hazardous substances; and
- know escape routes when working around or near hazardous substances; if they are unsure of the escape route check with the 1st assistant director to learn the escape route before entering the work area.
Managing Hazardous Substances
Anyone who operates or is responsible for, or has influence over, hazardous substances must read and understand this section, as well as the sections on minimum responsibilities and planning and guidance considerations and responsibilities.
Create an Inventory
First and foremost, it’s important to know what hazardous substances are being stored or used on a production.
- Make an inventory of all the hazardous substances manufactured, used, handled or stored at your workplace including hazardous waste.
- Keep your inventory up-to-date and accurate.
- Make sure your inventory is readily accessible to emergency services workers.
The Hazardous Substances Calculator will help you create an inventory and work out what key requirements you need to meet, based on the hazardous substances you use, handle, manufacture and store at your workplace.
*See: WorkSafe / Inventory
Assess and Manage the Risk
All hazardous substances have a level of risk.
If there is no alternative and it is necessary to use hazardous materials on the production, those responsible for the use of the hazardous substance need to identify all risks associated with the hazard and decide on how to manage the risk by minimising it.
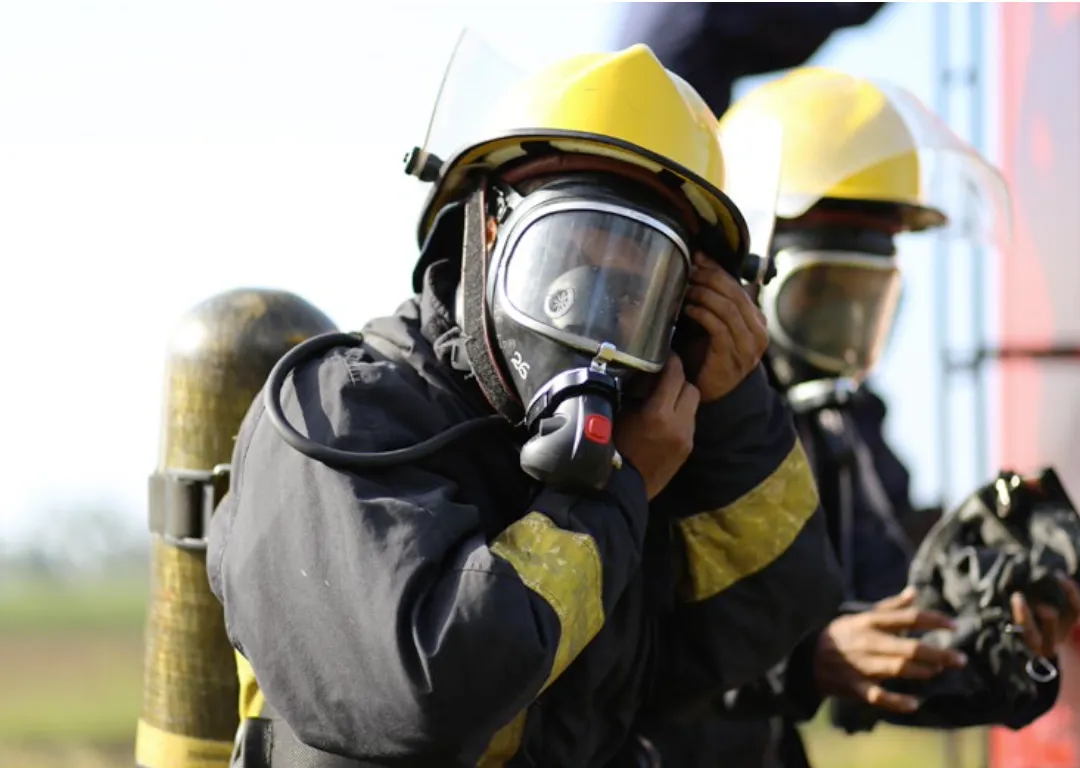
Minimising Risk
If you cannot eliminate the risk, there is a hierarchy of minimisation options.
*See: WorkSafe / What the Hazardous Substances Regulations mean for you
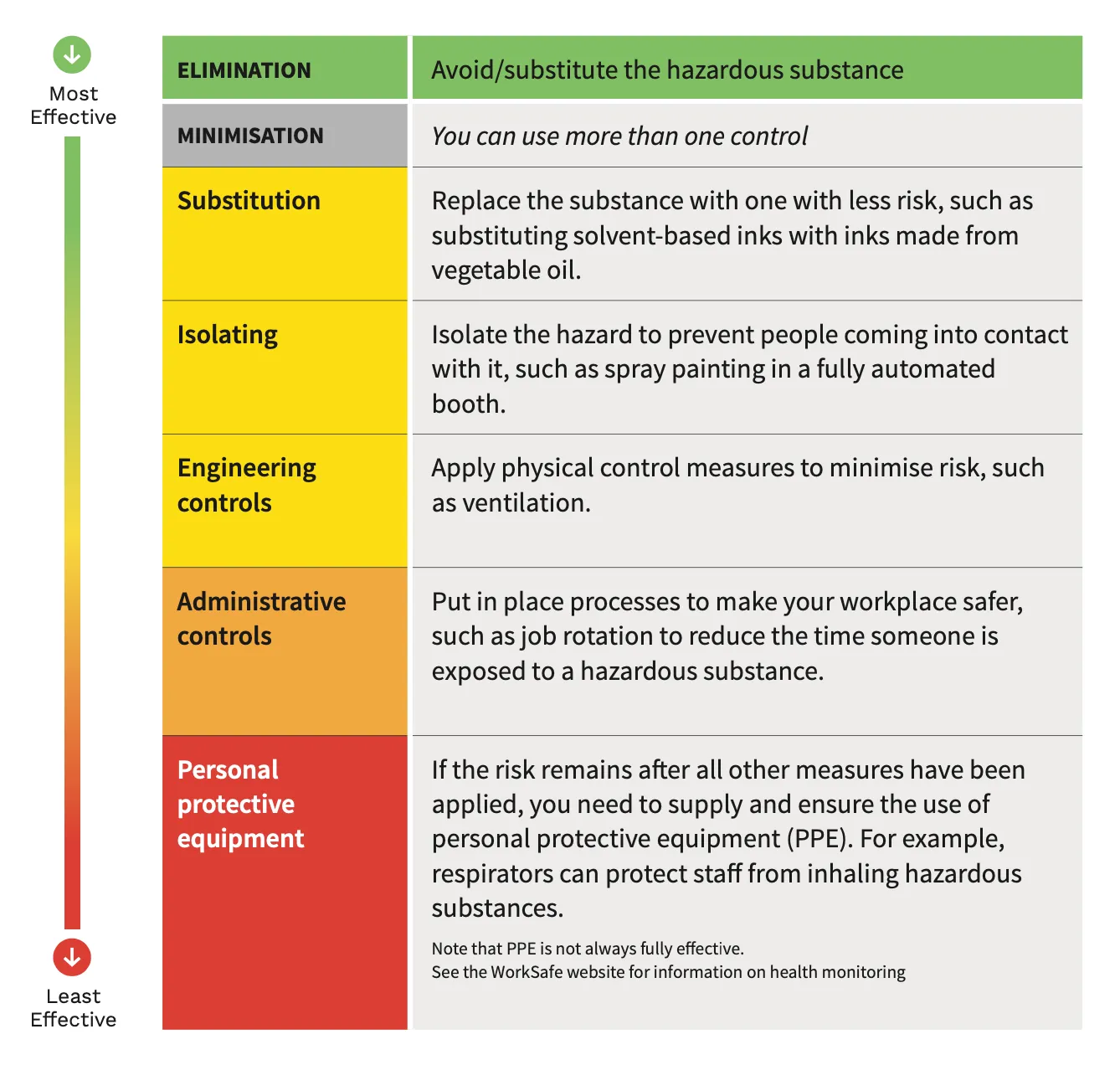
Keeping People Safe
If hazardous substances are used on a production, there are multiple ways you can keep workers and visitors safe.
Inform and Train Workers
Ensure everyone who works with or around hazardous substances has the experience and knowledge to do so safely.
Inform workers of hazardous substances on the production, and the control measures in place during the daily health and safety briefing and place this information on the call sheet.
Label Containers
You need to ensure containers of hazardous substances are always clearly and correctly labelled, this includes:
- substances that have come from a supplier and are therefore already labelled;
- substances that you decant or transfer into a smaller container at your workplace;
- stationary tanks, process containers and transportable containers; and
- hazardous waste.
*See: WorkSafe / Labelling
Install Signs
Place clearly visible signs at entranceways, and on buildings, or in outdoor areas, where substances are used or stored. They should inform people of what hazardous substances are present, the general type of hazard and what to do in an emergency.
*See: WorkSafe / Signs
Store Hazardous Substances Safely
Where and how you store hazardous substances will depend on the type of substance and the amount you have.
The Health and Safety at Work (Hazardous Substances) Regulations 2017 set out the requirements for storing different types, classes and quantities of hazardous substances in different situations.
The MSDS includes handling and storage information about the substance.
*See: WorkSafe / Storage
Plan for an Emergency
If using hazardous substances an emergency plan should be developed, it must:
- address all ‘reasonably foreseeable’ emergencies;
- state any special training needed to deal with an emergency involving each substance;
- include the inventory of hazardous substances present at the workplace;
- include a site plan showing all the hazardous substances locations in the workplace; and
- advise how you will:
- ~ call emergency services
- ~ warn people at the workplace and nearby about the emergency
- ~ advise people how they can protect themselves
- ~ help or treat any one injured in the emergency
- ~ manage the emergency to restrict its effects to the initial area, reduce its severity and if possible, eliminate it.
Fire and Emergency New Zealand (FENZ) can review your plan.
*See: WorkSafe / Emergency plans
Disposal and Recycling
Unused chemicals, and empty chemical containers, are a risk to people, the environment and animals.
You can arrange for unused chemicals to be disposed, or empty containers recycled, through AgRecovery. Information about disposing of products can also on be found on the MSDS.
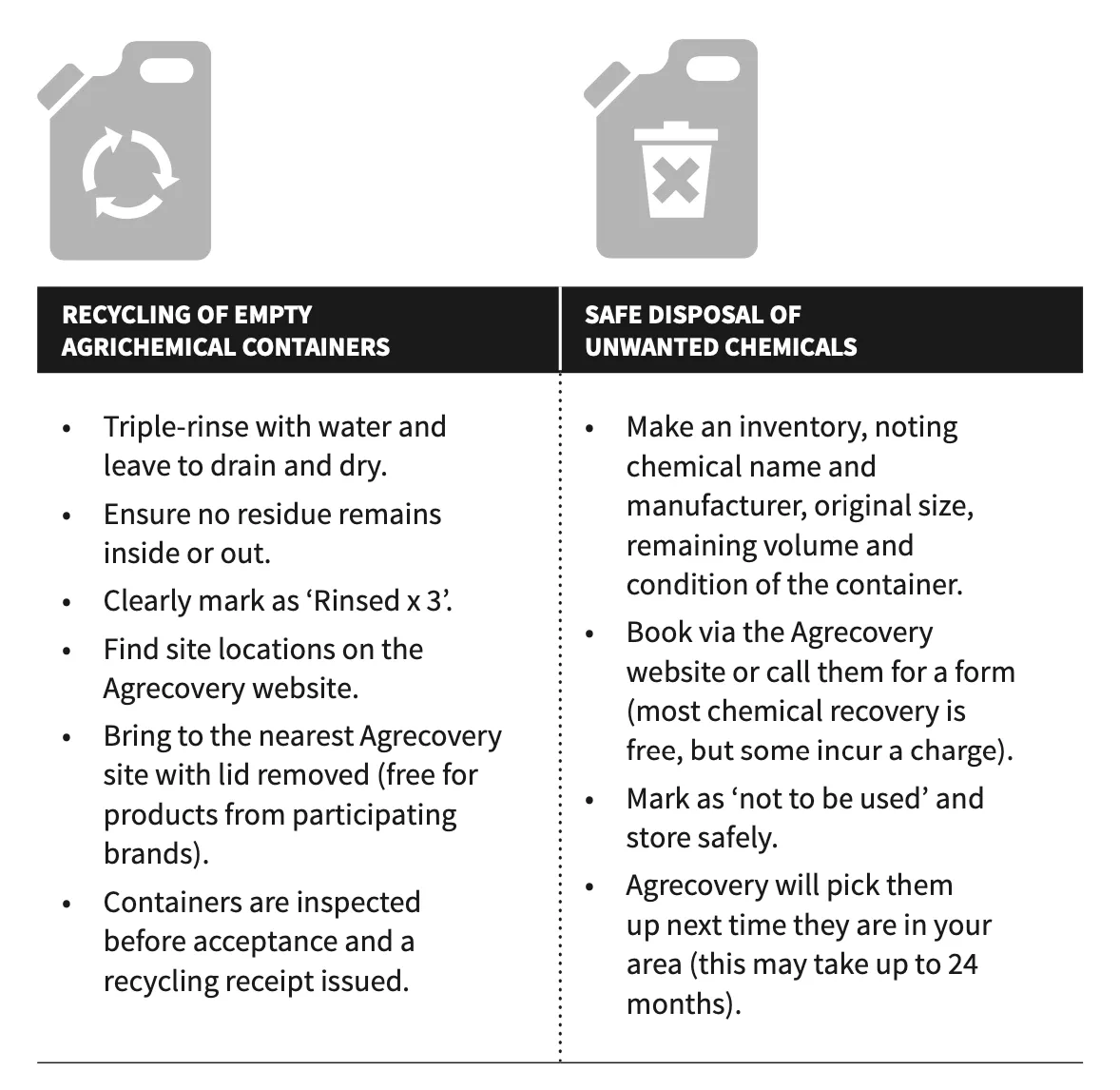
Transport
A certified handler must always be present when explosives are being transported.
Transport of hazardous substances are covered by the relevant transport agency.
Road and rail – the New Zealand Transport Agency
Key points to note:
- Generally, if you're transporting dangerous or hazardous goods, you need a dangerous goods (D) endorsement on your driver licence.
- For transport, dangerous goods are identified with a UN number, a proper shipping name and a diamond-shaped class warning label. Some products also have special marks to warn of hazards that are not indicated by other labels or marks.
- The Land Transport Rule: Dangerous Good 2005 (Rule 45001/1) details how you can transport dangerous goods safely and securely, depending on the nature and quantity of the dangerous goods.
Sea – Maritime New Zealand
Key points to note:
- Controls must be in place to safely manage the hazardous substances.
- An inventory of the hazardous substances you use, handle or store on board must be maintained.
- Anyone who uses or handle hazardous substances must have training to do so.
- The advice on the MSDS must be followed.
- All hazardous substances must be correctly labelled.
- Signs must be displayed to let workers, visitor and emergency service personnel know there are hazardous substances onboard.
Air – Civil Aviation Authority of New Zealand
Key points to note:
- Articles and substances must be properly classified according to a set of standard criteria.
- The packaging used for dangerous goods must meet certain criteria set by the technical instructions.
- The hazards posed by these articles and substances must be identified by markings, package labels and accompanying documentation.
- An airline must have the opportunity to inspect and verify the acceptability of each dangerous goods package as declared by the shipper.
Planning and Guidance Considerations and Responsibilities
Everyone has planning responsibilities for or planning influence over activities that interact with hazardous substances should read and understand this section, as well as the above sections.
This includes funders, the Production Company, Producers, Heads of Department, and Health and Safety Advisors.
Funders
Funders should:
- be assured, through the provision of the production’s health and safety plan, that the funding provided is adequate to provide for competent people to undertake and supervise work with hazardous substances; and
- ensure that all senior contractors have sufficient insurance cover, appropriate to the risk and scale of the work to be undertaken.
Production Company
In pre-production, production companies (likely to have primary responsibility over health and safety on the production) should:
- ensure people who use hazardous substances are competent in their use;
- consider the potential risks associated with hazardous substances when planning and allocating tasks; and
- ensure the potential risks associated are appropriately managed, either eliminating or minimising them.
Producers and Production Managers
As Producers and Production Managers have oversight across the production, they should:
- communicate to all personnel the presence and/or use of hazardous substances;
- provide appropriate information on safety matters should be included;
- ensure workers are provided appropriate personal protective equipment;
- ensure workers are wear appropriate personal protective equipment;
- ensure that emergency and first aid procedures are in place;
- ensure sufficient firefighting equipment is provided and that it is immediately available on set if required; and
- ensure there is a clear access way for emergency and firefighting equipment and vehicles on set.
Heads of Department
As Heads of Department have specific oversight of areas of work that may use hazardous substances for specific task, they should:
- ensure workers using hazardous substances carry the necessary skills, certifications and / or experience;
- ensure hazard identification and risk assessments are undertaken for all activities using hazardous substances, and controls implemented;
- ensure that emergency and first aid procedures are followed;
- ensure personal protective equipment specific for hazardous substance work is provided to, and used by, workers when required;
- communicate to all personnel the presence and/or use of hazardous substances;
- provide appropriate information on safety matters should be included;
- ensure workers are provided appropriate personal protective equipment; and
- ensure workers wear appropriate personal protective equipment.
Health and Safety Officer
The Health and Safety Officer should ensure potential risks associated with hazardous substances are discussed with all cast and crew during health and safety inductions and / or as required if circumstances on the set change.
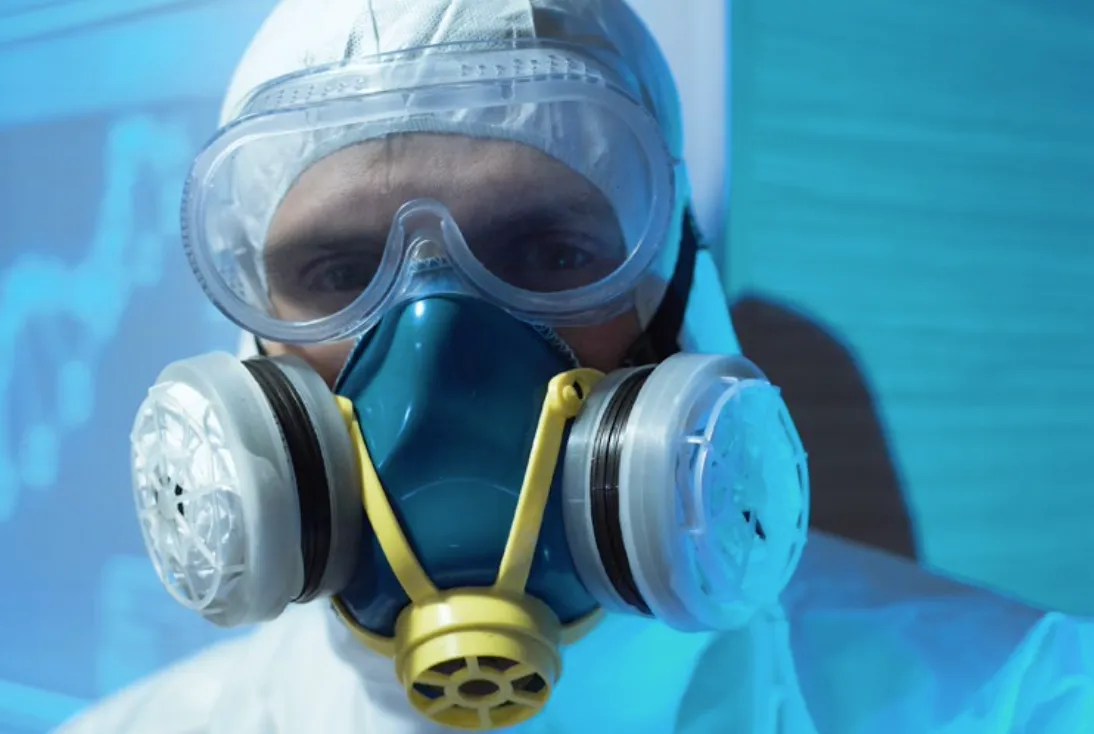
Training and Knowledge
Hazardous substances must only be used by people with knowledge about the substance, its health effects and emergency procedures.
Substances requiring a controlled substance licence (CSL), such as most explosives, fumigants and VTAs, and acutely toxic (class 6.1A and 6.1B) substances, such as certain pesticides and VTAs, need to be handled by a certified handler.
However, in some cases, people who are not certified handlers can handle substances with certified handler requirements, which are outlined in WorkSafe’s quick guide – certified handler requirements.
To check if you need a certified handler in your workplace, enter your substances into the Hazardous Substances Calculator or search the Environmental Protection Authority’s Approved Hazardous Substances with Controls database.
Anyone handling or working with hazardous substances needs to:
- be trained or supervised in safe handling procedures;
- be provided with information and MSDS about the product;
- understand the physico-chemical and health hazards associated with the hazardous substances;
- understand the procedures for the safe use, handling, manufacture, storage and disposal of the hazardous substances;
- ensure their safety, and the safety of others, when using the hazardous substances;
- understand obligations under the Health and Safety at Work (Hazardous Substances) Regulations 2017; and
- know the actions to be taken in an emergency involving the hazardous substances.
Being a certified handler can help fulfil these requirements.
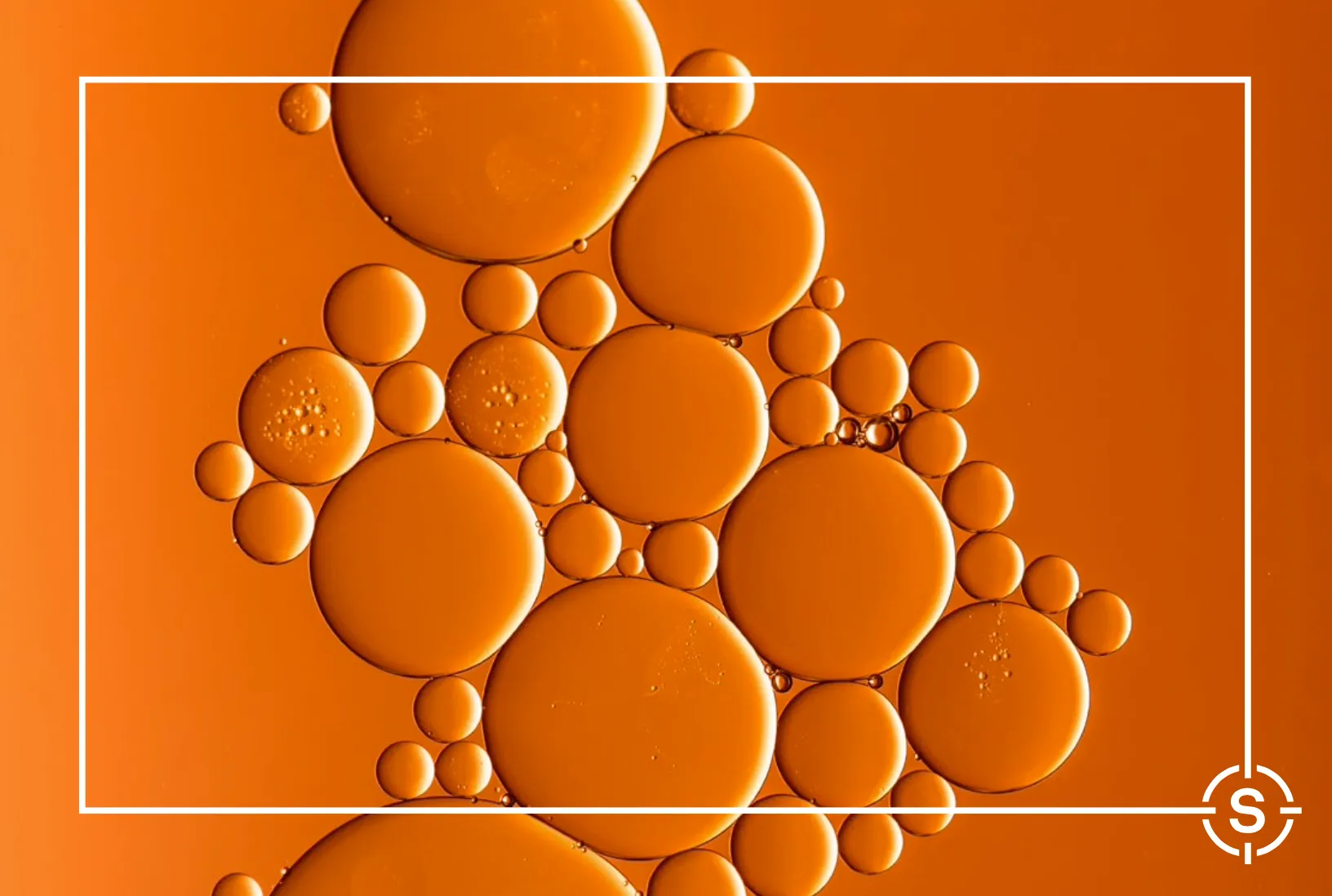
Hazardous Substances
Who needs to read this?
While all workers involved in a production have health and safety duties regarding the location of the shoot, roles that have specific responsibilities include the production company representatives, producer, director, production manager, heads of departments, assistant directors, health and safety officers and location manager.
What is a location?
A location, for the purpose of this chapter, is a place where some or all of a screen production – including film, television shows, documentaries, television commercials or web productions – is produced outside of a studio set (which is dealt with in a separate chapter). Potential locations are usually identified during scouting and then confirmed after consultation with heads of departments regarding workability.
The role of a Location Manager
A Location Manager is responsible for the finding and securing of the location/s to be used, obtaining required permits and coordinating the logistics involved to successfully complete the production. During the scouting process and pre-production, the location manager must take health and safety into consideration, advising directors and/or producers of potential risks when identifying possible locations and taking into account those risks when preparing the site for production.
Depending on the size of the production and available resources, there may or may not be a Location Manager If there is not a specified Location Manager, the person/s responsible for scouting and preparing the location/s for the production shoot should follow the guidance in this chapter provided for the Location Manager

Types of locations
When considering the type of location for the production shoot, the production company, Director, Producer, Production Manager and Location Manager must take into account potential risks to health and safety and how these could be controlled.
While this chapter will not go into detail about specific types of locations, as the variables will be different in every case, listed below are some general and specific health and safety considerations to be taken into account depending on the type of location being scouted and/or used for filming.
Remote locations
- Local knowledge and expertise should be sought when planning activities in remote locations.
- Competent guides should be used where appropriate, especially in extreme conditions, such as in snow, on mountains or around water areas.
- Local police and emergency services should be advised when workers are operating in remote locations, including specific details of the location/s and expected duration of the stay.
- Reliable two-way communications should be available at all times.
- Adequate food and water supplies should be available to meet the needs of an extended stay. Local water supplies might not be safe for drinking and potable water should be available.
- Emergency supplies and equipment should be taken in case of unforeseen and extended circumstances.
- In the case of an extended emergency stay, consideration should be taken as to how long it could take to evacuate all workers.
- At least one worker should be competent in first aid and CPR.
- The need for an emergency beacon and / or GPS should be considered, especially for those working alone.
Public places
- Local authorities and police should be consulted when planning activities in public places, and all necessary permissions received. Local authority or landowner
(for example the Department of Conservation or Land Information New Zealand) permission is required to block public access. - Access to all film equipment should be controlled, with public access suitably restricted.
- All warning signs, for example road control or information about access, should be clearly visible, taking into consideration the ability to see the signs at night.
- Public passageways should be kept tidy and free of obstructions; where necessary signs should be posted, lookouts posted or alternative routes organised.
- Provisions should be made to adequately control any crowd that may gather and / or to assist pedestrians passed the location.
Sacred places
- Many locations within New Zealand are tapu (sacred) to local iwi , who may have specific requirements or requests regarding the use of their land.
- Every location should be dealt with on a case-by-case basis, and local iwi should be consulted about safety and potential risks, not only regarding use of land and their local expertise, but for cultural and spiritual guidance where appropriate.
- Refer to The Brown Book for information about the Māori screen industry.

Minimum responsibilities for everybody on location
Everyone involved in a screen production should read and understand this section.
Everyone involved in a location shoot:
- is responsible for ensuring their tasks are conducted safely;
- is required to follow the Health and Safety at Work Act 2015, as well as all health and safety information, training and instruction they have received;
- should be familiar with all emergency plans developed for the location/s they are working at;
- should take part in all safety briefings for every location;
- should inform the production manager, 1st assistant director, head of department or health and safety officer if they feel unsafe or observe unsafe behaviour;
- should inform the location manager if they have a health and safety concern regarding the location of the production shoot;
- must take care of others on location – from the moment they start work on the production until wrap, ensuring others safely depart the location;
- must ensure their actions do not harm themselves or others, including visitors and the public; and
- must be aware of what personal protective equipment they are expected to provide themselves and what will be provided by the production.*
* Standard personal protective equipment, such as sturdy footwear / work boots and rain jackets, will likely be provided by the worker, unless specified by the producer / production manager.
Planning and guidance considerations and responsibilities
Everyone who is responsible for an activity or task in relation to the location of the production should read and understand this section as well as what is required by all workers. This includes the production company, director, producer, production manager, heads of department and assistant director/s.
Production Company
In pre-production, production companies (likely to be defined as the primary PCBU) must clearly identify who has control of the various locations that will be used throughout the production process, and ensure those people are competent.
During production, production companies must consult, cooperate and coordinate with other PBCUs on set, duty holders in charge of the location/s to be used and subject matter experts.
Producer / Production Manager
Producers and Production Managers should ensure:
- all information about potential risks associated with each location and required onsite activities are considered during pre-production location scouting and when deciding on the final location/s for the production;
- all workers are aware of health and safety risks on location;
- all workers have appropriate personal protective equipment for risks found on location;3
- there is at least one person with the appropriate level of first aid and CPR knowledge, if not more depending on the size of the production, location and type of shoot;
- emergency supplies appropriate to the location, including clothing, food and water, are provided in case of an emergency;
- information is distributed to cast and crew every day identifying all health and safety related matters specific to the location, such as specific risks and travel details – this could be included on the daily call sheets; and
- safety considerations are made regarding safely departing the location.
The Producer should also:
- consider hiring a competent location manager with suitable experience for the size of the project;
- consider appropriate safety measures required if the location manager is working alone in a remote setting – for example the use of personal locator beacons;
- ensure hazard identification and risk assessments are undertaken for all locations;
- ensure all potential risks on location are eliminated or, if elimination is not reasonably practicable, minimised; and
- ensure that emergency and first aid procedures, specific to each location, are in place.
The producer, together with the director and heads of department, should consider the number and level of risks associated with proposed locations ahead of any final location decisions being confirmed. It is important to identify the possible risks to workers’ health and safety as soon as is reasonably practicable during the location scouting and selection stage.
Director / Heads of Department
When proposing the type of location required for production, the Director and Heads of Departments should seek advice and consider the potential risks that may arise/be present.
From early in the pre-production process, they must consult, cooperate and coordinate with each other, and any appropriate subject matter experts working on the production, to ensure they are aware of all potential risks prior to committing to locations.
The Director, together with the Producer and Heads of Department, should consider all the information available and the number and level of potential risks associated with proposed locations ahead of any final location decisions being confirmed. It is important to identify the possible risks to workers’ health and safety as soon as is reasonably practicable during the location scouting and selection stage.
Heads of Departments
Heads of Departments should:
- ensure they are aware of, and understand, all identified potential risks associated with each location and how they may impact the work of their department;
- undertake their own hazard identification and risk assessment of their specific departmental activities on location (as the expert in their particular field of work);
- implement controls, ensuring all risks are eliminated or, if elimination is not reasonably practicable, minimised; and
- inform the location manager, production manager and/or health and safety officer of any new or altered risk.
Assistant Director/s
In the absence of a Health and Safety Officer, the Assistant Director/s should:
- ensure hazard identification and risk assessments are undertaken for all locations, and controls implemented;
- ensure that emergency and first aid procedures, specific to each location, are followed;
- ensure personal protective equipment, specific for the location is provided to, and used by, workers when required;
- conduct safety inductions with cast, crew and others whenever filming has moved to a new location; and
- read and understand the section of this chapter intended for health and safety officers.
Responsibilities specific to shooting locations
All those with specific technical responsibilities regarding locations, such as Location Managers and Health and Safety Officers, or persons charged with these responsibilities, should read and understand what is required in this section, as well as the above two sections.
Health and Safety Officer
Pre-production
The Health and Safety Officer should:
- work with the Location Manager and other Heads of Department to identify all potential hazards and assess risk;
- consider, from the outset, the size of the production and how much time is required to ensure all relevant people are able to provide input into the health and safety planning;
- conduct a health and safety specific assessment on each location before production;
- develop a health and safety report for the production and each location;
- liaise with the appropriate competent persons to identity and implement appropriate controls for all risks;
- conduct safety inductions whenever filming has moved to a new location;
- ensure workers are provided, or advised of, the appropriate personal protective equipment required on the location;
- ensure emergency supplies, including clothing, safety, food and water, are provided in case of an emergency;
- liaise with external medical facilities to ensure sufficient support can be provided if required; and
- ensure there is at least one person with the appropriate level of first aid and CPR knowledge, if not more depending on the size of the production, location and type of shoot.
Emergency Plans
The Health and Safety Officer should:
- develop an appropriate emergency plan to cover all emergency situations for each specific location; and
- ensure appropriate rescue and evacuation practices are undertaken.
Emergency Services
The Health and Safety Officer should:
- consider how long would it take for emergency services to reach all areas of each location;
- consider what communication avenues are available to enable contact with emergency services at all times;
- ensure the distance of emergency services and the ability to contact them are included in all emergency planning, along with an alternative plan should emergency services not be able to reach the location in a timely manner; and
- inform local emergency services of the location shoot, especially in remote locations.
Location Manager / Scout responsible for securing location
The primary role of the Location Manager / Scout is to identify and find ideal locations for a production shoot. They tend to report to the producer.
Location Managers should have a good understating of:
- the Health and Safety at Work Act 2015 and associated regulations; and
- potential risks found on location.
Scouting and Pre-producion
A Location Manager’s work starts when they are first contracted to scout a location for a production shoot and must understand the Director’s vision for the film in order to find ideal locations.
Considering health and safety issues for all workers during the scouting process not only ensures workers go home safe, but can reduce the cost of a production and save time and resources in the long term.
In scouting potential locations for a production shoot, Location Managers must:
- identify potential hazards and assess risk;
- request information about hazards and the associated risks from landowners;
- consult with relevant experts and authorities who have local knowledge of potential risks;
- collaborate with the health and safety officer in assessing the risks and required controls for any specific location; and
- ensure all information is captured in an appropriate and easy to understand manner. When refining location options, location managers must:
- assess the level of risk associated with potential hazards;
- weigh up the level of risk; and
- consider how risky a location would be for the cast and crew.
Consideration must also be made for having elderly, children and/or disabled on location, if applicable.
Welfare Arrangements
Welfare arrangements must be taken into consideration when both scouting potential locations and refining options; these arrangements must stay in place during production.

Risks to Safety and the Working Environment
When scouting for locations and refining options, specific issues with location environment and potential risks must be considered, and appropriate control measures put in place if required.


Multiple Risks
Location Managers must consider multiple risks while scouting locations and assessing those risks.

After considering all possible locations, the Location Manager must provide all information they have obtained, including identified potential risks with each location, to the Production Manager, Producer and/or Director.
Production
Once filming has started, location managers are responsible for managing all aspects of the shooting in, and overseeing the production’s use of, each location.
Location managers must ensure:
- the cast and crew know how to get to the location safely;
- access to the production site is controlled to stop other persons from entering and risking their own health and safety – or if use of the location is dependent on keeping access open to the public, security measures are in place to keep other persons safe;
- welfare requirements are adhered to at all times;
- there is appropriate heating, cooling and weather protection for crew and cast;
- safe access to locations;
- security is provided where required; and
- that potential contaminants, such as paints, thinners, repellents, gasoline and oils, do not pollute land and waterways.
General Public
Remember, even though the production company is likely to be the primary PCBU, all PCBUs are responsible for the overall safety of all users of each location while the production is operating, including visitors and other persons on, or in the vicinity, of the workplace.
The location manager should ensure appropriate signage, cones and/or barriers are in place to keep public safe.
If using a public road, the location manager must inform traffic control about what is required for the production shoot, ensuring the production does not place undue inconvenience on traffic or pedestrians and that pedestrians are never forced to step onto an adjoining road without adequate protection from traffic.
Movement of People On Set
Production sets are a busy work environment and control measures must be put in place to ensure all workers can safely move around the set. Issues to consider include, but are not limited to:
- slips, trips and falls on the same level – for example poor or uneven floor/pavement surfaces, badly lit walkways or a leak;
- falls from heights – both objects falling and injuring a person, or a person falling;
- being struck by intentional moving or flying objects – ensuring people know what is happening in front of and behind the camera;
- collisions with vehicles – think about separating pedestrians and vehicles; and
- striking a fixed or stationary object – ensure there is good lighting, hazards are signposted and define walkways.
Night Work
All steps necessary to make a location as safe at night as it is required to be during the day must be considered; this may include additional working/access lights as well as extra heating, clothing, food and time.
Signage
Signage to ensure the health and safety of workers and other persons must be considered, including:
- letting the public know what is happening; and
- informing cast and crew of any restricted areas, restricted access and welfare requirements.
Movement Orders
Location managers are responsible for preparing movement orders, outlining directions to locations, enabling cast and crew to travel safely from the production base or home to each location.
Movement orders must be accurate and easy to understand, and should be provided to cast and crew with daily call sheets.
Location managers should ensure the route to the location is clearly signposted, and check the conditions each day to ensure it is safe for driving. High-risk areas should be highlighted in the movement order.
Fatigue and Schedules
Fatigue is a high risk within the screen sector, and must be taken into consideration when scheduling shifts for cast and crew; this includes thinking about the regulations set out for driving hours.
See the guidance chapters on fatigue and motor vehicles for further information.
Vehicles and Traffic Routes
If vehicles are required on set, specific traffic routes and speed limits should be implemented. One-way systems and separate vehicle and pedestrian access should also be considered.
If vehicles cross public pathways, the safety of the general public must be considered. See the guidance chapter on motor vehicles for further information.
Wrapping Production
After filming, the Location Manager should ensure:
- potential contaminants, such as paints, thinners, repellents, gasoline and oils, do not pollute land and waterways;
- all signage, cones or barriers are removed;
- all rubbish is removed from the location;
- all location sites are left as they were found; and
- all workers safely depart the location.

Locations
Who needs to read this?
All workers who undertake work with, or work that interacts with, motor vehicles or drive to work should read and understand the section on ‘minimum responsibilities’.
Roles that have specific responsibilities, or influence, over work with motor vehicles should read the section on ‘planning and guidance considerations’ – this includes producers, directors, production managers, line producers, heads of departments, assistant directors and health and safety officers.
Anyone who operates or is responsible for, or has influence over, a motor vehicle must read and understand all sections of this chapter. This includes drivers of Heavy Motor Vehicles/ Goods Service Vehicles of more than two axles or greater than 3500 kilos manufacturer's gross laden weight, and to drivers of any vehicle carrying more than 10 passengers.
Definitions
Action vehicle means any moving vehicle being used as part of a film sequence.
All-terrain vehicle (ATV) means any vehicle that is principally designed for off-road use. They have three or more wheels, an engine capacity exceeding 50ml and a gross weight of less than 1000kg.
Motor vehicle means any powered vehicle or trailer used on or off the road. Tracking vehicle means a vehicle that is used for the mounting of cameras and
other equipment for photography of, or in, a stationary or moving vehicle.
Specific risks
- Being struck by a vehicle
- Crashes between vehicles and with structures and equipment
- Falls from vehicles
- Fatigue
- Fire
- Exhaust fumes
Minimum Responsibilities
Everyone on a screen production who does, or could, work with motor vehicles, or drives to work, should read and understand this section.
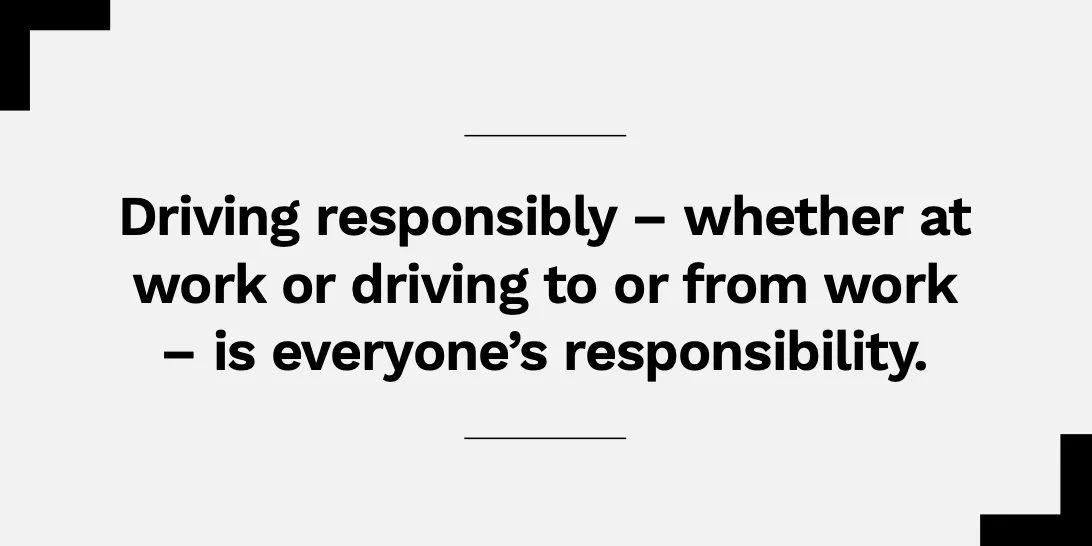
All workers must:
- hold the appropriate license/s for the vehicle/s they drive;
- understand and follow New Zealand laws and regulations relating to motor vehicles and driving;
- understand how fatigue can impact their ability to drive safely and should read the fatigue chapter;
- wear seatbelts, where fitted;
- abide by the alcohol and drugs chapter (link to alcohol and drug chapter); and
- inform the production manager if they lose their license.
Foreign drivers should follow this chapter and can find out more useful information from the NZ Transport Agency.
Planning and Guidance Considerations and Responsibilities
Everyone who has planning responsibilities for or planning influence over activities that interact with motor vehicles should read and understand this section, as well as the minimum responsibilities for everybody.
This includes funders, the Production Company, Producers, persons in charge, and Health and Safety Officers.
Person in charge
The person in charge / those with direct planning responsibilities for or influence over a driver (such as the worker’s superior or the person who hired them) must ensure the driver:
- holds the appropriate license/s for the vehicle/s they drive; and
- abides by the guidelines outlined in the section ‘Responsibilities specific to operating motor vehicles’ below;
- is given, and does not exceed, limitations for driving;
- is given adequate time off; and
- reads and understands the chapter on fatigue.
Funder
Funders should:
- be assured, through the provision of the production’s health and safety plan, that the funding provided is adequate to provide for competent people to undertake and supervise work with motor vehicles.
Production Company / Producer / Production Manager
- Production companies (likely to have primary responsibility over health and safety on the production) must:
- consider the potential risks associated with the use of motor vehicles when planning and allocating tasks;
- ensure the potential risks associated are appropriately managed, either eliminating or minimising them; and
- consider fatigue and workloads involving driving when creating schedules;
- engage competent persons to oversee and undertake work with motor vehicles.
- ensure location and studio driving restrictions are followed – for example a lower speed limit on a studio lot.
Health and Safety Officer
The Health and Safety Officer should ensure potential risks associated with motor vehicles are discussed with all cast and crew during health and safety inductions and / or as required if circumstances on the set change.
Responsibilities specific to operating Motor Vehicles
Anyone who operates or is responsible for, or has influence over, a motor vehicle must read and understand this section, as well as the previous sections, including, but not limited to, drivers of passenger vehicles, Heavy Motor Vehicles and Goods Service Vehicles.
Drivers – all
All drivers must:
- hold the appropriate license/s for the vehicle/s they drive; and
- understand and follow New Zealand laws and regulations relating to motor vehicles and driving – in particular restrictions specific to their type of driver’s license, for example:
- ~learners license;
- ~small passenger service vehicle license;
- ~heavy vehicle license; or
- ~motorcycle license.
All drivers should:
- undertake a safety check of the vehicle and any attachment before each job;
- check the vehicle has a current Warrant of Fitness or Certificate of Fitness or Permit to Operate;
- check heavy vehicles’ road user charges (RUC) are up-to-date;
- read and understand the section below on tracking vehicles, action vehicles, and/or all-terrain vehicles if relevant to their role as a driver;
- not exceed legal, or recommended, driving limitations; and
- have adequate time off duty.
Person in charge
The person in charge of those operating motor vehicles – such as a direct supervisor or the person who hired the worker – on or around the production should ensure:
- drivers have adequate time off duty; and
- where possible, that drivers do not exceed driving limitations.
Driving Limitations
It is recommended that all drivers on a production follow the same rules provided by the New Zealand government to drivers of heavy motor vehicles / good service vehicles and small passenger service vehicles.
This means, in any 24-hour period drivers:
- should not drive for more than 11 hours;
- should not drive for more than 5.5 hours continuously, and the minimum break is half an hour;
- should not be at work or be on duty for more than 14 hours
- ~~this includes all working and driving time combined, whether paid or unpaid; "on duty" is defined as any time required to carry out the requirements of the job and includes any other paid employment in which a person is engaged;
- should be off-duty for at least nine hours continuously; ie: from the time a person finishes work at the end of the working day to the time a person starts back at work.
NOTE: There are substantial fines and disqualification penalties for abuse of these rules and they may be imposed on both the driver and the employer.
Tracking Vehicles
Drivers of tracking vehicles should understand and ensure recommendations in this section are followed.
Vehicle-to-Vehicle Shoots
When performing vehicle-to-vehicle shoots, the vehicles should be driven by a driver competent in close moving vehicle driving.
Restricted Access to the Vehicle and Safe Loading
The vehicle should be restricted to essential personnel only and the loading shall be within the safe loading limits of the vehicle.
There should no more people in the vehicle than there are seats with seatbelts.
Public Roads
When filming on or adjacent to public roads a Traffic Management Plan (TMP) must be applied for and approved by the roading authority responsible for
that section of road. TMP's can only be obtained through a registered traffic management company. It is recommended that a traffic management company familiar with filming and events is contracted to provide these services.
When filming on or adjacent to a public road where the driving public may be distracted, the Police should be notified. Adequate warning should be given to other traffic of a tracking vehicle operating. The Traffic Management Company notifies Police if necessary, not the film company.
If on an open road, the overall dimensions of the vehicle should not exceed the dimensions set out by the NZ Transport Agency.
Traffic Controller
When filming on or adjacent to public roads, a designated traffic controller must be engaged, likely by the locations manager, to be responsible for carrying out temporary public traffic control duties as required.
The traffic controller:
- must use appropriate safety equipment and clothing; and
- has the responsibility to stop a shoot if the crew are operating outside of the approved condition of the TMP
Mounting Equipment on the Vehicle
Any equipment attached to a vehicle that is to be driven on a public road must be included in the TMP (see above) and approved of in advance by the issuing authority.
Equipment mounted on the vehicle must be firmly attached to the vehicle.
If using lamps or other equipment running off 230 volt power supply (mains, generator or invertor), lamps must comply to relevant New Zealand regulations and the chapter on electrical safety should be read and followed.
Any rigging on a vehicle must be undertaken by a competent person.
Equipment rigged inside or outside of a vehicle should be secured so as to not harm occupants in an accident.
NOTE: that rigging to outside and/or inside of vehicle may make vehicle safety devices inoperable or more dangerous in case of an incident.
Towing Weight Limitations
The manufacturers limitations on the maximum weight being towed by a vehicle should be complied with.
Safety in Adverse Conditions
Extra consideration should be given to the safety of personnel working on such vehicles in adverse conditions.
Communication between Traffic Controller and Driver
The 1st assistant director or person with delegated responsibility should ensure that adequate communication with the driver and traffic controller is established before any driving takes place.
Warning of Movement of Vehicles
Warning of the movement of vehicles should be given to all crew and cast members in the immediate vicinity of the vehicles.
Dry Run and Authority to Abort
A "dry run" or "walk through" of any action should be conducted prior to rehearsal or filming with all personnel involved present. An understanding of any intended action, possible deviations and authority to abort, should be made clear to all concerned.
Action Vehicles
The appropriate person in charge, for example the stunt or vehicle coordinator, must ensure action vehicles:
- are only be used under the control of a competent person; and
- whether independently mobile or not, are appropriate for the task for which it is to be used.
All-Terrain Vehicles
All-terrain vehicles (ATVs) include quad bikes, smaller ‘side-by-sides’ and amphibious vehicles.
On Road
When using ATVs on roads, drivers, and the person in charge, must ensure:
- the ATV is registered and licensed;
- the ATV has a current warrant of fitness (except if used as a farm vehicle);
- the driver holds a current New Zealand driver licence;
- the manufacturer’s recommendations for passengers and loading are followed
- ~~ there should only ever be one person on a quad bike; and
- the driver, and any passengers, wears an approved safety helmet.
Off Road
An ATV that is never used on a road does not need to be registered or licensed.
When using ATVs off roads, drivers, and the person in charge, must ensure:
- the manufacturer’s recommendations for passengers and loading are followed
- ~~there should only ever be one person on a quad bike; and
- the driver, and any passengers, wear an approved safety helmet.
For more information about ATV requirements visit the NZ Transport Agency website.
Recommended Reading
- Quads bikes and ATVs, NZTA
- Safe filming and recording in, from and around vehicles, HSE
- Vehicles: recording in, from and around, BBC
- Guidelines to filming on the move, Metropolitan Police
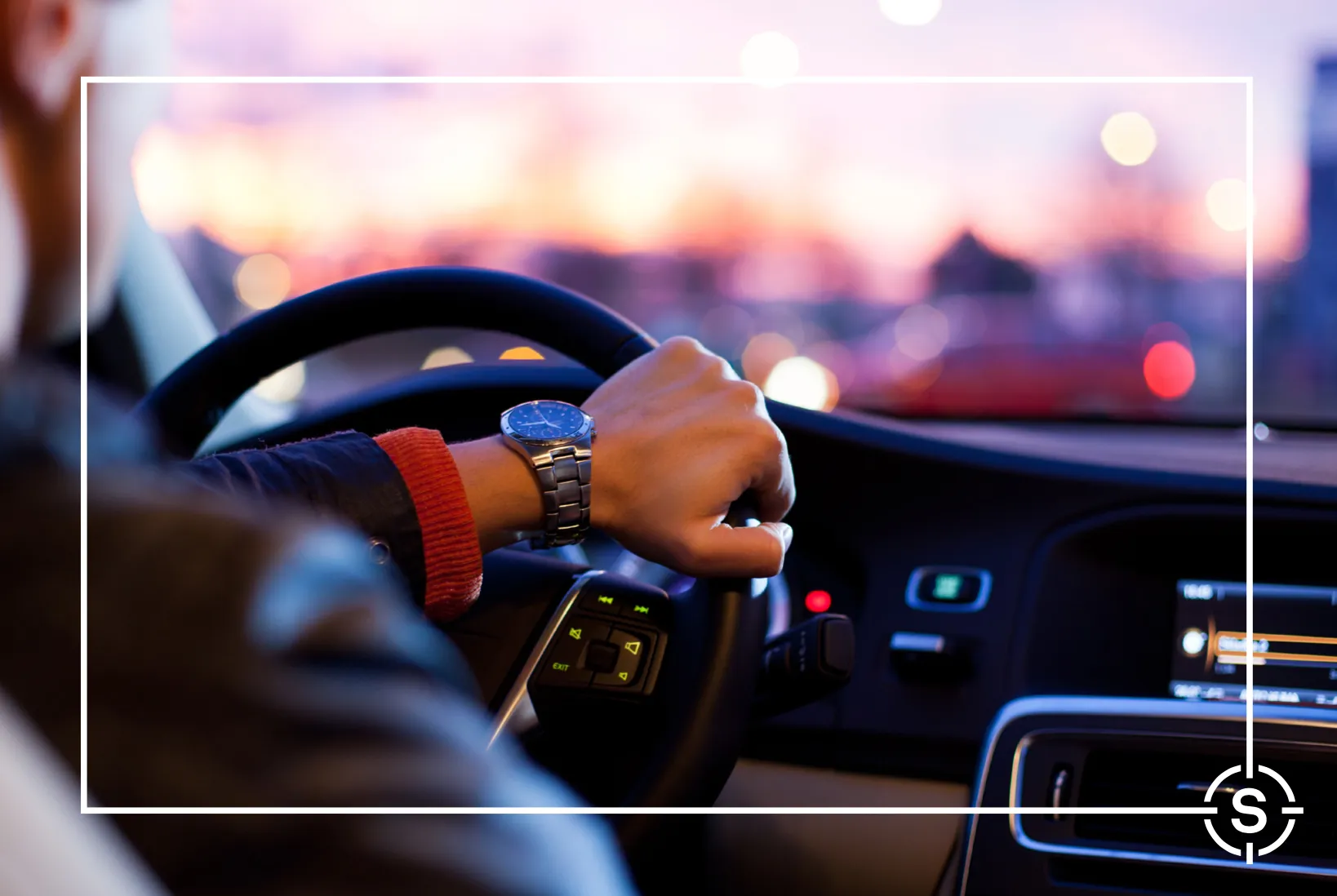
Motor vehicles – Restrictions
Noise Management
This chapter provides guidance in relation to noise, and is primarily based on New Zealand legislation and guidance issued by WorkSafe NZ.
Who needs to read this?
All workers who undertake tasks where they are, or could be, exposed to excessive noise should read and understand the section on ‘minimum responsibilities’.
Roles that have specific responsibilities, or influence, over workers who are, or could be, exposed to excessive noise should read the section on ‘planning and guidance considerations and responsibilities’ – this includes producers, directors, production managers, line producers, heads of departments, assistant directors and health and safety officers.
Definitions
Audiometry6 means the measurement of the hearing threshold level of a person by means of a bilateral pure tone air conduction threshold test.
Excessive noise, for the purpose of this document, is noise that is at or above the following levels—
~(1) eight-hour equivalent continuous A-weighted sound pressure level, LAeq,8h of 85 dB(A); and
~(2) a peak sound pressure level, L-peak, of 140 dB —whether or not the individual is wearing a personal hearing protector; or
~(3) if the threshold is lower, the levels defined in the Health and Safety at Work 2016 Regulations. Note: these Regulations are due to be updated and the noise threshold may be lowered.
Hearing protector means a device or pair of devices that have been tested to an appropriate national or international standard and classified (or graded) by a suitably equipped and independently audited laboratory with full trace ability to National Standards. Such a device is worn by a person or inserted in the ears of a person to protect that person from exposure to noise.
Impulse noise means noise consisting of a single pressure peak, or a sequence of such peaks, or a single burst with multiple pressure peaks, or a sequence of such bursts.
Noise means any sound which is present in the place of work whether it is wanted or not wanted, and includes sound energy of any frequency, whether or not capable of being perceived by the unaided human ear.
Noise induced hearing loss is hearing loss that occurs due to excessive noise exposure; it can be identified by deterioration in hearing, a loss excessive for age, or a noise pattern discovered during audiometric testing.
What we need to know about noise
Excessive noise, both short but extremely loud noise (impulse noise) and prolonged continuous noise, can cause noise induced hearing loss.
Exposure to excessive noise can also trigger workplace stress, causing anxiety or psychological harm, as well as headaches, fatigue and decreased concentration, increasing the risk of accidents. Excessive noise and noisy processes are also often associated with vibrations, which can impact a worker's health.
Excessive noise exposure can also prevent people from hearing alarms or warning signals, limiting awareness and potentially leading to avoidable accidents.
How can I tell what excessive noise is?
Daily exposure to noise above 85 decibels (dBA) will damage hearing; however, 85dBA might not mean a lot to most people.
Excessive noise, or a noise hazard, probably exists if:
- you have difficulty understanding what's being said one metre away;
- you have ringing in your ears (tinnitus) after exposure to the noise;
- or your hearing seems muffled after leaving a noisy area.
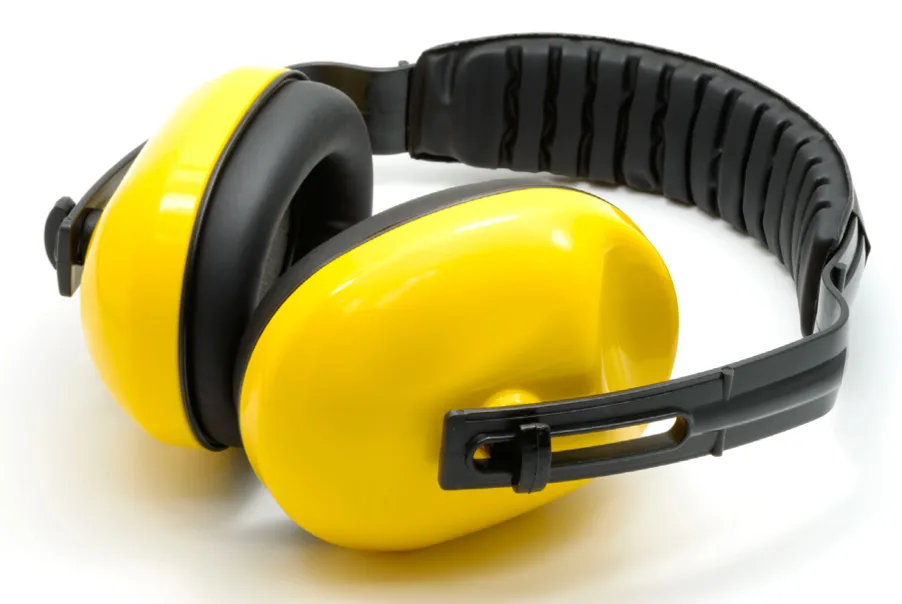
Example of noise levels are outlined below:
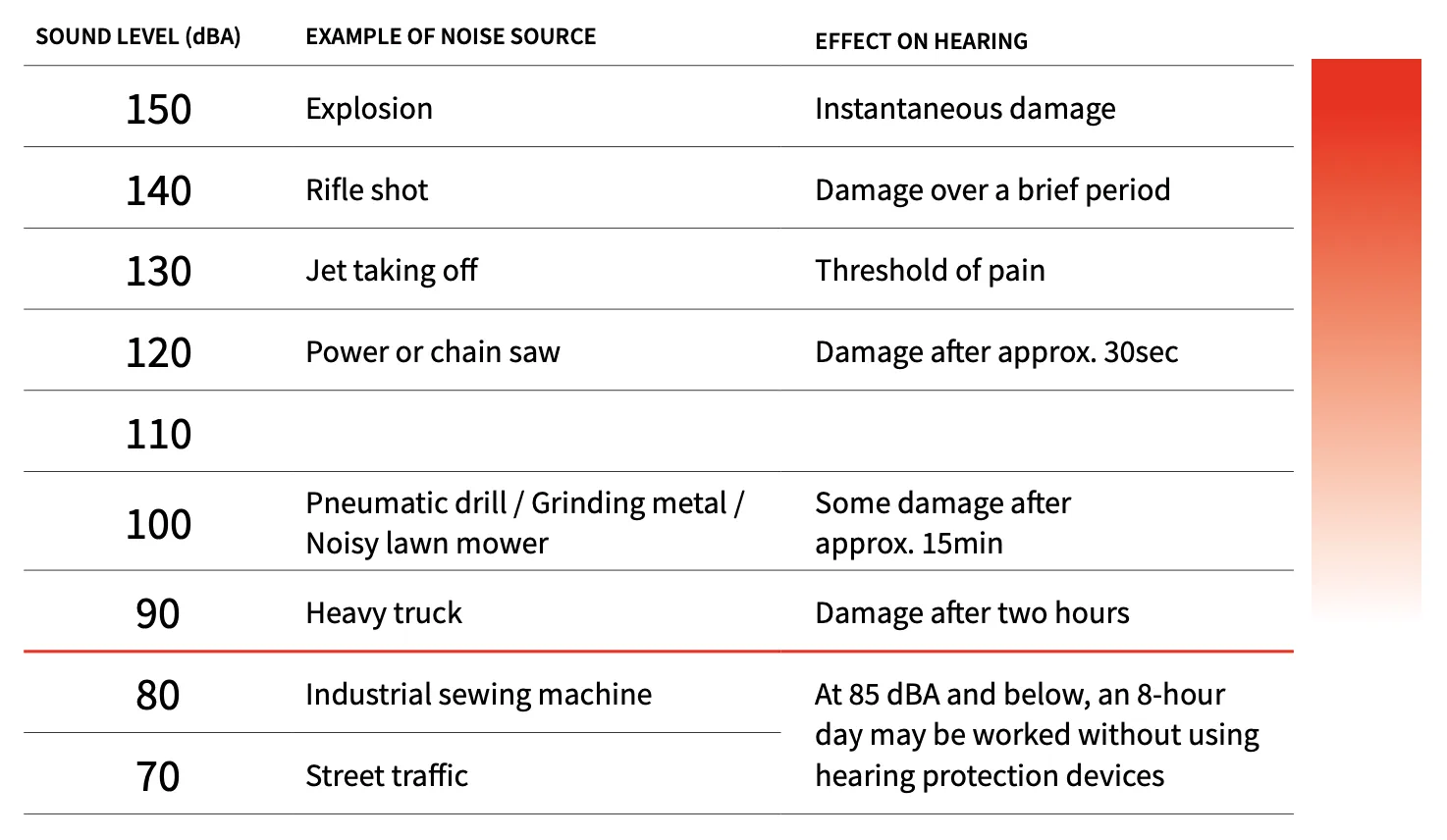
Minimum responsibilities – everyone!
Everyone who undertakes tasks where they are, or could be, exposed to excessive noise should read and understand this section, as well as the section above on ‘what we need to know about noise’.
Anyone who is responsible for, or has influence over, workers who are, or could be, exposed to excessive noise should also read and understand the following section on ‘planning and guidance considerations and responsibilities’.
All workers should:
- understand the risks associated with working in noisy environments;
- follow all procedures and controls put in place to keep themselves and others safe when working in noisy environments;
- use personal hearing protective devices when required, and ensure they are worn correctly;
- read the section later in this document on personal hearing protective devices;
- understand the noisy activities outside of work that can negatively impact on their hearing, such as listening to loud music or undertaking noisy tasks like mowing the lawn or using power tools at home; and
- advise their supervisor or the health and safety officer if they are concerned about the level of noise they, or others, are exposed to.
* See the Hearing Protection Guidebook from Worksafe
Planning and guidance considerations and responsibilities
Anyone who is responsible for, or has influence over, workers who are, or could be, exposed to excessive noise should also read and understand this section, as well as the minimum responsibilities for everyone.
This includes the production company, producers, directors, line producers, heads of departments, assistant directors and health and safety officers, who must consult, cooperate and coordinate with other PBCUs whose work may create, or be impacted by, excessive noise.
Everyone who is responsible for, or has influence over, an activity or task which creates, or is impacted by, excessive noise should:
- consider the risks associated with noise when planning and allocating tasks; and
- manage the risks associated with excessive noise, either eliminating or minimising them.
Identifying excessive noise
Everyone who is responsible for an activity or task in relation to the production should consider the risks associated with excessive noise.
Preliminary Noise Assessment
A preliminary noise assessment is often called a walkthrough survey. It is a screening tool, which will help identify probable or possible excessive noise and should highlight which tasks, processes or areas in the workplace require a detailed noise assessment.
Anyone can undertake a preliminary noise assessment – see appendix A below for an example of a checklist.
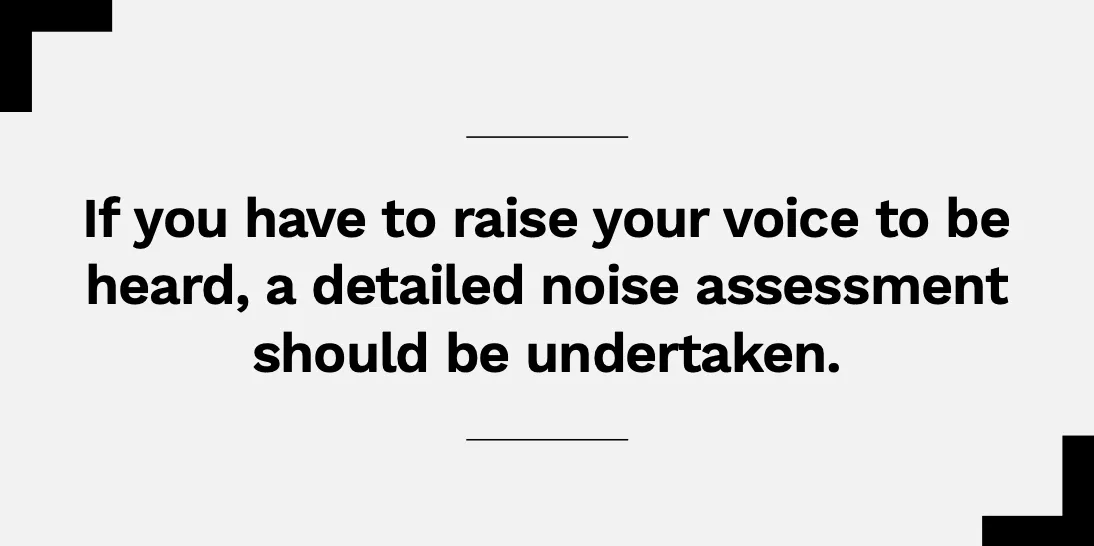
Detailed Noise Assessment
A detailed noise assessment will determine if the workplace contains noise that exceeds the exposure limits, and is required when:
- complex noise sources are present;
- if there is doubt over the noise levels – raised by the PCBU or workers; or
- if a preliminary noise assessment raises doubt over the noise levels.
A detailed noise assessment will:
- quantify the amount of noise workers are exposed to;
- help identify the noise source;
- assist in developing control solutions; and
- determine if hearing protection devices are required.
A detailed noise assessment must be undertaken by a competent person.
Further information can be found in Management of noise in the workplace - Approved Code of Practice (ACOP).
Hearing conservation programme
As soon as a PCBU is aware that workers are being exposed to noise that exceeds exposure limits, they must put in place a hearing conservation programme, which includes determining if hearing protection devices and hearing protection areas are required.
For more information about what needs to be considered as part of a hearing conservation programme refer to the Noise in the workplace – Approved Code of Practice (ACOP).
Hearing Protection Areas
Hearing protection areas are workspaces that have, or may have, excessive noise, where hearing protection devices must be worn, even if a worker or visitor is only in the area for a short amount of time.
These areas must be identified, with the areas and machinery concerned clearly labelled. The PCBU may wish to put up signs.
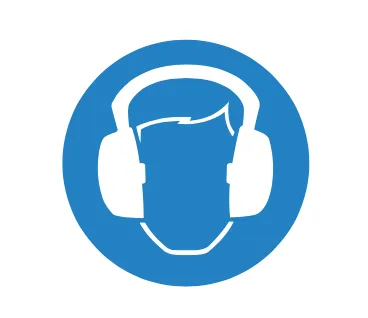
If signs are not practicable, the PBCU must work with workers to come up with other ways of informing both workers and visitors on set that they must wear hearing protection devices. This could include:
- warning notices;
- instructions on call sheets or during inductions; or
- specific supervision in areas with excessive noise.
The requirements for hearing protector areas are detailed in clause 10 Hearing protector areas of AS/NZ 1269.3
or you can read about them in part 6.4 (pg 23-24) of Approved Code of Practice (ACOP).
Managing the risk
Elimination is the most effective control method; you do this by completely removing or avoiding the possibility that someone will be exposed to excessive noise – 85dBA a day or a peak sound pressure level, Lpeak, of 140 dB.
If complete elimination is not reasonably practicable, you must consider ways to minimise the risk so workers are not exposed to excessive noise.
There are two primary ways to minimise, or control, excessive noise – at the source or by isolating either the source or the worker.
You can control the source of the noise by:
- purchasing equipment with the lowest noise rating;
- ensuring that, where reasonably practicable, machinery is installed with vibration isolators to reduce noise; or
- ensuring that equipment is properly maintained and operated.
Controlling noise at the source is best achieved at the planning stage; you can do this by:
- increasing the distance between the noise source and the exposed person;
- placing barriers between the noise source and the exposed person; or
- decreasing the time the at-risk person is exposed to the noise.
If you cannot reduce noise exposure to less than 85dBA a day, the final option is to minimise the risk using suitable hearing protection.
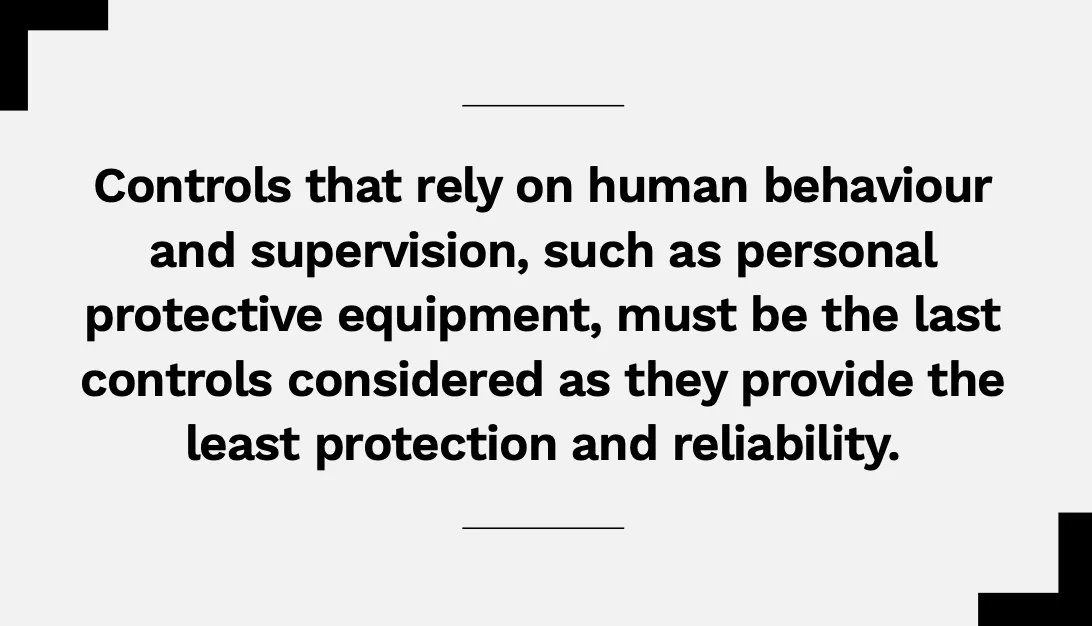
Hearing protection devices
If you cannot reduce the noise to a safe level for workers, you must ensure workers have suitable hearing protection devices (HPDs); the worker is responsible for using them appropriately.
Areas where HPDs must be worn must be designated hearing protection areas and, where practicable, signposted indicating that HPDs must be used.
The main types of HPDs are ear muffs and earplugs; either type can provide effective protection provided it makes an airtight seal in (plugs) or around (muffs) your ear.
The head of department, or equivalent supervisor:
- must ensure all HPDs are manufactured to a recognised Standard and must be the correct grade for the noise level encountered;
- should let the worker choose what HPD to use, providing it gives adequate protection;
- should ensure HPDs are clean and in a good state of repair.
It is important that hearing protectors fit correctly.
For more information about choosing and maintaining HPDs refer to the Noise in the workplace - Approved Code of Practice (ACOP).
See also - Hearing Protection (Worksafe booklet)
Training and Education
All workers should be trained in the selection, fitting, use, care and maintenance of HPDs.
Health and safety inductions should include an explanation about the risk that removing HPDs can have to an individual’s hearing.
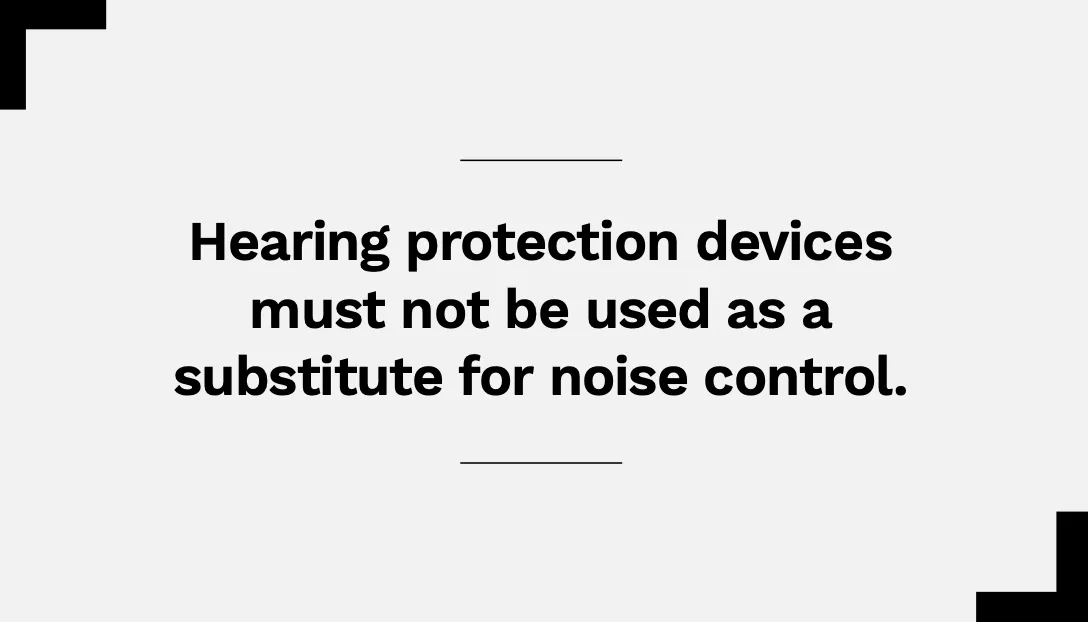
Monitoring the risk
During the production, workers’ exposure to noise should be monitored to ensure they are not being exposed to excessive noise.
If noise does exceed exposure limits, the PCBU must put in place a hearing conservation programme and may consider carrying out audiometric testing.
For more information refer to the Noise in the workplace - Approved Code of Practice (ACOP).
Funders
Funders should:
- be assured, through the provision of the production’s health and safety plan, that the funding provided is adequate to provide HPDs.
Production Company
In pre-production, production companies (likely to have primary responsibility over health and safety on the production) should:
- ensure workers’ exposure to noise to monitored; and
- ensure a hearing conservation programme is put in place.
Producer / Line Producer / Production Manager
As Producers and Production Managers have oversight across the production, they should:
- consider the potential for exposure to excessive noise when planning and allocating tasks;
- ensure the potential for exposure to excessive noise is either eliminated or minimised;
- ensure workers’ exposure to noise to monitored;
- ensure a hearing conservation programme is put in place;
- ensure information about hearing protection areas and the requirement for HPDs is included on daily call sheets.
Director
Directors should:
- consider the potential for exposure to excessive noise when planning and allocating tasks; and
- ensure the potential for exposure to excessive noise is either eliminated or minimised.
Heads of Department
Heads of Departments should:
- consider the potential for exposure to excessive noise when planning and allocating tasks;
- ensure the potential for exposure to excessive noise is either eliminated or minimised;
- ensure information about hearing protection areas and the requirement for HPDs is discussed at team meetings;
- let the worker choose what HPD to use, providing it gives adequate protection; and
- ensure HPDs are clean and in a good state of repair.
They must also ensure all HPDs are manufactured to a recognised Standard and are the correct grade for the noise level encountered. See the Approved Code of Practice.
Assistant Director/s
The Assistant Director/s should:
- ensure risks associated with excessive noise are discussed with all cast and crew during health and safety inductions and / or as required if circumstances on the set change; and
- report incidents of noise-related injury – notifiable event.
Health and Safety Officer
The Health and Safety Officer should:
- ensure risks associated with excessive noise are discussed with all cast and crew during health and safety inductions and / or as required if circumstances on the set change;
- explain the risk that removing HPDs can have to an individual’s hearing; and
- report incidents of noise related injury – notifiable event.
References
- Health and Safety in Employment Regulations 1995
- Occupational Health and Safety Service, Department of Labour (now WorkSafe New Zealand); A Message to Employers on Preventing Hearing Loss
- Occupational Health and Safety Service, Department of Labour (now WorkSafe New Zealand); Management of noise in the workplace – Approved Code of Practice (ACOP)
- Occupational Health and Safety Service, Department of Labour (now WorkSafe New Zealand); Management of Noise at Work - Control Guide (1996)
- ACC - Occupational Noise Levels
Appendix 1: preliminary noise assessment checklist
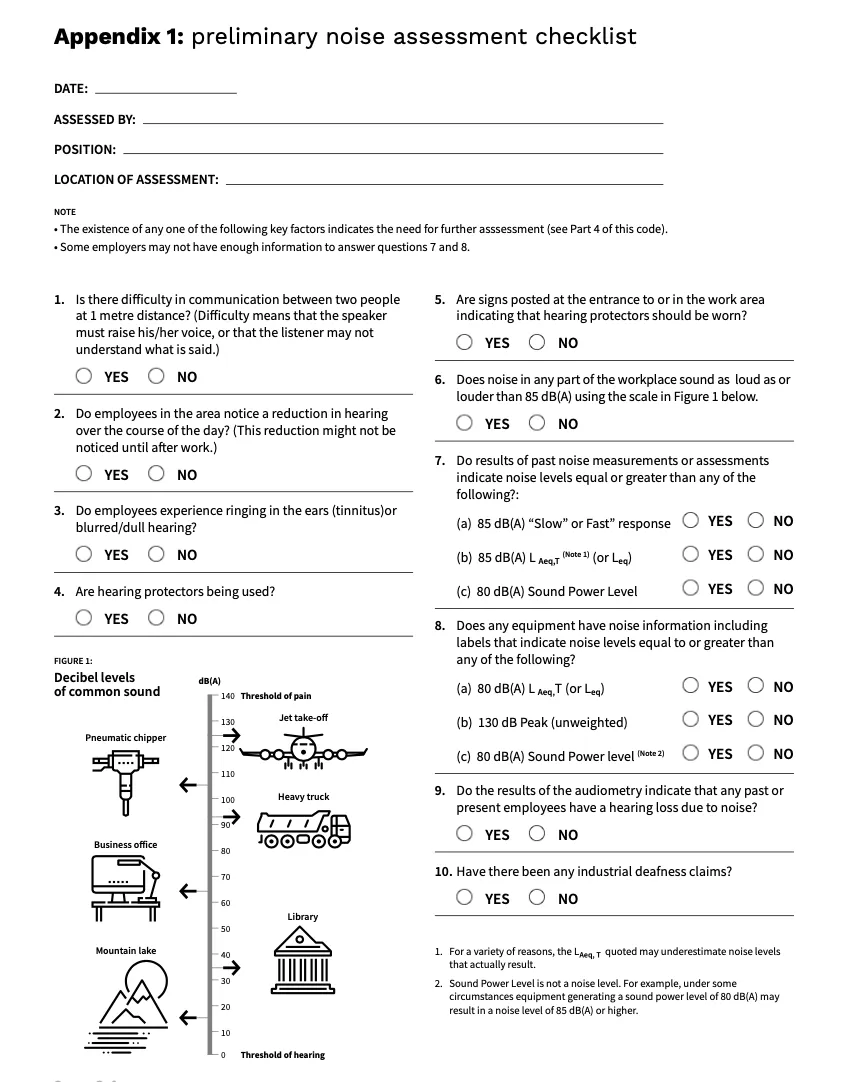
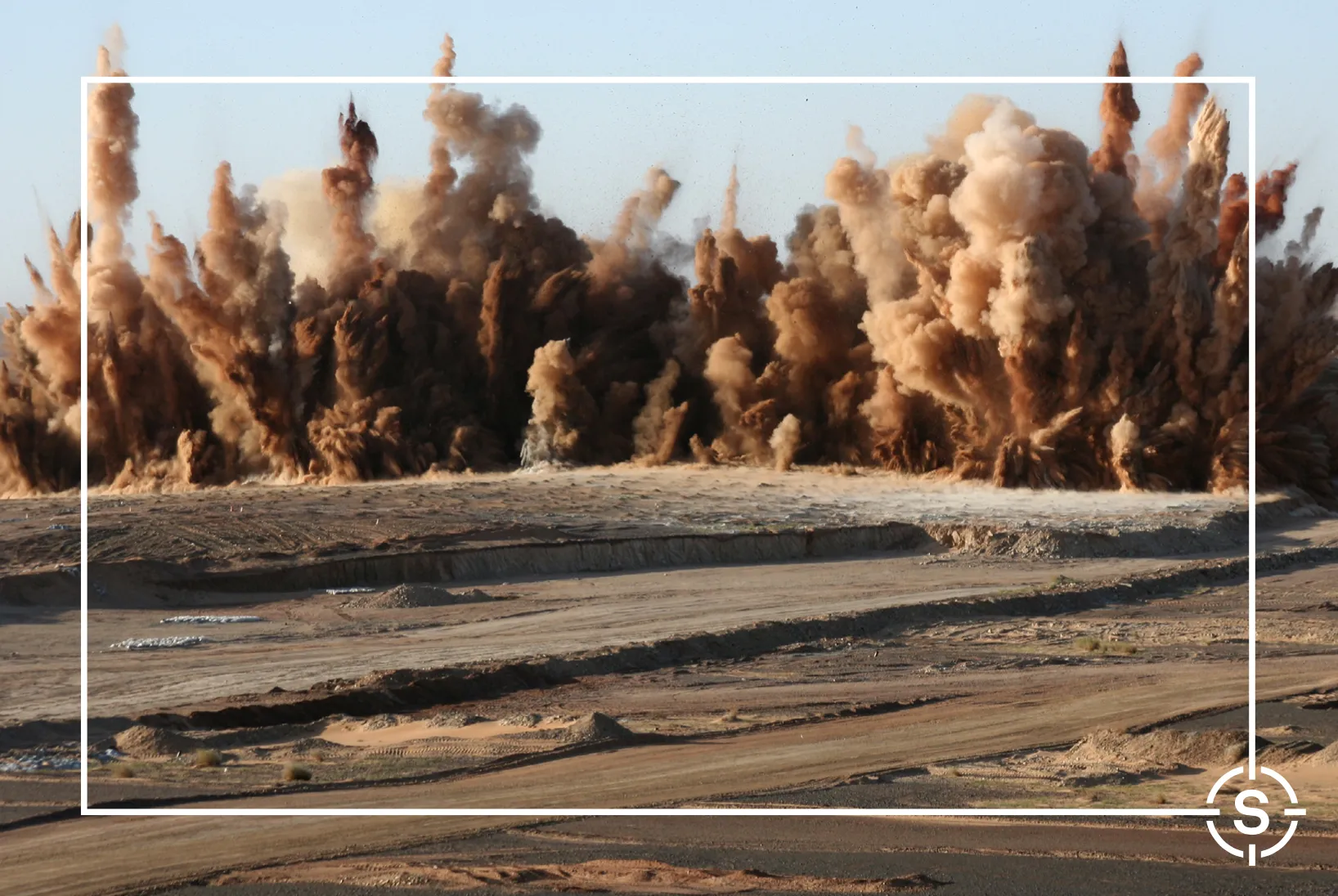
Noise Management
Who needs to read this?
Anyone involved in tasks that could lead to OOS (such as repetition), as well as those responsible for engaging staff to perform repetitive tasks on a production.
Roles that have direct influence over other workers should also read the ‘planning and guidance considerations’ section; this includes production company representatives, Producers, Directors, Production Managers, Heads of Department, Assistant Directors, Health and Safety Officers and Location Managers.
Definitions
OOS (Occupational Overuse Syndrome) or RSI (Repetitive Strain Injury) are terms used to describe a variety of conditions, including injury from discomfort. In accordance with WorkSafe New Zealand’s definition, OOS is characterised by discomfort or persistent pain in muscles, tendons and other soft tissues.
Symptoms
OOS is different to the type of pain associated with muscle pain and soreness after exercise, activity the body is not accustomed to, or other conditions such as arthritis.
Early symptoms of OOS may include:
- muscle discomfort
- fatigue
- aches and pains
- soreness
- hot and cold feelings
- muscle tightness
- numbness and tingling
- stiffness
- muscle weakness
Causes
OOS often occurs over time, and is normally caused or aggravated by specific types of work. The condition can also be created or made worse by activities away from the workplace.
Work that may result in OSS often involves repetitive movement, sustained or constrained postures, and/or forceful movements. It may also be provoked by other factors such as stress and working conditions. While some conditions of OOS are well understood medically, many are not and the cause of them is yet to be determined.
Prevention
Ensuring workers are provided a variety of tasks and regular rest breaks are believed to be the best preventative measures for OOS, as the absence of these is thought to strain muscle and tendons beyond their ability for short-term recovery.
High-Risk Roles
Some roles or tasks in the screen industry affected by OOS include:
- cleaners (studio and office cleaners)
- machinists (grips/riggers/set construction/camera department/art department)
- kitchen workers (craft service)
- typists (producers, assistants, production office)
- painters (set painters)
- hairdressers (hair and makeup)
- carpenters
- operators (camera, camera crane)
Minimum Responsibilities
Everyone involved in a screen production who undertakes tasks that could put them at risk of OOS should read and understand this section.
All workers should:
- read the above sections on definitions, symptoms, causes and prevention;
- understand the risk associated with activities that can lead to OOS; and
- inform their head of department if their workspace set up is not adequate.

Planning and Guidance Considerations and Responsibilities
Everyone who has responsibilities, or influence over, an activity or task that may result in OOS should read and understand this section, as well as the minimum responsibilities for everybody.
Prevention
The best way to avoid the consequences of OOS is through prevention rather than cure. Preventing OOS can be addressed through:
- design of equipment and tasks;
- organisation of work;
- work environment;
- training and education; and/or
- development of policies.
Roles and Responsibilities
Funders
Funders should:
- be assured, through the provision of the production’s health and safety plan, that the funding provided is adequate for the proposed length of the production process; and
- incorporate health and safety clause/s in the funding agreement.
Production Company
In pre-production, production companies (likely to have primary responsibility over health and safety on the production) should:
- ensure necessary planning is done to minimise risk of OOS occurring; and
- ensure senior staff hired are aware of OOS prevention.
Producer / Production Manager
In pre-production, the Producer / Production Manager should ensure:
- /adequate design of workstations and equipment;
- each person’s workstation is appropriately setup to minimise the risk of OOS;
- the number of people hired is in relation to the size of the project;
- there is enough variety of tasks in the organisation of work;
- enough people are hired to allow everyone appropriate rest breaks;
- staff are aware of ways to prevent OOS and provide any training or education on this where required; and
- sufficient resources, including budget, are allocated to enable appropriate and safe environments and working practices.
Director / Heads of Department
The Director and all Heads of Department should:
- be aware of the risk of OOS to their respective teams; and
- take steps to provide adequate workspaces, appropriate rest breaks and a variety of tasks where possible to minimise the risk of OOS developing.
Health and Safety Officer
The Health and Safety Officer should:
- work with the Producer, Production Manager and Heads of Department to help them assess workspaces that may present a risk for OOS; and
- ensure the potential for any OOS arising is discussed with cast and crew during health and safety inductions and / or as required if circumstances change.
Training
- Workers should be made aware of OOS during their health and safety induction.
References
The following were used as reference in the research and development of these guidelines:
NZ Technician’s Guild Safety Code of Practice (SCOP)
http://screensafe.co.nz/pdf/Technical Guidelines for ScreenSafe.pdf


Occupational Overuse Syndrome
Water safety
New Zealand has one of the highest fatal drowning rates in the OCED and New Zealand waters are unpredictable; if filming on, in or around water the production must take into consideration water safety for people and animals.
ScreenSafe suggests all productions are familiar with Water Safety New Zealand and AdventureSmart. Water can include the ocean, rivers, streams, lakes and pools.
Ensuring safety
Productions should ensure:
- competent guides are used where appropriate, especially in extreme conditions;
- qualified life-saving personnel are present for the duration of the production activity;
- equipment (such as safety boats, lifejackets and scuba diving equipment) is maintained and tested;
- all divers working on production have the relevant certificate of competence for the work they are undertaking and current medical clearance;
- WorkSafe’s guidelines are followed for all diving related to a production;
- actors required to dive have appropriate training, this could be a resort/discovery course (at a minimum) or a full Open Water course or higher:
- ~ if they only have done a resort / discovery course, they must have a safety diver, who holds a certificate of competence; if they
hold a higher level of training, the number of safety divers is determined as part of the risk assessment approved by the diver supervisor; - people understand the risk of hypothermia, how to identify it and what to do;
- two-way communication is available;
- anyone expected to swim is competent to do so;
- life jackets are used where practicable;
- water is checked for hazards, including depth, currents and rips, tides, waves, objects and dangerous marine life;
- weather forecasts are checked, especially when working around, in or on rivers as water levels can rise rapidly;
- people or animals are not fatigued when required to work in, on or around water;
- if people or animals are required to enter the water, quality tests should be undertaken to ensure the water is free of contaminants;
- if people or animals are required to enter the water, water temperature and length of exposure should be considered;
- have an emergency plan in place;
- only competent people, who understand maritime rules, drive vessels;
- if working at a beach, crew know how to identify a rip and what to do if stuck in one;
- if crossing rivers, this is done so safely and sensibly;
- if animals are used, trainers should be adequately instructed in water safety precautions; it is recommended that trainers be acquainted with the hazards and procedures for working safely around water and that any animals working on, in or at the water’s edge are comfortable doing so prior to the production.
Navigation and safety rules
Be aware navigation and safety rules can vary from region to region in New Zealand, in the form of regional bylaws; ScreenSafe recommends that productions take the time to get acquainted with the rules relevant to that region.
References
https://www.watersafetynz.org
https://www.adventuresmart.nz
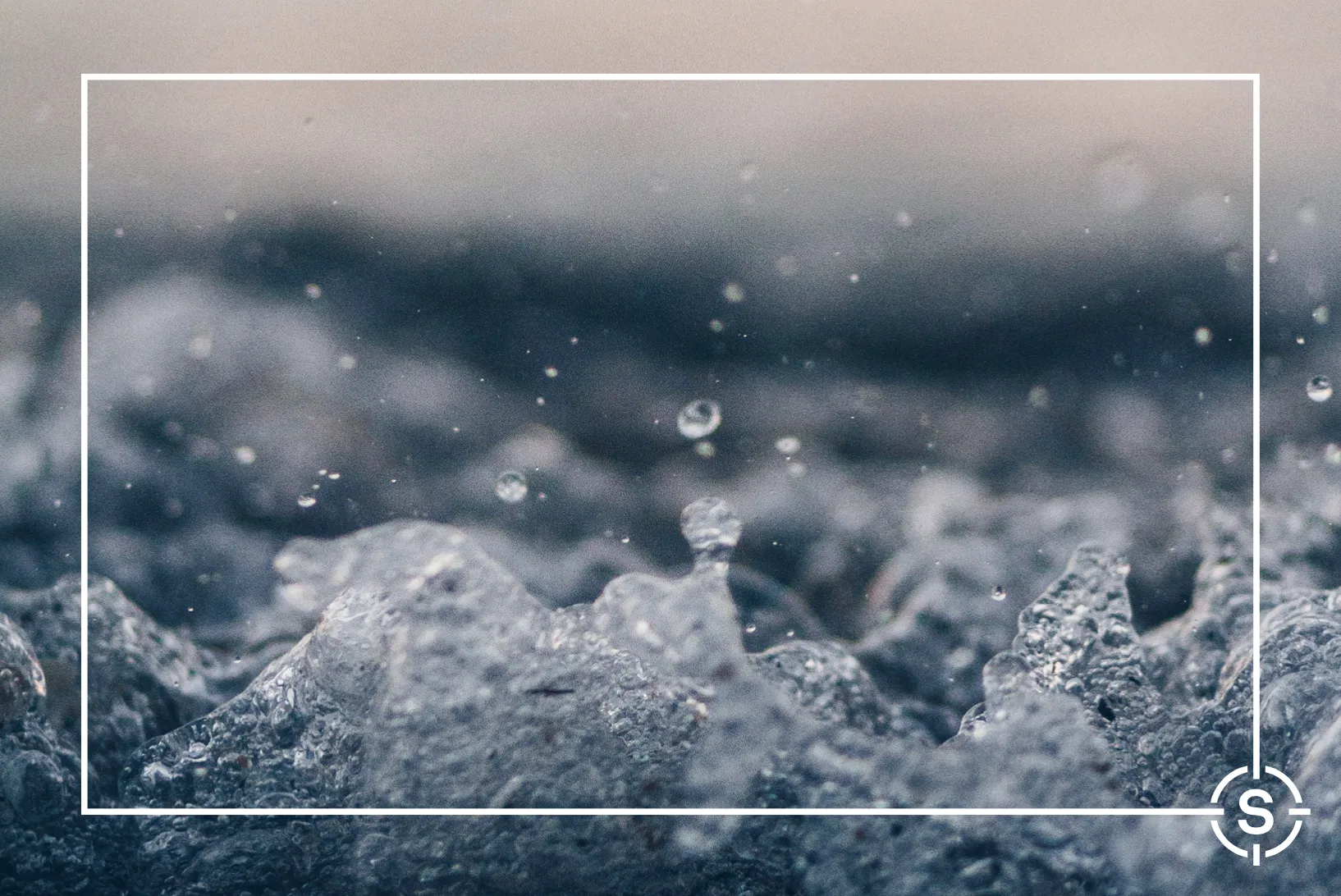
Water Safety
Who needs to read this?
Anyone involved in the use of animals or who interacts with animals and their trainers on a production, as well as those responsible for engaging animals and animal trainers on a production.
Definitions
This chapter provides guidance on working with animals. This is defined as any instance when an animal is required to be present on the set of a production.
An “animal” is defined as any animal provided for theatrical purposes in any film, video or moving image production.
A “trainer” means a person who handles and trains any animal. This includes a wrangler.
Detailed guidance around the engagement of animals on a production is provided by the American Humane Association (AHA). These are mentioned only for reference, as they are not in force in New Zealand, but are generally accepted in the absence of a local detailed equivalent. Some offshore productions, such as those by major motion picture studios, may be bound by agreements with the AHA, which must be adhered to.
Minimum Responsibilities
Everyone involved in a screen production who undertakes tasks relating to working with animals, or who is working in an environment where animals and their trainers may be working or resting, should read and understand this section.
Beyond trainers or assigned performers authorised by a trainer, workers on a production should never engage, touch or interact with working animals. Animals on a production are working and should be treated as such and should not be distracted.
Planning and Guidance Considerations and Responsibilities
Everyone who has responsibilities, or influence over, an activity or task in relation to working with animals should read and understand this section, as well as the minimum responsibilities for everybody.
The Producer and Production Manager should consider the resources needed to engage animals on a production safely during pre-production; this includes:
- ensuring all animals required for a production (including action and dressing animals) are engaged through an established and reputable company with qualified trainers to coordinate action for camera
- hiring competent people with an appropriate level of training, experience and/ or qualifications for handling and training the animals and the requirements of those animals for the production;
- ensuring the number of people hired in relation to the size of the project and number of animals required is sufficient; and
- ensuring sufficient resources and facilities, including budget, are allocated to enable appropriate and safe practices for keeping and working with the animals on the production.
Hazards and Associated Risks
The following potential hazards in relation to working with animals should be considered, and the level of risk assessed.
Refer to Appendix 2: Health and Safety Risk Assessment process for more information on identifying hazards and assessing risk.
The most common expected hazards and risks associated with working with animals may include:
- bites, kicks and scratches
- crushes and bumps
- falls
- unexpected movement and noise
- compromised wellbeing of animals as a result of fatigue.
General Safety Guidance
The trainer, producer and any other persons deemed responsible for the animals should consult with the owner on the safe handling and transport of the animals. They should also ensure that adequate time is given to familiarise themselves, and the animals, to the routine and working environment for any given shot or sequence.
Call sheets / Closed Set and Notification of Personnel
The Producer or person with delegated responsibility and the Trainer should communicate to all personnel that animals are on location. Appropriate information on safety matters specific to the species should be included, particularly during pre-production for any planning considerations to be taken into account.
Notice should be given on the call sheet prior to shooting and a reminder of instructions for workers during briefing at the beginning and/or prior to the animals being brought onto the set of a production.
Safety guidance specific to the species of animals being used should be attached to the call sheet. An opportunity should be given to the trainer and stunt coordinator to address the cast, crew and parents or chaperones of any children on the set about the safety precautions while animals are on set.
It is recommended that a “closed set” notice be displayed on all stages or locations where animals are working. Every effort should be made to maintain a closed set where animals are working. Based on trainer’s discretion, all non- essential personnel should be cleared from a set when an animal is working.
Handling and Transportation of Animals
The Trainer is responsible for the handling and transportation of the animal. Assistant Directors must ensure all animals are cleared from the set (at lunch, break or wrap) before others are cleared. Horses should always be given a clear path to their holding area.
Provision of Animal Facilities
The trainer in consultation with the producer or person with delegated responsibility should provide facilities for:
- an easily accessible area available for loading and unloading animals; and
- a stress-free area.
Trainer to Animal Ratio
The Trainer and the Producer should determine the ratio of trainers or assistants to animals to ensure the safe control of the animals.
As a general guide, a recommended ratio would be one trainer to three action horses and two trainers for each undomesticated animal.
Interaction with Animals
Be aware that animals can be easily distracted. No member of cast or crew is permitted to pet, fondle, play with or feed animals on set or on standby if the Trainer believes it is not in the animals’ best interests or believes it is unsafe. Permission to approach, handle or pet animals on or around a set should be obtained from the Trainer or person in charge of the animal. If you do not have permission to do so, refrain from any contact with the animal.
Motion, noise or smells, such as food, perfume or alcohol, should be avoided when around animals. It is recommended that any unit catering be moved away from where animals are kept or working.
Moving and Setting up Equipment
If animals are on set, the trainer must be alerted before any equipment is moved or adjustments are made. Special care should be taken when moving or setting up any equipment near animals. Equipment such as ladders or lighting stands that can easily tip over and make a noise that may startle animals should be secured.
Set Construction
The set should be constructed, or the location layout arranged, to meet the requirements of the animals and action in the scene.
Supervision
All animal action should be carried out under the supervision of the Trainer or person in charge of the animal. The Trainer shall ensure that all animals required to work on the set of a production are well prepared and trained to be acclimatised to the conditions. The Trainer should be satisfied that the animals will perform in a way that is safe for the cast, crew and general public.
Performers and Animals
If an animal and a Performer are required to perform together in a scene that is deemed a stunt or a dangerous situation, ample time should be given for the Trainer, Stunt Coordinator, Performer(s) and animals to be familiar with the routine and each other.
Use of Firearms and Ammunition
The Armourer and Animal Trainer should consult on the handling of animals and firearms, and the level of blank ammunition loads should be determined in consultation with the Animal Trainer/Wrangler and the Armourer. Live ammunition should not be used, only blank ammunition. All Trainers should be given prior notice to shots being fired or the detonation of explosions around performing animals.
Veterinary Provisions
The Trainer or person supplying the animal shall be responsible for ensuring that all necessary vaccinations, inoculations, applicable licenses and medical safeguards are current and that documentation is available.
Sedation of Animals
The Trainer should consult with the Producer or person with delegated responsibility on the need for sedation and the safety precautions to be taken. Where there is a potentially dangerous animal action, sedation equipment should be available with a qualified veterinarian present. Sedation should not be used for the purpose of ‘calming’ a performing animal. Sedated animals are unpredictable.
Special Effects
All animals should be trained and prepared for work around special effects such as explosions, ammunition, artillery, pyrotechnics or the use of chemicals.
For further detailed recommendations on the use of special effects around animals, see Chapter 6 (pg 43) of the American Humane Association’s guidelines.
First Aid and Emergency Medical Transport
There should always be a qualified first aid provider present on set. Based on the types of animals used and the location, consideration should be given to providing onsite emergency medical transportation with qualified medical personnel, up to and including life support if deemed necessary. If the location is particularly remote, access to telecommunications and the necessary modes of transportation should be considered.

Animal Specific Recommendations
The following section includes safety guidance specific to a species of animal that might be required to work on a production.
Horses – Specific Guidance
The following guidance should be followed when working with horses.
- They are appropriately shod for the working surface.
- Under no circumstances horse falls be accomplished by tripping or pitfalls.
- No one rides a horse off-camera except for those designated by the trainer.
- Under no circumstances are spurs to be worn by any performer without the prior approval of the stunt coordinator and/or the trainer.
- All hitching posts or rails are fastened in the ground so that the tugging of a frightened horse cannot pull it loose; on a stage, hitching posts or rails should be bolted or fastened in a rigid manner.
Livestock and large numbers of Animals
Where large numbers of animals are required (such as battle scenes, or historical re-enactments), a chain of responsibility should be established to coordinate the work during the production.
Appointed by the Producer, the person in charge of each unit should be directly responsible for the conduct of the people and the care of the horse/livestock under his or her care.
The ratio of trainers to animals should still be observed.
Exotic Animals
The Trainer should provide the Producer with information instructing the cast and crew on how to behave in the presence of exotic animals. This information should be attached to the call sheet and conveyed to all persons working with or near these animals.
- Children should only be near potentially dangerous exotic animals when monitored by a trainer and in a controlled environment when rehearsing or filming.
- For smaller exotic animals, a separate temperature-controlled room should be provided when necessary.
- Larger exotic animals should be provided with a separate sheltered area where cast and crew are prohibited from visiting.
- A plan to prevent the escape of any wild or exotic animals should be in place. In the event an escape does take place, a plan to safely recapture them, without any harm to the animal, should be in place.
Insects and Arachnids
The following guidance is specific to the use of insects and arachnids.
- Nothing should be done to an insect that would cause it permanent harm or alter its physical characteristics or behaviour.
- A trainer knowledgeable of the particular insect(s) should be on set when in use.
- All insects used should be collected after completion of a scene and none should be allowed to remain on the set or location.
- Care should be taken when using an insect species not indigenous to an area and any appropriate permissions should be sought.
- Precautions should be taken to prevent or at least minimise the number of insects that fly into the lights.
Apes and Monkeys
The following guidance is specific to the use of apes and monkeys.
- Stages, sets and locations should be checked by the Trainer for escape routes or other possible hazards.
- Any products containing harmful chemicals or sharp items should be removed from the area. Apes and monkeys are fast climbers and are capable of opening or closing doors and drawers.
- Props being used on the set should be checked and approved by the trainer.
- Only personnel necessary for filming should have contact with apes and monkeys.
- Anyone with a cold or other contagious virus should keep a distance from apes or monkeys.
- Care should be taken to ensure rest when a significant amount of work is needed, trainers should be able to advise on each animal’s capabilities.
- For apes working for long periods on a production, such as more than a few consecutive days, a play area, empty room or private park where the animal(s) can relax and exercise should be made available.
- Apes should only work after sundown if the trainer has conditioned them to do so. It is recommended to avoid this where possible.
- If clothing is to be used on apes, they should be easy to remove and loose. Clothing should not restrict the ability of the animal to walk, hear or see.
- Apes should be introduced to anything that may be frightening or otherwise unnatural, including any moving objects. They should be familiarized with any animatronic objects, people in costumes and props.• Sets and locations should be kept cool around apes.
- Apes should not be on set for any reason other than when filming, rehearsal or preparation or familiarisation with objects or people in the scene.
- Do not use apes as stand-ins for lighting adjustments.
Wildlife
The following guidance relates to a working environment that may result in wildlife being encountered on set.
- The producer is responsible for assuring the safety of any animals that are naturally present in the surrounding area where a production is present.
- The producer should consult the relevant agencies or contact persons responsible for removing or relocating wildlife from location sets. Any native animals that remain on the set are subject to the applicable animal safety guidelines and procedures.
- If native animals are not to remain on set, they should be carefully removed, relocated, properly housed and cared for before being safely returned after filming.
- The production company should never intentionally harm nests, dens, caves or caverns and precautions should be taken to protect them. Care should be taken to ensure that any non-indigenous animals are removed from the area after production is complete.
Uncontrolled Animals
All personnel should be aware of the unpredictability of uncontrolled animals on and around a location (e.g. farm animals, wandering dogs, horses or other livestock in paddocks etc.) as well as the effect that events such as bright lights or sudden noise may have on them.

Water Safety
An Animal Trainer should be adequately instructed in safety precautions to be taken when working on, in or at the water’s edge. It is recommended that the trainer be familiar with the hazards and procedures for working safely around water and that any animals working on, in or at the water’s edge are comfortable doing so prior to the production.
Qualified life-saving personnel and equipment (such as safety boats) should be present for the duration of the production activity.
Water temperature and length of exposure should also be considered.
Air Safety
Animals must be adequately conditioned to work in and around aircraft prior to filming. If animals become stressed, they must be removed from the aircraft or filming area immediately.
The Animal Handler, and the Pilot or Aerial Coordinator must work together to ensure the safety of the animals.
Training
Trainers should have the appropriate minimum level of training and experience required to perform their duties on the production. This should be provided to and verified by the production company prior to the trainer being hired.

Roles and Responsibilities
Funders
Funders should:
- be assured, through the provision of the production’s health and safety plan, that the funding provided is adequate for the proposed length of the production process; and
- incorporate health and safety clause/s in the funding agreement.
Production Company
In pre-production, Production Companies (likely to have primary responsibility over health and safety on the production) should ensure:
- experience and qualifications are verified for specialist personnel such as Trainers and a record kept of this;
- that all workers are briefed about safe working practices whenever animals are present;
- All workers are made aware of the guidelines and their minimum responsibilities if animals are to be engaged on the production.
Producer / Production Manager
As Producers and Production Managers have oversight across the production, they should:
- request evidence of, and verify experience of Trainers, or proof of the appropriate certification.
- consult and coordinate during pre-production with the relevant parties to ensure the budgeting, scheduling and resources allocated to the animals department is sufficient enough to ensure the safety and comfort of animals working on the production.
- ensure workers are briefed on safety procedures for working around animals during their induction, pre-production and on the day when animals are present.
Line Producer
Line Producers also have oversight of the production process and should create a production schedule that provides adequate time for work involving animals to be undertaken safely.
Consideration should be given to the additional time required for Trainers and their animal performers to do their work safely and allowances in scheduling should be made for this.
Director / Heads of Department
Directors and Heads of Department should:
- be mindful of the delays working with animals on a production can cause;
- always defer to the Trainer’s advice and judgment on when an animal is tired and allow for appropriate rest time; and
- never pressure the Trainer or animals to work beyond the amount of time a Trainer recommends.
Assistant Director/s
The Assistant Director/s should ensure potential hazards and risks are discussed with all cast and crew during health and safety inductions and / or as required any time that circumstances on the set change. Assistant Directors should also create a production schedule that provides adequate time for work to be undertaken safely.
Health and Safety Officer
The Health and Safety Officer should:
- work with the producer, production manager and heads of department to help them identify the potential for hazards and risks relating to the engagement of animals on a production; and
- ensure the potential of hazards and risks involving animals is discussed with all cast and crew during health and safety inductions and / or as required if circumstances on the set change.
References
NZ Technician’s Guild Safety Code of Practice (SCOP) section on Working with Animals:
http://screensafe.co.nz/pdf/Technical Guidelines for ScreenSafe from SCOP FINAL.pdf
Ontario Ministry of Labour, Safety Guidelines for the Screen Industry:
https://www.labour.gov.on.ca/english/hs/pubs/filmguide/gl_40.php


Working with Animals
Workplace bullying
This chapter provides guidance on the prevention and response to bullying in the New Zealand screen industry.
This chapter is primarily based on guidance issued by WorkSafe New Zealand.
Introduction
This chapter provides guidance on the prevention and response to bullying in the New Zealand screen industry, from the initial concept for the film, television show or advertisement, to casting, production, post production through to the final delivery of the project.
Everyone involved in the screen industry is responsible for creating an environment where individuals are treated with respect and dignity.
Bullying during any stage of a production can have serious effects on the health and safety, and the overall performance, of workers.
Bullying is unacceptable both morally and legally – as outlined in the Health and Safety at Work Act 2015.

Who needs to read this?
All workers on a production have a legal duty to ensure health and safety legislation, regulations and guidelines are followed, and are directly responsible for their individual conduct.

Anyone working within or with the screen industry, including those responsible for engaging with talent and crew on a production, should follow these guidelines.
Roles that have direct influence over other workers should also read the ‘planning and guidance considerations and responsibilities’ section; this includes production company representatives, casting agents, agents, cast, producers, directors, production managers, heads of departments, assistant directors, health and safety officers, and location managers, along with any other crew and all other contractors.
Definitions
Workplace bullying, as defined by WorkSafe New Zealand, is repeated and unreasonable behaviour directed towards a worker or group of workers that can lead to physical or psychological harm.
What we need to know about workplace bullying

* Find out more about what workplace bullying is, and is not, on the WorkSafe New Zealand website.
Discussion between workers, even when there are different ideas / disagreement of ideas, can be useful if it promotes new solutions and ideas; however, this needs to be observed as it could escalate to bullying.
When Can Bullying Occur?

Bullying could:
- be between managers and workers, or co-workers, or workers and visitors on set;
- occur at any time;
- be carried by one or multiple people;
- be directed at one or multiple people;
- occur outside of work hours.
Bullying can be carried out in person, by email, text messages, internet chat rooms or other social media channels.
How to Identify Workplace Bullying – what Kind of Behaviour Can Be Perceived as Bullying?
Bullying can be physical, verbal or relational / social (such as excluding someone from a peer group or spreading rumours).
Common bullying behaviours fit into two main categories:
1. Attacks that are direct and personal
- such as belittling remarks, silent treatment, attacking a person’s beliefs, race, gender, gender identity, sexual orientation, lifestyle or appearance, threats of violence, humiliations, intimidation, unwanted sexual approaches, verbal abuse; or
2. Attacks that are indirect and task related
- such as impossible deadlines or tasks, meaningless tasks, withholding information, constant criticism of work, underwork, unreasonable monitoring, no support from manager, scapegoating.
Minimum responsibilities for everyone
Everyone involved in a screen production should read and understand this section.
Everyone involved in a production should have read the section on ‘what we need to know about workplace bullying’ above and:
- understand what workplace bullying is;
- understand how to identify workplace bullying; and
- ensure they advise the health and safety officer, their direct supervisor, the assistant directors, and/or the production manager/office if they become aware of bullying.

* Download the "Bullying at Work: Advice for Workers - Quick Guide" by clicking the image below.

* For more detail on roles and responsibilities regarding workplace bullying see section 3.8 of WorkSafe New Zealand’s Good Practice Guide ‘Preventing and responding to bullying at work’.

Planning and Guidance Considerations and Responsibilities
Everyone who is responsible for, or has influence over, an activity or task in relation to a production should read and understand this section, as well as the minimum responsibilities for everybody.
This includes funders, production company representatives, directors, producers, production managers, line producers, heads of department, assistant director/s and health and safety officers. All of whom should follow the guidance provided in the below sections on assessing the risk and managing the risk, as well as the section for their specific role.
Assessing the Risk

How Can You Tell if Bullying is Occurring?
Anyone who is responsible for an activity or task in relation to a production should understand what workplace bullying is, when it may occur and
know how to identify it.
We are all responsible for taking reasonable care of our own health and safety and ensuring that our actions, or inactions, do not harm others – including understanding bullying.
A good starting point to tell if bullying is occurring is to look at, but not limited to:
- unexpected turnover of workers;
- unexpected absenteeism – sick leave;
- formal complaints / reports of unreasonable behaviour;
- worker interviews / focus groups; or
- feedback from workers or/or health and safety representatives.
* Detailed information can be found in tables 4 and 5 in section 2 of WorkSafe New Zealand’s Good Practice Guide ‘Preventing and responding to bullying at work’.
Managing the risk

Bullying
It is unlikely you will ever be able to completely eliminate bullying; however, you must, so far as is reasonable, minimise the likelihood of bullying by putting in control measures and effectively managing it when it does occur.
You can help minimise bullying by:
- building good relationships in a respectful work environment;
- developing good managers;
- educating workers about bullying;
- making sure your workers know how to report unreasonable behaviour;
- making sure everyone knows their responsibilities;
- making your anti-bullying policies, processes and systems transparent; and
- providing support to workers who experience unreasonable behaviour.
This could include having a code of conduct – for an example see the NZ Police Code of Conduct: https://www.police.govt.nz/about-us/publication/new-zealand-police-code-conduct

* Detailed information about how you can minimise bullying can be found in section 3 of WorkSafe New Zealand’s Good Practice Guide ‘Preventing and responding to bullying at work’.
ScreenSafe highly recommends everyone who is responsible for, or has influence over, an activity or task in relation to a production read this section.
Investigating Bullying

Quick Guide ‘Preventing and responding to bullying at work: Advice for small businesses’
The below flow chart can help you decide what approach to take.


Detailed information about who can help in cases of bullying can be found in section 6 of WorkSafe New Zealand’s Good Practice Guide ‘Preventing and responding to bullying at work’. This section outlines relevant legislation and external parties who can help you and / or your workers.
Workplace Anti-bullying Policy
Consider developing an anti-bullying policy to sit alongside your health and safety policy.
The policy should:
- define bullying;
- state what will be done on the production to minimise the risk of bullying;
- outline workers responsibilities;
- outline procedures for reporting bullying risks; and
- outline procedures for managing bullying.
* An anti-bullying policy template can be found HERE
Responsibilities
Funders
Funders should:
- incorporate anti-bullying clauses, such as implementing an anti-bullying policy, in the funding agreement.
Production Company
The production company (likely to have primary responsibility over health and safety on the production) should develop an anti-bullying policy.
Producer / Production Manager / Line Producer / Director / Heads of Department
As positions with oversight across the production, Producers, Production Managers, Line Producers, Directors and Heads of Departments should:
- understand how to identify bullying;
- minimise bullying as far as is reasonably practicable, following the guidelines outlined in ‘managing the risk’;
- investigate any claims of bullying.
Assistant Director/s
The Assistant Director/s should:
- understand how to identify bullying and the processes for dealing with bullying.
Health and Safety Officer
The Health and Safety Officer should:
- work with Producers, Production Managers, Line Producers, Directors and Heads of Departments to help identify and investigate bullying.
Who can help?
Acts of violence should be reported to the Police as soon as possible; this could be verbal (verbal abuse, threats, shouting, swearing) or physical (stalking, throwing objects, hitting, damage to property).
As outlined in WorkSafe’s quick guide “Bullying at Work: Advice for Workers”, help and advice may be found from places like:
- WorkSafe, as New Zealand’s primary health and safety regulator: 0800 030 040 (24 hours)
- Human Rights Commission (for complaints about discrimination): https://tikatangata.org.nz
- Community law centres: http://communitylaw.org.nz
- The Citizens Advice Bureau: www.cab.org.nz
- Helplines such as Lifeline 0800 543 354, Samaritans 0800 726 666 and Healthline 0800 611 116 (for more information see: www.mentalhealth.org.nz/get-help/in-crisis/helplines)
- NetSafe (for cyberbullying): www.netsafe.org.nz/what-is-cyberbullying

Workplace Bullying
Did you find what you need?
Email ScreenSafe Support
Provide some details on what you are looking for and we will be in touch.
Search our Website
Provide some details on what you are looking for and we will be in touch.